What Are Impact Sockets?
Impact sockets are essential tools in the toolkit of mechanics, DIY enthusiasts, and professionals who frequently deal with high-torque applications. Unlike standard sockets, impact sockets are specifically designed to withstand the intense forces generated by impact drivers and wrenches. Their primary purpose is to efficiently transfer the power from these tools to loosen or tighten fasteners, such as nuts and bolts, without compromising the integrity of the socket or the fastener itself.
The defining features of impact sockets include their robust construction, typically made from high-strength materials like chrome vanadium or alloy steel. These materials ensure that the sockets can endure the repetitive impacts and vibrations without cracking or deforming. Additionally, impact sockets often feature a thicker wall compared to standard sockets, providing extra durability and strength. The design also includes a polished interior surface, which minimizes friction and reduces the risk of rounding off fasteners during use.
Precision is another critical aspect of impact sockets. The internal geometry of the socket must match the fastener’s shape perfectly to ensure a secure fit. This precision helps in preventing slippage, which can lead to damaged fasteners or injury to the user. Moreover, the exterior of impact sockets is usually treated with specialized finishes and coatings, which play a significant role in enhancing their performance and longevity.
Impact sockets come in various sizes and drive types to accommodate different applications. Common drive sizes include 1/4-inch, 3/8-inch, and 1/2-inch, each suitable for specific tasks and tool compatibility. The versatility of impact sockets makes them indispensable in automotive repair, construction, and general maintenance work, where reliability and performance are paramount.

In summary, impact sockets are meticulously engineered tools designed to handle the demanding conditions of high-torque applications. Their superior construction, precision, and specialized finishes make them a reliable choice for professionals and hobbyists alike, ensuring efficient and safe fastening operations.
Importance of Finish and Coating in Impact Sockets
The finish and coating of impact sockets play a pivotal role in determining their overall performance and longevity. These surface treatments are not merely aesthetic; they serve functional purposes that enhance the tool’s durability, corrosion resistance, and operational efficiency. Understanding the significance of these finishes and coatings can help users make informed decisions when selecting impact sockets for their specific needs.
Firstly, the finish applied to an impact socket significantly impacts its durability. High-quality finishes provide a protective barrier against wear and tear caused by constant use. For instance, black oxide finishes are popular because they offer a degree of corrosion resistance while also reducing glare, which is beneficial in brightly lit work environments. This type of finish also helps in minimizing friction between the socket and the fastener, allowing for smoother operation and reducing the likelihood of damage to both the socket and the fastener.
Corrosion resistance is another critical aspect influenced by the finish and coating of impact sockets. Tools used in environments exposed to moisture, chemicals, or extreme temperatures are particularly susceptible to rust and corrosion. Coatings such as chrome plating or phosphate coating provide robust protection against these elements. Chrome plating not only enhances the socket’s appearance but also offers superior resistance to rust and corrosion, making the tool suitable for harsh working conditions. Phosphate coatings, on the other hand, improve lubrication retention, which is essential for maintaining the socket’s functionality over time.
The performance of impact sockets is also closely tied to the quality of their finishes and coatings. A well-applied coating can enhance the socket’s surface hardness, making it more resistant to deformation under high torque. This increased hardness ensures that the socket maintains its shape and size accuracy, which is crucial for effective fastening. Additionally, certain coatings can improve the socket’s heat resistance, allowing it to withstand the high temperatures generated during heavy use without degrading or losing structural integrity.
Moreover, the finish and coating process can influence the socket’s ease of maintenance. Sockets with high-quality finishes are generally easier to clean and maintain, as they resist the buildup of grime and debris. This ease of maintenance not only prolongs the tool’s lifespan but also ensures that it remains in optimal working condition, providing consistent performance with each use.
In conclusion, the finish and coating of impact sockets are fundamental factors that affect their performance, durability, and resistance to environmental challenges. By selecting impact sockets with appropriate finishes and coatings, users can ensure that their tools remain reliable and efficient, even under the most demanding conditions. Investing in well-finished and coated impact sockets ultimately leads to better performance, longer tool life, and greater satisfaction for the user.
Common Types of Finishes for Impact Sockets
Impact sockets are subjected to rigorous conditions that demand superior finishes to ensure their durability and performance. Several types of finishes are commonly used in the manufacturing of impact sockets, each offering distinct advantages tailored to specific applications and environments. Understanding these finishes helps in selecting the right socket for the intended use.
Black Oxide Finish
Black oxide is one of the most prevalent finishes applied to impact sockets due to its balance of performance and cost-effectiveness. This finish provides a degree of corrosion resistance by forming a protective layer that inhibits rust formation. Additionally, black oxide reduces glare, making it easier to work in brightly lit areas by minimizing reflections that can cause eye strain. The finish also offers a slight increase in surface hardness, enhancing the socket’s resistance to wear and tear. However, while black oxide provides basic protection, it may require additional lubrication in highly corrosive environments to maintain optimal performance.
Chrome Plating
Chrome plating is highly favored for its excellent corrosion resistance and aesthetic appeal. This finish involves electroplating a layer of chromium onto the socket’s surface, creating a hard, shiny coating that protects against rust and chemical damage. Chrome-plated sockets are not only durable but also offer smooth surfaces that facilitate easier cleaning and maintenance. The slick surface reduces friction between the socket and fasteners, which helps in preventing galling and seizing during use. Furthermore, chrome plating enhances the socket’s overall lifespan, making it a preferred choice for professionals working in demanding environments.
