Impact sockets are essential tools for both professionals and DIY enthusiasts. They are designed to withstand the high torque and impacts generated by impact drivers and wrenches, making tasks like automotive repairs, construction, and heavy machinery maintenance more efficient. Choosing the right impact socket can significantly enhance your toolset’s performance, durability, and versatility. In this comprehensive guide, we’ll delve into the key factors that make a good impact socket, helping you make informed decisions for your specific needs.
Material Composition
Types of Steel Used
When it comes to impact sockets, the material composition plays a crucial role in determining their performance and longevity. The most common types of steel used are Chrome Vanadium (Cr-V) and S2 steel.
Chrome Vanadium steel is renowned for its excellent toughness and resistance to wear and tear. It is a popular choice for many standard impact sockets because it offers a good balance between strength and flexibility. Cr-V sockets are typically more affordable, making them a preferred option for those who need reliable performance without breaking the bank.
On the other hand, S2 steel is a higher-grade alloy that offers superior hardness and strength compared to Chrome Vanadium. S2 sockets are designed to endure more rigorous use, making them ideal for heavy-duty applications where maximum durability is required. These sockets can handle higher torque levels and are less likely to deform or break under extreme conditions.
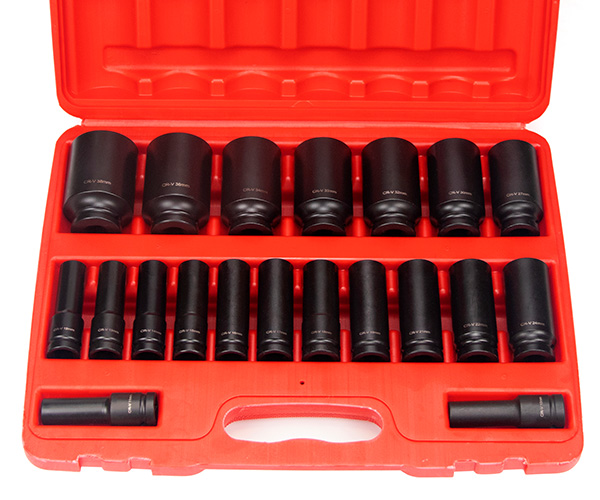
The choice between Chrome Vanadium and S2 steel depends on your specific requirements. If you frequently work with high-torque applications or need sockets that can withstand harsh environments, investing in S2 steel sockets might be worthwhile. However, for general use and lighter applications, Chrome Vanadium sockets provide ample performance and durability.
Heat Treatment Processes
Heat treatment is another critical factor that influences the quality and performance of impact sockets. This process involves heating and cooling the steel to alter its physical and mechanical properties, enhancing its strength and resilience.
Proper heat treatment ensures that the sockets have the necessary hardness to resist deformation under high torque and impacts. It also improves the steel’s ability to absorb shocks, reducing the likelihood of cracks and fractures during use. Without adequate heat treatment, even high-quality steel can fail prematurely, leading to safety hazards and increased costs due to frequent replacements.
Manufacturers that prioritize quality will implement rigorous heat treatment protocols, ensuring each socket meets stringent performance standards. This attention to detail results in impact sockets that not only last longer but also perform more consistently, providing reliable torque transfer and minimizing the risk of tool slippage or damage.
In summary, the combination of high-quality steel and effective heat treatment processes is fundamental to producing impact sockets that deliver exceptional performance and durability. When selecting impact sockets, it’s essential to consider both the type of steel and the heat treatment methods used by the manufacturer to ensure you’re getting a tool that meets your specific needs.
Design and Construction
Socket Thickness and Weight
The design and construction of an impact socket significantly impact its performance and ease of use. One of the critical design aspects is the socket’s thickness and weight. A thicker socket generally offers greater strength and durability, allowing it to withstand higher torque levels without deforming or breaking. Thicker sockets are particularly beneficial in heavy-duty applications where maximum force is applied, such as in automotive repairs or industrial machinery maintenance.
However, increased thickness often comes with added weight. While sturdiness is essential, excessive weight can make the socket cumbersome and tiring to use, especially during prolonged tasks. Therefore, finding the right balance between thickness and weight is crucial. High-quality impact sockets are engineered to provide optimal strength without being overly heavy, ensuring they are both durable and user-friendly.
Manufacturers achieve this balance through advanced manufacturing techniques and material selection. For instance, using high-strength steel alloys allows for thinner walls without compromising strength, resulting in lighter sockets that are easier to handle. Additionally, ergonomic design elements, such as streamlined shapes and smooth finishes, contribute to reduced weight and enhanced maneuverability.
Another consideration is the socket’s overall size and compatibility with various drive tools. Ensuring that the socket fits snugly onto impact drivers and wrenches is vital for effective torque transfer and minimizing the risk of tool slippage. A well-designed socket will have precise dimensions and tolerances, ensuring a secure fit across different tool types and applications.
Hex Size and Fit
Hex size and fit are fundamental aspects of impact socket design that determine their compatibility and performance with different fasteners. The hex size refers to the internal dimensions of the socket that engage with the fastener’s hexagonal head. Common hex sizes include 6-point and 12-point configurations, each offering distinct advantages.
6-point sockets provide a more robust grip on fasteners, reducing the likelihood of rounding off corners, especially under high torque conditions. They are ideal for applications requiring maximum strength and stability, such as automotive repairs and heavy machinery maintenance. The increased contact area ensures a secure fit, enhancing torque transfer efficiency and minimizing the risk of tool slippage.
12-point sockets, on the other hand, offer greater versatility and quicker engagement with fasteners, particularly in tight or confined spaces. They allow for faster socket changes and easier access to fasteners at various angles, making them suitable for general-purpose use and situations where speed and flexibility are essential. While 12-point sockets may not provide the same level of grip as 6-point sockets, their convenience and adaptability make them a popular choice for many users.
Ensuring the correct hex size and fit is crucial for maximizing the performance of impact sockets. A proper fit ensures efficient torque transfer, reducing the effort required to loosen or tighten fasteners. It also minimizes the risk of damaging both the socket and the fastener, prolonging the lifespan of your tools and ensuring consistent performance.
In summary, the design considerations of socket thickness, weight, hex size, and fit all contribute to the overall effectiveness and user experience of impact sockets. By selecting sockets with the appropriate design features, you can enhance your toolset’s performance, durability, and versatility, making your tasks more efficient and reliable.
Compatibility and Fitment
Drive Sizes and Types
Impact sockets come in various drive sizes and types, each tailored to specific applications and tool compatibility. The most common drive sizes include 1/4″, 3/8″, 1/2″, and 3/4″. Each size corresponds to different torque requirements and fastener sizes, making it essential to choose the right drive size for your needs.
1/4″ impact socket sets are ideal for light-duty applications and smaller fasteners. They are commonly used with impact drivers and ratchets for tasks like assembling furniture, installing fixtures, and working with electronics. Their compact size allows for greater maneuverability in tight spaces, making them a versatile addition to any toolset.
3/8″ impact socket sets are the most widely used and offer a balance between size and strength. They are suitable for medium-duty applications, including automotive repairs, construction, and general maintenance tasks. The 3/8″ drive size accommodates a broad range of fastener sizes, providing versatility and flexibility for various projects.
1/2″ impact socket sets are designed for heavy-duty applications that require higher torque levels. They are commonly used with larger impact wrenches and ratchets for tasks such as automotive lug nuts, industrial machinery maintenance, and construction equipment assembly. The increased drive size allows for better torque transfer and reduced strain on the tool and user.
3/4″ impact socket sets are specialized for the most demanding applications, where maximum torque and durability are essential. They are typically used in industrial settings, heavy machinery maintenance, and other high-torque tasks that require robust tools. The 3/4″ drive size provides the highest torque capacity, ensuring reliable performance under extreme conditions.
Choosing the right drive size is crucial for optimizing tool performance and ensuring compatibility with your existing tools. It also affects the ease of use, efficiency, and overall effectiveness of your impact sockets. By selecting the appropriate drive size based on your specific applications and torque requirements, you can enhance your toolset’s functionality and reliability.
