Introduction to Impact Sockets
Impact sockets are essential tools in various industries, particularly in automotive repair and construction. These specialized sockets are designed to withstand the high torque and repetitive impacts generated by impact drivers and wrenches. Unlike standard hand-tool sockets, impact sockets are built with superior materials and construction techniques to ensure durability and safety. High-quality impact sockets not only enhance efficiency but also prevent tool failure, which can lead to costly downtime and safety hazards. Understanding the manufacturing process of these impact sockets is crucial for businesses seeking reliable tools that meet specific performance standards and customization needs.
Understanding the Use Cases and Applications
Who Uses Impact Sockets?
Impact sockets are indispensable tools for a wide range of professionals and enthusiasts. Professional mechanics and automotive technicians rely heavily on impact sockets for tasks such as engine repairs, brake replacements, and suspension work. These sockets enable them to quickly and efficiently remove and install bolts and nuts that are often tightened to high torque specifications. Additionally, industrial maintenance teams use impact sockets in machinery upkeep and repairs, ensuring that equipment runs smoothly and safely.
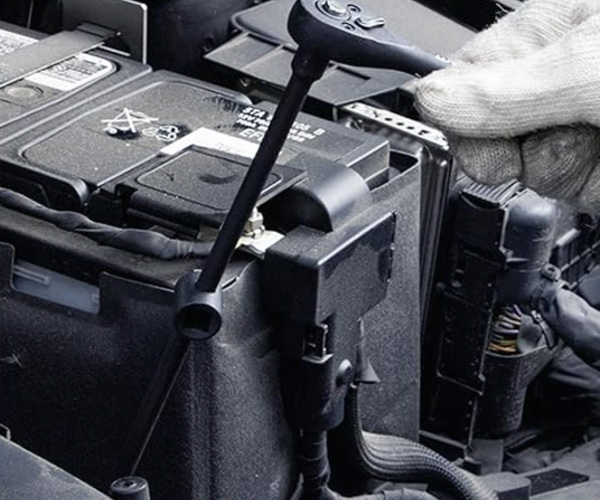
DIY enthusiasts and hobbyists also find impact sockets valuable for home improvement projects and automotive tinkering. The ability to apply high torque with minimal effort makes these sockets ideal for tasks that require both speed and precision. Furthermore, construction workers utilize impact sockets in assembling and disassembling structural components, where the durability and reliability of the tools are paramount.
Typical Work Environments
Impact sockets are designed to perform in demanding environments where high torque and repeated use are common. Automotive repair shops, for instance, are bustling with activity, requiring tools that can handle continuous operation without compromising performance. The rugged conditions of these shops, including exposure to oil, grease, and other contaminants, necessitate sockets that are resistant to corrosion and wear.
Assembly lines in manufacturing plants also benefit from the use of impact sockets. The repetitive nature of assembly tasks demands tools that maintain consistency and reliability over extended periods. In construction sites, impact sockets are used in conjunction with pneumatic tools to assemble large structures, where the strength and durability of the tools directly impact the quality and safety of the construction.
Common Tools That Use Impact Sockets
Impact sockets are typically paired with high-torque tools such as impact wrenches, pneumatic impact drivers, and cordless high-torque drivers. These tools generate the force required to loosen or tighten bolts and nuts that are otherwise difficult to manage with standard hand tools. An impact socket set often includes a variety of sizes and drive types to accommodate different applications and user preferences.
For example, a 1/2 impact socket set is commonly used in automotive and heavy-duty applications, providing the necessary strength to handle large fasteners. On the other hand, an impact socket set 3/8 is preferred for lighter tasks and applications that require greater maneuverability. Specialized tools like the impact driver socket adapter and impact socket adapter enable users to switch between different drive types seamlessly, enhancing the versatility of their toolkits.
Specialized Impact Sockets
Brands like Milwaukee impact sockets are renowned for their quality and innovation. Milwaukee, known for its durable and high-performance tools, offers impact sockets that cater to both professional and DIY users. These sockets are engineered with precision to ensure a perfect fit and optimal performance, reducing the risk of slippage and tool damage. The use of advanced materials and coatings in Milwaukee impact sockets enhances their longevity and resistance to wear and tear, making them a preferred choice among users who demand reliability and efficiency.
Impact Sockets in Various Industries
Different industries leverage the benefits of impact sockets to enhance their operational efficiency. In the automotive industry, impact sockets are critical for vehicle assembly and maintenance, where time and precision are crucial. In manufacturing, these sockets facilitate the assembly of machinery and equipment, ensuring that components are securely fastened and aligned correctly.
The construction industry relies on impact sockets for the assembly of structural frameworks and heavy machinery, where the robustness and durability of the tools are essential for safety and productivity. Additionally, in the aerospace sector, impact sockets are used in the assembly and maintenance of aircraft, where precision and reliability are paramount.
Enhancing Productivity and Safety
The use of high-quality impact sockets significantly enhances productivity by reducing the time and effort required to perform fastening tasks. The ability to apply high torque with minimal manual effort allows workers to complete tasks more quickly and efficiently. This not only boosts productivity but also reduces the physical strain on workers, leading to improved job satisfaction and reduced risk of injury.
Safety is another critical aspect addressed by quality impact sockets. Poorly made sockets can fail under high torque, leading to tool breakage, which poses serious safety risks to users. High-quality impact sockets are designed to withstand the stresses of heavy use, ensuring that they remain reliable and safe throughout their service life. This reliability is crucial in environments where tool failure can lead to accidents and costly downtime.
The Role of Impact Sockets in Modern Toolkits
Modern toolkits, whether for professional use or personal projects, increasingly include impact sockets due to their versatility and reliability. The integration of impact sockets into these toolkits allows users to tackle a wide range of tasks with confidence, knowing that they have the right tools to handle high-torque applications effectively. The availability of various sizes and drive types ensures that users can find the perfect fit for any job, enhancing the overall functionality of their toolkits.
In summary, impact sockets are essential tools across various industries and applications. Their ability to withstand high torque and repetitive use makes them indispensable for professionals and enthusiasts alike. Understanding the diverse use cases and applications of impact sockets underscores their importance in modern toolkits and highlights the need for high-quality manufacturing processes to ensure their reliability and performance.
Key Characteristics of High-Quality Impact Sockets
Material Strength and Toughness
One of the most critical factors that distinguish high-quality impact sockets from standard sockets is the material used in their construction. Impact sockets are typically made from high-grade steel, such as chromium-molybdenum (Cr-Mo) or chromium-vanadium (Cr-V) steel, which offers superior strength and toughness. These materials are selected for their ability to withstand the high torque and repetitive impacts generated by impact drivers and wrenches without deforming or breaking.
The strength of the steel ensures that the sockets can handle the stress of heavy-duty applications, providing a longer service life and reducing the need for frequent replacements. Toughness, on the other hand, refers to the material’s ability to absorb energy and resist fracture, which is crucial for preventing socket failure during high-impact use. High-quality impact sockets are engineered to maintain their integrity under extreme conditions, ensuring reliable performance in demanding environments.
Design for Withstanding Repeated Stress
The design of impact sockets plays a significant role in their ability to withstand repeated stress and high torque applications. High-quality impact sockets feature thicker walls and robust geometries that distribute the stress more evenly across the socket. This design minimizes the risk of deformation and enhances the socket’s overall durability.
Additionally, impact sockets often incorporate unique design elements, such as reinforced walls and specialized drive interfaces, to improve their ability to handle high-impact forces. These design considerations ensure that the sockets remain stable and secure during use, reducing the likelihood of slippage and tool damage. The careful balance between strength and weight in the design of impact sockets also contributes to their ease of use, allowing users to apply high torque without excessive effort.
Safety Considerations
Safety is a paramount concern when it comes to the manufacturing and use of impact sockets. High-quality impact sockets are designed with safety features that prevent shattering or cracking under high torque and repeated impacts. The use of tempered steel and precise heat treatment processes enhances the socket’s ability to resist fatigue and avoid catastrophic failure.
Furthermore, the design of impact sockets includes features such as reinforced drive interfaces and secure mounting systems to ensure that the socket remains firmly attached to the impact tool during use. This stability reduces the risk of the socket slipping or detaching unexpectedly, which can cause injuries or damage to the workpiece. Safety certifications and adherence to industry standards are also indicators of the socket’s reliability and safety, providing users with confidence in their tools.
Visual and Functional Differences From Standard Sockets
High-quality impact sockets often have distinct visual and functional differences compared to standard hand-tool sockets. One noticeable difference is the color coating; impact sockets typically feature a black oxide or other durable coatings that provide corrosion resistance and reduce glare, making them easier to identify and use in various lighting conditions.
Functionally, impact sockets are designed with specific features that enhance their performance in high-torque applications. For example, the internal drive interface of impact sockets is often constructed with reinforced materials or unique geometries to ensure a secure fit with impact tools. This design minimizes the risk of stripping or damaging the drive interface, which can compromise the socket’s performance and longevity.
