Introduction
When it comes to working with impact wrenches, using the right tools is critical for efficiency, safety, and the longevity of both your tools and fasteners. A common mistake made by many DIYers and even some professionals is using conventional sockets on an impact wrench. While it might seem like a simple, quick fix, using the wrong type of socket can lead to a range of issues, including damaged tools and compromised safety. In this article, we will explore what can go wrong if you use conventional sockets with an impact wrench, how it affects your tools, and why it’s important to choose the correct socket for your impact wrench.
What is an Impact Wrench?
An impact wrench is a powerful tool designed to provide high torque output to fasten or loosen nuts and bolts with minimal effort from the user. These tools are most commonly used in automotive repair, construction, and manufacturing, where fasteners need to be tightened or loosened quickly and efficiently. Impact wrenches come in a variety of types, including pneumatic, electric, and cordless, each with its own strengths depending on the application.
The reason impact wrenches are so effective is their ability to deliver repeated bursts of torque, unlike a regular hand wrench or ratchet. The tool essentially “impacts” the fastener with high rotational force, making it much easier to work with tough, stubborn bolts. However, this unique torque output is not something all tools are built to handle, which is where the issue of using the wrong socket comes into play.
If you use a conventional socket, which is designed for manual hand tools, the torque delivered by the impact wrench can overwhelm the socket. As a result, it can cause the socket to wear out prematurely or, in some cases, break altogether. Understanding the mechanics of an impact wrench and how it differs from traditional hand tools is essential for using the tool correctly and safely.
The Importance of High-Torque Sockets
The main feature that sets impact sockets apart from conventional ones is their design, specifically made to withstand high-impact forces. Conventional sockets, often made from chrome-plated steel, are not designed to handle the extreme stresses caused by an impact wrench. Impact sockets, on the other hand, are made from much stronger, more durable materials like chrome-molybdenum. These materials can handle the repeated, high-torque bursts without deforming or breaking.
What is a Conventional Socket?
Conventional sockets are basic tools used with hand wrenches or ratchets. They are designed to fit over fasteners such as nuts and bolts, allowing the user to rotate them to tighten or loosen. These sockets are typically made from steel alloys and are finished with chrome plating for added protection against rust and corrosion. Conventional sockets come in a variety of sizes to fit different fastener types and are used in a wide range of mechanical, automotive, and household applications.
While conventional sockets are effective for use with hand tools, they are not designed to withstand the intense forces produced by impact wrenches. Impact wrenches generate significant levels of torque, which is delivered in short, powerful bursts that can quickly damage conventional sockets. The high stress on the socket material can lead to it warping, cracking, or breaking, potentially causing serious issues for both the user and the fastener.
Why Conventional Sockets Aren’t Suitable for Impact Wrenches
The primary issue with using a conventional socket on an impact wrench is that it is not built to withstand the high, repetitive force generated by impact wrenches. Conventional sockets are designed for steady, continuous torque, such as when using a hand wrench, where the torque is applied gradually. Impact wrenches, however, deliver quick bursts of torque that can easily damage the socket if it is not designed to handle such force. This can lead to failure of the socket, which may cause the wrench to slip or break, potentially damaging the fastener or the tool itself.
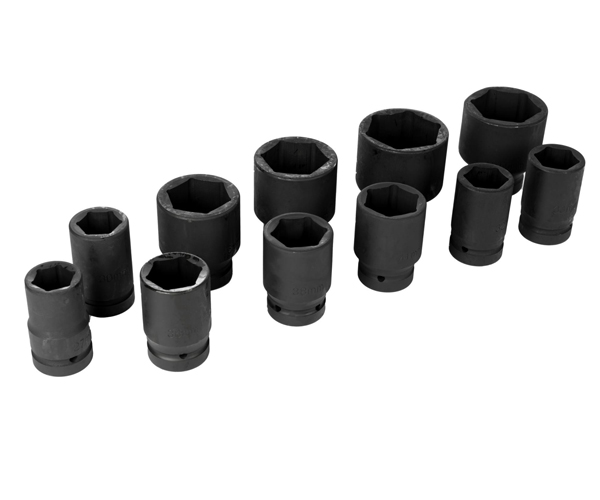
Understanding Torque: The Core Difference
Torque is the rotational force applied to a fastener or other object. In the context of tools, torque is a measure of how much force is being used to turn the object, and it is critical for proper fastening. Impact wrenches are designed to generate high levels of torque to quickly loosen or tighten bolts, making them ideal for applications where speed and power are essential, such as in automotive or industrial work.