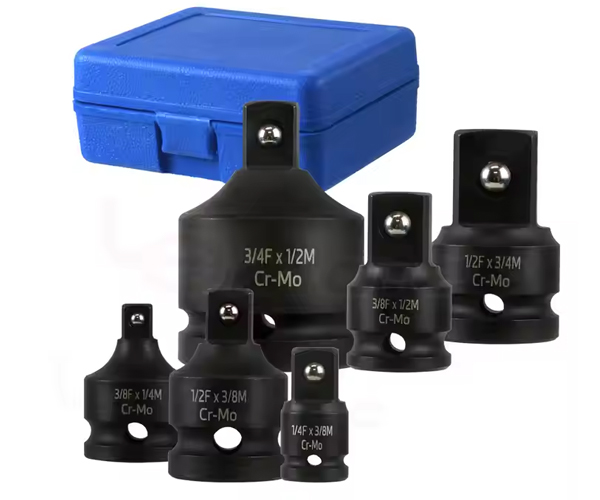
Universal vs. Specific Fit
When selecting impact sockets, understanding the difference between universal and specific fit sockets is essential for ensuring optimal performance and compatibility. Universal fit sockets are designed to accommodate a wide range of fastener sizes and types, making them versatile and convenient for various applications. They often feature flexible designs or adaptable features that allow them to fit different hex sizes and shapes, reducing the need for multiple socket sets.
Universal sockets are ideal for users who require flexibility and adaptability in their toolset. They are particularly useful in environments where different fastener types and sizes are frequently encountered, such as automotive workshops, construction sites, and maintenance facilities. The ability to adjust and fit various fasteners quickly enhances efficiency and reduces the time spent switching between different sockets.
Specific fit sockets, on the other hand, are designed to match precise fastener sizes and types. They offer a more secure and snug fit, minimizing the risk of tool slippage and fastener damage. Specific fit sockets are often used in applications where precision and reliability are paramount, such as in high-torque environments, detailed mechanical work, and specialized industries.
While universal sockets offer greater flexibility, specific fit sockets provide enhanced performance and safety in demanding applications. The choice between universal and specific fit depends on your specific needs, work environment, and the types of fasteners you commonly encounter. For users who prioritize versatility and convenience, universal sockets are an excellent choice. Conversely, those who require maximum precision and reliability in their tasks may prefer specific fit sockets.
In conclusion, both universal and specific fit impact sockets have their unique advantages and applications. By understanding the differences and selecting the appropriate type based on your requirements, you can ensure that your impact socket set meets your performance and compatibility needs effectively.
Durability and Longevity
Resistance to Wear and Tear
Durability is a paramount consideration when selecting impact sockets, as these tools are subjected to high levels of stress and impact during use. The resistance to wear and tear directly influences the socket’s lifespan and performance consistency. High-quality impact sockets are engineered to withstand repeated impacts and high torque applications without compromising their structural integrity.
Several factors contribute to a socket’s resistance to wear and tear. The type of steel used, the heat treatment process, and the overall design all play significant roles. Sockets made from premium materials like S2 steel or Chrome Vanadium are more resistant to deformation, cracking, and other forms of wear. Additionally, advanced heat treatment processes enhance the socket’s hardness and toughness, allowing it to endure prolonged use without succumbing to fatigue.
Manufacturers also implement specific design features to enhance durability. Reinforced walls, precision-machined edges, and robust coupling mechanisms ensure that the socket maintains its shape and functionality even under extreme conditions. These design elements help distribute the stress evenly across the socket, reducing the likelihood of localized wear and extending the tool’s overall lifespan.
Proper maintenance further contributes to the durability of impact sockets. Regular cleaning, proper storage, and timely inspection for signs of wear can prevent minor issues from escalating into significant problems. By taking proactive measures to care for your sockets, you can ensure they remain in optimal condition, providing reliable performance for years to come.
Corrosion Resistance
Corrosion resistance is another critical aspect that affects the longevity and performance of impact sockets. Exposure to moisture, chemicals, and varying environmental conditions can lead to rust and corrosion, compromising the socket’s integrity and functionality. High-quality impact sockets are treated with corrosion-resistant coatings to protect against these elements, ensuring they remain in excellent condition even in harsh environments.
Common corrosion-resistant coatings include chrome plating, black oxide finishes, and phosphate coatings. Chrome plating not only provides a sleek appearance but also offers a durable barrier against moisture and chemicals. Black oxide finishes enhance the socket’s resistance to rust while also reducing glare, making it easier to work in low-light conditions. Phosphate coatings improve the socket’s corrosion resistance and provide a smooth surface that facilitates better torque transfer.
In addition to protective coatings, the design of the socket itself can influence its susceptibility to corrosion. Sockets with fewer joints and seams are less prone to moisture accumulation, reducing the risk of rust formation. Precision-machined surfaces and tight tolerances also minimize gaps where corrosive agents can settle, enhancing the socket’s overall resistance to environmental factors.
Proper storage and maintenance are essential for preventing corrosion. Keeping sockets dry, using protective storage cases, and regularly applying lubricants can further protect against rust and corrosion. By combining high-quality materials, effective coatings, and diligent maintenance practices, impact sockets can achieve exceptional durability and longevity, maintaining their performance and appearance over time.
In summary, resistance to wear and tear, coupled with robust corrosion-resistant features, are fundamental to the durability and longevity of impact sockets. Investing in well-crafted sockets with these qualities ensures reliable performance, reduces the need for frequent replacements, and provides excellent value for your investment.
Performance Under Impact
Torque Handling Capabilities
One of the primary functions of impact sockets is to handle high levels of torque efficiently and safely. Torque handling capabilities are a critical factor that determines an impact socket’s performance under demanding conditions. High-quality impact sockets are designed to transfer torque from impact drivers or wrenches directly to the fastener, minimizing energy loss and maximizing efficiency.
The torque rating of an impact socket indicates the maximum torque it can handle without failure. Sockets with higher torque ratings are essential for heavy-duty applications where significant force is required to loosen or tighten stubborn fasteners. These sockets are built with robust materials and reinforced designs to withstand the intense rotational forces, ensuring they remain intact and functional even under extreme conditions.
Moreover, the design of the socket’s internal geometry plays a crucial role in torque transfer. Precision-machined internal hex sizes and optimized coupling mechanisms ensure a snug fit with the fastener, reducing slippage and enhancing torque efficiency. This design minimizes the amount of energy wasted during use, allowing for quicker and more effective fastening and unfastening.
Proper torque handling also contributes to user safety. Sockets that can reliably handle high torque levels reduce the risk of tool failure, such as socket breakage or deformation, which can lead to accidents and injuries. Additionally, efficient torque transfer means users can complete tasks more quickly and with less effort, improving overall productivity and reducing fatigue.
In conclusion, torque handling capabilities are a fundamental aspect of a good impact socket. By selecting sockets with appropriate torque ratings and optimized designs, users can ensure efficient, safe, and effective performance in a wide range of applications.
Shock Absorption Features
Shock absorption is a vital feature in impact sockets that enhances both tool performance and user safety. During the operation of impact drivers and wrenches, significant vibrations and shocks are generated, which can adversely affect both the tool and the user. Impact sockets equipped with shock absorption features are designed to mitigate these effects, ensuring smoother operation and prolonging the lifespan of both the socket and the tool.
One common shock absorption feature is the inclusion of flexible joints or dampening materials within the socket’s design. These elements help absorb and dissipate the energy generated by impacts, reducing the overall vibration transmitted to the tool and the user. This not only makes the tool more comfortable to use for extended periods but also minimizes the risk of hand fatigue and repetitive strain injuries.
Additionally, shock-absorbing designs can enhance the tool’s efficiency by preventing excessive vibrations that can interfere with torque transfer. By absorbing and redirecting the impact energy, these sockets ensure that more of the force is effectively applied to the fastener, improving the overall performance and speed of the task.
Another important aspect is the prevention of socket damage. High-impact forces can cause sockets to deform or crack over time, especially if they lack adequate shock absorption. Sockets with built-in shock absorption features are better equipped to handle repeated impacts without sustaining damage, thereby extending their operational lifespan and maintaining consistent performance.
Manufacturers achieve shock absorption through various design innovations and material enhancements. Some sockets feature reinforced structures that provide added strength and flexibility, while others incorporate specialized coatings or internal components designed to absorb impact energy. These advancements contribute to the development of impact sockets that offer superior shock resistance and durability.
In summary, shock absorption features are essential for enhancing the performance, safety, and longevity of impact sockets. By reducing vibrations and absorbing impact energy, these features make impact sockets more comfortable to use, improve torque transfer efficiency, and prevent premature tool wear and damage.
Ease of Use
Grip and Handle Design
The ease of use of impact sockets is significantly influenced by their grip and handle design. Ergonomic features that enhance grip comfort and control are essential for ensuring that users can work efficiently and safely, especially during prolonged or demanding tasks. High-quality impact sockets are designed with user comfort in mind, incorporating features that reduce hand fatigue and improve maneuverability.