Additionally, impact sockets may include specialized markings and size indicators that facilitate quick identification and selection during use. These visual cues help users find the right socket size quickly, improving efficiency and reducing the time spent searching for the correct tool. The combination of visual distinctions and functional enhancements makes high-quality impact sockets a valuable addition to any toolkit, providing both reliability and ease of use in demanding applications.
Enhanced Grip and Ergonomics
Another characteristic of high-quality impact sockets is their enhanced grip and ergonomic design. The exterior of impact sockets is often treated with textures or coatings that improve grip, allowing users to handle the sockets more securely even in oily or greasy conditions. This enhanced grip reduces the likelihood of the socket slipping during use, contributing to both safety and efficiency.
Ergonomic considerations also play a role in the design of impact sockets. The shape and weight distribution of the socket are engineered to provide a comfortable and balanced feel, reducing user fatigue during prolonged use. This attention to ergonomics ensures that users can maintain control and precision, even when working with high-torque applications that require sustained effort.
Compatibility and Versatility
High-quality impact sockets are designed to be highly compatible and versatile, accommodating a wide range of tools and applications. They come in various drive sizes, such as 1/2-inch and 3/8-inch, to match different impact tools and specific tasks. This versatility allows users to select the appropriate socket for each job, ensuring optimal performance and minimizing the risk of tool damage.
Additionally, impact sockets are available in a variety of sizes and configurations, including deep sockets, shallow sockets, and specialty sockets, to address different fastening needs. This broad range of options makes impact sockets suitable for a diverse array of applications, from automotive repairs to industrial maintenance and construction projects.
Durability and Longevity
Durability and longevity are key attributes of high-quality impact sockets. The combination of premium materials, robust design, and precise manufacturing processes ensures that impact sockets can endure the rigors of heavy-duty use without compromising performance. These sockets are built to last, providing reliable service over extended periods and reducing the need for frequent replacements.
The durability of impact sockets is further enhanced by protective coatings and surface treatments that guard against corrosion, wear, and environmental damage. These coatings not only prolong the life of the sockets but also maintain their appearance and functionality, even in harsh working conditions. As a result, users can rely on their impact sockets to perform consistently, delivering the strength and reliability required for demanding tasks.
Brand Reputation and Quality Assurance
The reputation of the manufacturer plays a significant role in the perceived quality of impact sockets. Established brands like Milwaukee are known for their commitment to excellence, consistently delivering high-quality impact sockets that meet stringent performance standards. These brands invest in research and development to innovate and improve their products, ensuring that their impact sockets remain at the forefront of the industry.
Quality assurance measures, such as rigorous testing and adherence to industry standards, further reinforce the reliability of high-quality impact sockets. Manufacturers implement comprehensive quality control processes to verify that each socket meets specific criteria for strength, durability, and performance. These measures provide users with confidence in their tools, knowing that they are backed by reputable brands that prioritize quality and customer satisfaction.
Conclusion
High-quality impact sockets are indispensable tools for professionals and enthusiasts alike, offering superior strength, durability, and safety compared to standard hand-tool sockets. The meticulous selection of materials, robust design, and stringent quality control processes ensure that these sockets can withstand the demands of high-torque applications and repetitive use. Distinct visual and functional features, enhanced grip and ergonomics, and compatibility with a wide range of tools further enhance their value and versatility. Brands with strong reputations and comprehensive quality assurance measures provide users with reliable and long-lasting impact sockets that meet their specific needs. Investing in high-quality impact sockets not only improves efficiency and productivity but also ensures the safety and reliability of the tools used in various demanding environments.
Raw Materials: Selecting the Right Steel
Common Steels Used in Impact Sockets
The foundation of high-quality impact sockets lies in the selection of the right steel. Two primary types of steel are commonly used in the manufacturing of impact sockets: chromium-molybdenum (Cr-Mo) steel and chromium-vanadium (Cr-V) steel. Both of these alloys are chosen for their exceptional strength, toughness, and durability, which are essential for handling the high torque and repetitive impacts encountered in various applications.
Chromium-molybdenum steel is renowned for its high tensile strength and excellent wear resistance. The addition of molybdenum enhances the steel’s ability to withstand extreme forces without deforming, making it ideal for heavy-duty impact sockets used in automotive and industrial settings. Chromium-vanadium steel, on the other hand, offers a balanced combination of strength and flexibility. The presence of vanadium improves the steel’s toughness, allowing it to absorb and distribute impacts more effectively, reducing the risk of cracking or shattering.
Properties That Make Certain Metals Ideal
The ideal steel for impact sockets must possess a balance of hardness, tensile strength, and flexibility. Hardness ensures that the socket can resist deformation and wear, maintaining its shape and functionality over time. Tensile strength is crucial for withstanding the high forces exerted during impact use, preventing the socket from breaking under stress. Flexibility, or toughness, allows the socket to absorb and dissipate energy from impacts without becoming brittle or cracking.
Chromium-molybdenum steel excels in these properties, providing the necessary hardness and tensile strength for heavy-duty applications. Its ability to maintain these characteristics under extreme conditions makes it a preferred choice for high-torque impact sockets. Chromium-vanadium steel, with its enhanced toughness, is particularly suited for applications where sockets may encounter sudden shocks or stresses, offering greater resilience and longevity.
Sourcing Quality Metals
Sourcing high-quality steel is a critical step in the manufacturing process of impact sockets. Reputable manufacturers establish strong relationships with trusted steel mills and suppliers to ensure a consistent supply of premium-grade materials. These suppliers adhere to strict quality standards and certifications, guaranteeing that the steel meets the required specifications for impact socket production.
Consistency in the quality of raw materials is essential for maintaining the performance and reliability of impact sockets. Manufacturers conduct thorough inspections and tests on incoming steel batches to verify their composition, hardness, and tensile strength. This meticulous quality control ensures that only the best materials are used in the production process, resulting in impact sockets that deliver superior performance and durability.
Importance of Steel Quality in Impact Socket Performance
The quality of steel directly impacts the performance and longevity of impact sockets. High-quality steel ensures that the sockets can withstand the rigors of heavy-duty use without compromising their structural integrity. Poor-quality steel, on the other hand, can lead to premature wear, deformation, and failure, resulting in tools that are unreliable and potentially dangerous to use.
By selecting the right steel and maintaining strict quality control measures, manufacturers can produce impact sockets that offer exceptional performance, durability, and safety. This commitment to quality not only enhances the reputation of the manufacturer but also provides users with tools they can trust to perform reliably in demanding environments.
Enhancing Steel Properties Through Alloying
Alloying elements such as chromium, molybdenum, and vanadium are added to steel to enhance its properties and suitability for impact socket manufacturing. Chromium increases hardness and corrosion resistance, making the steel more durable and resistant to rust and wear. Molybdenum enhances the steel’s ability to withstand high temperatures and stresses, improving its overall strength and toughness. Vanadium contributes to the steel’s hardness and wear resistance, allowing it to maintain its integrity under repeated impacts and heavy use.
These alloying elements work synergistically to create a steel composition that meets the demanding requirements of impact socket applications. The precise balance of these elements ensures that the steel possesses the necessary characteristics to deliver high performance and longevity, making it ideal for manufacturing top-quality impact sockets.
Innovations in Steel Processing
Advancements in steel processing techniques have further improved the quality and performance of impact sockets. Modern manufacturing processes, such as precise heat treatment and controlled forging, enhance the microstructure of the steel, increasing its strength and toughness. These innovations allow manufacturers to produce impact sockets with superior mechanical properties, ensuring that they can handle the high torque and repetitive impacts of demanding applications.
Additionally, surface treatments and coatings applied during the manufacturing process enhance the corrosion resistance and durability of impact sockets. These treatments protect the steel from environmental factors such as moisture and chemicals, extending the life of the sockets and maintaining their appearance and functionality over time.
Sustainability in Steel Sourcing
Sustainability is becoming increasingly important in steel sourcing and manufacturing practices. Responsible manufacturers prioritize sourcing steel from suppliers that adhere to environmentally friendly practices, such as reducing emissions and minimizing waste. By choosing sustainable steel sources, manufacturers contribute to the preservation of natural resources and reduce the environmental impact of their production processes.
Sustainable practices also extend to the manufacturing of impact sockets, where efforts are made to optimize energy usage, recycle materials, and implement eco-friendly coatings. These initiatives not only benefit the environment but also appeal to environmentally conscious consumers who prioritize sustainability in their purchasing decisions.
Conclusion
Selecting the right steel is fundamental to the production of high-quality impact sockets. The choice between chromium-molybdenum and chromium-vanadium steel, along with the precise balance of alloying elements, determines the socket’s strength, toughness, and durability. Sourcing premium-grade steel from reputable suppliers ensures consistency and reliability in the manufacturing process, resulting in impact sockets that perform exceptionally well in demanding applications. Innovations in steel processing and a commitment to sustainability further enhance the quality and environmental responsibility of impact socket production. By prioritizing steel quality, manufacturers can deliver impact sockets that meet the highest standards of performance and longevity, providing users with tools they can trust for their most challenging tasks.