Conventional sockets are designed to handle low to moderate amounts of torque, typically from hand tools or ratchets. When using a hand tool, the torque is applied steadily, which allows the socket to absorb the force without issue. However, impact wrenches apply torque in bursts, which increases the risk of damaging a conventional socket. These sudden, high-torque impacts can cause the socket to bend, crack, or break, leading to potential safety hazards and tool damage.
Why High Torque Matters
Impact wrenches generate significantly more torque than standard hand tools, which is essential for applications where large or rusted bolts need to be removed quickly. However, this additional torque requires specialized tools, such as impact sockets, that are designed to withstand these high levels of force. Conventional sockets simply aren’t built to handle such bursts of torque, and using them in this environment can lead to rapid wear and tear, reducing the socket’s lifespan and affecting the overall efficiency of the job.
The Risk of Socket Deformation
One of the most common consequences of using a conventional socket on an impact wrench is socket deformation. Impact wrenches deliver high amounts of force in quick bursts, which puts significant stress on the material of the socket. Conventional sockets, which are made of materials that are not designed for such stress, can warp or deform over time under these conditions.
How Conventional Sockets Deform
Conventional sockets are typically made from chrome vanadium steel, which is durable but not designed to absorb the intense shock and torque from an impact wrench. Over time, the repeated force can cause the socket to lose its shape. The edges of the socket may become rounded or uneven, making it difficult to properly grip the fastener. In some cases, the socket may even crack or break, rendering it useless and potentially damaging the fastener it was supposed to work with.
Signs Your Socket is Deforming
If you use conventional sockets on an impact wrench, the first signs of deformation may not be immediately apparent, but they can become more noticeable with extended use. You may notice that the socket no longer fits snugly around the fastener, or that it slips or rounds off the edges of the fastener. Over time, this wear and tear can significantly impact your ability to properly complete tasks, and it may also result in stripped or damaged fasteners.
The Safety Risks of Using Conventional Sockets
Using conventional sockets on an impact wrench presents significant safety risks. When a socket is used outside of its intended purpose, the pressure and torque from the wrench can cause it to break or explode. A failed socket can send sharp pieces flying, posing a danger to the user and others in the vicinity. Additionally, if the socket breaks or deforms during use, it can cause the impact wrench to slip, damaging the fastener, surrounding equipment, or even the operator.
The Dangers of a Broken Socket
A socket that breaks while in use can be dangerous. The high velocity at which impact wrenches work means that any broken parts can become projectiles. These flying shards of metal can injure the operator, bystanders, or damage surrounding tools and equipment. Even if the socket does not break completely, significant deformation can cause the wrench to malfunction, potentially leading to further damage and injury.
Increased Risk of Accidents in High-Torque Environments
Impact wrenches are typically used in high-pressure environments where speed and efficiency are important. However, using the wrong type of socket increases the likelihood of accidents. Broken or deformed sockets can cause the wrench to slip, leading to loss of control and potentially severe injury. Using impact-specific sockets is crucial for maintaining safety during high-torque operations.
What Happens to the Impact Wrench Itself?
When conventional sockets are used with an impact wrench, it’s not just the socket that suffers. The internal components of the impact wrench are also at risk. The added stress caused by using the wrong tools can damage the impact wrench’s motor, gears, or housing. This can reduce the overall performance of the tool, shortening its lifespan and requiring costly repairs or replacements.
Damage to the Internal Mechanisms
The motor and internal gears of an impact wrench are designed to withstand certain levels of torque. When conventional sockets are used, the added stress from the improperly matched tool can strain these internal components. Over time, this may result in malfunctioning gears or reduced power output. Repairing or replacing these internal components can be expensive and time-consuming.
Effect on Wrench Performance and Longevity
The performance of an impact wrench will inevitably decline if it is used improperly. A damaged wrench may operate less efficiently, affecting the speed and power with which it performs tasks. Additionally, as internal components wear out, the overall lifespan of the tool is shortened, requiring frequent repairs or replacements. Using the right socket is crucial for maximizing the longevity of both the socket and the impact wrench.