Non-slip grips are a common design element that enhances user control and safety. These grips are often made from materials like rubber or textured coatings that provide a firm hold, even in wet or greasy conditions. A secure grip prevents the socket from slipping during use, reducing the risk of accidents and ensuring precise torque application.
Ergonomic handle designs also play a crucial role in user comfort. Sockets with contoured or angled handles allow for better hand positioning and reduce strain on the wrists and fingers. This is particularly important when working in tight or awkward spaces where maintaining a comfortable grip can be challenging. Ergonomic designs enable users to apply force more effectively, enhancing both comfort and performance.
Additionally, lightweight construction contributes to ease of use by reducing the overall weight of the socket set. Lighter sockets are easier to handle and maneuver, making them ideal for tasks that require extended use or repetitive movements. This not only improves user comfort but also enhances productivity by allowing for quicker and more efficient operations.
Some impact sockets feature additional design innovations, such as swivel heads or quick-release mechanisms, which further enhance usability. Swivel heads provide greater flexibility and access in confined spaces, while quick-release mechanisms allow for rapid socket changes without the need for additional tools. These features streamline the workflow and reduce downtime, making impact sockets more efficient and user-friendly.
In summary, grip and handle design are critical factors that determine the ease of use of impact sockets. By incorporating ergonomic features, non-slip materials, and innovative design elements, manufacturers create impact sockets that offer superior comfort, control, and efficiency, enhancing the overall user experience.
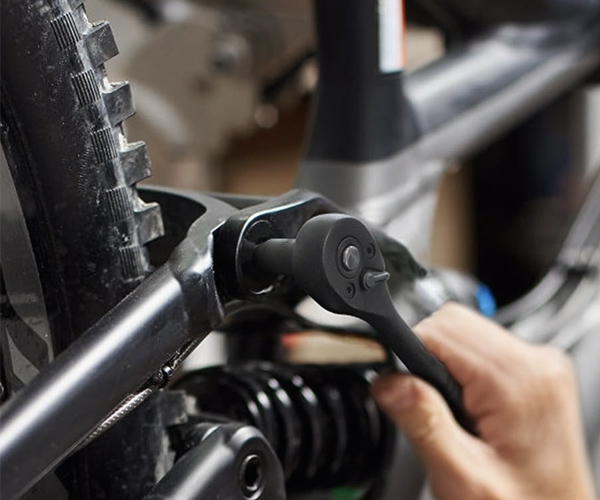
Quick-Release Mechanisms
Quick-release mechanisms are a valuable feature in impact sockets that enhance efficiency and convenience during use. These mechanisms allow users to rapidly change sockets without the need for additional tools, significantly speeding up the workflow and reducing downtime. High-quality impact sockets often incorporate quick-release features to improve their functionality and user experience.
The primary advantage of quick-release mechanisms is the ability to switch between different socket sizes and types swiftly. In environments where time is of the essence, such as automotive repair shops or construction sites, the ability to change sockets quickly can lead to significant productivity gains. Instead of manually unscrewing and attaching sockets, users can simply engage the quick-release feature to swap sockets effortlessly, maintaining a steady workflow.
Quick-release mechanisms also contribute to better tool management and organization. By reducing the time and effort required to change sockets, these features encourage users to keep their toolsets well-organized and readily accessible. This leads to a more streamlined and efficient work environment, where the right socket is always within reach when needed.
Moreover, quick-release mechanisms enhance the overall versatility of impact sockets. They allow users to adapt to varying task requirements without interrupting their workflow. Whether switching between different drive sizes, hex configurations, or specialized sockets, the quick-release feature provides the flexibility needed to handle diverse applications effectively.
From a safety perspective, quick-release mechanisms also minimize the risk of tool slippage or damage. Manual socket changes can sometimes result in forced adjustments or improper fittings, leading to socket deformation or tool wear. Quick-release features ensure that sockets are securely attached and aligned correctly, reducing the likelihood of accidents and maintaining the integrity of both the socket and the tool.
In conclusion, quick-release mechanisms are a beneficial feature that enhances the functionality and efficiency of impact sockets. By enabling rapid socket changes, improving tool management, and increasing versatility, these mechanisms contribute to a more productive and user-friendly experience, making them an essential aspect of high-quality impact sockets.
Compatibility with Tools
Impact Drivers vs. Ratchets
Understanding the compatibility of impact sockets with different tools, such as impact drivers and ratchets, is essential for maximizing their effectiveness and longevity. Impact drivers and ratchets are both commonly used tools that deliver high torque output, but they operate differently and require specific socket designs to perform optimally.
Impact drivers are designed to deliver rapid, high-torque impacts in a rotational manner, making them ideal for loosening or tightening stubborn fasteners quickly. They use concussive blows to break free rusted or tightly secured bolts, providing efficiency and speed in tasks that require significant torque. Impact sockets used with impact drivers must be robust and capable of handling these high-impact forces without deforming or breaking.
Ratchets, on the other hand, are manually operated tools that provide controlled torque application. They allow for precise tightening and loosening of fasteners, making them suitable for tasks that require accuracy and finesse. Impact sockets used with ratchets should still be durable but may not need to withstand the same level of impacts as those used with impact drivers.
The key difference lies in the design and construction of the sockets. Impact sockets are specifically engineered to handle the high torque and impacts delivered by impact drivers. They often feature thicker walls, reinforced corners, and robust coupling mechanisms to withstand the intense forces and prevent socket deformation or failure. Ratchet sockets, while still durable, are generally designed for lower torque applications and may not offer the same level of reinforcement.
Using the appropriate socket with the right tool is crucial for maintaining tool integrity and ensuring safe and efficient operations. Impact sockets used with impact drivers provide the necessary strength and durability to handle high-torque tasks, while ratchet sockets offer the precision and control needed for more delicate applications. Mixing and matching sockets with incompatible tools can lead to reduced performance, increased wear and tear, and potential safety hazards.
In summary, selecting the correct impact socket based on the tool you are using—whether an impact driver or a ratchet—ensures optimal performance, durability, and safety. By understanding the specific requirements of each tool, users can make informed decisions and enhance their overall toolset’s effectiveness.
Versatility Across Applications
Impact sockets are renowned for their versatility, making them indispensable in various industries and applications. Their ability to handle high torque and withstand impacts makes them suitable for a wide range of tasks, from automotive repairs and construction to heavy machinery maintenance and DIY projects. Understanding the versatility of impact sockets can help users maximize their toolset’s potential and apply these sockets effectively across different scenarios.
In the automotive industry, impact sockets are essential for tasks such as removing lug nuts, engine components, and suspension parts. Their high-torque capabilities allow mechanics to work efficiently, even with stubborn or rusted fasteners. Impact sockets ensure that automotive repairs are completed quickly and effectively, minimizing downtime and enhancing productivity.
In construction, impact sockets are used for assembling and disassembling structures, fastening building materials, and maintaining equipment. Their durability and strength make them ideal for handling the rigorous demands of construction sites, where tools are frequently subjected to heavy use and harsh conditions. Impact sockets contribute to the overall efficiency and reliability of construction projects, ensuring that fasteners are securely tightened and maintained.
Heavy machinery maintenance also benefits from the versatility of impact sockets. These tools are used to service and repair equipment such as excavators, bulldozers, and industrial machines, where high torque and precision are required. Impact sockets ensure that fasteners are tightened to the correct specifications, preventing equipment failures and ensuring operational safety.
DIY enthusiasts find impact sockets equally valuable for a variety of home improvement and repair tasks. From assembling furniture and installing fixtures to working on personal vehicles and outdoor equipment, impact sockets provide the necessary strength and efficiency to complete projects effectively. Their versatility allows users to tackle a broad spectrum of tasks with confidence and ease.
Furthermore, impact sockets are adaptable to different tool types and configurations. They can be used with impact drivers, wrenches, and ratchets, enhancing their functionality and making them suitable for diverse applications. This adaptability ensures that users can rely on a single set of impact sockets for multiple tasks, simplifying tool management and reducing the need for extensive tool inventories.
In conclusion, the versatility of impact sockets makes them a valuable addition to any toolset, capable of handling a wide range of applications across various industries. Their ability to adapt to different tools and tasks ensures that users can perform their work efficiently and effectively, maximizing the utility and performance of their impact socket sets.
Brand Reputation and Reviews
Choosing Trusted Brands
When investing in impact sockets, selecting products from trusted and reputable brands is essential for ensuring quality, durability, and performance. Established brands have a proven track record of manufacturing reliable tools that meet industry standards and user expectations. They invest in research and development, employ skilled engineers, and adhere to stringent quality control measures to produce high-quality impact sockets.