Designing the Perfect Impact Socket
Engineering the Socket’s Shape and Profile
The design of an impact socket is a critical factor that influences its performance and durability. Engineers meticulously craft the shape and profile of the socket to ensure it can handle the high torque and repeated impacts typical in heavy-duty applications. The internal drive size must match the specific impact tool, whether it’s a 1/2-inch or 3/8-inch drive, ensuring a secure fit and efficient torque transfer.
The external shape of the socket is also carefully designed to provide optimal strength without adding unnecessary weight. Thicker walls and reinforced edges contribute to the socket’s ability to withstand high torque forces, while maintaining a manageable weight for ease of use. The balance between strength and weight is essential, as it affects both the performance and the ergonomics of the socket, making it easier for users to handle the tools during prolonged use.
Balancing Thickness for Strength Without Adding Unnecessary Bulk
Achieving the right balance in wall thickness is crucial in impact socket design. While thicker walls provide additional strength and durability, they also add weight to the socket, which can make it cumbersome during use. Engineers use advanced modeling techniques to determine the optimal thickness that offers maximum strength without compromising the socket’s lightweight characteristics.
This balance ensures that the socket can endure high torque applications without deforming or breaking, while still being easy to handle and maneuver. The precise engineering of the socket’s thickness also contributes to its longevity, reducing the need for frequent replacements and ensuring consistent performance over time.
CAD and Prototyping
Computer-Aided Design (CAD) plays a significant role in the development of high-quality impact sockets. CAD software allows engineers to create detailed 3D models of the socket, enabling precise measurements and simulations of stress and torque forces. This digital prototyping helps identify potential design flaws and optimize the socket’s geometry before moving to the production stage.
Prototyping is an essential step in the design process, allowing manufacturers to test and refine their designs. By creating prototypes, engineers can evaluate the socket’s performance under real-world conditions, making necessary adjustments to enhance its strength, durability, and functionality. This iterative process ensures that the final product meets the highest standards of quality and performance, providing users with reliable and efficient impact sockets.
Making Prototypes to Test Functionality Before Mass Production
Before committing to mass production, manufacturers create prototypes of their impact socket designs to test their functionality and performance. These prototypes undergo rigorous testing to ensure they can handle the stresses and impacts typical of their intended applications. Feedback from these tests is used to make refinements and improvements to the design, addressing any weaknesses or inefficiencies identified during the testing phase.
This hands-on testing process is crucial for verifying that the impact sockets perform as expected and meet the required standards for strength, durability, and safety. By thoroughly testing prototypes, manufacturers can ensure that their impact sockets are ready for mass production, minimizing the risk of defects and ensuring consistent quality across all units.
Incorporating User Feedback into Design
User feedback is an invaluable resource in the design and development of impact sockets. Manufacturers actively seek input from professionals and enthusiasts who use these tools in various applications. This feedback provides insights into the practical challenges and requirements faced by users, helping manufacturers refine their designs to better meet their needs.
By incorporating user feedback, manufacturers can address specific pain points and enhance the usability and performance of their impact sockets. This collaborative approach ensures that the final product is not only technically sound but also aligned with the practical needs and preferences of its users, resulting in impact sockets that are both reliable and user-friendly.
Enhancing Ergonomics and Handling
Ergonomics and handling are critical aspects of impact socket design that directly impact user experience and efficiency. Manufacturers design impact sockets with features that enhance grip and control, making them easier to handle during high-torque applications. Textured surfaces, ergonomic shapes, and balanced weight distribution contribute to a more comfortable and secure grip, reducing user fatigue and improving precision.
Enhanced ergonomics also play a role in reducing the risk of accidents and injuries, as users can maintain better control over their tools. By prioritizing ergonomics in the design process, manufacturers create impact sockets that are not only powerful and durable but also comfortable and safe to use, enhancing overall productivity and user satisfaction.
Integrating Specialized Features
High-quality impact sockets often include specialized features that enhance their functionality and performance. These features may include reinforced drive interfaces to prevent stripping and cracking, precision-machined edges for better fit and alignment, and unique coatings that provide additional corrosion resistance and durability.
Additionally, some impact sockets incorporate design elements that allow for quick and easy switching between different drive sizes or configurations. This versatility enables users to adapt their tools to a variety of tasks without the need for multiple sockets, streamlining their workflow and improving efficiency.
Conclusion
Designing the perfect impact socket involves a careful balance of strength, durability, ergonomics, and functionality. Engineers use advanced tools like CAD and prototyping to create and refine socket designs, ensuring they can withstand high torque and repetitive impacts while remaining lightweight and easy to handle. By incorporating user feedback and integrating specialized features, manufacturers enhance the performance and usability of impact sockets, making them indispensable tools for professionals and enthusiasts alike. The meticulous design process ensures that each impact socket delivers reliable performance, safety, and efficiency, meeting the diverse needs of users across various industries and applications.
Initial Forging and Forming Processes
Hot Forging Basics
Hot forging is a fundamental step in the manufacturing process of high-quality impact sockets. This technique involves heating the steel to a high temperature, making it malleable and easier to shape without compromising its structural integrity. The elevated temperature allows the steel to be formed under significant pressure, ensuring that the final product has the desired shape and properties.
Heating the metal to the appropriate temperature is crucial, as it enhances the steel’s ductility and reduces the risk of cracking or deforming during the forging process. Proper temperature control ensures that the steel remains within the optimal range for forging, allowing for precise shaping and consistent quality across all sockets produced.
The Forging Process Explained
During the forging process, heated steel billets are placed into forging dies that shape the socket blank. These dies are meticulously crafted to match the exact dimensions and specifications of the final impact socket. The steel is then subjected to high pressure, forcing it to conform to the die’s shape and form the basic structure of the socket.
This process not only shapes the steel but also refines its grain structure, enhancing the metal’s overall strength and toughness. The forging process aligns the grain flow with the direction of stress, which improves the socket’s ability to withstand high torque and repeated impacts. This alignment is essential for maintaining the socket’s durability and performance over time.
Grain Structure and Strength
The grain structure of the steel plays a significant role in the socket’s strength and durability. Proper forging techniques ensure that the grain flow is aligned with the direction of the applied forces, enhancing the socket’s ability to absorb and distribute stress. This alignment reduces the likelihood of cracks and fractures, allowing the socket to maintain its integrity under heavy use.
Refining the grain structure through controlled forging processes results in a more uniform and resilient metal, capable of withstanding the rigors of high-torque applications. This improved grain structure contributes to the overall longevity and reliability of the impact socket, making it a dependable tool for professionals and enthusiasts alike.
Benefits of Hot Forging in Impact Socket Manufacturing
Hot forging offers several benefits in the manufacturing of impact sockets, including increased strength, improved toughness, and enhanced durability. The process allows for the creation of complex shapes and precise dimensions, ensuring that each socket meets the exact specifications required for high-performance applications.
Additionally, hot forging reduces the need for extensive machining and finishing processes, as the basic shape and properties of the socket are established during forging. This efficiency not only lowers production costs but also contributes to a more consistent and reliable final product.
Quality Control During Forging
Maintaining strict quality control during the forging process is essential to ensure the consistency and reliability of impact sockets. Manufacturers implement comprehensive inspection and testing protocols to monitor the forging process, verifying that each socket meets the required specifications for size, shape, and material properties.
Regular inspections and tests help identify any defects or inconsistencies early in the manufacturing process, allowing for prompt corrective actions. This proactive approach ensures that only high-quality sockets proceed to the next stages of production, maintaining the overall integrity and performance of the final product.
Advanced Forging Techniques
Advancements in forging technology have further enhanced the quality and efficiency of impact socket manufacturing. Techniques such as precision forging and closed-die forging allow for greater control over the shaping process, resulting in sockets with superior dimensional accuracy and surface finish.
These advanced techniques also enable the production of sockets with complex geometries and specialized features, catering to specific user needs and applications. By leveraging these innovations, manufacturers can produce impact sockets that offer enhanced performance, durability, and versatility, meeting the diverse demands of the market.
Conclusion
The initial forging and forming processes are pivotal in the manufacturing of high-quality impact sockets. Hot forging, with its ability to shape steel into precise and durable forms, lays the foundation for sockets that can withstand high torque and repetitive impacts. By refining the grain structure and enhancing the metal’s strength and toughness, the forging process ensures that each socket is built to last. Advanced forging techniques and strict quality control measures further elevate the manufacturing process, resulting in impact sockets that deliver exceptional performance and reliability. This meticulous approach to forging guarantees that users receive tools that meet the highest standards of quality, making them indispensable for demanding applications across various industries.
Precision Machining and Internal Detailing
CNC Machining the Socket Interiors
After the forging process, precision machining is employed to refine the internal and external features of the impact sockets. Computer Numerical Control (CNC) machining plays a critical role in achieving the high level of accuracy and consistency required for these tools. CNC machines use programmed instructions to remove excess material and shape the socket’s interior and exterior to exact specifications.
This level of precision ensures that the drive size and fit are perfect, which is essential for the socket’s performance and longevity. Accurate machining minimizes the risk of stripping or damaging bolts and nuts during use, enhancing the socket’s reliability and safety. Additionally, CNC machining allows for the production of sockets with consistent dimensions, ensuring uniformity across large batches and reducing variability in performance.
