Introduction
It’s easy to overlook material differences when you’re shopping for impact sockets. Folks often assume that any heavy-duty socket is basically the same, which can lead to costly mistakes later. Here’s the deal: Impact sockets experience tremendous torque and repeated jolts, so the alloys and manufacturing processes behind them must be spot-on. The last thing anyone wants is a socket that shatters under pressure, sending metal fragments flying. Professionals rely on impact sockets for automotive work, industrial maintenance, and high-level repair tasks that demand both strength and consistency. That’s why so many experts keep talking about the importance of carefully selected metals like chrome molybdenum or chrome vanadium. A broken or poorly machined socket might stall projects or even cause injuries, which is why material quality isn’t just about marketing—it’s about tangible user safety and enhanced tool longevity.
Manufacturers also know that users care about cost-effectiveness, so they strive to find alloys that deliver maximum performance without pushing the price tag too high. If you’re running a workshop or a garage where time is money, then consistent reliability becomes the number one concern. You might be wondering if all this talk about steel composition and heat treatment really matters. Absolutely. Quality control processes ensure that every batch of material meets specific standards for impact and tensile strength, thereby reducing the risk of fractures. Knowing you have a socket that won’t crack under pressure frees you to work efficiently and focus on technique rather than second-guessing your tools. In the end, understanding impact socket materials means you’re prepared to invest wisely and avoid the frustration that comes from cheap alternatives.
What Exactly Is an Impact Socket?
Defining the Tool
Impact sockets are specialized attachments engineered for high-torque environments. They look similar to standard hand-tool sockets, yet they sport thicker walls, different alloy compositions, and design features that dissipate extreme rotational forces. Standard sockets usually can’t handle continuous hammering from an impact wrench or pneumatic driver. The repeated force eventually leads to cracks or warping. Because of that, impact sockets serve as problem-solvers when the job calls for serious strength.
Primary Uses
Automotive specialists dealing with stubborn nuts on suspension systems or lug nuts on wheels regularly turn to impact sockets. Construction workers also apply them for heavy equipment maintenance, and industrial technicians rely on them for large-scale machinery overhauls. That repetitive push-pull torque—combined with sudden jolts—demands superior durability. It’s not just about dismantling a stuck bolt. Now listen up: Impact sockets often see daily abuse in professional environments, so they must stand up to everything from high-speed rotations to accidental drops.
Material Quality Is Crucial
Why does material selection matter? Here’s the scoop: Lower-grade metals might work initially, but repeated stress will cause micro-fractures in the socket walls. Even well-made standard sockets, typically made from chrome vanadium, may not have the heat treatment or thickness needed for impact-level performance. The extra torque means more mechanical energy is transferred, and that energy has to go somewhere. If the steel can’t absorb it, the socket cracks or shatters. That’s a pricey risk if you rely on your tools daily.
Differences in Shape and Coating
Impact sockets usually have a matte or black oxide finish, unlike standard chrome-plated sockets. That finish isn’t just for looks. It helps reduce corrosion and tends to show less surface damage after repeated usage. Thicker walls also help disperse the powerful vibrations, offering a margin of safety. Some cheap imitation impact sockets may look the part due to a black finish, but actual composition and manufacturing processes define whether they’ll last more than a few heavy rounds.
Common Misconceptions
Some folks think you can use any old socket with an impact driver. That misconception often leads to broken sockets flying dangerously around a workspace. Others believe that a higher price tag always means better material. Not necessarily. You might be wondering: Should you pick brand A or brand B? It depends on what steel alloys and heat treatments they employ. Skilled manufacturers design their impact sockets to withstand repeated compressive forces by focusing on both the metal’s chemical makeup and the final tempering process.
Long-Term Safety and Performance
If you’re a mechanic or a DIY fanatic who pushes tools to their limit, you understand the value of peace of mind. Quality impact sockets—crafted from robust alloys—are less likely to fail mid-task. This reliability can save your knuckles from bruises or your eyes from flying shards. Proper maintenance goes a long way, too. Wipe them clean, check for cracks, and store them safely. High-grade materials offer extended lifespans, so you don’t have to constantly replace sockets or second-guess their condition.
Why This Matters
Here’s the deal: If you’re interested in how materials shape the performance of an impact socket, it’s because you care about efficiency, safety, and cost-effectiveness. Skilled manufacturers leave nothing to chance; they perform rigorous testing to ensure their sockets meet industrial requirements. It might seem like overkill if you’re new to the topic, but imagine halting a production line because an inferior socket exploded. The downtime, repairs, and potential injury risks outweigh any savings from cut-rate materials. Knowledge here is power, equipping you to identify what sets a proper impact socket apart from a cheap imitation. That insight alone protects your investments and your peace of mind.
The Role of Strength and Toughness
Key Properties
Torque. Shock. Shear force. These terms come to life when you’re spinning lug nuts or working on industrial machinery. Strength and toughness aren’t just marketing buzzwords. They refer to measurable attributes that help materials survive repeated battering. You might be wondering why balancing hardness, ductility, and tensile strength is so vital. Without that balance, a socket can chip or crack. Hardness helps an impact socket resist surface wear, while toughness ensures it won’t shatter under extreme conditions. Impact sockets need both.
Too Hard vs. Too Soft
What happens if steel is too hard? It becomes brittle and can fail catastrophically upon impact. Think of how some types of glass can be incredibly hard but shatter when struck. Conversely, steel that is too soft will deform under high torque, leading to rounding or stripping of fasteners. Here’s the scoop: Manufacturers use specialized heat treatments to find that sweet spot between hardness and flexibility. The result is an alloy that can handle repeated blows without excessive wear.