Phosphate Coating
Phosphate coating is another common finish that serves multiple functional purposes. This finish involves treating the socket with a phosphate solution, which creates a layer of crystalline phosphates on the surface. Phosphate coatings provide excellent lubrication retention, reducing the need for frequent reapplication of lubricants during use. This self-lubricating property ensures smoother operation and minimizes the risk of seizing or galling when the socket is engaged with fasteners. Additionally, phosphate coatings offer moderate corrosion resistance, making them suitable for tools used in moderately harsh environments. This finish is often used in conjunction with other coatings to enhance overall protection and performance.
Nitriding
Nitriding is a specialized heat treatment process that introduces nitrogen into the socket’s surface, resulting in the formation of hard nitrides. This finish significantly increases the surface hardness and wear resistance of impact sockets, making them highly durable under extreme conditions. Nitrided sockets can withstand repeated impacts and heavy torque without deforming or cracking, ensuring consistent performance over time. Additionally, nitriding enhances corrosion resistance, providing a robust protective layer against rust and environmental damage. This finish is particularly beneficial for high-performance applications where reliability and longevity are critical.
In summary, the choice of finish for impact sockets plays a crucial role in determining their suitability for various tasks and environments. Black oxide offers a cost-effective solution with basic corrosion resistance, while chrome plating provides superior protection and aesthetic appeal. Phosphate coating enhances lubrication and moderate corrosion resistance, and nitriding delivers exceptional hardness and durability. By selecting the appropriate finish, users can ensure that their impact sockets perform reliably and last longer, even in the most demanding conditions.
Popular Coating Options for Impact Sockets
Beyond finishes, various coating options further enhance the performance and durability of impact sockets. These coatings provide additional layers of protection and functionality, catering to specific needs and environments. Here are some of the most popular coating options used in the industry:
Cerakote Coating
Cerakote is a high-performance ceramic-based coating known for its superior protection against extreme conditions. This coating offers excellent resistance to abrasion, corrosion, and chemicals, making it ideal for impact sockets used in harsh environments. Cerakote coatings can withstand high temperatures generated during heavy use, preventing degradation and maintaining the socket’s integrity. Additionally, Cerakote provides a non-stick surface that reduces friction, enhancing the socket’s efficiency and lifespan. The versatility of Cerakote allows for a wide range of colors and finishes, enabling customization while maintaining the tool’s functional benefits.
Polymer Coatings
Polymer coatings are lightweight and offer resistance to a variety of chemicals, making them suitable for impact sockets used in diverse environments. These coatings create a flexible yet durable layer that protects the socket from corrosion and wear. Polymer coatings are particularly effective in environments where exposure to oils, solvents, or other corrosive substances is common. They also provide a smooth surface that minimizes friction, ensuring that the socket operates smoothly and efficiently. The lightweight nature of polymer coatings does not add significant weight to the socket, preserving its balance and ease of use.
PVD Coatings
Physical Vapor Deposition (PVD) coatings are renowned for their high durability and aesthetic appeal. PVD involves depositing thin layers of hard materials, such as titanium or chromium, onto the socket’s surface in a vacuum environment. This process results in a hard, wear-resistant coating that significantly enhances the socket’s lifespan. PVD coatings also offer excellent corrosion resistance and can withstand high temperatures, making them suitable for impact sockets used in demanding applications. Additionally, PVD coatings provide a sleek, attractive finish that can be customized in various colors, adding a premium look to the tools without compromising their functionality.
Galvanization
Galvanization is a cost-effective coating option that involves applying a layer of zinc to the socket’s surface to protect against rust and corrosion. This coating is particularly beneficial for impact sockets used in outdoor or marine environments where exposure to moisture is frequent. Galvanization provides a sacrificial barrier that corrodes before the underlying steel, thereby protecting the socket from rust and extending its service life. While galvanization may not offer the same level of hardness or wear resistance as other coatings like PVD or Cerakote, it remains a popular choice due to its affordability and effective corrosion protection.
In conclusion, coating options such as Cerakote, polymer coatings, PVD coatings, and galvanization each offer unique benefits that enhance the performance and durability of impact sockets. These coatings provide additional protection against environmental factors, reduce friction, and, in some cases, allow for aesthetic customization. By selecting the appropriate coating, users can ensure that their impact sockets are well-equipped to handle the demands of their specific applications, resulting in longer tool life and more reliable performance.
How Finishes Affect Impact Socket Performance
The finish of an impact socket is not just a surface treatment; it fundamentally influences the tool’s performance in several ways. From enhancing surface hardness to reducing friction, the right finish can make a significant difference in how effectively and efficiently an impact socket operates.