Creating the Square Drive
The square drive is a fundamental component of an impact socket, providing the interface between the socket and the impact tool. Precision machining ensures that the square drive corners are crisp and uniformly sized, which is crucial for maintaining a secure fit and efficient torque transfer. Any inconsistencies in the drive size or shape can lead to slippage, stripping, or damage to both the socket and the fastener.
Advanced machining techniques are used to create sharp, well-defined edges on the square drive, enhancing the socket’s grip and stability during use. This precision is particularly important for heavy-duty applications where high torque levels are applied, as it ensures that the socket remains firmly attached to the impact tool, preventing accidents and tool failure.
Chamfering and Radius Edges
Chamfering and radius edges are essential finishing processes in the manufacturing of impact sockets. Chamfering involves beveling the edges of the socket to create a smooth transition between surfaces, which improves the socket’s fit and reduces stress concentration points. Radius edges further enhance the socket’s durability by distributing stress more evenly, preventing cracks and fractures from forming under high torque.
These finishing techniques not only improve the structural integrity of the socket but also enhance its overall functionality. Smooth, well-defined edges allow for easier insertion and removal of the socket from fasteners, reducing wear and tear on both the socket and the impact tool. Additionally, chamfered and radius edges contribute to the socket’s aesthetic appeal, giving it a polished and professional appearance.
Ensuring Tolerances Meet Strict Industry Standards
Precision machining ensures that all impact sockets meet strict industry tolerances and specifications. Manufacturers adhere to stringent quality control measures to verify that each socket aligns with the required dimensions and performance criteria. This adherence to standards guarantees that the sockets perform consistently and reliably across different applications and environments.
Regular inspections and measurements are conducted throughout the machining process to identify and correct any deviations from the specified tolerances. This meticulous attention to detail ensures that each impact socket meets the highest standards of quality and performance, providing users with tools they can trust for their most demanding tasks.
Enhancing Performance Through Precision Machining
Precision machining significantly enhances the performance of impact sockets by ensuring optimal fit, torque transfer, and durability. Accurate machining of the internal and external features allows the socket to perform efficiently under high-torque conditions, reducing the risk of tool slippage and wear. This efficiency translates to faster, more effective fastening and loosening of bolts and nuts, improving overall productivity.
Furthermore, the enhanced durability resulting from precision machining ensures that the sockets can withstand repeated use without degrading in performance. This longevity reduces the need for frequent replacements, providing users with cost-effective and reliable tools that maintain their functionality over time.
Incorporating Specialized Machining Techniques
In addition to standard CNC machining, specialized techniques are sometimes employed to enhance the performance and functionality of impact sockets. Techniques such as honing, grinding, and lapping may be used to achieve even higher levels of precision and surface finish. These advanced machining processes refine the socket’s surfaces, improving their smoothness and reducing friction during use.
Specialized machining techniques also allow for the creation of unique features, such as reinforced drive interfaces or specialized coatings, that further enhance the socket’s performance and durability. By integrating these advanced methods, manufacturers can produce impact sockets that offer superior functionality and reliability, meeting the specific needs of various applications and users.
Conclusion
Precision machining and internal detailing are crucial steps in the manufacturing of high-quality impact sockets. CNC machining ensures that each socket meets exact specifications, providing a secure fit and efficient torque transfer. Creating sharp, well-defined square drives and implementing chamfering and radius edges enhance the socket’s durability and functionality, preventing wear and tear under high-torque conditions. Adhering to strict industry tolerances guarantees consistent performance and reliability, making precision machining a cornerstone of impact socket production. By incorporating specialized machining techniques, manufacturers can further enhance the performance and longevity of their impact sockets, delivering tools that meet the highest standards of quality and excellence.
Heat Treatment: Hardening and Tempering
Why Heat Treatment Matters
Heat treatment is a critical process in the manufacturing of high-quality impact sockets, significantly enhancing their mechanical properties and overall performance. This process involves heating and cooling the steel in a controlled manner to alter its microstructure, thereby increasing its hardness, strength, and toughness. Proper heat treatment ensures that the impact sockets can withstand the high torque and repetitive impacts encountered during use without deforming or failing.
Without heat treatment, the steel used in impact sockets would be too soft and ductile, making it prone to wear, deformation, and cracking under stress. Heat treatment transforms the steel into a harder and more resilient material, capable of maintaining its shape and integrity even under extreme conditions. This transformation is essential for producing impact sockets that are durable, reliable, and safe for heavy-duty applications.
Hardening Processes
Hardening is the first stage of heat treatment, where the steel is heated to a high temperature to increase its hardness. This process involves heating the steel to a temperature where its crystal structure changes, allowing carbon atoms to diffuse and create a harder microstructure. The steel is then rapidly cooled, or quenched, typically in oil or water, to lock in this hardened structure.
The hardening process significantly increases the tensile strength and hardness of the steel, making the impact sockets more resistant to deformation and wear. However, without subsequent tempering, the steel would become too brittle, increasing the risk of cracking or shattering under impact.
Tempering Steps
Tempering is the second stage of heat treatment, following hardening. This process involves reheating the hardened steel to a lower temperature and then allowing it to cool slowly. Tempering reduces the brittleness introduced during hardening while maintaining much of the increased hardness and strength.
The tempering process restores some ductility to the steel, allowing it to absorb and dissipate energy more effectively during impacts. This balance between hardness and toughness ensures that the impact sockets can withstand repeated high-torque applications without failing. The specific tempering temperature and duration are carefully controlled to achieve the desired mechanical properties, tailored to the specific requirements of the impact sockets.
Achieving the Right Balance Between Hardness and Ductility
The key to effective heat treatment is achieving the right balance between hardness and ductility. While hardening increases the steel’s resistance to wear and deformation, tempering ensures that the steel remains tough and resistant to cracking. This balance is crucial for producing impact sockets that are both strong and resilient, capable of performing reliably under high-stress conditions.
Manufacturers meticulously control the heat treatment parameters to optimize this balance, ensuring that each impact socket meets the necessary performance standards. By fine-tuning the hardening and tempering processes, manufacturers can produce impact sockets that offer exceptional durability and reliability, providing users with tools they can depend on for demanding tasks.
Advanced Heat Treatment Techniques
Advancements in heat treatment technology have further enhanced the performance and quality of impact sockets. Techniques such as induction hardening, where the steel is rapidly heated using electromagnetic induction before quenching, offer greater control over the hardening process. This method allows for precise targeting of specific areas, improving the socket’s overall strength and durability.
Additionally, vacuum heat treatment processes reduce the risk of oxidation and contamination, resulting in a cleaner and more uniform microstructure. These advanced techniques contribute to the production of impact sockets with superior mechanical properties, enhancing their performance and longevity.
Quality Control in Heat Treatment
Maintaining strict quality control during the heat treatment process is essential to ensure the consistency and reliability of impact sockets. Manufacturers implement comprehensive testing and inspection protocols to verify that each socket achieves the desired hardness and toughness levels. Techniques such as hardness testing, microstructural analysis, and impact testing are used to assess the effectiveness of the heat treatment process.
Regular monitoring and calibration of heat treatment equipment also play a crucial role in maintaining consistent results. By adhering to stringent quality control measures, manufacturers can produce impact sockets that meet the highest standards of performance and durability, providing users with dependable tools for their most demanding applications.
Conclusion
Heat treatment is a vital process in the manufacturing of high-quality impact sockets, enhancing their hardness, strength, and toughness. Through precise hardening and tempering steps, manufacturers achieve the ideal balance between hardness and ductility, ensuring that impact sockets can withstand high torque and repeated impacts without compromising their integrity. Advanced heat treatment techniques and stringent quality control measures further elevate the performance and reliability of impact sockets, making them indispensable tools for professionals and enthusiasts alike. By investing in robust heat treatment processes, manufacturers deliver impact sockets that offer exceptional durability and reliability, meeting the highest standards of quality and performance.
Surface Treatments and Protective Coatings
Black Oxide Coating
Black oxide coating is a commonly used surface treatment for impact sockets, providing several functional and aesthetic benefits. This coating is achieved through a chemical reaction that converts the surface of the steel into magnetite, a stable black oxide. The primary purpose of black oxide coating is to enhance the socket’s corrosion resistance, protecting it from rust and other forms of oxidation that can degrade the steel over time.
In addition to its protective qualities, black oxide coating reduces glare, making the sockets easier to identify and use in various lighting conditions. This feature is particularly useful in automotive repair shops and industrial settings where bright lights can cause reflections and hinder visibility. The sleek black finish also gives impact sockets a professional and uniform appearance, contributing to their overall aesthetic appeal.
Corrosion Resistance and Reduced Glare
The black oxide coating significantly improves the corrosion resistance of impact sockets, extending their service life and maintaining their appearance even in harsh environments. By forming a protective barrier on the steel’s surface, the coating prevents moisture, chemicals, and other corrosive agents from reaching the underlying metal, reducing the risk of rust and degradation.
Reduced glare is another advantage of black oxide coating, enhancing the usability of impact sockets in brightly lit workspaces. The matte black finish minimizes reflections, allowing users to see clearly when working in well-lit areas without the distraction of shining surfaces. This feature contributes to improved safety and efficiency, enabling users to focus on their tasks without visual impediments.