The Cost of Replacing Damaged Tools
The cost of replacing damaged tools due to improper use can quickly add up. If you consistently use conventional sockets with an impact wrench, you will likely find yourself needing to replace not only the sockets but the impact wrench as well. Both types of tools are expensive, and frequent replacements can put a significant strain on your budget.
How Frequent Misuse Leads to Expensive Repairs
When conventional sockets are used on impact wrenches, it places unnecessary strain on both the socket and the wrench. Over time, this wear and tear can cause the tools to break, leading to the need for expensive repairs or replacements. If you don’t replace the damaged components, they can further degrade the performance of your tools, creating a cycle of constant repair and replacement costs.
Replacing Deformed Sockets vs. Impact Wrenches
While replacing a deformed socket is generally less expensive than replacing an entire impact wrench, it can still add up over time. If the wrench itself is damaged due to the improper use of sockets, the cost of replacing the tool can be significantly higher. The long-term cost of improper tool usage can far exceed the initial investment in proper impact sockets and wrenches.
Why Impact-Specific Sockets Are a Must
Impact-specific sockets are essential for anyone working with impact wrenches. These sockets are designed to handle the high torque and repeated impacts generated by impact wrenches. Unlike conventional sockets, which can quickly wear out or break, impact sockets are made from materials and designed in a way that allows them to absorb the shock and withstand the force of an impact wrench.
What Are Impact Sockets?
Impact sockets are a specialized type of socket designed specifically for use with impact tools. They are typically made from stronger materials such as chrome-molybdenum steel, which is much more resistant to wear and tear than the materials used in conventional sockets. Impact sockets also have a thicker wall construction and a different finish to help absorb the impact forces they will be subjected to.
How Impact Sockets Are Designed to Handle High Torque
The design of impact sockets is specifically tailored to withstand the extreme forces produced by impact wrenches. The materials used in their construction are not only stronger but are also more flexible, allowing them to absorb the shock of impact without cracking or breaking. This durability ensures that the socket can continue to perform at a high level, even under the most demanding conditions.
Impact Sockets vs. Conventional Sockets: Key Differences
The most significant difference between impact sockets and conventional sockets is the material and design. Impact sockets are made from materials that are far more durable and impact-resistant than conventional sockets. Chrome-molybdenum steel is a common material used in impact sockets, while chrome-vanadium steel is used for conventional sockets. Impact sockets also have thicker walls and deeper recesses to handle the repeated shock of impact wrenches.
Material Differences
Impact sockets are made from stronger alloys, such as chrome-molybdenum, which are specifically chosen for their ability to handle high stress. Conventional sockets, on the other hand, are often made from chrome-vanadium, which, while strong, is not designed to withstand repeated high impacts. The tougher material of impact sockets ensures they can absorb shock without failing, making them ideal for use with impact wrenches.
The Design of Impact Sockets
Impact sockets are designed to be thicker and more robust than conventional sockets. They feature deeper recesses to allow for better gripping of fasteners and are often blackened or coated with anti-corrosion materials for added durability. Conventional sockets, on the other hand, are thinner and may be more susceptible to cracking or breaking under stress.
How to Choose the Right Socket for Your Impact Wrench
Choosing the right socket for your impact wrench is crucial for ensuring optimal performance and safety. The right socket will not only prevent tool damage but also improve the efficiency of your work.
Selecting the Correct Size
The most important factor when choosing a socket is ensuring it fits the fastener correctly. A socket that is too large or too small can cause damage to the fastener or socket. It’s also important to choose a socket that matches the specifications of your impact wrench, including the drive size.
Choosing the Right Material
The material of the socket is just as important as the size. Impact sockets are made from stronger materials like chrome-molybdenum steel, which are able to handle the high torque produced by impact wrenches. Conventional sockets are not designed for this level of force and can easily deform under pressure.
What Are Some Other Common Mistakes with Impact Wrenches?
While using conventional sockets on impact wrenches is one of the most common mistakes, there are other errors that users make when working with these powerful tools.