Trusted brands often offer warranties and customer support, providing additional assurance of their products’ reliability. These brands are more likely to use premium materials and advanced manufacturing techniques, resulting in impact sockets that can withstand heavy use and high torque applications without compromising their integrity. By choosing trusted brands, users can minimize the risk of tool failure, reduce the need for frequent replacements, and enjoy consistent performance over time.
Furthermore, reputable brands are more likely to stay updated with the latest technological advancements and industry trends. They continuously improve their product lines to incorporate innovative features, such as enhanced shock absorption, quick-release mechanisms, and ergonomic designs. This commitment to innovation ensures that users have access to the best tools available, enhancing their overall work experience and efficiency.
Another advantage of selecting trusted brands is the availability of a wide range of products and sizes. Established brands offer comprehensive impact socket sets that cater to various needs and applications, making it easier for users to find the right tools for their specific tasks. This extensive product range allows users to build a versatile and reliable toolset without compromising on quality or performance.
In addition to product quality, trusted brands are known for their ethical business practices and commitment to customer satisfaction. They prioritize building long-term relationships with their customers by delivering on their promises and addressing any issues promptly and effectively. This focus on customer satisfaction fosters loyalty and trust, ensuring that users can rely on their chosen brand for future tool purchases.
In summary, choosing impact sockets from trusted brands ensures access to high-quality, durable, and reliable tools that meet diverse needs and applications. The reputation, innovation, and customer-centric approach of established brands provide users with the confidence and assurance that their investment in impact sockets will deliver consistent performance and long-term value.
Reading and Interpreting Reviews
Reading and interpreting reviews is a valuable practice when selecting impact sockets, as it provides insights into the real-world performance and reliability of the tools. User reviews offer firsthand experiences and feedback that can help potential buyers make informed decisions, ensuring they choose impact sockets that meet their specific needs and expectations.
When evaluating reviews, it’s important to consider both positive and negative feedback to gain a balanced perspective. Positive reviews often highlight the strengths of the impact sockets, such as durability, ease of use, and effective torque transfer. These reviews can confirm the reliability and performance of the sockets, reinforcing their suitability for various applications.
Negative reviews, on the other hand, can reveal potential drawbacks or issues that may not be apparent from product descriptions alone. Common concerns may include socket breakage, poor fitment, or dissatisfaction with customer service. By understanding these limitations, users can make more informed choices and select impact sockets that address their specific concerns and requirements.
It’s also beneficial to look for detailed and specific reviews that provide comprehensive insights into the product’s performance in different scenarios. Reviews that include information about the socket’s performance under heavy use, compatibility with various tools, and longevity offer valuable information that can guide purchasing decisions. Additionally, reviews from users with similar needs or applications can be particularly relevant and helpful.
Comparing reviews across different platforms and sources can further enhance the reliability of the feedback. Checking reviews on multiple websites, forums, and social media channels can help identify consistent patterns and trends in user experiences. This comprehensive approach ensures that users have a well-rounded understanding of the impact sockets’ performance and reliability.
Moreover, considering the overall rating and the number of reviews can provide a general indication of the product’s popularity and acceptance among users. Products with high ratings and a substantial number of reviews are often more reliable choices, as they have been tested and validated by a larger user base.
In conclusion, reading and interpreting reviews is a crucial step in selecting the best impact sockets. By carefully evaluating user feedback and considering both positive and negative aspects, users can make informed decisions that align with their specific needs and preferences, ensuring they invest in impact sockets that deliver exceptional performance and value.
Cost vs. Quality
Balancing Budget with Performance
When selecting impact sockets, striking the right balance between cost and quality is essential for maximizing value without compromising performance. While it’s tempting to opt for the cheapest available options, this approach can lead to long-term issues such as tool failure, frequent replacements, and decreased efficiency. On the other hand, exclusively focusing on high-end, expensive impact sockets may not be necessary for all users, especially those with moderate usage needs.
Finding the optimal balance involves evaluating the intended use, frequency of use, and specific requirements of your tasks. For heavy-duty applications and professional use, investing in higher-quality impact sockets may be justified due to their superior durability and performance. These sockets are designed to withstand frequent use and high torque applications, offering long-term reliability and reducing the need for costly replacements.
For occasional or light-duty use, mid-range or budget-friendly impact sockets can provide adequate performance without breaking the bank. These sockets may not offer the same level of durability as premium options, but they can still deliver reliable performance for less demanding tasks. By assessing your specific needs and usage patterns, you can determine the appropriate level of investment that aligns with your budget and performance expectations.
Another factor to consider is the overall value proposition of the impact sockets. Higher-quality sockets may come with additional features such as enhanced shock absorption, quick-release mechanisms, and ergonomic designs that can improve user experience and efficiency. These added benefits can justify the higher cost by providing greater functionality and ease of use, ultimately enhancing productivity and reducing user fatigue.
Additionally, purchasing impact sockets from reputable brands often ensures better quality and longer lifespan, offering better value over time despite the higher initial cost. Trusted brands are more likely to provide warranties and customer support, offering peace of mind and protection against defects or issues that may arise.
In summary, balancing budget with performance requires a thoughtful evaluation of your specific needs, usage patterns, and the value offered by different impact socket options. By carefully considering these factors, you can make informed decisions that optimize both cost and quality, ensuring you invest in impact sockets that deliver the best possible performance for your budget.
Long-Term Savings Through Quality
Investing in high-quality impact sockets may involve a higher initial cost, but it often leads to significant long-term savings and enhanced productivity. Quality impact sockets are designed to endure extensive use without compromising their performance, reducing the need for frequent replacements and repairs. This durability translates into cost savings over time, as users do not have to continually replace worn-out or broken sockets, which can add up quickly.
High-quality sockets also contribute to improved efficiency and productivity. Reliable tools perform consistently, allowing users to complete tasks more quickly and with less effort. This efficiency can lead to faster project completion times, increased output, and the ability to take on more work without sacrificing quality. For professionals, this can mean higher earnings and greater job satisfaction, as they can rely on their tools to meet the demands of their work without interruption.
Additionally, quality impact sockets often come with better warranties and customer support, providing added protection and assurance. These warranties can cover defects or issues that may arise, offering free replacements or repairs and further reducing the long-term costs associated with tool maintenance. Investing in reputable brands that stand behind their products ensures that users receive reliable support and value for their investment.
Another aspect of long-term savings is the reduction in downtime caused by tool failure or malfunction. High-quality impact sockets are less likely to break or wear out under heavy use, ensuring that users can rely on their tools to perform when needed. This reliability minimizes interruptions in workflow, allowing for smoother operations and less time wasted dealing with tool issues.
Moreover, quality impact sockets often feature advanced design elements and superior materials that enhance their performance and longevity. These features not only improve the tool’s effectiveness but also extend its useful life, providing more value for the initial investment. Users can enjoy consistent performance and durability over an extended period, maximizing the return on their investment.
In conclusion, investing in high-quality impact sockets offers substantial long-term savings by reducing replacement costs, enhancing productivity, and minimizing downtime. The durability, reliability, and performance of quality sockets ensure that users receive excellent value for their investment, making it a wise choice for both professionals and DIY enthusiasts looking to optimize their toolsets.
OEM Customization Capabilities
Benefits of Customization
OEM (Original Equipment Manufacturer) customization capabilities offer significant advantages for businesses and users seeking tailored impact socket solutions. Customization allows for the creation of impact sockets that meet specific requirements, enhance brand identity, and improve overall functionality, providing a competitive edge in various applications and markets.
One of the primary benefits of customization is the ability to tailor impact sockets to meet precise specifications and requirements. Businesses can specify unique features such as socket size, material composition, and design elements that align with their specific needs. This level of customization ensures that the impact sockets perform optimally in their intended applications, enhancing efficiency and reliability.
Customization also allows businesses to differentiate their products in the market, strengthening their brand identity and recognition. By incorporating unique design elements, colors, engravings, or packaging solutions, businesses can create impact sockets that stand out from generic offerings. This differentiation not only enhances the aesthetic appeal of the tools but also reinforces the brand’s commitment to quality and innovation, attracting customers and building loyalty.
Moreover, OEM customization enables the development of specialized impact sockets for niche applications. Businesses operating in specific industries or handling unique tasks can benefit from customized sockets designed to address their particular challenges and requirements. This specialization can lead to improved performance, increased customer satisfaction, and a stronger market presence.
Customization also provides flexibility in responding to changing market demands and technological advancements. Businesses can collaborate with manufacturers to incorporate new features, materials, or designs into their impact sockets, ensuring that their products remain competitive and relevant. This adaptability is crucial in dynamic markets where innovation and responsiveness are key to maintaining a competitive advantage.