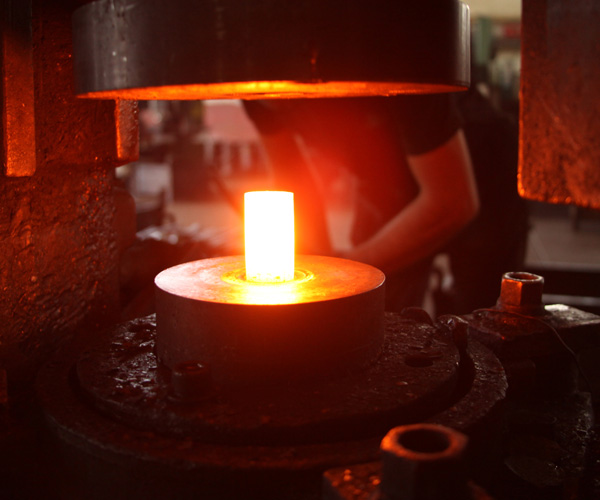
Real-World Implications
Look at a busy automotive garage. Mechanics might remove and replace hundreds of lug nuts in a single week. An improperly tempered or poorly chosen steel can develop hairline fractures from the repeated jarring. That’s not just an annoyance; it can be hazardous. Picture a socket fracturing mid-operation. Metal shards could pierce skin, or the broken tool could slip and round off the fastener. Either scenario can cost time and money, or lead to an injury. Reliable strength and toughness alleviate these concerns.
The Science of Impact Absorption
When an impact wrench delivers a jolt, the socket’s walls compress slightly, then rebound to their original shape. Quality steels exhibit elasticity that allows them to flex in response to sudden force. Now listen up: That microscopic movement dissipates energy. If a steel lacks this elasticity, that force has nowhere to go, and cracks begin to form. Over time, repeated stress can cause fatigue failure. Manufacturers test these properties extensively using Rockwell or Vickers hardness tests, along with standardized torque testing to confirm consistent performance.
High-Torque Demands
Modern automotive applications and industrial settings often involve advanced torque values. Performance engines, heavy machinery, and specialized hardware demand higher clamp loads. Impact sockets must keep pace with these evolving requirements. That’s why you see many big brands boasting about their proprietary alloys. They adjust chemical compositions, adding elements like chromium, vanadium, or molybdenum for improved performance. This helps guarantee that when you’re torquing beyond average specs, your socket remains intact.
Protective Coatings
Strength and toughness apply not just internally but on the surface. A poorly coated surface allows rust to form, which can weaken the metal over time. Chipped finishes open the door to corrosion. While the base steel is the star of the show, coatings help preserve that star by preventing moisture intrusion. This synergy of strong internal alloy plus stable external finish ensures consistent performance across different environments.
Finding the Right Balance
Here’s the deal: Some people chase maximum hardness, thinking that hardness alone makes a superior tool. Others focus solely on ductility, hoping that a super-tough metal means it never breaks. The real key is equilibrium. Impact sockets require enough hardness to resist compressive forces but enough ductility to manage shock. Heat treatment specialists spend years mastering these parameters. If you pick a reputable manufacturer, odds are they’ve already refined this balance for their product line.
Why It Matters to You
If you’re reading about material strength and toughness, it’s probably because you want tools that last. Whether you’re a seasoned mechanic or a weekend tinkerer, investing in well-made impact sockets translates to fewer replacements and safer work. You might be wondering if you can just choose any brand on the shelf. Risking your time and safety on untested alloys isn’t worth it. When a manufacturer publicly shares details about alloy composition and hardness testing, that transparency should give you confidence in the product. Understanding strength and toughness helps you interpret those specs effectively.
Common Metals in Impact Socket Manufacturing
Steel Alloys Overview
Steel is everywhere in the tool world, but not all steels are identical. Regular carbon steel might suffice for a basic wrench, yet it’s typically inadequate for high-impact tasks. Here’s the scoop: Impact socket manufacturers gravitate toward alloy steels that incorporate elements like chromium, vanadium, and molybdenum. These elements fortify the base metal’s structural integrity, making the steel more resistant to torque-induced deformation.
Traditional vs. Modern Alloys
Older generations might remember plain carbon steel tools. Those tools were serviceable, but they often rusted quickly or lost shape under intense workloads. As industries evolved, so did steelmaking techniques. Now, modern smelting and alloying processes produce steels with much narrower tolerances for impurities. That means a more predictable performance in extreme conditions. If you’re using an older set of sockets, you might notice they look more pitted or corroded compared to newer sets.
Chromium’s Role
Chromium is a critical component in many tool steels. It boosts corrosion resistance and enhances hardness. That’s why you see “chrome-molybdenum” or “chrome-vanadium” listed on packaging. Chromium also interacts with carbon in the steel, forming carbides that push hardness to higher levels. You might be wondering whether the chrome you see in bright, shiny tools is the same as chrome plating. It’s not. Chrome in the alloy is integrated at a molecular level, unlike a surface coating that can flake off.
Molybdenum’s Influence
Molybdenum helps steel sustain its strength under high temperatures. This is beneficial for high-impact tasks because friction can generate heat, and repeated hammering can elevate local temperatures. Molybdenum also improves pitting resistance, making the steel more durable over time. Impact sockets labeled “Cr-Mo” typically boast better shock absorption than basic steels, which is why they’re standard in professional garages.
Vanadium’s Contribution
Vanadium is another secret weapon. It refines the grain structure of steel, contributing to enhanced toughness. Here’s the deal: A finer grain structure translates to fewer stress points within the metal. That means improved resilience under sudden loads. Chrome-vanadium steels (Cr-V) are popular for a broad spectrum of tools, from spanners to mid-tier impact sockets. They balance cost and performance effectively, though they may not handle extreme industrial demands as well as high-end Cr-Mo.
Hybrid Alloy Blends
Some manufacturers mix multiple alloying elements to achieve specific performance characteristics. That might include partial amounts of tungsten or nickel for even more specialized properties. Custom blends can yield a sweet spot of hardness, toughness, and corrosion resistance. The biggest brands often have proprietary recipes they test in-lab to achieve consistent quality.
Cost Considerations
Crafting these specialized steels isn’t cheap. The process of adding alloy elements, refining the mixture, and heat treating each batch demands a sophisticated production line. Smaller brands might opt for lower-grade steels to keep costs down, but that comes at the expense of performance. Understanding the trade-off helps you pick the best tool for your budget and your needs. Now listen up: If you rely on your impact sockets daily, investing in more robust alloys could save money in the long run.