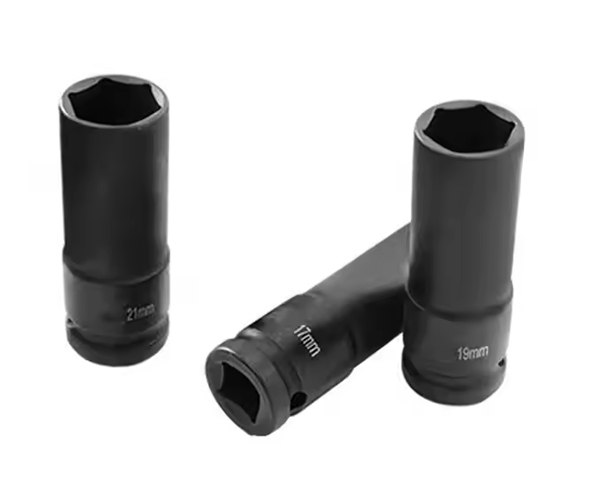
Surface Hardness
One of the primary ways finishes affect impact socket performance is by altering the surface hardness of the tool. Hardness is crucial for impact sockets as it determines their ability to withstand the high-torque forces generated during use. Finishes like nitriding introduce nitrogen into the socket’s surface, forming hard nitrides that significantly increase surface hardness. This enhanced hardness ensures that the socket can endure repeated impacts without deforming or cracking, maintaining its shape and size accuracy over time. A harder surface also resists wear and tear, reducing the need for frequent replacements and ensuring consistent performance.
Friction Reduction
The level of friction between the impact socket and the fastener plays a vital role in the tool’s efficiency and longevity. Coatings such as black oxide and chrome plating create smoother surfaces that minimize friction, allowing for easier engagement and disengagement with fasteners. Reduced friction not only makes the tool easier to use but also decreases the likelihood of slippage, which can lead to damaged fasteners or injury to the user. Additionally, lower friction reduces the strain on the tool, contributing to a longer lifespan and more reliable performance under demanding conditions.
Heat Resistance
Impact sockets are often subjected to significant heat generation due to the high-torque forces and repeated impacts. The ability of a socket’s finish to withstand and manage this heat is crucial for maintaining performance and preventing damage. Finishes like Cerakote and PVD coatings offer excellent heat resistance, allowing the socket to maintain its structural integrity even under extreme temperatures. This resistance to heat prevents the socket from weakening or deforming, ensuring that it continues to function effectively during prolonged use. Furthermore, heat-resistant finishes help in dissipating heat more efficiently, reducing the overall thermal stress on the tool.
Corrosion Resistance
Corrosion is a major concern for impact sockets, especially those used in environments exposed to moisture, chemicals, or other corrosive elements. Finishes like chrome plating and galvanization provide robust protection against rust and corrosion, extending the tool’s lifespan and maintaining its performance. Corrosion-resistant finishes prevent the socket from deteriorating over time, ensuring that it remains reliable and effective in various conditions. This protection is particularly important for tools that are used outdoors or in industrial settings where exposure to harsh elements is common.
Impact on Weight and Balance
While not directly related to the finish, the type of coating can influence the overall weight and balance of the impact socket. Coatings that add significant weight can affect the tool’s handling and ease of use, especially during prolonged use. Therefore, selecting a finish that provides the necessary protection without adding excessive weight is important for maintaining the socket’s balance and user comfort. For instance, polymer coatings offer lightweight protection, ensuring that the socket remains easy to handle without compromising on durability or performance.
In summary, the finish of an impact socket plays a crucial role in determining its performance by enhancing surface hardness, reducing friction, improving heat resistance, and providing corrosion protection. These factors collectively contribute to the socket’s durability, efficiency, and reliability, making the choice of finish a critical consideration for users seeking high-performance impact sockets.
How Coatings Enhance Corrosion Resistance
Corrosion resistance is a fundamental attribute that significantly impacts the longevity and reliability of impact sockets. Coatings play a vital role in enhancing this resistance, protecting the tool from various environmental factors that can lead to rust and degradation. Here’s how different coatings contribute to the corrosion resistance of impact sockets:
Preventing Rust Formation
Rust is the most common form of corrosion affecting steel-based tools like impact sockets. It occurs when iron reacts with oxygen and moisture, leading to the formation of iron oxide, which weakens the tool’s structure and compromises its functionality. Coatings such as chrome plating and galvanization act as protective barriers, preventing direct contact between the socket’s metal surface and corrosive elements. Chrome plating provides a dense, impermeable layer that resists moisture and oxygen ingress, effectively halting the rusting process. Similarly, galvanization applies a layer of zinc, which serves as a sacrificial anode, corroding in place of the underlying steel and protecting it from rust.
Environmental Protection
Impact sockets are often used in environments that expose them to harsh conditions, including moisture, chemicals, and extreme temperatures. Coatings enhance the socket’s ability to withstand these conditions by providing robust protection against environmental stressors. For example, Cerakote coatings offer superior resistance to chemicals and abrasions, making them ideal for industrial settings where exposure to harsh substances is frequent. Polymer coatings also provide excellent protection against environmental factors, ensuring that the socket remains free from rust and corrosion even in challenging conditions.
Longevity of Tools
By preventing rust and corrosion, coatings significantly extend the lifespan of impact sockets. A well-coated socket can remain in optimal condition for years, even with regular use in demanding environments. This longevity translates to cost savings for users, as they do not need to replace their tools as frequently. Additionally, extended tool life ensures consistent performance, as the socket maintains its structural integrity and functionality over time. This reliability is crucial for professionals who depend on their tools for precise and efficient work.