Furthermore, OEM customization can enhance the overall user experience by incorporating features that improve comfort, safety, and ease of use. Custom designs can include ergonomic grips, quick-release mechanisms, or enhanced shock absorption, making impact sockets more user-friendly and efficient. These enhancements contribute to increased productivity and reduced user fatigue, benefiting both the business and its customers.
In summary, OEM customization capabilities offer numerous benefits, including tailored performance, enhanced brand identity, specialization for niche applications, flexibility in innovation, and improved user experience. By leveraging customization, businesses can create impact sockets that meet their specific needs, differentiate their products in the market, and deliver exceptional value to their customers.
Process of Customizing Impact Sockets
The process of customizing impact sockets involves several key steps that ensure the final product meets the specific requirements and expectations of the business or user. Understanding this process is essential for effectively collaborating with manufacturers and achieving the desired customization outcomes.
1. Identifying Requirements: The first step in customizing impact sockets is clearly defining the requirements and objectives. This involves determining the specific features, materials, sizes, and design elements needed to meet the intended applications. Businesses should consider factors such as torque requirements, fastener sizes, environmental conditions, and any unique specifications that differentiate their impact sockets from standard offerings.
2. Selecting a Manufacturer: Choosing a reliable OEM manufacturer is crucial for successful customization. Businesses should research and evaluate potential manufacturers based on their expertise, reputation, capabilities, and previous experience with similar customization projects. Selecting a manufacturer with a proven track record and a commitment to quality ensures that the customized impact sockets will meet the desired standards.
3. Collaboration and Design Development: Once a manufacturer is selected, the next step involves collaborating on the design development. This includes providing detailed specifications, design drawings, and any specific requirements for the impact sockets. Manufacturers may offer design consultations and suggestions to optimize the design for performance, durability, and manufacturability. This collaborative approach ensures that the final design aligns with the business’s needs and objectives.
4. Prototyping and Testing: After the initial design is developed, the manufacturer typically creates prototypes for testing and evaluation. Prototyping allows businesses to assess the functionality, performance, and quality of the customized impact sockets before proceeding with full-scale production. Testing may involve evaluating torque handling, durability, fitment, and other critical performance metrics to ensure that the sockets meet the specified requirements.
5. Refinement and Finalization: Based on the feedback from testing, the design may undergo refinements and adjustments to address any issues or enhance performance. This iterative process ensures that the final product is optimized for its intended use and meets the highest quality standards. Once the design is finalized, the manufacturer proceeds with full-scale production, adhering to the agreed-upon specifications and quality control measures.
6. Production and Quality Assurance: During production, stringent quality assurance protocols are implemented to ensure that each customized impact socket meets the defined standards. This includes regular inspections, testing, and adherence to manufacturing best practices. Quality assurance ensures consistency, reliability, and performance across all customized impact sockets.
7. Delivery and Support: After production, the customized impact sockets are delivered to the business, often accompanied by warranties and customer support. Ongoing support from the manufacturer ensures that any issues or adjustments can be addressed promptly, maintaining the quality and performance of the impact sockets over time.
In conclusion, the process of customizing impact sockets involves careful planning, collaboration, design development, prototyping, testing, refinement, production, and quality assurance. By following these steps and working closely with a reliable OEM manufacturer, businesses can achieve customized impact sockets that meet their specific needs, enhance their brand identity, and deliver exceptional performance and value.
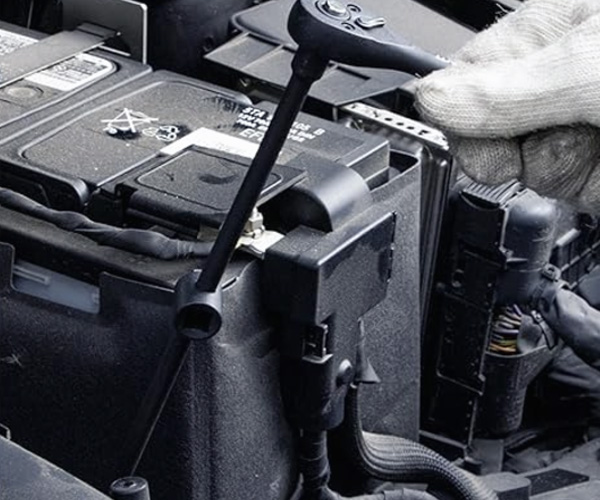
Safety Features
Anti-Slip Technologies
Safety is a paramount concern when using impact sockets, given the high torque and impact forces involved in their operation. Anti-slip technologies are essential safety features that enhance control, reduce the risk of tool slippage, and prevent accidents during use. High-quality impact sockets incorporate various anti-slip technologies to ensure secure and efficient torque application, protecting both the user and the tool.
One common anti-slip feature is the use of textured or coated surfaces on the socket’s interior and exterior. Textured surfaces provide better grip between the socket and the fastener, minimizing the likelihood of slippage during high-torque applications. Coatings such as black oxide or chrome plating not only offer corrosion resistance but also improve the socket’s grip, enhancing safety and performance.
Another anti-slip technology is the inclusion of reinforced coupling mechanisms. These mechanisms ensure a tight and secure fit between the socket and the impact driver or ratchet, reducing the chances of the socket slipping or disengaging during use. A secure coupling is critical for maintaining control and ensuring efficient torque transfer, preventing tool slippage and potential injuries.
Additionally, some impact sockets feature built-in locking mechanisms or retention clips that hold the socket firmly in place on the tool. These features provide an extra layer of security, ensuring that the socket remains attached even under extreme torque conditions. Locking mechanisms help prevent accidental socket changes and reduce the risk of the socket flying off during use, enhancing overall safety.
Ergonomic design elements also contribute to anti-slip safety features. Sockets with ergonomic grips or handles that offer a firm and comfortable hold allow users to maintain better control over the tool, reducing the risk of accidental slips or drops. Ergonomic designs ensure that the user can apply force more effectively and with greater precision, enhancing both safety and efficiency.
Incorporating anti-slip technologies in impact sockets not only improves safety but also enhances performance and user confidence. Users can work more comfortably and efficiently, knowing that their tools are designed to minimize slippage and provide a secure grip, even in challenging conditions.
In summary, anti-slip technologies are critical safety features that enhance the control, reliability, and safety of impact sockets. By reducing the risk of tool slippage and improving grip, these technologies protect users from accidents and injuries while ensuring efficient and effective torque application.
Protective Coatings and Finishes
Protective coatings and finishes play a significant role in enhancing the safety and durability of impact sockets. These coatings provide a barrier against environmental factors such as moisture, chemicals, and abrasion, protecting the socket’s surface and maintaining its integrity under demanding conditions. High-quality impact sockets often feature advanced protective coatings that contribute to their overall safety and performance.
One of the most common protective coatings is chrome plating. Chrome plating offers excellent corrosion resistance, preventing rust and degradation caused by exposure to moisture and chemicals. This coating not only protects the socket but also provides a smooth surface that facilitates easy torque transfer. Additionally, chrome plating enhances the socket’s appearance, giving it a sleek and professional finish.
Black oxide finishes are another popular protective coating used on impact sockets. Black oxide provides effective corrosion resistance while also reducing glare, making it easier to work in low-light conditions. This finish enhances the socket’s durability by protecting it from rust and wear, ensuring consistent performance over time. Black oxide coatings also contribute to the socket’s grip, improving user control and reducing the risk of slippage.
Phosphate coatings are used to enhance the socket’s surface hardness and provide additional corrosion protection. This type of coating creates a rougher surface that improves the socket’s grip on fasteners, reducing the likelihood of tool slippage and enhancing torque transfer efficiency. Phosphate coatings also act as a lubricant, minimizing friction and wear during use, which extends the socket’s lifespan and maintains its performance.
Cerakote coatings offer advanced protection by providing a hard, wear-resistant surface that withstands high-impact forces and abrasive conditions. This ceramic-based coating is highly durable, offering superior protection against scratches, dents, and corrosion. Cerakote finishes are ideal for impact sockets used in harsh environments, where maximum protection and longevity are required.
In addition to corrosion resistance, protective coatings and finishes enhance the socket’s safety by preventing surface defects and maintaining structural integrity. By safeguarding the socket against environmental damage and wear, these coatings ensure that the socket remains reliable and safe to use, even under extreme conditions.
Proper maintenance of protective coatings is essential for sustaining their protective properties. Regular cleaning and proper storage help preserve the integrity of the coatings, ensuring that the impact sockets continue to perform safely and effectively over time.