Identifying Alloy Steel by Markings
Many impact sockets have stamped markings or engravings specifying their composition. You might see “Cr-V” or “Cr-Mo” near the size marking. Reputable manufacturers want you to know what you’re getting. If a socket is suspiciously cheap and lacks any marking, it could be subpar material. Checking for brand authenticity and looking up manufacturer data sheets can also confirm the alloy used. That peace of mind makes a difference when your livelihood depends on reliable, safe tools.
Chrome Molybdenum Steel (Cr-Mo)
Composition Details
Chrome molybdenum steel blends chromium, molybdenum, and carbon with iron. This alloy typically includes small percentages of manganese or silicon that fine-tune mechanical properties. The interplay between these elements results in a metal known for high tensile strength and superior shock absorption. You might be wondering if this formula is universal. Different manufacturers might adjust exact ratios, but the underlying principle remains: deliver durability under punishing conditions.
Strength and Impact Resistance
Cr-Mo steels are stars in industrial settings. They handle repeated impact loading with ease, which is why so many top-tier impact sockets advertise this composition. When you slam a high-torque wrench on a stubborn bolt, the Cr-Mo steel’s molecular structure absorbs that energy. It returns to its original form without fracturing, even after repeated abuse. That resilience sets it apart from cheaper steel types that can’t handle the same stress cycles.
Common Applications
Automotive mechanics swear by Cr-Mo for tasks like removing rusted lug nuts or dealing with heavy-duty suspension components. Aeronautics technicians also appreciate the reliability it offers, especially when servicing aircraft engines or landing gear systems. If you’re operating in a workshop that constantly tests the limits of your tools, Cr-Mo sockets become indispensable. The consistency they offer across countless cycles fosters confidence in the work environment.
Why Professionals Prefer Cr-Mo
Here’s the deal: Professionals often pick Cr-Mo sockets for their track record of resisting breakage. Imagine a scenario where a manufacturing plant runs 24-hour shifts, and technicians rotate tasks frequently. Tools are passed from hand to hand, enduring relentless torque. Cr-Mo’s robust nature sustains its structure without frequent replacements. Time lost to a broken socket can translate to production delays, not to mention potential safety hazards. People willing to invest in longevity will see the payoff quickly.
Heat Treatment Synergy
One can’t overstate how pivotal heat treatment is to final product quality. Cr-Mo steels respond well to processes like quenching and tempering. After forging, controlled heating and rapid cooling fix the alloy’s microstructure in a tougher, harder state. Another tempering step refines that hardness so it doesn’t become too brittle. Skilled heat treatment ensures your Cr-Mo impact socket has minimal internal defects and a consistent hardness profile from the surface inward.
Maintenance Tips
Cr-Mo sockets, despite their inherent rust resistance, still need basic upkeep. Wiping them down after use removes debris and grime that could lead to surface scratches or moisture buildup. Occasional lubrication helps preserve their protective finishes. You might be wondering if these materials rust easily. While they resist corrosion better than plain carbon steels, neglect can still undermine performance. Store them in a dry environment or use a rust-preventive spray to keep them pristine.
Considering Cost
High-grade Cr-Mo sockets can be pricier than their Cr-V counterparts. That difference arises from both raw material costs and specialized forging processes. But professional shops often see this as a worthwhile investment. Going cheap might mean more frequent replacements and potentially catastrophic failures that cost far more in downtime and repairs. Remember, a single shattered socket can ruin a critical job.
Final Thoughts on Cr-Mo
Now listen up: Chrome molybdenum steel stands among the top choices for impact sockets precisely because it merges strength, ductility, and reliability. Many leading brands invest heavily in R\&D to fine-tune their Cr-Mo formulations. That’s why you see them recommended in high-pressure jobs across automotive, industrial, and heavy machinery sectors. If you want peace of mind that your socket will handle intense torque without breaking, Cr-Mo is a strong contender.
Chrome Vanadium Steel (Cr-V)
Composition and Structure
Chrome vanadium steel, labeled Cr-V, is another widely recognized alloy in the tool world. It blends chromium, vanadium, and carbon alongside iron, much like Cr-Mo, but with different ratios and occasional additional elements. This yields an alloy known for a decent balance between hardness and ductility. You might be wondering if it’s as tough as Cr-Mo. The answer often depends on the specific application and the manufacturer’s heat treatment process.
Performance Characteristics
Cr-V steels typically provide robust tensile strength, making them well-suited for hand tools like wrenches and standard sockets. In the realm of impact sockets, some brands do utilize Cr-V due to its cost-efficiency and respectable properties under moderate torque loads. However, for extended high-impact situations, Cr-Mo is frequently preferred. That said, Cr-V can handle its fair share of punishment, especially for DIY or mid-level professional usage.
Ideal Use Cases
Here’s the deal: Not everyone needs industrial-grade durability. A part-time mechanic or an avid car enthusiast might find that Cr-V sockets check enough boxes to justify their price. If you’re not repeatedly maxing out torque values or slamming the socket with a pneumatic impact gun all day, Cr-V could be perfectly fine. In fact, many popular tool sets sold at consumer hardware stores feature Cr-V. They aim to satisfy hobbyists or professionals with moderate usage demands.
Comparing Cr-V with Cr-Mo
A straightforward difference lies in how these alloys handle repeated shock. Cr-Mo typically absorbs sudden jolts better, which translates to fewer micro-fractures over time. Cr-V might exhibit signs of wear or distortion a bit earlier if pushed to extremes. The cost advantage, however, can sway budget-conscious buyers toward Cr-V. You might be wondering if that means Cr-V is inherently inferior. Not necessarily. Properly treated Cr-V can do wonders, but longevity under relentless torque often favors Cr-Mo.