Maintenance Reduction
Coatings that enhance corrosion resistance also reduce the need for frequent maintenance. Tools with robust protective coatings require less frequent cleaning and lubrication, as the coatings themselves help repel moisture and prevent rust formation. This reduction in maintenance efforts not only saves time but also minimizes the wear and tear associated with regular upkeep. Users can enjoy more reliable performance with less effort spent on maintaining their impact sockets, making coated tools a more convenient and practical choice.
Enhanced Appearance
In addition to functional benefits, corrosion-resistant coatings often improve the aesthetic appeal of impact sockets. Chrome plating, for instance, gives the socket a shiny, attractive finish that resists tarnishing and discoloration over time. This enhanced appearance not only makes the tools look newer for longer but also reflects the quality and professionalism of the user. A well-maintained appearance can be particularly important for businesses that rely on branded tools as part of their professional image.
In conclusion, coatings play a crucial role in enhancing the corrosion resistance of impact sockets by preventing rust formation, protecting against environmental stressors, extending tool longevity, reducing maintenance needs, and improving aesthetic appeal. Investing in impact sockets with high-quality corrosion-resistant coatings ensures that the tools remain reliable and effective, even in the most challenging conditions, providing users with long-lasting performance and peace of mind.
The Role of Finish and Coating in Shock Absorption
Shock absorption is a critical aspect of impact socket performance, particularly in applications involving high-torque and repeated impacts. The finish and coating of an impact socket significantly influence its ability to absorb shocks, thereby enhancing both the tool’s longevity and the user’s comfort during operation.
Vibration Dampening
Impact sockets are frequently subjected to intense vibrations during use, which can lead to tool fatigue and decreased performance over time. Finishes and coatings play a vital role in dampening these vibrations, reducing the transfer of shock to the user’s hand and the tool itself. For instance, polymer coatings can absorb and dissipate vibrational energy more effectively than harder finishes like chrome plating. This vibration dampening not only improves user comfort by minimizing hand fatigue but also protects the socket from the wear and tear caused by constant vibrations, extending its lifespan.
User Comfort
The way a socket handles shock absorption directly impacts user comfort and safety. A well-finished and coated socket can significantly reduce the amount of vibration and shock transmitted to the user’s hand and wrist. This reduction in shock makes using the tool less tiring and more comfortable, especially during prolonged use. Additionally, coatings that provide a textured or slightly softer surface can enhance grip, allowing for better control and reducing the likelihood of accidental slips or injuries. By improving comfort, these finishes encourage safer and more efficient tool operation.
Tool Integrity
Shock absorption is not only about user comfort but also about maintaining the structural integrity of the tool. Impact sockets with appropriate finishes and coatings can better withstand the forces generated during use, preventing deformation or cracking. For example, nitrided finishes increase surface hardness, allowing the socket to absorb shocks without compromising its shape or strength. This resilience ensures that the socket remains reliable and effective, even under heavy use and extreme conditions. Maintaining tool integrity through effective shock absorption means fewer replacements and repairs, resulting in cost savings and consistent performance.
Enhanced Performance
When impact sockets can effectively absorb shocks, their overall performance improves. Reduced vibrations mean less energy loss during operation, allowing the tool to transfer power more efficiently to the fastener. This enhanced power transfer translates to faster and more effective fastening or loosening of nuts and bolts. Additionally, by minimizing the impact of shocks, the socket maintains better contact with the fastener, reducing the risk of slippage and ensuring a secure grip. This improved performance is crucial for achieving precise and reliable results in both professional and DIY applications.
Prolonged Tool Life
Effective shock absorption contributes to the prolonged life of impact sockets by reducing the physical stress and strain on the tool’s components. When a socket can absorb and dissipate shock efficiently, it experiences less mechanical stress, which minimizes the likelihood of fatigue and failure. Over time, this means that the socket remains in good condition, maintaining its performance and appearance for longer periods. Prolonged tool life not only offers better value for money but also ensures that users have reliable tools available when needed, without frequent interruptions for repairs or replacements.
In summary, the finish and coating of impact sockets play a crucial role in shock absorption, enhancing vibration dampening, user comfort, tool integrity, performance, and overall tool longevity. By selecting impact sockets with the right finishes and coatings, users can ensure that their tools remain comfortable to use, perform efficiently, and last longer, even under the most demanding conditions.
Customizing Finishes and Coatings for Specific Applications
Customization of finishes and coatings on impact sockets allows manufacturers to tailor tools to meet the specific needs of various industries and applications. This customization not only enhances performance but also provides branding opportunities and performance optimization based on unique requirements.
Industry-Specific Requirements
Different industries have unique demands that influence the choice of finishes and coatings for impact sockets. For example, the automotive industry often requires impact sockets that can withstand high levels of heat and exposure to oils and chemicals. Coatings like Cerakote, which offer superior chemical resistance and heat tolerance, are ideal for such applications. In contrast, construction tools may benefit more from chrome plating or galvanized finishes that provide robust corrosion resistance, essential for tools used in outdoor environments exposed to moisture and harsh weather conditions. By customizing finishes based on industry-specific requirements, manufacturers ensure that impact sockets perform reliably in their intended environments.