In conclusion, protective coatings and finishes are essential safety features that enhance the durability, corrosion resistance, and overall performance of impact sockets. By providing a robust barrier against environmental factors and wear, these coatings ensure that impact sockets remain safe, reliable, and efficient tools for a wide range of applications.
Maintenance and Care
Proper Cleaning Techniques
Maintaining impact sockets through proper cleaning techniques is essential for ensuring their longevity, performance, and safety. Regular cleaning removes dirt, grease, debris, and corrosive substances that can accumulate during use, preventing wear and corrosion and maintaining the socket’s functionality. Implementing effective cleaning practices helps preserve the quality of impact sockets, ensuring they remain reliable and efficient over time.
One of the most effective cleaning methods for impact sockets involves using solvents or degreasers to remove stubborn grease and grime. Applying a high-quality solvent to the socket’s surface and allowing it to penetrate can help dissolve and lift away built-up contaminants. After applying the solvent, using a wire brush or abrasive pad to scrub the socket gently can further remove any remaining residue. Rinsing the socket with clean water or wiping it with a dry cloth ensures that all cleaning agents are removed, preventing any potential damage from leftover chemicals.
For impact sockets with corrosion-resistant coatings, it is important to avoid abrasive cleaning tools that can scratch or damage the protective surface. Instead, using soft-bristle brushes, microfiber cloths, or non-abrasive pads can effectively clean the sockets without compromising their protective coatings. This approach helps maintain the socket’s corrosion resistance and overall integrity.
Drying the sockets thoroughly after cleaning is crucial to prevent moisture from causing rust and corrosion. Using compressed air to blow out any remaining moisture or placing the sockets in a dry environment ensures that they are completely dry before storage. Applying a light coating of oil or a protective lubricant can provide an additional layer of protection against moisture and corrosion, further enhancing the socket’s durability.
Regular inspection during the cleaning process allows users to identify any signs of wear, damage, or corrosion early on. Detecting and addressing these issues promptly can prevent minor problems from escalating into significant damage, ensuring that the impact sockets remain in optimal condition.
In addition to manual cleaning, using cleaning tools such as ultrasonic cleaners can provide a thorough and efficient cleaning process. Ultrasonic cleaners use high-frequency sound waves to agitate the cleaning solution, effectively removing contaminants from the socket’s surface and internal passages. This method ensures a deep and comprehensive clean, enhancing the socket’s performance and lifespan.
In summary, proper cleaning techniques are essential for maintaining the quality, performance, and safety of impact sockets. By implementing effective cleaning methods, avoiding abrasive tools, ensuring thorough drying, and conducting regular inspections, users can preserve their impact sockets in excellent condition, ensuring reliable performance and extended tool lifespan.
Storage Solutions to Prevent Damage
Proper storage of impact sockets is crucial for preventing damage, maintaining their condition, and ensuring easy access when needed. Effective storage solutions protect sockets from environmental factors, reduce the risk of loss or misplacement, and enhance tool organization, contributing to overall toolset efficiency and longevity.
One of the most effective storage solutions is using a dedicated socket organizer or case. These organizers are designed with individual compartments or slots for each socket, preventing them from clanging together and causing dents or scratches. A well-organized socket case allows users to easily locate and access the required socket, streamlining workflow and reducing time spent searching for tools.
Toolboxes with customizable trays or inserts offer another excellent storage option for impact sockets. These trays can be adjusted to fit various socket sizes and types, providing flexibility and adaptability for different toolsets. The adjustable nature of these trays ensures that impact sockets are stored securely and can be easily rearranged as needed, accommodating changes in socket collections or tool requirements.
Magnetic tool holders and wall-mounted storage systems provide convenient and accessible storage solutions for impact sockets. Magnetic holders allow sockets to be stored visibly and within easy reach, facilitating quick selection and reducing the risk of misplacement. Wall-mounted storage systems, such as pegboards or slatwall organizers, keep impact sockets organized and accessible, optimizing workspace efficiency and reducing clutter.
Proper storage environments are also essential for maintaining the condition of impact sockets. Storing sockets in a dry, temperature-controlled environment helps prevent rust and corrosion, preserving their integrity and performance. Avoiding exposure to extreme temperatures, moisture, and direct sunlight ensures that impact sockets remain in optimal condition, free from damage and degradation.
Using protective storage accessories, such as socket covers or sleeves, can provide additional protection against dust, debris, and environmental factors. These accessories shield sockets from contaminants, reducing the need for frequent cleaning and maintenance. Additionally, socket covers can help prevent accidental damage or deformation during storage, maintaining the socket’s shape and functionality.
Labeling storage compartments or cases can further enhance organization and efficiency. Clearly labeling each compartment with the corresponding socket size or type allows for easy identification and quick access, reducing the time spent searching for specific sockets and improving overall productivity.
In summary, implementing effective storage solutions is essential for preventing damage, maintaining the condition, and enhancing the organization of impact sockets. By using dedicated organizers, customizable toolboxes, magnetic holders, and maintaining proper storage environments, users can ensure their impact sockets remain in excellent condition, ready for reliable performance whenever needed.
Innovation and Technological Advancements
Latest Trends in Impact Socket Design
The impact socket industry is continually evolving, driven by advancements in materials, manufacturing processes, and design innovations. These latest trends in impact socket design enhance performance, durability, and user experience, ensuring that impact sockets remain essential tools for professionals and DIY enthusiasts alike.
One of the significant trends in impact socket design is the use of advanced materials. Manufacturers are increasingly incorporating high-strength alloys like S2 steel and chrome vanadium into their socket designs to improve durability and torque handling capabilities. These materials offer superior resistance to wear and deformation, allowing impact sockets to withstand high-torque applications and heavy use without compromising their integrity.
Another notable trend is the development of ergonomic designs that enhance user comfort and control. Impact sockets now feature contoured grips, textured surfaces, and balanced weights that reduce hand fatigue and improve maneuverability. Ergonomic designs ensure that users can apply torque more effectively and with greater precision, enhancing overall efficiency and reducing the risk of repetitive strain injuries.
Innovative coupling mechanisms are also gaining popularity in impact socket designs. These mechanisms provide a more secure and stable connection between the socket and the impact driver or ratchet, minimizing the risk of slippage and ensuring efficient torque transfer. Quick-release features and advanced locking systems allow for faster socket changes and greater flexibility, streamlining workflow and enhancing productivity.
The integration of modular designs is another emerging trend in impact socket design. Modular sockets consist of interchangeable components, allowing users to customize and adapt their socket sets to meet specific needs and applications. This flexibility enables users to expand their toolsets without investing in multiple socket sets, providing cost-effective and versatile solutions for various tasks.
Additionally, manufacturers are focusing on enhancing the visual and functional aspects of impact sockets through innovative finishes and coatings. Protective coatings like Cerakote and advanced black oxide finishes offer superior corrosion resistance, improved grip, and a sleek appearance. These finishes not only protect the socket from environmental factors but also contribute to a more professional and aesthetically pleasing toolset.
Smart technology integration is another frontier in impact socket innovation. Some manufacturers are exploring the incorporation of sensors and digital interfaces that provide real-time feedback on torque levels, socket performance, and tool health. These smart sockets offer enhanced precision and control, allowing users to monitor and optimize their tool usage for better results and reduced wear.
In summary, the latest trends in impact socket design focus on using advanced materials, enhancing ergonomics, innovating coupling mechanisms, adopting modular designs, improving finishes and coatings, and integrating smart technology. These innovations drive the evolution of impact sockets, ensuring they remain powerful, durable, and user-friendly tools that meet the ever-changing demands of various industries and applications.
Future of Impact Sockets
The future of impact sockets promises continued advancements and innovations that will further enhance their performance, durability, and versatility. As technology evolves and user needs become more sophisticated, impact sockets will adapt to meet these demands, offering new features and improvements that set the standard for high-quality tools.
One anticipated development in the future of impact sockets is the integration of smart technology. Smart sockets equipped with sensors and digital interfaces could provide real-time feedback on torque levels, socket usage, and maintenance needs. This data-driven approach allows users to monitor and optimize their tool usage, enhancing precision and efficiency while preventing overuse and wear. Additionally, smart sockets could communicate with other smart tools and devices, creating a connected ecosystem that streamlines workflows and enhances productivity.
Another promising trend is the advancement of materials and manufacturing processes. Continued research into high-strength alloys and innovative composites will result in impact sockets that are even more durable, lightweight, and resistant to wear and corrosion. Advanced manufacturing techniques, such as 3D printing and precision machining, will enable the creation of complex designs and features that enhance socket performance and user experience.