Heat Treatment Nuances
Chrome vanadium steel responds to heat treatment in a manner that increases both hardness and corrosion resistance. Manufacturers will quench and temper Cr-V similarly to how they treat Cr-Mo, though the specific times and temperatures vary. This process influences how well the finished socket resists impact. If you see a reputable brand using Cr-V for impact sockets, rest assured they’re applying advanced heat treatment protocols. That helps mitigate potential brittleness.
Visual Cues and Coatings
Many Cr-V tools flaunt a polished chrome finish to combat corrosion. For impact sockets, manufacturers might opt for black phosphate coatings or black oxide to maintain a non-reflective surface. This black finish can be confusing if you assume black automatically equals better performance. The underlying alloy plus the heat treatment matter more than the finish color. The best way to judge is by brand reputation, metal composition, and real-world feedback.
Durability vs. Price
Cost often becomes a deciding factor. Cr-V sets usually hit a lower price point than Cr-Mo equivalents, making them appealing for less intensive tasks. If you’re operating in a modest workshop or tackling weekend car repairs, spending a premium on Cr-Mo might be overkill. However, professionals who rely on their tools daily might prefer to pay a bit extra for the extended lifespan and reliability. Now listen up: Evaluate how hard you plan to push your tools before deciding which alloy meets your needs.
When to Upgrade
Some people begin with Cr-V sets, then upgrade to Cr-Mo once they realize their usage demands more robust gear. Others remain satisfied with Cr-V for years. Understanding your typical torque loads and the frequency of impact tool usage helps you gauge which material best suits you. If you find yourself pushing your sockets to their limit or seeing early damage, it may be time to switch to Cr-Mo. This step up can save money in the long haul by reducing breakage and associated downtime.
S2 Steel and Other Specialty Alloys
What Is S2 Steel?
S2 steel is known for its high hardness, commonly used in applications like screwdriver bits and specialty drivers. It incorporates silicon, chromium, and molybdenum in specific quantities, giving it robust tensile strength. Here’s the deal: S2’s hardness rating can exceed that of some Cr-V steels, so it excels in tasks where consistent torque transmission is necessary. Yet, for impact sockets, S2 is less prevalent due to cost factors and potential brittleness if not tempered meticulously.
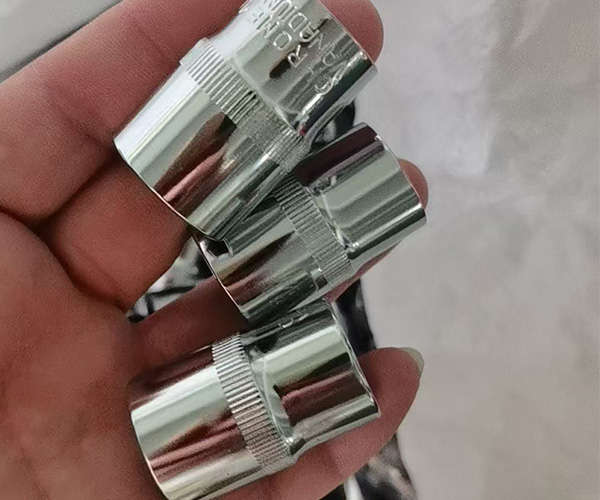
Additional Specialty Alloys
Beyond S2, you’ll encounter niche alloys that incorporate tungsten, nickel, or cobalt for specialized scenarios. Aerospace or heavy industries sometimes call for exotic metals that remain stable under extreme temperatures or corrosive conditions. These alloys can be significantly more expensive, so they tend to be reserved for mission-critical applications. If you’re just swapping out brake calipers in your garage, these might be overkill.
Why Some Manufacturers Use Them
Performance is the name of the game. Specialty alloys might yield exceptional hardness or corrosion resistance, so if a manufacturer markets sockets for specialized industrial or military uses, these exotic recipes become relevant. They also serve as a brand differentiator. You might be wondering if that marketing hype is justified. Often, yes, because advanced alloys can handle punishment that would crack or deform lesser metals.
Limitations and Trade-Offs
High hardness sometimes equals reduced ductility. A tool that is ultra-hard can crack if subjected to sudden shocks outside its operating parameters. Specialty steels demand precise heat treatment to mitigate brittleness. Additionally, the cost may double or triple compared to Cr-Mo or Cr-V, so the buyer base narrows significantly. Manufacturers must decide whether the benefits outweigh these higher production expenses.
Application Scenarios
You see S2 bits in high-end sets for repetitive tasks such as screw driving in industrial assembly lines. They deliver consistent torque transfer and endure thousands of cycles. In the realm of impact sockets, a small segment of advanced or custom items might feature S2 or other super-alloys. These could be found in aerospace maintenance kits or specialized heavy-machinery repair shops. Now listen up: If you’re a standard user, you might never encounter these special compositions.
Brand-Specific Alloys
Some big tool brands name their proprietary blends to stand out. They might list them as “Performance Steel” or “Ultra-Duty Alloy.” The crucial factor is verifying test data and real-world reviews. If a manufacturer invests in R\&D, they’ll likely share details about how their alloy stands up to repeated torque. That’s how you distinguish genuine innovation from marketing fluff.
Maintenance Considerations
S2 steel and other specialty alloys can be more sensitive to corrosion if improperly stored. They might also demand more rigorous heat treatment. For the user, routine cleaning and occasional lubrication remain essential. Even exotic metal can degrade if coated in rust or grime. A consistent cleaning routine ensures that you get the full benefit of the specialized alloy over its lifespan.
How to Decide
You might be wondering if you should buy into the hype surrounding specialized metals. If you’re running a standard auto shop or tackling DIY projects, Cr-Mo or Cr-V is typically sufficient. Specialty alloys come with higher price tags, so unless you have unique environmental or performance demands, they might be unnecessary. That said, if your work environment is extremely harsh—think sub-zero temperatures or maritime conditions—these advanced steels could justify the extra cost.
Heat Treatment Basics
Why Heat Treatment Matters
Heat treatment is the process of heating and cooling metals to alter their internal structures, and this influences hardness, strength, and ductility. Here’s the deal: For impact sockets, a proper heat treatment can be the difference between consistent, reliable performance and catastrophic failure. Even the best alloy becomes lackluster if not heat-treated correctly, so manufacturers invest heavily in specialized furnaces, quenching setups, and tempering protocols.