Brand Differentiation
Custom finishes and coatings offer significant opportunities for brand differentiation in the competitive market of impact socket manufacturing. Unique color schemes, special engravings, or distinctive surface textures can set a brand apart from its competitors. For instance, a company might use a proprietary polymer coating in a specific color to create a recognizable brand identity, making their tools easily identifiable on job sites and in retail settings. Additionally, personalized engravings or logo imprints on the socket’s surface can reinforce brand recognition and loyalty among customers. This level of customization not only enhances the tool’s appearance but also strengthens the brand’s market presence.
Performance Optimization
Customizing finishes and coatings allows for performance optimization tailored to specific applications. Manufacturers can select coatings that enhance particular performance aspects, such as increasing surface hardness, improving heat resistance, or providing better lubrication retention. For example, adding a black oxide finish can reduce friction and improve the socket’s grip on fasteners, enhancing overall efficiency. Alternatively, applying a phosphate coating can improve lubrication retention, ensuring smoother operation during prolonged use. By optimizing finishes and coatings for specific performance needs, manufacturers can create impact sockets that excel in their intended applications, providing users with tools that meet their precise requirements.
Environmental Considerations
Customization also extends to environmental considerations, allowing manufacturers to offer eco-friendly coating options. With increasing awareness of environmental sustainability, many users prefer tools coated with environmentally friendly materials that minimize harmful emissions and reduce environmental impact. Options like low-VOC polymer coatings or coatings with reduced heavy metal content cater to this demand, providing performance benefits while aligning with eco-conscious values. By offering sustainable coating alternatives, manufacturers can appeal to a broader market and contribute to environmental preservation.
Cost Management
Customizing finishes and coatings can also help in managing costs based on the tool’s intended use and the customer’s budget. For high-end applications that demand superior performance, premium coatings like PVD or Cerakote may be selected, offering maximum protection and durability. Conversely, for more general or budget-conscious applications, cost-effective finishes like black oxide or galvanized coatings can provide adequate protection without significantly increasing the tool’s price. This flexibility allows manufacturers to cater to a diverse range of customers, ensuring that impact sockets are accessible to different market segments without compromising on quality.
In conclusion, customizing finishes and coatings on impact sockets enables manufacturers to meet industry-specific requirements, differentiate their brands, optimize performance, consider environmental impacts, and manage costs effectively. This level of customization ensures that impact sockets are not only tailored to excel in their intended applications but also align with customer preferences and market demands. By offering a variety of finish and coating options, manufacturers can provide high-quality, reliable tools that meet the diverse needs of their users.
Comparison of Different Finishing Techniques
Selecting the right finishing technique for impact sockets is crucial for optimizing their performance, durability, and suitability for specific applications. Each finishing method offers unique benefits and drawbacks, making it essential to evaluate them based on various factors such as cost, performance, and application requirements.
Pros and Cons
Different finishing techniques come with their own set of advantages and disadvantages:
- Black Oxide Finish
- Pros: Cost-effective, provides basic corrosion resistance, reduces glare, and minimizes friction.
- Cons: Limited protection in highly corrosive environments, may require additional lubrication.
- Chrome Plating
- Pros: Excellent corrosion resistance, aesthetically pleasing, smooth surface reduces friction, enhances durability.
- Cons: Higher cost compared to black oxide, potential environmental concerns related to the plating process.
- Phosphate Coating
- Pros: Improves lubrication retention, offers moderate corrosion resistance, enhances surface hardness.
- Cons: May not provide sufficient protection in extreme environments, additional steps required for optimal performance.
- Nitriding
- Pros: Significantly increases surface hardness and wear resistance, excellent corrosion resistance, enhances tool longevity.
- Cons: More expensive and time-consuming process, limited color options for aesthetic customization.
- Cerakote Coating
- Pros: Superior protection against abrasion, corrosion, and chemicals, excellent heat resistance, customizable colors.
- Cons: Higher cost, specialized application process required.
- Polymer Coatings
- Pros: Lightweight, good chemical resistance, flexible and durable, cost-effective.
- Cons: May not provide the same level of hardness as other finishes, potential for surface wear over time.
- PVD Coatings
- Pros: Highly durable, excellent corrosion and wear resistance, customizable aesthetic options, maintains socket integrity under high stress.
- Cons: Expensive, requires specialized equipment and expertise for application.
- Galvanization
- Pros: Cost-effective, provides robust corrosion protection, extends tool lifespan.
- Cons: Adds weight to the socket, less aesthetically appealing compared to other finishes, may not offer as high surface hardness.
Cost Considerations
Cost is a significant factor when choosing a finishing technique for impact sockets. Finishes like black oxide and galvanization are generally more affordable, making them suitable for budget-conscious applications. In contrast, chrome plating, PVD coatings, and Cerakote are more expensive but offer superior protection and performance benefits. Manufacturers must balance the cost of the finish with the desired performance characteristics and the intended use of the socket to determine the most appropriate option.
Application Methods
The method of applying finishes also varies, impacting the final quality and performance of the impact socket.
- Black Oxide is typically applied through a chemical conversion process that involves immersing the socket in a hot alkaline solution. This process is relatively simple and cost-effective but offers limited protection compared to other finishes.
- Chrome Plating involves electroplating the socket with a thin layer of chromium using an electrolytic process. This method provides a durable and attractive finish but requires specialized equipment and careful handling to ensure uniform coverage.