Alternative Finishes
While black oxide is a popular choice, there are alternative finishes and coatings available for impact sockets, each offering unique benefits. Phosphate coatings, for example, provide additional corrosion resistance and enhance the socket’s surface hardness, further increasing its durability. These coatings are particularly useful in environments where impact sockets are exposed to aggressive chemicals or extreme weather conditions.
Special anti-rust treatments, such as zinc plating or ceramic coatings, are also used to protect impact sockets from corrosion and wear. These treatments offer superior protection against environmental factors, ensuring that the sockets remain in optimal condition even after prolonged use. Additionally, some manufacturers offer decorative coatings that provide a distinctive look while maintaining the socket’s protective properties.
Marking and Labeling
Clear and precise marking and labeling are essential features of high-quality impact sockets. Laser etching or engraving is commonly used to mark size indicators, part numbers, and brand logos on the sockets. These markings provide easy identification, allowing users to quickly select the correct socket size and type for their specific needs.
Precise labeling also helps prevent confusion and errors during use, ensuring that the right socket is used for each application. Clear markings contribute to the overall organization and efficiency of toolkits, making it easier for users to locate and use their impact sockets effectively. Additionally, branded logos and identifiers reinforce brand recognition and trust, highlighting the socket’s quality and origin.
Enhancing Durability Through Surface Treatments
Surface treatments and protective coatings play a crucial role in enhancing the durability and longevity of impact sockets. By providing a protective barrier against corrosion, wear, and environmental damage, these treatments ensure that the sockets maintain their structural integrity and performance over time. This enhanced durability reduces the need for frequent replacements, offering users cost-effective and reliable tools.
Moreover, surface treatments improve the socket’s resistance to abrasions and impacts, preventing surface damage that can compromise the socket’s functionality. This resistance is particularly important in high-torque applications where repeated impacts can cause significant wear and tear. By protecting the socket’s surface, these treatments extend the tool’s service life and maintain its performance, making them indispensable for demanding applications.
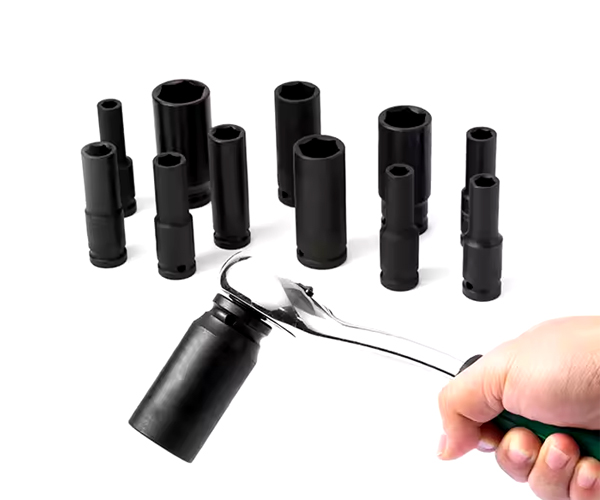
Customization and Branding
Manufacturers often offer customization options for impact sockets, allowing businesses to incorporate their branding and unique design elements. Custom coatings, engravings, and color schemes enable companies to differentiate their products from competitors and reinforce their brand identity. Personalized markings and logos enhance the professional appearance of the sockets, making them a valuable addition to branded toolkits.
Customization also extends to functional features, such as specialized coatings that provide additional protection or unique design elements that improve grip and handling. By offering tailored solutions, manufacturers cater to the specific needs and preferences of their customers, ensuring that the impact sockets meet their unique requirements and enhance their overall tool experience.
Conclusion
Surface treatments and protective coatings are integral components in the manufacturing of high-quality impact sockets, providing essential benefits such as corrosion resistance, reduced glare, and enhanced durability. Black oxide coating is a popular choice, offering both functional and aesthetic advantages, while alternative finishes provide additional protection and customization options. Clear marking and labeling improve usability and organization, ensuring that impact sockets are easy to identify and use effectively. By incorporating these surface treatments, manufacturers enhance the performance and longevity of impact sockets, delivering reliable and durable tools that meet the highest standards of quality and functionality.
Quality Control and Testing Procedures
Dimensional Inspections
Dimensional inspections are a fundamental aspect of quality control in the manufacturing of impact sockets. These inspections ensure that each socket meets precise size and dimensional specifications, which are critical for proper fit and performance. Advanced measuring tools, such as coordinate measuring machines (CMM) and digital calipers, are used to verify the accuracy of each socket’s dimensions, including drive size, socket length, and overall geometry.
Consistency in dimensions across all sockets is essential for maintaining uniform performance and reliability. Any deviations from the specified measurements can lead to improper fit, slippage, or damage to both the socket and the fastener. By conducting thorough dimensional inspections, manufacturers can identify and correct any inconsistencies early in the production process, ensuring that only sockets that meet strict size criteria proceed to the next stages of manufacturing.
Torque and Impact Tests
Torque and impact tests are critical for verifying the strength and durability of impact sockets. These tests simulate the high-torque conditions that the sockets will encounter during actual use, ensuring that they can withstand the stresses without deforming or failing. Torque tests measure the socket’s ability to handle specific torque levels, while impact tests evaluate its performance under repeated high-impact forces.
During torque testing, sockets are subjected to increasing levels of torque until they reach their maximum capacity. This process identifies the socket’s breaking point and ensures that it can safely handle the intended load without failure. Impact testing involves repeatedly striking the socket with an impact driver or wrench, mimicking the real-world conditions of high-torque applications. This testing evaluates the socket’s ability to maintain its integrity and performance under continuous stress.
Hardness Testing and Material Verification
Hardness testing and material verification are essential components of quality control in impact socket manufacturing. These tests assess the steel’s hardness and composition, ensuring that it meets the required standards for strength and durability. Common hardness testing methods include Rockwell hardness tests, which measure the material’s resistance to indentation, providing an indication of its overall hardness and strength.
Material verification involves analyzing the steel’s chemical composition to confirm that it contains the appropriate alloying elements, such as chromium, molybdenum, and vanadium. This verification ensures that the steel possesses the necessary properties for high-performance impact sockets, including hardness, tensile strength, and toughness. By conducting thorough hardness and material tests, manufacturers can ensure that each socket meets the specified requirements and performs reliably under demanding conditions.
Random Batch Inspections
Random batch inspections are a key strategy in maintaining consistent quality across large production runs of impact sockets. Instead of inspecting every single socket, a random sampling of sockets from each batch is selected for thorough examination. This approach allows manufacturers to assess the overall quality of the batch without incurring the time and cost associated with 100% inspection.
During random batch inspections, selected sockets undergo a series of tests, including dimensional measurements, torque and impact tests, and hardness assessments. The results of these inspections provide insights into the batch’s overall quality and consistency. If any defects or inconsistencies are detected, corrective actions can be taken to address the issues before the entire batch proceeds to the next stage of production.
Quality Assurance Programs
Quality assurance programs are comprehensive frameworks that encompass all aspects of the manufacturing process, from raw material sourcing to final product testing. These programs are designed to ensure that every impact socket produced meets the highest standards of quality and performance. Key components of quality assurance programs include:
- Standard Operating Procedures (SOPs): Detailed guidelines that outline the steps and processes involved in manufacturing impact sockets, ensuring consistency and adherence to best practices.
- Continuous Improvement: Ongoing efforts to identify and implement improvements in the manufacturing process, enhancing efficiency, quality, and reliability.
- Employee Training: Comprehensive training programs for manufacturing staff, ensuring that they possess the necessary skills and knowledge to produce high-quality impact sockets.
- Documentation and Traceability: Maintaining detailed records of the manufacturing process, including material specifications, inspection results, and testing data, to ensure traceability and accountability.
By implementing robust quality assurance programs, manufacturers can consistently produce impact sockets that meet or exceed industry standards, providing users with reliable and durable tools.
Compliance with Industry Standards
Compliance with industry standards is a crucial aspect of quality control in impact socket manufacturing. Adhering to standards such as ASME (American Society of Mechanical Engineers) and ISO (International Organization for Standardization) ensures that the sockets meet established criteria for performance, safety, and quality. These standards provide a benchmark for manufacturers to evaluate and improve their products, ensuring consistency and reliability across the industry.
Compliance with industry standards also facilitates the acceptance of impact sockets in global markets, as customers and regulatory bodies recognize and trust products that meet these established benchmarks. By aligning their manufacturing processes with industry standards, manufacturers can enhance their reputation, build customer trust, and expand their market reach.
Conclusion
Quality control and testing procedures are integral to the manufacturing of high-quality impact sockets, ensuring that each socket meets the necessary standards for performance, durability, and safety. Dimensional inspections, torque and impact tests, hardness testing, and material verification are essential for maintaining consistency and reliability across all sockets produced. Random batch inspections and comprehensive quality assurance programs further enhance the manufacturing process, allowing for continuous improvement and adherence to industry standards. By implementing rigorous quality control measures, manufacturers deliver impact sockets that users can trust to perform reliably in demanding applications, reinforcing the importance of quality in tool manufacturing.