Hardening vs. Tempering
Hardening typically involves heating the steel to a specific temperature—often between 800°C and 900°C—then rapidly cooling it in oil or water. This step locks the microstructure in a harder state. But that hardness can lead to brittleness, so a subsequent tempering cycle re-heats the metal at a lower temperature. Tempering relieves internal stresses and balances hardness with toughness. You might be wondering if more hardening is always better. Absolutely not, as too much hardness can cause fracturing under high torque.
Quenching Variations
Manufacturers select quenching mediums (oil, water, polymer solutions) based on the alloy composition. Cr-Mo steels, for instance, may require an oil quench to prevent cracks that might arise from the more severe cooling rate of water. Quenching speed influences final grain structure and internal stresses. Some advanced processes utilize vacuum furnaces with inert gas quenching, giving precise control over cooling rates.
Annealing and Normalizing
If the steel is pre-hardened or contains certain impurities, an annealing or normalizing phase can refine its grain structure before final hardening. This step helps ensure a more uniform microstructure, reducing potential weak spots. It also helps manufacturers keep each batch consistent. Now listen up: Regular internal inspections or sample testing confirm that these steps were applied correctly across production runs.
Tests for Heat-Treatment Quality
The Rockwell or Vickers hardness test reveals whether the steel meets target hardness parameters. For impact sockets, too high a hardness reading might signal brittleness. Too low, and the socket might be too soft. Torque tests measure if the socket can handle specified load cycles without damage. Operators may also conduct micrographic exams to see if the grain structure is uniform.
Heat Treatment Errors
If the steel is overheated, underheated, or cooled too rapidly, the metal can develop micro-cracks or uneven hardness layers. A common issue is the presence of a brittle core with a softer exterior, or vice versa. Users might see cracks along edges or experiences with quick deformation. That’s why consistent quality assurance is essential in a mass-production environment.
Manufacturer Transparency
Well-established brands often state that they follow specific heat-treatment protocols or meet industry standards like ISO or ASME. They know that buyers want reliable data. You might be wondering if you can trust every brand that claims “heat-treated steel.” Some unscrupulous manufacturers might skip steps or do subpar quenching to cut costs. Looking for recognized certifications, brand reputation, and user reviews is key.
Summing Up
Heat treatment is central to an impact socket’s performance. Balancing hardness and toughness ensures that sockets don’t fail prematurely. When combined with carefully chosen alloys, proper heat treatment helps guarantee that your sockets survive heavy torque day in and day out. That’s the silent advantage behind well-made impact tools. This process is invisible once the socket is finished, yet it shapes nearly everything about how that tool behaves under stress.
Surface Coatings and Finishes
Types of Finishes
Impact sockets typically feature darker finishes like black oxide or phosphate. You might be wondering why they’re not all chrome-plated and shiny. Chrome plating can chip under impact, exposing the underlying steel to corrosion. Black oxide, phosphate, or even powder coatings do a better job adhering to an impact tool that experiences continual hammering. These finishes also reduce glare in brightly lit workshops.
Purpose of Coatings
Coatings protect against moisture and external contaminants. They also reduce friction, aiding in easier fastening or unfastening under high torque. In many production lines, a slip or jammed socket can slow down workflow. A consistent finish helps minimize those annoyances. Here’s the deal: Some manufacturers add specific lubricative coatings to reduce friction even further, an advantage in specialized high-speed assembly tasks.
Pros and Cons
Black oxide is inexpensive and commonly used, but it may wear off gradually, especially at contact points. Phosphate coatings often offer better rust resistance, though they can add slightly more texture. Powder coating, on the other hand, forms a thicker layer that can be prone to chipping if the tool is severely abused. Chrome plating looks appealing yet can flake under repeated impacts, leading to rust infiltration underneath the plating.
Environmental Considerations
Manufacturers increasingly focus on eco-friendly processes. Chemical baths used in older coating methods could produce hazardous waste. Some forward-thinking companies incorporate low-VOC finishes or water-based processes to minimize environmental impact. If you see a brand touting green credentials, they might be using these newer coatings.
Maintenance and Wear
Even the toughest finish eventually shows signs of use. Swapping sockets frequently at high RPMs or bashing them against stubborn fasteners scuffs the coating. The key is ensuring the underlying steel remains protected from moisture. Now listen up: Wiping your sockets dry and storing them in a place free from extreme humidity prolongs coating life. A worn coating isn’t necessarily a deal-breaker, but it does open the door to corrosion if neglected.
Aesthetic vs. Functional
Some users prefer the sleekness of polished finishes, but polished surfaces can show scratches more readily. For impact sockets, function typically trumps style. Matte black or gunmetal finishes help conceal wear and often provide better grip. That said, a high-end brand might still refine the finish for brand recognition.
Selecting the Right Finish
Different finishes suit different usage patterns. If your environment is extremely wet or corrosive, a more robust anti-rust finish may be essential. Occasional home users might be less concerned, focusing instead on cost. You might be wondering how to confirm a finish’s durability. Many manufacturers publish salt-spray test results, indicating how long a finish withstands corrosion. Combine that info with user reviews for a bigger picture.
Ongoing Evolution
Toolmakers continually refine finishes in response to customer demands for longevity. Hybrid or multi-layer coatings are emerging, combining phosphate or oxide layers with specialized topcoats. These can extend the life of the socket further. Keep an eye on industry news if you’re looking to upgrade or if you run a shop that punishes tools daily.
Testing and Quality Control
Importance of Testing
A top-tier manufacturer won’t release an impact socket until it clears rigorous testing protocols. Here’s the deal: This goes beyond marketing claims. Repetitive torque testing, hardness checks, and real-world simulations validate that each batch meets set specifications. That thoroughness matters because a single weak socket in a production run can compromise user safety.