Ergonomic and user-centric design will remain a key focus in the future of impact sockets. Manufacturers will continue to refine socket shapes, grips, and weight distributions to improve comfort, control, and ease of use. Enhanced ergonomic designs will reduce user fatigue, increase efficiency, and make impact sockets more accessible to a broader range of users, including those with specific ergonomic needs.
Sustainability and eco-friendly practices will also influence the future of impact sockets. Manufacturers are increasingly adopting sustainable materials and environmentally friendly production methods to reduce their ecological footprint. Impact sockets designed with recyclability and longevity in mind will become more prevalent, catering to environmentally conscious users and industries committed to sustainable practices.
Customization and modularity will continue to evolve, offering users even greater flexibility and adaptability in their toolsets. Future impact sockets may feature more advanced modular designs, allowing for easy adjustments and expansions to accommodate diverse applications and preferences. This level of customization ensures that users can tailor their impact socket sets to meet specific needs, enhancing their overall functionality and efficiency.
Furthermore, advancements in coating and finishing technologies will result in impact sockets with superior protection and performance. New coatings that offer enhanced corrosion resistance, improved grip, and reduced friction will become standard features, ensuring that impact sockets remain reliable and effective in various environments and conditions.
In summary, the future of impact sockets is poised for significant advancements driven by smart technology integration, material innovations, ergonomic design improvements, sustainability initiatives, enhanced customization, and superior coating technologies. These developments will ensure that impact sockets continue to evolve as essential tools, meeting the changing needs of users and maintaining their position as indispensable components of any toolset.
Environmental Considerations
Sustainable Manufacturing Practices
Sustainable manufacturing practices are becoming increasingly important in the production of impact sockets, reflecting a growing commitment to environmental responsibility and resource efficiency. Manufacturers are adopting eco-friendly processes and materials to minimize their environmental impact, ensuring that the production of impact sockets aligns with global sustainability goals.
One of the primary aspects of sustainable manufacturing is the use of recycled and recyclable materials. By incorporating recycled steel and other materials into the production process, manufacturers reduce the need for virgin resources, decreasing the overall environmental footprint. Recyclable materials ensure that impact sockets can be repurposed or recycled at the end of their lifecycle, promoting a circular economy and reducing waste.
Energy-efficient manufacturing processes are another critical component of sustainable practices. Manufacturers are investing in advanced technologies and optimizing production workflows to minimize energy consumption and reduce greenhouse gas emissions. Energy-efficient processes not only lower operational costs but also contribute to the broader effort to combat climate change and environmental degradation.
Water conservation and waste reduction are also key elements of sustainable manufacturing. Implementing water-efficient systems and recycling water used in the production process helps preserve this vital resource and reduce the environmental impact. Additionally, minimizing waste through improved material handling, recycling scrap materials, and reducing packaging waste ensures that manufacturing operations are more environmentally friendly.
Manufacturers are also focusing on reducing the use of hazardous substances and implementing safer chemical processes. By opting for non-toxic and environmentally benign chemicals in coatings and treatments, they minimize the release of harmful pollutants into the environment. This approach not only protects the ecosystem but also ensures a safer working environment for employees.
Eco-friendly packaging is another area where sustainable practices are being adopted. Using recyclable or biodegradable packaging materials reduces the environmental impact of product distribution and disposal. Manufacturers are increasingly designing packaging that minimizes material usage while still providing adequate protection for impact sockets during shipping and handling.
Furthermore, sustainable manufacturing practices extend to product design and lifecycle management. Designing impact sockets for longevity and durability reduces the need for frequent replacements, decreasing overall resource consumption. Additionally, offering repair and refurbishment services allows for the extension of the tool’s lifecycle, promoting sustainability and reducing waste.
In summary, sustainable manufacturing practices in the production of impact sockets encompass the use of recycled and recyclable materials, energy-efficient processes, water conservation, waste reduction, safer chemical practices, eco-friendly packaging, and lifecycle management. By embracing these practices, manufacturers contribute to environmental sustainability, ensuring that impact sockets are produced responsibly and with minimal impact on the planet.
Recyclability and End-of-Life Disposal
Recyclability and responsible end-of-life disposal are critical considerations in the lifecycle of impact sockets, contributing to environmental sustainability and resource conservation. As essential tools with long usage periods, impact sockets must be managed properly at the end of their lifecycle to minimize environmental impact and promote recycling and reuse.
Impact sockets are primarily made from steel alloys such as Chrome Vanadium and S2 steel, both of which are highly recyclable materials. Steel is one of the most recycled metals globally, with a well-established recycling infrastructure that ensures efficient processing and reuse. When impact sockets reach the end of their useful life, they can be collected and sent to recycling facilities where the steel is melted down and repurposed for new products, reducing the demand for virgin materials and conserving natural resources.
Manufacturers play a vital role in facilitating the recyclability of impact sockets by designing products with end-of-life recycling in mind. This includes using materials that are easily recyclable, avoiding the use of non-recyclable components or coatings that hinder the recycling process, and providing clear instructions on how to properly dispose of or recycle the sockets. Some manufacturers may also offer take-back programs or partnerships with recycling centers, encouraging users to return old sockets for responsible recycling.
Proper disposal of impact sockets is essential for preventing environmental contamination and reducing waste. Users should avoid disposing of impact sockets in regular trash or landfills, where they can contribute to metal waste and environmental degradation. Instead, impact sockets should be recycled through appropriate channels, ensuring that the materials are reclaimed and reused efficiently.
Additionally, promoting the reuse and refurbishment of impact sockets can extend their lifecycle and reduce environmental impact. Impact sockets that are still in good condition can be refurbished and resold or donated, providing a second life for the tools and minimizing waste. This approach aligns with the principles of the circular economy, where products are kept in use for as long as possible, extracting maximum value before recovery and regeneration.
Educating users about the importance of recycling and proper disposal practices is also crucial for promoting environmental responsibility. Clear labeling, instructional guides, and awareness campaigns can encourage users to take proactive steps in managing the end-of-life of their impact sockets, fostering a culture of sustainability and environmental stewardship.
In conclusion, recyclability and responsible end-of-life disposal are essential for minimizing the environmental impact of impact sockets. By utilizing recyclable materials, designing for recyclability, promoting reuse and refurbishment, and educating users, the impact socket industry can contribute to environmental sustainability and resource conservation, ensuring that these valuable tools are managed responsibly throughout their lifecycle.
Choosing the Right Impact Socket for Your Needs
Assessing Your Specific Requirements
Choosing the right impact socket involves a thorough assessment of your specific requirements, ensuring that the selected sockets align with your tasks, tools, and performance expectations. This assessment helps in identifying the key features and specifications that are essential for your applications, enhancing efficiency, reliability, and overall tool effectiveness.
The first step in assessing your specific requirements is identifying the types of tasks you frequently perform and the environments in which you work. For example, if you are involved in automotive repairs, you may need impact sockets that can handle high torque levels and fit a wide range of fastener sizes commonly found in vehicles. On the other hand, if you work in construction or heavy machinery maintenance, you might require sockets that offer greater durability and resistance to wear and tear.
Another critical factor is determining the appropriate drive size and type that matches your tools. Impact sockets come in various drive sizes, such as 1/4″, 3/8″, 1/2″, and 3/4″, each suited for different torque levels and applications. Assessing the compatibility with your existing impact drivers, wrenches, and ratchets ensures that the sockets will function seamlessly with your tools, providing optimal performance and reducing the risk of tool slippage or damage.
Evaluating the material composition and quality of the impact sockets is also essential. Depending on the intensity and frequency of use, you may need sockets made from high-strength alloys like S2 steel or Chrome Vanadium to ensure durability and resistance to deformation. Additionally, considering the heat treatment processes and protective coatings can enhance the socket’s longevity and performance, making it better suited for demanding applications.
The design and construction of the impact sockets should also be taken into account. Features such as socket thickness, weight, hex size, and fitment are crucial for ensuring that the sockets perform effectively and comfortably during use. Ergonomic grips, quick-release mechanisms, and shock absorption features can significantly improve user experience and efficiency, making the sockets easier to handle and more reliable under high-torque conditions.
Furthermore, assessing the need for customization and specialized features can help in selecting impact sockets that cater to unique requirements. OEM customization capabilities allow for tailored socket designs that meet specific specifications, enhancing functionality and brand identity. Whether it’s custom sizes, unique finishes, or specialized grip designs, customization can provide a competitive edge and ensure that the sockets meet your exact needs.
Lastly, considering the cost versus quality ratio is vital for making informed purchasing decisions. Balancing budget constraints with the need for high-quality, durable sockets ensures that you invest in tools that offer long-term value and performance without overspending.