Industry Standards, Certifications, and Compliance
Common Standards (e.g., ASME, ISO)
Adherence to industry standards is a critical aspect of manufacturing high-quality impact sockets. Standards set by organizations such as the American Society of Mechanical Engineers (ASME) and the International Organization for Standardization (ISO) provide guidelines for the design, production, and testing of impact sockets, ensuring consistency, safety, and reliability across the industry.
ASME standards, for example, outline specific requirements for the dimensions, materials, and performance characteristics of impact sockets. These standards ensure that sockets are manufactured to precise specifications, guaranteeing a consistent fit and performance across different tools and applications. ISO standards complement these guidelines by providing a framework for quality management systems, ensuring that manufacturers maintain high levels of quality control and continuous improvement in their production processes.
What These Standards Mean and Why They Matter
Compliance with ASME, ISO, and other industry standards signifies that impact sockets meet established criteria for quality, safety, and performance. These standards provide a benchmark for manufacturers to evaluate and enhance their products, ensuring that they deliver reliable and durable tools to users. Adherence to these standards also facilitates the acceptance of impact sockets in global markets, as customers and regulatory bodies recognize and trust products that meet these established benchmarks.
Moreover, compliance with industry standards enhances the reputation of manufacturers, demonstrating their commitment to quality and excellence. This commitment builds trust with customers, who can rely on certified impact sockets to perform consistently and safely in their demanding applications.
Quality Assurance Programs
Quality assurance programs are comprehensive frameworks that encompass all aspects of the manufacturing process, from raw material sourcing to final product testing. These programs are designed to ensure that every impact socket produced meets the highest standards of quality and performance. Key components of quality assurance programs include:
- Standard Operating Procedures (SOPs): Detailed guidelines that outline the steps and processes involved in manufacturing impact sockets, ensuring consistency and adherence to best practices.
- Continuous Improvement: Ongoing efforts to identify and implement improvements in the manufacturing process, enhancing efficiency, quality, and reliability.
- Employee Training: Comprehensive training programs for manufacturing staff, ensuring that they possess the necessary skills and knowledge to produce high-quality impact sockets.
- Documentation and Traceability: Maintaining detailed records of the manufacturing process, including material specifications, inspection results, and testing data, to ensure traceability and accountability.
By implementing robust quality assurance programs, manufacturers can consistently produce impact sockets that meet or exceed industry standards, providing users with reliable and durable tools.
ISO Certifications and Continuous Improvement Measures
ISO certifications, such as ISO 9001, are internationally recognized standards that validate a company’s quality management system. Achieving ISO certification demonstrates that a manufacturer has implemented effective quality control measures and is committed to continuous improvement. These certifications involve rigorous assessments and audits, ensuring that manufacturers adhere to best practices in quality management and production processes.
Continuous improvement measures, such as lean manufacturing and Six Sigma methodologies, further enhance the quality and efficiency of impact socket production. These initiatives focus on identifying and eliminating waste, reducing variability, and optimizing processes to achieve higher levels of quality and performance. By embracing continuous improvement, manufacturers can maintain their competitive edge, consistently deliver high-quality impact sockets, and adapt to evolving market demands.
Meeting Global Market Requirements
Meeting global market requirements is essential for manufacturers aiming to distribute impact sockets internationally. Different regions may have specific regulations, certifications, and standards that impact socket manufacturers must comply with to enter and succeed in those markets. Understanding and adhering to these regional requirements ensures that impact sockets are accepted and trusted by customers worldwide.
For instance, European markets may require impact sockets to comply with CE marking and specific DIN (Deutsches Institut für Normung) standards, while North American markets may prioritize ASME certifications. Manufacturers must adapt their production processes and quality control measures to meet these diverse requirements, ensuring that their products are compatible with various regional standards and regulations.
Additionally, meeting global market requirements involves understanding and addressing the unique needs and preferences of different customer bases. This may include offering customization options, adhering to specific design standards, or providing tailored solutions that cater to the specific demands of each market segment.
Importance of Compliance in Building Trust
Compliance with industry standards and certifications plays a crucial role in building trust with customers and partners. When manufacturers demonstrate adherence to recognized standards, they signal their commitment to quality, safety, and reliability. This trust is essential for establishing long-term relationships with customers, who rely on certified impact sockets to perform consistently and safely in their applications.
Moreover, compliance with standards enhances the credibility of manufacturers, distinguishing them from competitors who may not prioritize quality and adherence to industry guidelines. This credibility is particularly important in competitive markets, where customers seek assurance that the tools they purchase meet the highest standards of performance and safety.
Conclusion
Industry standards, certifications, and compliance are integral components of high-quality impact socket manufacturing. Adhering to standards set by organizations like ASME and ISO ensures that impact sockets meet established criteria for quality, safety, and performance, fostering trust and reliability among users. Comprehensive quality assurance programs, ISO certifications, and continuous improvement measures further enhance the manufacturing process, ensuring consistency and excellence in every socket produced. Meeting global market requirements expands the reach of manufacturers, allowing their products to be trusted and accepted worldwide. By prioritizing compliance and quality, manufacturers can deliver impact sockets that meet the highest standards, providing users with dependable and durable tools for their most demanding tasks.
Packaging, Labeling, and Shipping Requirements
Protecting Finished Products
Effective packaging is essential for protecting finished impact sockets during transportation and storage. Manufacturers use robust packaging materials, such as custom foam inserts, sturdy boxes, or blister packs, to safeguard the sockets from physical damage, moisture, and environmental factors. These protective measures ensure that the sockets arrive at their destination in pristine condition, ready for use.
Custom foam inserts are often tailored to fit the specific shape and size of the impact sockets, providing a secure and cushioned environment that absorbs shocks and impacts during transit. Sturdy boxes offer additional protection against crushing and punctures, maintaining the integrity of the sockets throughout the shipping process. Blister packs, with their clear plastic coverings, provide visibility while also protecting the sockets from dust and moisture.
Labeling for Easy Identification
Clear and precise labeling is crucial for the easy identification and organization of impact sockets. Manufacturers implement labeling systems that include size markers, part numbers, and brand logos on each socket. These labels facilitate quick selection and identification, allowing users to find the right socket size and type efficiently.
Laser etching or engraving is commonly used to mark size indicators and other essential information directly onto the socket’s surface. This method ensures that the markings are permanent, resistant to wear, and easily readable, even in challenging work environments. Clear labeling helps prevent errors and confusion, enhancing the overall usability and efficiency of the impact sockets.
Branding and Product Information
In addition to size and part number markings, packaging often includes branding elements and product information to reinforce the manufacturer’s identity and provide essential details to the user. Brand logos and names are prominently displayed on the packaging, enhancing brand recognition and trust. Product information, such as usage instructions, material specifications, and performance characteristics, is included to inform users about the features and benefits of the impact sockets.
Including detailed product information on the packaging helps users make informed purchasing decisions, understanding the value and capabilities of the sockets they are acquiring. This transparency builds trust and confidence in the product, encouraging customer satisfaction and loyalty.
Logistics and Transport
Efficient logistics and transport are vital for ensuring that impact sockets reach their destination promptly and in excellent condition. Manufacturers work with reliable logistics partners to manage the transportation process, coordinating the movement of products from the factory to distribution centers, retailers, or directly to customers.
Proper handling and storage during transit are crucial for maintaining the quality and integrity of the impact sockets. Packaging is designed to withstand the rigors of transportation, protecting the sockets from impacts, vibrations, and environmental conditions that could compromise their performance. Additionally, manufacturers implement tracking systems to monitor shipments, providing visibility and ensuring timely delivery.
Handling Documentation and Customs Requirements
For manufacturers exporting impact sockets to international markets, handling documentation and customs requirements is a critical aspect of the shipping process. Accurate and complete documentation, including invoices, packing lists, and certificates of origin, is essential for facilitating smooth customs clearance and avoiding delays or penalties.
Understanding and complying with the specific customs regulations of each destination country ensures that shipments are processed efficiently and reach their intended recipients without issues. Manufacturers stay informed about the latest import/export regulations and work closely with logistics partners to navigate the complexities of international shipping, ensuring that impact sockets are delivered reliably and on time.
Sustainable Packaging Practices
Sustainability is becoming increasingly important in packaging and shipping practices. Manufacturers are adopting eco-friendly packaging materials and methods to reduce their environmental impact and meet the growing demand for sustainable products. This includes using recyclable or biodegradable packaging materials, minimizing packaging waste, and optimizing packaging sizes to reduce transportation emissions.
Sustainable packaging practices not only benefit the environment but also enhance the brand’s reputation, appealing to environmentally conscious consumers who prioritize sustainability in their purchasing decisions. By integrating sustainable practices into their packaging and shipping processes, manufacturers contribute to the preservation of natural resources and demonstrate their commitment to environmental responsibility.