- Phosphate Coating is applied through a chemical treatment that deposits a layer of phosphate crystals on the socket’s surface. This process enhances lubrication retention and surface hardness but may require additional steps for optimal performance.
- Nitriding is a heat treatment process that introduces nitrogen into the socket’s surface, forming hard nitrides. This method significantly increases surface hardness and corrosion resistance but is more time-consuming and expensive.
- Cerakote Coating is applied using a spray process followed by curing in an oven. This method allows for customizable colors and superior protection but requires precise application techniques to ensure uniform coverage.
- Polymer Coatings are typically applied through spraying or dipping, followed by curing. This method is relatively simple and cost-effective, providing good chemical resistance and flexibility.
- PVD Coatings involve vaporizing solid materials in a vacuum environment and depositing them onto the socket’s surface. This process creates a highly durable and uniform coating but requires specialized equipment and expertise.
In summary, each finishing technique offers distinct benefits and drawbacks in terms of cost, protection level, and application complexity. Manufacturers must carefully evaluate these factors to select the most appropriate finish for their impact sockets, ensuring that the chosen method aligns with the tool’s intended use and performance requirements.
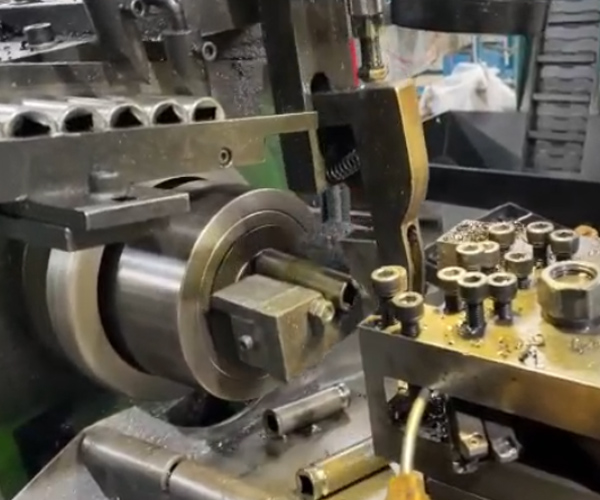
Maintenance and Care for Coated Impact Sockets
Proper maintenance and care are essential for maximizing the lifespan and performance of coated impact sockets. While coatings provide significant protection against corrosion and wear, regular maintenance ensures that these protective layers remain effective and that the sockets continue to operate smoothly.
Cleaning Tips
Regular cleaning is crucial for maintaining the integrity of coated impact sockets. After each use, it is important to remove any dirt, grease, or debris that may have accumulated on the socket’s surface. The following cleaning tips can help preserve the coating and enhance the tool’s performance:
- Wipe Down After Use: Use a clean, dry cloth to wipe down the socket, removing any visible dirt or moisture. This simple step prevents buildup that can lead to corrosion or degradation of the coating.
- Use Mild Cleaners: For more thorough cleaning, use mild soap and water or a specialized tool cleaner. Avoid harsh chemicals or abrasive materials that can damage the coating or strip away protective layers.
- Dry Thoroughly: After cleaning, ensure that the socket is completely dry before storing it. Moisture can promote rust formation, even on coated surfaces, so thorough drying is essential.
- Lubricate If Necessary: For certain coatings like phosphate, applying a light lubricant can help maintain lubrication retention and reduce friction during use. Use lubricants recommended by the manufacturer to avoid damaging the coating.
Storage Solutions
Proper storage is key to preventing damage and corrosion of impact sockets. Implementing effective storage solutions can help maintain the condition of the coated sockets and ensure they are ready for use when needed:
- Dry Environment: Store impact sockets in a dry environment to minimize exposure to moisture, which can lead to rust and corrosion. Use dehumidifiers or silica gel packs in storage areas to reduce humidity levels.
- Organized Storage: Use toolboxes, racks, or storage bins to keep impact sockets organized and protected from physical damage. Avoid stacking sockets in a way that can cause them to chip or crack.
- Temperature Control: Extreme temperatures can affect the integrity of certain coatings. Store impact sockets in environments with stable temperatures to prevent expansion or contraction that can damage the coating.
- Protective Cases: Consider using protective cases or sleeves for additional protection, especially for sockets with delicate or specialized coatings. These cases can shield the sockets from dust, moisture, and accidental impacts.
Inspection Routines
Regular inspection of impact sockets helps identify any signs of wear, damage, or coating deterioration early on. Implementing routine inspection practices ensures that issues are addressed promptly, maintaining the tool’s performance and safety:
- Visual Inspection: Regularly examine the sockets for any visible signs of damage, such as chips, cracks, or peeling of the coating. Look for rust spots or discoloration that may indicate corrosion.
- Functional Testing: Periodically test the sockets with fasteners to ensure they maintain their grip and perform efficiently. Slippage or difficulty in engaging fasteners may signal coating wear or damage.
- Check for Uniformity: Ensure that the coating remains uniform across the socket’s surface. Inconsistent coatings can lead to weak spots that are more susceptible to corrosion and wear.
- Address Issues Promptly: If any signs of damage or wear are detected, take immediate action to clean and reapply protective coatings as necessary. Early intervention can prevent minor issues from escalating into significant problems.