Hardness Tests (Rockwell, Vickers)
Rockwell tests measure indentation depth after a standardized force is applied. Vickers tests gauge diagonal lengths made by a diamond indenter. Both yield numeric values correlating to hardness. For impact sockets, you don’t want a super-high number that suggests brittleness. Instead, you look for a range that indicates balanced toughness.
Torque and Impact Tests
Manufacturers will often mount sockets on specialized rigs that mimic real-world usage with repeated hits from an impact tool. Over a set number of cycles, they check for cracks, deformations, or material fatigue. You might be wondering why these tests are critical. They confirm that the socket can handle specified torque values repeatedly, giving end users confidence.
Visual and Dimensional Inspections
Beyond mechanical tests, inspectors measure wall thickness, interior geometry, and drive size tolerances. Small misalignments can lead to poor fit, slip-offs, or rounding of fasteners. The best companies calibrate their forging and machining processes meticulously, with in-process checks to catch defects early.
Industry Standards
Standards from organizations like ISO, ANSI, and ASME set baseline requirements for socket strength, hardness, and dimensional accuracy. Products that meet or exceed these standards often boast certifications on packaging or in marketing materials. While not a guarantee of absolute perfection, these seals indicate that the brand follows recognized benchmarks. Now listen up: Subpar or unbranded sockets might skip these certifications entirely.
Quality Assurance vs. Quality Control
Quality assurance (QA) involves system-wide processes designed to prevent defects, like thorough documentation of heat-treat cycles. Quality control (QC) is the step where finished products are inspected to verify they meet specs. Together, QA and QC form a holistic approach that ensures consistent performance across thousands of sockets.
User Responsibility
No matter how well a socket is made, misuse or abuse can lead to premature failure. Over-torquing beyond manufacturer specs or using a damaged socket invites accidents. Here’s the scoop: Inspect your tools regularly. If you see cracks or notice unusual rounding, retire that piece. Even the best brand can’t save you from ignoring obvious wear.
Long-Term Confidence
When a brand invests in thorough testing, that brand invests in your peace of mind. Seeing documentation of torque specs, reading about repeated impact tests—these details make a tangible difference. They confirm the tool is built to endure your daily demands. It’s one reason professionals gravitate toward established names with proven track records.
Balancing Cost vs. Quality
Price Differences Explained
Impact sockets vary widely in cost, from budget-friendly sets sold in big-box stores to premium lines marketed to professional mechanics. Here’s the deal: You typically get what you pay for in terms of alloy quality, heat treatment precision, and brand reputation. Cheaper sets might cut corners on steel composition or skip rigorous testing, resulting in a higher chance of failure down the road.
Long-Term Savings
A premium set often outlasts multiple low-cost sets. If you’re a professional relying on daily usage, those replacements add up. If a cheaper socket shatters and damages a client’s equipment or injures a co-worker, the financial and legal ramifications can far exceed the initial savings. You might be wondering how much cost difference we’re talking about. Premium sets can be double or triple the price, yet they can last years longer under demanding conditions.
When to Invest
Not everyone needs high-end gear. Occasional DIY tasks might not justify the expense of Cr-Mo or specialized steel. A good-quality Cr-V set can suffice for changing tires or tackling basic household projects. However, if you’re an automotive technician or a contractor facing high torque daily, investing in robust Cr-Mo makes sense. Evaluate your usage frequency, torque levels, and the potential cost of tool downtime.
Middle-Ground Options
Some brands offer mid-range lines aimed at prosumers. These lines feature decent alloy compositions and pass moderate testing but may not hold up to the harshest industrial abuse. They strike a balance between cost and performance, suiting serious hobbyists or small garages. Now listen up: Research brand reviews, user feedback, and warranty policies to see if you can find a sweet spot.
Warranties and Guarantees
Reputable tool makers sometimes provide lifetime warranties on their impact sockets. If a socket cracks under normal use, they’ll replace it free of charge. This signals a manufacturer’s confidence in their processes. Budget brands might offer limited warranties or none at all. That difference alone can be a deciding factor if you value long-term assurance.
Hidden Costs of Cheap Tools
A fractured socket can round off a fastener, meaning you spend extra time drilling or extracting the stripped bolt. That translates to lost labor hours or missed deadlines. If you’re a professional, that hits your bottom line. Even for hobbyists, a broken tool mid-project can be infuriating. Here’s the scoop: These intangible costs sometimes outweigh the upfront savings you get from budget tools.
Professional vs. DIY Perspectives
Professionals typically demand robust, reliable tools because their livelihoods depend on them. DIY enthusiasts might lean toward more affordable options unless they anticipate heavy usage. If you fall between those categories, it’s often smarter to invest a bit more rather than deal with repeated failures.
Making an Informed Choice
You might be wondering how to decide. Start by listing your usage scenarios and frequency. Then consider the potential risks of failure. Check manufacturer specs and read genuine user reviews. Factor in warranties, brand reputation, and personal budget. This approach ensures you pick a set of impact sockets that matches your demands without breaking the bank or compromising on safety.
Innovations in Material Technology
New Alloy Developments
Metallurgy doesn’t stand still. Researchers constantly experiment with novel alloy compositions, introducing elements like boron or tungsten in micro-quantities to fine-tune properties. Here’s the deal: These advanced steels aim to boost toughness or reduce weight, a game-changer in certain industries. Such research often trickles down from aerospace or defense sectors into consumer tools over time.
Manufacturing Advances
Automated forging and advanced CNC processes produce sockets with tighter tolerances and more uniform walls. Innovative forging techniques can reduce internal stress, leading to fewer defects. Laser or robotic inspection systems quickly identify micro-cracks or dimensional inconsistencies. The outcome is more reliable, consistent products that satisfy demanding industrial clients.
3D Metal Printing
Though still in its infancy for mass production, 3D metal printing or additive manufacturing holds potential for producing specialized sockets. Complex internal geometries might be possible, distributing stress more efficiently. You might see prototyping or small-batch runs in the near future. You might be wondering if this is cost-effective. At the moment, it’s often too expensive for mainstream lines, but it’s an exciting glimpse into the future.