Conclusion
Packaging, labeling, and shipping are integral components of the impact socket manufacturing process, ensuring that the finished products reach users in excellent condition and are easy to identify and use. Protective packaging materials safeguard the sockets during transit, while clear labeling and branding enhance usability and brand recognition. Efficient logistics and compliance with customs requirements facilitate timely and reliable delivery, while sustainable packaging practices contribute to environmental responsibility. By prioritizing these aspects, manufacturers can deliver high-quality impact sockets that meet customer expectations and maintain their integrity throughout the shipping process, reinforcing the importance of comprehensive packaging and logistics strategies in tool manufacturing.
Choosing the Right Manufacturer
What Buyers Should Look For
Selecting the right manufacturer is crucial for businesses seeking high-quality impact sockets that meet their specific needs. Buyers should prioritize manufacturers with a strong reputation for quality, reliability, and customer service. Key factors to consider include the manufacturer’s track record, certifications, and ability to consistently deliver products that meet or exceed industry standards.
Reputable manufacturers often have extensive experience in producing impact sockets, demonstrating their expertise and commitment to quality. Reviews, testimonials, and case studies from existing customers can provide valuable insights into the manufacturer’s performance and reliability. Additionally, manufacturers with recognized certifications, such as ISO 9001, indicate a commitment to maintaining high standards in their quality management systems.
Evaluating OEM Capabilities
Original Equipment Manufacturer (OEM) capabilities are a significant advantage when choosing a manufacturer for impact sockets. OEM capabilities allow manufacturers to customize impact sockets to meet the specific requirements of buyers, including size variations, material specifications, and branding options. This flexibility is essential for businesses that need impact sockets tailored to their unique applications and branding strategies.
When evaluating OEM capabilities, buyers should consider the manufacturer’s ability to accommodate custom orders, their expertise in design and engineering, and their willingness to collaborate on product development. Manufacturers with strong OEM capabilities can provide tailored solutions that enhance the functionality and branding of impact sockets, meeting the precise needs of their clients.
Assessing Production Capacity and Lead Times
Production capacity and lead times are critical factors in ensuring that manufacturers can meet the demand and delivery schedules of buyers. Assessing a manufacturer’s production capacity involves evaluating their manufacturing facilities, equipment, and workforce to determine their ability to handle large orders and maintain consistent output.
Lead times, or the time required to produce and deliver impact sockets, are equally important. Buyers should inquire about the manufacturer’s typical lead times for different order sizes and customization options, ensuring that they align with their business needs and project timelines. Manufacturers with efficient production processes and reliable supply chains can offer shorter lead times, enabling buyers to receive their orders promptly and maintain smooth operations.
Quality Assurance and Certifications
Quality assurance and certifications are indicators of a manufacturer’s commitment to producing high-quality impact sockets. Certifications such as ISO 9001 demonstrate that the manufacturer has implemented robust quality management systems and adheres to international standards for quality and efficiency.
Quality assurance measures, including rigorous testing, inspections, and continuous improvement initiatives, ensure that each impact socket meets the required specifications and performance criteria. Buyers should inquire about the manufacturer’s quality control processes, testing procedures, and any additional certifications that validate the quality and reliability of their products.
Communication and Responsiveness
Effective communication and responsiveness are essential for a successful partnership with a manufacturer. Buyers should choose manufacturers that are accessible, responsive, and willing to engage in open and transparent communication. This ensures that any questions, concerns, or customization requests are addressed promptly and efficiently.
Manufacturers that prioritize clear and consistent communication are more likely to understand and meet the specific needs of their clients, fostering a collaborative and productive relationship. Responsive manufacturers can also provide timely updates on order status, production progress, and any potential issues, allowing buyers to plan and manage their projects effectively.
Evaluating Sample Products
Requesting sample products is a crucial step in evaluating a manufacturer’s quality and capabilities. Samples provide firsthand experience of the manufacturer’s craftsmanship, material quality, and overall performance of their impact sockets. By examining and testing samples, buyers can assess whether the sockets meet their quality standards and functional requirements.
Samples also offer an opportunity to evaluate the manufacturer’s attention to detail, finish quality, and consistency. This hands-on evaluation helps buyers make informed decisions, ensuring that they choose a manufacturer that can deliver the high-quality impact sockets they require.
Pricing and Value
While pricing is an important consideration, buyers should focus on the overall value offered by the manufacturer rather than solely on cost. High-quality impact sockets may come at a higher price point, but the investment is justified by the durability, reliability, and performance they provide. Buyers should consider factors such as material quality, manufacturing processes, customization options, and after-sales support when evaluating the value offered by a manufacturer.
Comparing prices with other manufacturers while considering the overall quality and service can help buyers find a balance between cost and value, ensuring that they receive impact sockets that meet their needs without compromising on quality.
Conclusion
Choosing the right manufacturer is a critical decision for businesses seeking high-quality impact sockets. By evaluating factors such as reputation, OEM capabilities, production capacity, quality assurance, communication, and pricing, buyers can identify manufacturers that align with their specific needs and standards. Requesting samples and assessing certifications further ensure that the chosen manufacturer can deliver reliable and durable impact sockets that meet industry standards and performance requirements. Making an informed choice in selecting a manufacturer not only enhances the quality and reliability of the impact sockets but also fosters a successful and long-term partnership, contributing to the overall success and efficiency of the buyer’s operations.
Innovations, Trends, and the Future of Impact Socket Manufacturing
Advanced Materials and Alloys
The manufacturing of impact sockets is continuously evolving, with advancements in materials and alloys playing a significant role in enhancing performance and durability. Researchers and manufacturers are exploring new steel compositions that offer even greater strength, toughness, and wear resistance. Innovations in metallurgy allow for the development of alloys that can withstand higher torque levels and resist deformation and fatigue over extended periods.
These advanced materials not only improve the longevity of impact sockets but also enhance their performance in demanding applications. By leveraging cutting-edge materials, manufacturers can produce impact sockets that offer superior strength and durability, meeting the increasing demands of professionals and enthusiasts alike.
Automation and Robotics in Production
Automation and robotics are revolutionizing the manufacturing process of impact sockets, increasing efficiency, precision, and consistency. Automated systems streamline various stages of production, from forging and machining to heat treatment and finishing. Robotics enhance the accuracy of these processes, reducing human error and ensuring that each socket meets exact specifications.
The integration of automation and robotics also accelerates production rates, allowing manufacturers to meet high demand while maintaining quality standards. This technological advancement not only improves productivity but also reduces production costs, making high-quality impact sockets more accessible to a broader range of users.
Data-Driven Quality Improvements
Data-driven approaches are increasingly being adopted in impact socket manufacturing to enhance quality and performance. By collecting and analyzing data from various stages of production, manufacturers can identify patterns, optimize processes, and implement continuous improvements. Sensors and monitoring systems track critical parameters such as temperature, pressure, and torque during manufacturing, providing real-time insights into the production process.
This data-driven approach enables manufacturers to detect and address issues proactively, ensuring consistent quality and minimizing defects. Additionally, the use of data analytics helps in predicting maintenance needs and optimizing production schedules, further enhancing efficiency and reliability in impact socket manufacturing.
Sustainability and Environmental Considerations
Sustainability is becoming a key focus in impact socket manufacturing, with manufacturers adopting eco-friendly practices to reduce their environmental impact. This includes using recyclable materials, minimizing waste through optimized production processes, and implementing energy-efficient technologies. Sustainable manufacturing practices not only benefit the environment but also align with the growing consumer demand for environmentally responsible products.
Manufacturers are also exploring the use of eco-friendly coatings and surface treatments that provide the necessary protection and durability while reducing the use of harmful chemicals. By prioritizing sustainability, manufacturers contribute to the preservation of natural resources and demonstrate their commitment to environmental responsibility, appealing to environmentally conscious consumers.
Integration of Smart Technologies
The integration of smart technologies is paving the way for innovative advancements in impact socket manufacturing. Smart impact sockets equipped with sensors and connectivity features can provide real-time data on usage, performance, and maintenance needs. This technology enables users to monitor the condition of their tools, track usage patterns, and receive alerts for maintenance or replacement, enhancing the overall efficiency and reliability of their toolkits.
Smart technologies also facilitate better inventory management and supply chain optimization, allowing manufacturers and users to track and manage their impact sockets more effectively. This integration of technology not only improves the functionality and performance of impact sockets but also enhances the user experience by providing valuable insights and data-driven recommendations.
Customization and Personalization
Customization and personalization are becoming increasingly important trends in impact socket manufacturing. Manufacturers are offering more options for customizing impact sockets to meet the specific needs and preferences of users. This includes variations in size, drive types, coatings, and branding options, allowing businesses and individuals to tailor their toolkits to their unique requirements.
Personalization also extends to ergonomic features and specialized designs that enhance the usability and performance of impact sockets. By offering customized solutions, manufacturers cater to a diverse range of applications and user preferences, ensuring that impact sockets meet the specific demands of different industries and tasks.
Conclusion
The future of impact socket manufacturing is marked by continuous innovation and adaptation to emerging trends. Advanced materials and alloys, automation and robotics, data-driven quality improvements, sustainability, smart technologies, and customization are driving significant advancements in the industry. These innovations enhance the performance, durability, and functionality of impact sockets, meeting the evolving needs of professionals and enthusiasts across various applications.