In summary, assessing your specific requirements involves evaluating the types of tasks, drive size compatibility, material quality, design features, customization needs, and cost considerations. By thoroughly understanding your requirements, you can select impact sockets that deliver optimal performance, durability, and value, enhancing your overall toolset’s effectiveness and efficiency.
Making an Informed Purchase Decision
Making an informed purchase decision when selecting impact sockets involves a comprehensive evaluation of various factors, ensuring that the chosen sockets meet your specific needs and expectations. This process encompasses research, comparison, and consideration of key attributes that contribute to the overall quality, performance, and value of the impact sockets.
The first step in making an informed purchase decision is conducting thorough research on different impact socket brands and models. Exploring manufacturer websites, product specifications, and industry reviews provides valuable insights into the available options and their respective features. Understanding the reputation and track record of the brands ensures that you are considering reliable and trusted products known for their quality and performance.
Comparing product specifications is essential for identifying the sockets that best match your requirements. Key specifications to consider include drive size, hex size, material composition, heat treatment processes, and protective coatings. Evaluating these specifications against your specific tasks and tools helps in narrowing down the options to those that offer the necessary durability, torque handling capabilities, and compatibility.
Reading and interpreting user reviews and testimonials further enhances the decision-making process. Reviews provide firsthand experiences and feedback on the performance, reliability, and durability of impact sockets, offering valuable perspectives that go beyond product descriptions. Positive reviews highlight the strengths and benefits of the sockets, while negative reviews can reveal potential drawbacks or issues to be aware of. Balancing these insights allows for a more comprehensive understanding of the product’s real-world performance.
Assessing the warranty and customer support offered by the manufacturer is another critical factor. A robust warranty provides assurance that the manufacturer stands behind their product, offering repairs or replacements in case of defects or issues. Good customer support ensures that you can receive assistance and guidance if you encounter any problems or have questions about the sockets. These elements contribute to the overall value and reliability of the impact sockets.
Considering the cost versus quality ratio is vital for ensuring that you receive the best value for your investment. While higher-priced sockets often offer superior materials and construction, mid-range options can provide adequate performance for less demanding applications. Evaluating the long-term benefits and durability of the sockets helps in determining whether the higher initial cost is justified by the extended lifespan and reduced need for replacements.
Additionally, evaluating the availability of complementary tools and accessories can enhance the functionality and versatility of your impact socket set. Accessories such as extension bars, adapters, and socket organizers can improve the usability and efficiency of the sockets, making them more adaptable to various tasks and applications.
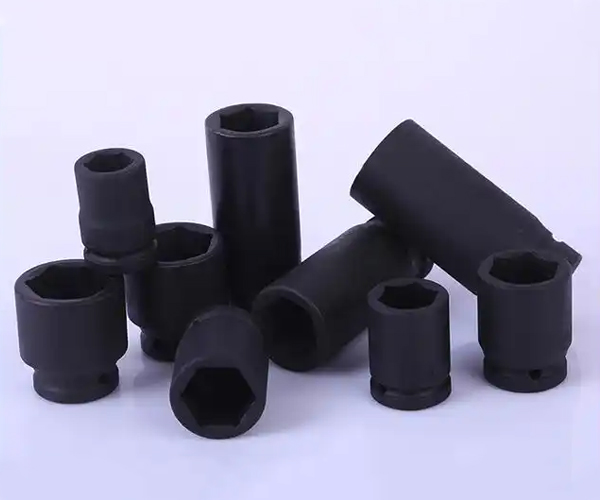
Lastly, considering the ergonomic and user-friendly features of the impact sockets contributes to overall satisfaction and ease of use. Features such as non-slip grips, quick-release mechanisms, and balanced weights enhance the user experience, making the sockets more comfortable and efficient to use during extended tasks.
In conclusion, making an informed purchase decision involves conducting thorough research, comparing product specifications, reading user reviews, assessing warranties and customer support, evaluating cost versus quality, considering complementary tools, and prioritizing ergonomic features. By carefully considering these factors, you can select impact sockets that meet your specific needs, deliver exceptional performance, and provide excellent value for your investment.
Conclusion
Summarizing the key factors of a good impact socket, it’s clear that material composition, design and construction, compatibility, durability, performance under impact, ease of use, brand reputation, cost vs. quality, OEM customization, safety features, maintenance, innovation, and environmental considerations all play pivotal roles. Each of these aspects contributes to the overall effectiveness and reliability of impact sockets, ensuring they meet the diverse needs of professionals and DIY enthusiasts alike.
Emphasizing the importance of quality and reliability, selecting the right impact socket can significantly enhance your toolset’s performance, efficiency, and longevity. High-quality impact sockets offer superior torque handling, durability, and safety features, making them indispensable tools for a wide range of applications. Investing in trusted brands and well-reviewed products ensures that you receive tools that are built to last and perform consistently under demanding conditions.
As you evaluate your current toolset and consider upgrading or expanding your impact socket collection, take the time to assess your specific requirements and make informed decisions based on the factors outlined in this guide. Whether you need sockets for automotive repairs, construction, heavy machinery maintenance, or DIY projects, choosing the right impact sockets tailored to your needs will enhance your productivity and ensure that you can tackle any task with confidence.
Feel secure knowing that by selecting impact sockets with the right features and quality, you are investing in tools that will support your work effectively and efficiently. Take action today by evaluating your toolset, exploring high-quality impact socket options, and making informed choices that align with your goals and requirements. Embrace the reliability and performance of top-notch impact sockets, and watch as they elevate your work to new heights of success and satisfaction.
FAQ Section
What materials are best for impact sockets?
Impact sockets are typically made from Chrome Vanadium (Cr-V) or S2 steel. Chrome Vanadium offers a good balance of toughness and flexibility, making it suitable for general use. S2 steel, being a higher-grade alloy, provides superior hardness and strength, ideal for heavy-duty applications that require maximum durability and torque handling.
How do I know which drive size to choose?
Choosing the right drive size depends on the specific tasks and tools you use. Common drive sizes include 1/4″, 3/8″, 1/2″, and 3/4″. For light-duty applications and smaller fasteners, 1/4″ sockets are ideal. For medium-duty tasks, 3/8″ sockets offer a good balance, while 1/2″ and 3/4″ sockets are suitable for heavy-duty applications requiring higher torque levels.
Can impact sockets be used with regular ratchets?
Yes, impact sockets can be used with regular ratchets, but it’s important to ensure compatibility. While impact sockets are designed to handle high torque and impacts from impact drivers, they can also be used with ratchets for more controlled and precise tasks. However, using them with impact drivers ensures maximum performance and durability.
What maintenance is required for impact sockets?
Regular maintenance includes cleaning sockets after use to remove dirt, grease, and debris. Proper storage in a dry, organized environment helps prevent rust and damage. Periodic inspection for signs of wear or damage is also important. Applying a light coating of oil can provide additional protection against corrosion and wear.
Are there impact sockets with quick-release features?
Yes, some impact sockets come with quick-release mechanisms that allow for rapid socket changes without the need for additional tools. These features enhance efficiency and convenience, making it easier to switch between different socket sizes and types during tasks.
How do OEM customization options benefit my business?
OEM customization allows businesses to tailor impact sockets to their specific needs, enhancing brand identity and product differentiation. Custom designs can include unique sizes, materials, finishes, and branding elements, providing a competitive edge and ensuring that the sockets meet precise specifications for various applications.
What safety features should I look for in impact sockets?
Key safety features include anti-slip technologies, protective coatings, and ergonomic designs. Anti-slip grips ensure better control and reduce the risk of tool slippage. Corrosion-resistant coatings prevent rust and degradation, while ergonomic designs enhance user comfort and reduce fatigue.
How long do high-quality impact sockets typically last?
High-quality impact sockets, when properly maintained, can last for many years. The lifespan depends on factors such as frequency of use, application intensity, and maintenance practices. Investing in durable materials and adhering to proper care routines can significantly extend the lifespan of your impact sockets.
Can I use impact sockets for both automotive and DIY projects?
Absolutely. Impact sockets are versatile tools suitable for a wide range of applications, including automotive repairs, construction, heavy machinery maintenance, and various DIY projects. Their ability to handle high torque and withstand impacts makes them ideal for both professional and personal use.
What are the top brands for impact sockets and why?
Top brands for impact sockets include Snap-On, Craftsman, GearWrench, and Milwaukee. These brands are known for their quality, durability, and innovative designs. They offer a wide range of impact sockets that meet various needs and applications, backed by strong warranties and excellent customer support, ensuring reliable performance and value.