Using the Wrong Fasteners
Using the wrong type of fastener can cause significant damage to your impact wrench and the surrounding equipment. Fasteners that are not compatible with your impact wrench can become damaged during tightening or loosening, leading to further complications and potential tool failure.
Not Using the Right Settings on the Wrench
Impact wrenches often come with variable settings to adjust the torque output. Not using the correct setting for the task at hand can lead to over-tightening or under-tightening, which can cause damage to both the fastener and the tool.
How to Properly Maintain Your Impact Wrench and Sockets
Regular maintenance of your impact wrench and sockets is essential for prolonging their lifespan and ensuring they perform at their best.
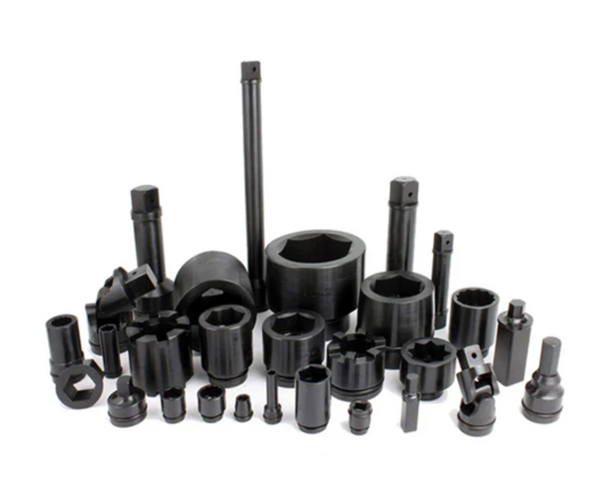
Routine Cleaning and Inspection
Cleaning your tools regularly can help prevent the buildup of debris and dirt, which can damage the tool’s components. It’s also important to inspect the sockets for any signs of wear or damage, as using damaged tools can cause further issues.
Lubrication and Storage
Proper lubrication is essential for keeping the moving parts of your impact wrench functioning smoothly. Additionally, storing your tools in a clean, dry place can help prevent rust and corrosion, which can degrade their performance.
Expert Advice on Using an Impact Wrench Safely
When using an impact wrench, it’s important to follow proper safety protocols to protect yourself and your tools.
Best Practices for Using Impact Wrenches and Sockets
Always use the correct socket for the job and ensure that the fasteners are properly fitted. Avoid over-tightening or under-tightening and use the correct settings for your wrench. When working with high-torque tools, always wear protective gear, including eye protection and gloves, to minimize the risk of injury.
Avoiding Common Pitfalls
Make sure to regularly inspect your tools for wear and tear. If a socket or wrench shows signs of damage, replace it immediately to prevent accidents.
Ensuring Safety for the Operator and Equipment
Using the right tools for the job not only protects your equipment but also ensures your safety. Always follow manufacturer guidelines and never use tools for purposes outside of their intended design.
Conclusion
In conclusion, using conventional sockets on impact wrenches can lead to numerous problems, including damaged tools, safety risks, and costly repairs. It’s essential to use impact sockets, which are specifically designed to handle the high torque and repeated force produced by these powerful tools. By choosing the correct socket, maintaining your tools, and following best practices for safety, you can ensure efficient, safe, and long-lasting use of your impact wrench and sockets. Always invest in quality tools and take the necessary precautions to protect both your equipment and yourself.
FAQ
Can I use regular sockets on a low-torque impact wrench?
- While it may be acceptable to use regular sockets on a low-torque impact wrench, it’s still advisable to use impact sockets to ensure optimal performance and safety.
How can I tell if my socket is compatible with my impact wrench?
- Check for markings indicating it’s an impact socket, ensure the size matches the fastener and wrench drive, and verify the material is suitable for high torque.
What happens if I use a damaged socket on my impact wrench?
- A damaged socket can cause the wrench to slip, break, or wear out quickly, leading to possible accidents and further damage to the fastener and tools.
Are there universal impact sockets that can work with all impact wrenches?
- While some impact sockets are labeled as universal, it’s essential to verify compatibility with your specific impact wrench to ensure proper fit and function.
Can using the wrong socket void my tool warranty?
- Using the wrong socket or improper tool care can potentially void warranties, depending on the manufacturer’s terms and conditions. Always follow recommended guidelines to ensure your warranty remains valid.