Manufacturers that embrace these trends and invest in cutting-edge technologies and sustainable practices are well-positioned to lead the industry, delivering high-quality impact sockets that offer superior performance and reliability. As the demand for efficient, durable, and customizable tools continues to grow, the manufacturing of impact sockets will continue to evolve, providing users with the tools they need to perform their tasks effectively and safely.
Maintenance, Care, and Maximizing Tool Life
Proper Cleaning and Storage
Proper maintenance of impact sockets is essential for maximizing their longevity and ensuring consistent performance. After each use, sockets should be thoroughly cleaned to remove any dirt, grease, or debris that can cause corrosion or wear over time. Using a clean cloth or brush, remove any visible contaminants from the socket’s surface, paying particular attention to the drive interface and any crevices where debris can accumulate.
Once cleaned, sockets should be dried completely to prevent moisture from causing rust or corrosion. Applying a light coating of oil or a protective spray can provide an additional layer of protection against moisture and environmental factors, further extending the socket’s lifespan.
Proper storage is equally important for maintaining the condition of impact sockets. Sockets should be stored in a dry, well-ventilated area to minimize exposure to moisture and prevent rust formation. Organizing sockets in a tool chest or storage rack ensures that they are kept in an orderly manner, reducing the risk of damage from accidental impacts or misplacement.
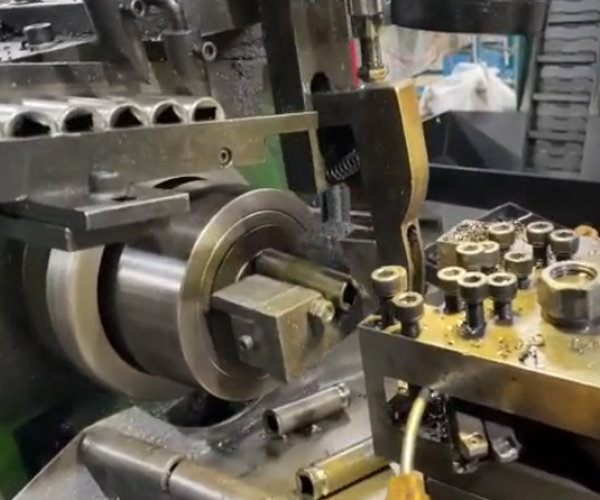
Checking for Signs of Wear
Regular inspection of impact sockets is crucial for identifying signs of wear and addressing issues before they lead to tool failure. Users should periodically examine their sockets for any visible signs of damage, such as cracks, deformation, or excessive wear on the drive interface. These indicators can signify that the socket is nearing the end of its service life and may require replacement.
In addition to visual inspections, users can perform functional checks to assess the socket’s performance. Testing the socket with different impact tools and fasteners can help identify any inconsistencies or performance issues that may indicate underlying wear or damage. Addressing these signs of wear promptly ensures that the sockets remain reliable and safe to use, preventing potential accidents and maintaining tool efficiency.
Proactive Maintenance Tips
Implementing proactive maintenance practices can significantly enhance the lifespan and performance of impact sockets. Regular lubrication of the drive interface and other moving parts reduces friction and wear, ensuring smooth operation and preventing damage from high-torque applications. Using appropriate lubricants, such as penetrating oils or silicone sprays, helps maintain the socket’s functionality and reduces the risk of corrosion.
Establishing a routine maintenance schedule, including regular cleaning, inspections, and lubrication, ensures that impact sockets are kept in optimal condition. This proactive approach not only extends the tool’s lifespan but also enhances its performance, providing users with reliable and efficient tools for their tasks.
Safe Usage Guidelines
Proper usage of impact sockets is essential for maximizing their lifespan and ensuring safety during use. Users should always select the correct socket size and drive type for their specific application, avoiding the use of sockets that are too small or too large for the fasteners being worked on. Using the appropriate socket size ensures a secure fit, reducing the risk of slippage and damage to both the socket and the fastener.
Impact sockets should be used with compatible impact tools, such as impact wrenches or drivers, to ensure optimal torque transfer and performance. Avoiding the use of sockets with damaged or worn drive interfaces further prevents tool failure and enhances safety.
Additionally, users should follow proper handling techniques, such as maintaining a firm grip on the impact tool and applying steady, controlled force during use. These practices reduce the risk of accidental drops, slips, or other mishaps that can damage the sockets or cause injuries.
Professional Maintenance Services
For businesses and professionals who rely heavily on impact sockets, utilizing professional maintenance services can ensure that their tools remain in top condition. Professional maintenance services offer comprehensive cleaning, inspection, and repair services, addressing any issues that may arise and maintaining the sockets’ performance and reliability.
Regular professional maintenance can identify and rectify potential problems before they escalate, preventing costly downtime and tool failure. Additionally, professional services can provide specialized treatments, such as advanced coatings or refinishing, to enhance the socket’s durability and appearance, further extending its service life.
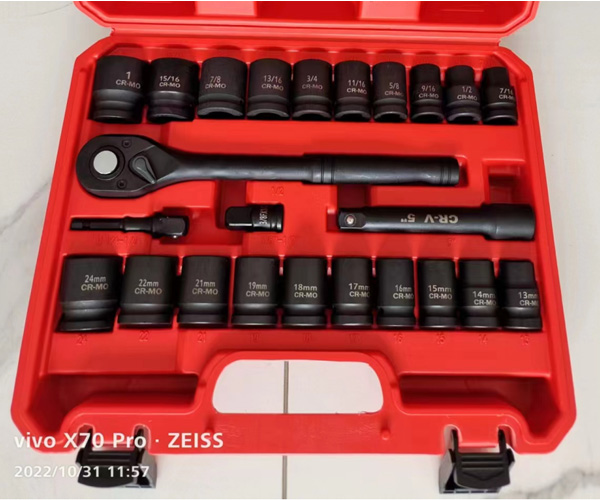
Conclusion
Proper maintenance and care are essential for maximizing the lifespan and performance of impact sockets. Regular cleaning, inspection, and lubrication ensure that sockets remain in optimal condition, preventing corrosion, wear, and damage. Implementing proactive maintenance practices and following safe usage guidelines further enhance the reliability and safety of impact sockets, providing users with dependable tools for their most demanding tasks. For businesses and professionals, utilizing professional maintenance services offers an additional layer of assurance, ensuring that impact sockets are consistently maintained and ready for use. By prioritizing maintenance and care, users can maximize the value and longevity of their impact sockets, ensuring sustained performance and efficiency in their operations.
Now, let’s wrap it up, understanding the manufacturing process of high-quality impact sockets reveals the meticulous attention to detail and advanced techniques that ensure these tools perform reliably under the most demanding conditions. From selecting the right steel and precision forging to implementing rigorous quality control and innovative surface treatments, each step is designed to enhance the socket’s strength, durability, and functionality. The incorporation of advanced materials, automation, and smart technologies further elevates the quality and performance of impact sockets, meeting the evolving needs of professionals and enthusiasts alike.
Choosing the right manufacturer is crucial, as it ensures that the impact sockets you rely on are produced to the highest standards, offering consistent performance and longevity. By prioritizing quality, compliance with industry standards, and continuous improvement, manufacturers deliver impact sockets that users can trust to handle their toughest tasks with ease and efficiency.
You might be asking, what next? If you’re in the market for reliable and high-performance impact sockets, consider partnering with a reputable manufacturer that prioritizes quality and innovation. Request samples, evaluate their quality assurance processes, and explore customization options to find the perfect fit for your specific needs. Invest in impact sockets that not only meet but exceed your expectations, ensuring that your tools are up to the task and built to last.
Feel secure knowing that with the right impact sockets, your work will be more efficient, safer, and more productive. Don’t settle for less when it comes to essential tools that drive your success. Here’s another thing, make an informed decision today and elevate your toolkit with impact sockets that reflect your commitment to quality and excellence. Embrace the reliability and performance of high-quality impact sockets and watch as they transform your work, providing the strength and durability you need to achieve your goals and thrive in your endeavors.
FAQ Section
You might have questions, right? That’s normal. Below are common inquiries:
Q: How do I confirm product quality before placing big orders?
One approach involves requesting sample batches, inspecting hardness tests, verifying material compositions, and confirming dimensional accuracy. Once satisfied, scale up orders confidently.
Q: Can they match brand colors or special finishes for my sockets?
Absolutely. They handle OEM requests gracefully. You can propose unique colors, coatings, or engravings that differentiate your products from mainstream offerings.
Q: How long does production usually take?
Lead times vary depending on order complexity and volume. Communicating requirements early helps them provide accurate estimates, ensuring you plan inventory strategies accordingly.
Q: Are shipping and logistics reliable?
Yes, they work with established logistics partners, organizing shipments that reach destinations promptly. Transparent tracking info keeps you informed, preventing unpleasant surprises.
Q: What if I need changes after production starts?
Discuss adjustments immediately. They aim for flexibility whenever possible. Early communication ensures minimal disruption and timely resolution.
Q: Do they offer any certifications or references?
Yes, they often hold necessary quality certifications and may provide references from satisfied clients. Checking these credentials builds confidence and reassures you that you’ve chosen wisely.