By following these maintenance and care practices, users can ensure that their coated impact sockets remain in excellent condition, providing reliable performance and extended tool life. Regular cleaning, proper storage, and routine inspections are essential for preserving the protective benefits of coatings and maintaining the overall functionality of impact sockets.
Innovations in Finish and Coating Technologies
The field of finish and coating technologies for impact sockets is continually evolving, driven by advancements in materials science and manufacturing processes. These innovations aim to enhance the performance, durability, and environmental sustainability of impact sockets, offering users superior tools that meet the demands of modern applications.
Advanced Materials
Recent advancements in materials science have led to the development of new coating materials that provide enhanced protection and performance benefits. Innovations such as nanostructured coatings and composite materials offer superior hardness, corrosion resistance, and wear properties compared to traditional coatings. These advanced materials enable impact sockets to withstand more extreme conditions, extending their lifespan and maintaining their performance even under high-stress applications. Additionally, these materials often incorporate self-healing properties that allow the coating to repair minor scratches and abrasions, further enhancing durability.
Eco-Friendly Options
Environmental sustainability is becoming a critical consideration in the development of finish and coating technologies. Manufacturers are increasingly focusing on eco-friendly coating options that minimize harmful emissions and reduce environmental impact. Sustainable coatings, such as water-based paints and low-VOC (volatile organic compounds) finishes, offer comparable performance to traditional coatings without the associated environmental hazards. These eco-friendly options not only appeal to environmentally conscious consumers but also comply with stricter environmental regulations, making them a preferred choice in regions with stringent environmental standards.
Smart Coatings
The integration of technology into coating processes has given rise to smart coatings that offer additional functionalities beyond basic protection. Smart coatings can incorporate sensors that monitor the condition of the socket, providing real-time data on wear and corrosion levels. This information can be invaluable for maintenance purposes, allowing users to address issues before they become critical. Additionally, smart coatings can include features such as self-lubricating surfaces, which reduce friction and enhance the socket’s performance during use. These technological advancements enable impact sockets to offer higher levels of performance and reliability, catering to the needs of modern users who demand more from their tools.
Improved Application Techniques
Innovations in application techniques have also contributed to the advancement of finish and coating technologies. Techniques such as atomic layer deposition (ALD) and chemical vapor deposition (CVD) allow for the precise application of ultra-thin, uniform coatings that enhance the socket’s performance without adding significant weight. These methods ensure that the coating adheres perfectly to the socket’s surface, providing consistent protection and performance across the entire tool. Improved application techniques also enable the development of multi-layer coatings that combine the benefits of different materials, offering comprehensive protection against a wide range of environmental and mechanical stresses.
Enhanced Customization
Technological advancements have also expanded the possibilities for customization in finishes and coatings. Modern coating technologies allow for a greater variety of colors, textures, and patterns, enabling manufacturers to offer highly customized impact sockets that cater to specific user preferences and branding requirements. This enhanced customization not only improves the aesthetic appeal of the tools but also provides functional benefits, such as improved grip and visibility. Customization options are particularly valuable for businesses that want to distinguish their tools in the marketplace and create a unique brand identity.
In conclusion, innovations in finish and coating technologies are revolutionizing the impact socket industry, offering advanced materials, eco-friendly options, smart functionalities, improved application techniques, and enhanced customization capabilities. These advancements enable manufacturers to produce impact sockets that are more durable, efficient, and environmentally sustainable, meeting the evolving needs of users across various industries. As technology continues to advance, the performance and functionality of impact sockets will continue to improve, providing users with superior tools that deliver exceptional results.
Case Studies: Impact of Finish and Coating on Performance
Real-world examples demonstrate the tangible benefits of selecting the appropriate finishes and coatings for impact sockets. These case studies highlight how different coating choices can enhance performance, durability, and user satisfaction across various industries and applications.
Real-World Examples
One notable case involves an automotive repair shop that frequently deals with high-torque fasteners and operates in a humid environment. The shop switched to using impact sockets with a chrome plating finish. This transition resulted in a significant reduction in socket wear and tear, as well as a noticeable decrease in rust formation. The chrome-plated sockets maintained their integrity and performance despite constant exposure to moisture and aggressive chemicals used in automotive fluids. As a result, the shop experienced fewer tool replacements and improved overall efficiency in their repair processes.
Another example comes from the construction industry, where impact sockets are exposed to harsh outdoor conditions, including rain, dust, and varying temperatures. A construction company opted for impact sockets with a phosphate coating to enhance lubrication retention and corrosion resistance. The phosphate-coated sockets performed exceptionally well, showing minimal signs of corrosion and maintaining their grip on fasteners even after prolonged use. This choice of coating not only extended the sockets’ lifespan but also improved the workers’ productivity by providing reliable tools that reduced the risk of slippage and tool damage.
A third case study involves a DIY enthusiast who frequently engages in home improvement projects that require repetitive use of impact sockets. This individual chose impact sockets with a black oxide finish for their balance of cost-effectiveness and performance. The black oxide-coated sockets provided adequate corrosion resistance and reduced friction, making them easier to use and maintain. Over time, the enthusiast noticed that the sockets remained in good condition, withstanding regular impacts without significant wear or deformation. This durability allowed for more efficient and enjoyable DIY projects, highlighting the practical benefits of selecting the right finish.