Nano-Structured Alloys
Nano-structured or grain-refined alloys offer improved strength by manipulating grain boundaries at microscopic levels. This can result in metals that exhibit superior toughness while retaining ductility. Large-scale adoption remains limited due to production complexities, but these breakthroughs indicate the path forward.
Eco-Friendly Options
Industry pressure to reduce hazardous byproducts has spurred research into greener heat treatments and coatings. Solvent-free or water-based coatings reduce environmental impact. Some forging plants run on renewable energy sources or recycle quenching mediums. Brands that market sustainable production processes often highlight these efforts. Now listen up: This can be a selling point if you care about minimizing your carbon footprint.
Customer-Driven Innovation
Buyers request new features like color-coded sizes or integrated magnets. While these don’t directly relate to material composition, they illustrate how the market drives changes. If enough users ask for a property—like even better corrosion resistance—brands respond by tweaking alloy or finish formulations.
Proprietary Blends and R\&D
Major players in the tool industry invest heavily in R\&D, resulting in trademarked blends or patented forging techniques. They conduct stress tests on new steels to see if they can surpass existing benchmarks. If successful, they release specialized lines labeled “Pro Series” or “Ultra Duty,” sometimes with the price tag to match. You might be wondering if that hype is warranted. It often is for professionals who push their gear to extremes.
The Future Outlook
Expect more synergy between manufacturing automation, material science, and user feedback. Each iteration yields sockets that are lighter, stronger, or longer-lasting. As global competition intensifies, top manufacturers differentiate themselves through continuous improvement. For the end user, this means an ever-expanding range of options. That’s a plus, as you can find precisely what you need, whether you’re a weekend tinkerer or a 24/7 industrial powerhouse.
Choosing the Right Material for Your Needs
Critical Questions
It helps to ask: How often will I use the socket? What torque levels do I typically encounter? Do I work in a professional setting or a home garage? Here’s the scoop: Different materials excel under different circumstances, so clarity on your usage is key. If you rarely push above moderate torque, you might not need to pay extra for Cr-Mo.
Industry-Specific Scenarios
Automotive shops dealing with frequent tire rotations or axle maintenance benefit from robust Cr-Mo sets. Aviation technicians or engineers in a manufacturing plant might also demand top-tier tools. Meanwhile, a hobbyist who occasionally changes spark plugs can manage with a simpler Cr-V set. You might be wondering if it’s worth splurging if you do sporadic tasks. The answer depends on how critical the job is and your tolerance for tool failure.
Evaluating Brand Reputation
Reputable manufacturers have a long trail of reviews and test data backing their claims. Many pros gravitate toward names like Snap-on, MAC Tools, or Proto because these brands demonstrate consistent material quality. If you opt for a less established brand, look for certifications or detailed product specs that confirm robust materials and testing.
Specialized Requirements
In certain fields, you might handle non-standard fasteners or extremely tight spaces. Some sockets come in specialized shapes or with added features like external ribs. Material selection extends to these variants, as you still need an alloy that can handle the same stress. If you notice your tasks involve repeated usage in harsh environments—saltwater exposure, for instance—stainless or heavily coated sockets might be an option, though they come at a premium.
Local vs. Global Sourcing
Some consumers care whether their tools are made domestically or overseas. This can matter because different facilities maintain different QC standards. However, many global manufacturers hold themselves to top-tier procedures. It’s more about verifying the plant’s track record rather than its geography alone. Now listen up: If a brand is transparent about sourcing and QC, that’s a good sign.
Checking Product Markings
Does the socket state “Cr-Mo” or “Cr-V”? Is there a brand name? Does it mention ISO or ANSI compliance? Genuine products typically provide these details. Counterfeit or no-name sockets might omit crucial info. Taking a moment to inspect markings helps you avoid subpar or unsafe products.
Trying Before Buying
If you have an opportunity to test a socket—perhaps at a friend’s garage or a professional trade show—do it. Hearing real-world feedback often trumps marketing copy. Tools that feel solid and fit snugly on fasteners typically reflect good craftsmanship and well-chosen materials. You might be wondering if that’s enough to decide. Coupled with known brand reliability, probably yes.
Final Decision
Ultimately, choosing the right material means balancing your usage, budget, and expectations. Investing in high-grade Cr-Mo if you only tighten a few bolts a month may be overkill. On the other hand, running a busy repair shop with a bargain-basement set is a recipe for frustrations. Knowing the difference between Cr-Mo, Cr-V, S2, or specialty alloys positions you to select a product that won’t let you down when it counts most.
Care and Maintenance Tips
Regular Cleaning
Dust, grime, and metal flakes can accumulate in the recesses of an impact socket. Over time, these particles may lead to corrosion or even jam the socket onto a fastener. Here’s the deal: A few moments spent wiping the socket after each use prevents bigger headaches later. A rag or brush can remove debris quickly, and a bit of mild solvent dissolves stubborn grease.
Storage Practices
When sockets are tossed haphazardly into a damp toolbox, rust becomes a real threat. Organizing them in a socket rail or dedicated holder helps you keep track and avoid collisions that cause chipping. Some professionals store them in foam inserts or custom cases. Keeping them off concrete floors in humid garages also pays dividends. You might be wondering if applying a light coat of oil is necessary. It can’t hurt, especially if you live in a humid area or store them for extended periods.
Recognizing Wear
Look for cracks, chips, or signs of distortion around the drive end. If a socket seems looser than usual on a fastener, it might be wearing out or rounding internally. Now listen up: Continuing to use a compromised socket can further damage fasteners and risk unexpected failure under torque. Replacing worn-out sockets promptly is a safer, more cost-effective move than waiting for a catastrophic break.
Addressing Rust
Surface rust can often be removed with a wire brush or rust-removing solution, followed by a protective oil or coating. If the rust is extensive, you may have compromised the metal’s integrity. At that point, weigh the risk of continuing usage. If you’re uncertain, safer to retire that socket.
Respect Torque Limits
Impact sockets are tough, but every tool has a limit. Using a small socket on an industrial-grade impact wrench set to maximum torque is an invitation for disaster. That’s particularly relevant when dealing with stubborn fasteners that require serious force. Here’s the scoop: Step up the socket size or double-check your tool’s specs. Pushing beyond rated limits reduces the lifespan of even the best socket.
Using the Right Accessory
Don’t insert a regular chrome extension bar or adaptor in a high-torque environment. Accessory mismatch can shift stress to weak points, leading to breakage. If you need an extension, pick an impact-rated version. The entire chain of tools must share the same toughness level.
Ongoing Inspections
A quick glance during tool cleanup can reveal early warning signs. That small crack near the corner might expand after another heavy use. Addressing issues sooner keeps your set complete and ensures you’re not left scrambling mid-job. You might be wondering if brand warranties cover normal wear. Some do, some don’t. Read the fine print and keep your receipts if you rely on warranties.
Maximizing Lifespan
With consistent cleaning, mindful storage, and using the correct socket for each job, you can prolong the service life of your impact sockets significantly. Maintenance doesn’t need to be complicated, just routine. Such diligence pays off in safer operations, reduced downtime, and better overall performance.
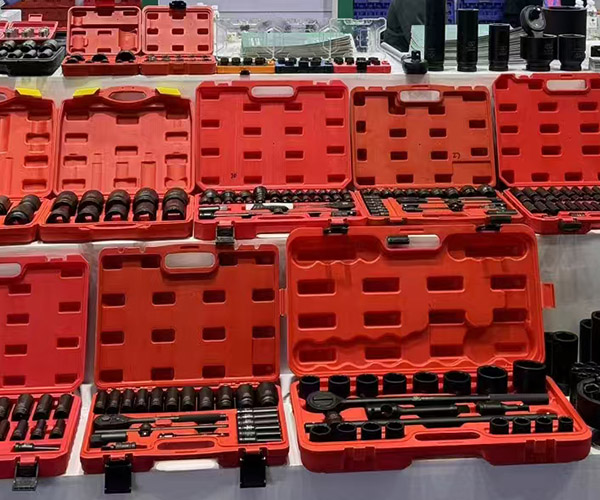
Conclusion
To wrap things up, remember that material selection lies at the heart of impact socket performance. Without a sturdy alloy and proper heat treatment, no fancy coating or brand name can save a socket from failing under serious torque. Here’s the deal: Chrome molybdenum (Cr-Mo) and chrome vanadium (Cr-V) stand out as two major players, each with unique properties suited to different user needs. Professionals who hammer away all day generally favor Cr-Mo for its superior shock absorption, while occasional users might do fine with a well-made Cr-V set.
Quality control processes like hardness tests and torque simulations ensure that you’re getting a tool that meets industry standards. Investing in advanced materials or specialized alloys pays dividends for those who frequently push their tools to the limit. You might be wondering if you can skip the deeper research and just grab any black-finished socket. That approach risks disappointment or even dangerous breakage. Instead, keep an eye on brand reputation, manufacturing details, and real-world reviews.
By now, you know how material composition, heat treatment, coatings, and careful QC protocols combine to yield a top-notch impact socket. With routine maintenance and a bit of caution, your sockets can deliver reliable service for years. And that’s the bottom line: Tools that stand the test of time ultimately save you money and hassle. Stay informed, choose wisely, and your workshop or job site will reap the rewards of strong, resilient impact sockets.
FAQ
1. What’s the difference between chrome molybdenum and chrome vanadium for impact sockets?
Chrome molybdenum (Cr-Mo) is typically better at handling repeated shocks and higher torque loads, which makes it a top choice for heavy-duty, professional use. Chrome vanadium (Cr-V) can still be strong and cost-effective but isn’t always as shock-absorbent under extreme conditions. Professionals who rely on impact sockets daily usually pick Cr-Mo, while hobbyists or moderate users often find Cr-V sufficient.
2. Is heat treatment really necessary for socket durability?
Absolutely. Heat treatment helps create the ideal balance between hardness and toughness in the alloy. Without proper hardening and tempering, sockets can either become too brittle and crack, or too soft and deform over time. Quality manufacturers invest in rigorous heat treatment processes to ensure each impact socket can handle repeated high-torque scenarios.
3. Can surface coatings chip or peel off easily under heavy use?
They can if the coating isn’t applied correctly or if the material and coating aren’t well matched. Black oxide and phosphate finishes generally hold up better to heavy impact than chrome plating, which can crack or flake. Even durable coatings will wear over time, but high-quality finishes applied by reputable manufacturers usually last longer.
4. How often should I replace an impact socket?
Replacement depends on usage frequency and the torque levels applied. Check your sockets regularly for cracks, warping, or significant wear around the edges. If you spot any damage, it’s best to replace that socket immediately. Even hairline fractures can lead to sudden failure, so routine inspections are crucial.
5. Do I need different materials for automotive vs. industrial use?
In many cases, yes. Automotive tasks often involve high torque but at a consistent, controlled level, so either Cr-Mo or Cr-V might work, depending on the frequency of use. Industrial environments sometimes demand nonstop, heavy-duty applications, which typically makes Cr-Mo the safer bet because of its improved shock resistance.
6. Are there eco-friendly coating options on the market?
Yes. Many manufacturers are moving away from processes that produce harmful waste. Water-based or low-VOC coatings are becoming more common. While some finishes still use chemical baths, the trend is toward coatings that reduce environmental impact without compromising performance.
7. Which brand or manufacturer is most reliable for high-quality alloy blends?
Reputable brands like Snap-on, Proto, Mac Tools, and certain specialized lines from Gearwrench or Sunex have strong track records for consistent alloy quality. Look for certifications (ISO, ANSI, ASME) and seek out user reviews to see how their products perform under real-world conditions. Each brand may have a different proprietary blend, so it’s worth comparing their specs if you’re looking for something very specific.
Ready to invest in reliable, long-lasting tools? Don’t wait. Explore our top-rated impact socket selections or reach out for more info about the perfect alloy blend for your needs. Secure efficiency, safety, and performance by choosing quality gear today!