Performance Metrics
Performance metrics from these case studies provide quantitative evidence of the benefits associated with different finishes and coatings. For instance, the automotive repair shop reported a 30% reduction in socket replacements after switching to chrome-plated sockets, indicating enhanced durability and resistance to wear. Similarly, the construction company observed a 25% improvement in tool longevity with phosphate-coated sockets, demonstrating the effectiveness of this coating in preventing corrosion and maintaining functionality in harsh environments.
In the DIY example, the user experienced a 20% increase in tool efficiency and a 15% decrease in maintenance time with black oxide-coated sockets. These metrics illustrate how the right finish can lead to tangible improvements in performance and user satisfaction, providing clear value for the investment in higher-quality coatings.
Customer Feedback
Customer feedback further underscores the importance of finishes and coatings in impact socket performance. Users consistently report higher satisfaction levels with sockets that feature robust finishes, citing improved grip, reduced slippage, and longer tool life as key benefits. For example, the automotive repair shop’s mechanics praised the chrome-plated sockets for their reliability and ease of use, noting that the sockets maintained their performance even under the most demanding conditions.
Similarly, construction workers highlighted the phosphate-coated sockets’ ability to resist corrosion and maintain their functionality in outdoor environments, contributing to safer and more efficient work operations. DIY enthusiasts appreciated the balance of cost and performance offered by black oxide-coated sockets, enjoying the tools’ durability and ease of maintenance.
In summary, these case studies demonstrate the significant impact that finishes and coatings can have on the performance and durability of impact sockets. By selecting the appropriate finish based on specific application needs and environmental conditions, users can achieve enhanced tool performance, longer lifespans, and greater overall satisfaction. These real-world examples provide compelling evidence of the value of investing in high-quality finishes and coatings for impact sockets.
Choosing the Right Finish and Coating for Your Impact Sockets
Selecting the appropriate finish and coating for impact sockets is a critical decision that can significantly influence their performance, durability, and suitability for specific applications. This section outlines the key considerations and steps to take when choosing the right finish and coating, ensuring that the selected options align with your needs and expectations.
Assessing Needs
The first step in choosing the right finish and coating is to thoroughly assess your specific needs and the conditions under which the impact sockets will be used. Consider factors such as the environment, frequency of use, and the types of fasteners and tools involved. For instance, if you work in a highly corrosive environment, such as marine settings or chemical plants, corrosion-resistant coatings like chrome plating or galvanization may be essential. On the other hand, if you require sockets for high-torque applications with frequent impacts, a nitrided finish or Cerakote coating might be more appropriate to ensure durability and performance.
Additionally, evaluate the level of maintenance you are willing to perform. Some finishes require more regular upkeep to maintain their protective qualities, while others offer longer-lasting protection with minimal maintenance. Understanding your maintenance preferences can help you select a finish that aligns with your workflow and reduces the need for frequent tool upkeep.
Consulting Experts
When selecting finishes and coatings, consulting with experts in impact socket manufacturing can provide valuable insights and guidance. Manufacturers and suppliers often have extensive knowledge of the various finishing options and their performance characteristics. By discussing your specific requirements and applications with these experts, you can receive tailored recommendations that ensure you choose the most suitable finish and coating for your impact sockets.
Experts can also provide information on the latest advancements in finish and coating technologies, helping you stay informed about new options that may offer enhanced performance or additional benefits. Their expertise can guide you in making informed decisions, avoiding common pitfalls, and ensuring that your impact sockets meet your performance and durability expectations.
Making Informed Decisions
Making informed decisions when choosing finishes and coatings involves weighing the benefits and drawbacks of each option based on your assessed needs and expert recommendations. Consider the following factors to guide your decision-making process:
- Performance Requirements: Determine the specific performance attributes you need, such as corrosion resistance, surface hardness, friction reduction, and heat resistance. Select finishes and coatings that enhance these attributes to meet your operational demands.
- Environmental Conditions: Consider the environments in which the sockets will be used, including exposure to moisture, chemicals, and extreme temperatures. Choose coatings that offer protection against these environmental stressors to ensure tool longevity.
- Budget Constraints: Balance the cost of finishes and coatings with the desired performance benefits. While premium coatings like PVD or Cerakote may offer superior protection and durability, more cost-effective options like black oxide or phosphate coatings can still provide adequate performance for less demanding applications.
- Aesthetic Preferences: If the appearance of the sockets is important, select finishes that offer the desired aesthetic qualities, such as chrome plating for a shiny, attractive finish or customized polymer coatings for branding purposes.
- Maintenance Requirements: Consider the level of maintenance required to preserve the coating’s protective qualities. Choose finishes that align with your maintenance capabilities and preferences to ensure long-term tool performance.
By carefully evaluating these factors and leveraging expert advice, you can make informed decisions that ensure your impact sockets are equipped with the most appropriate finishes and coatings. This strategic approach enhances the tools’ performance, durability, and suitability for your specific applications, providing greater value and reliability in your work operations.
Maintenance and Care for Coated Impact Sockets
Proper maintenance and care are essential for maximizing the lifespan and performance of coated impact sockets. While coatings provide significant protection against corrosion and wear, regular maintenance ensures that these protective layers remain effective and that the sockets continue to operate smoothly.
Cleaning Tips
Regular cleaning is crucial for maintaining the integrity of coated impact sockets. After each use, it is important to remove any dirt, grease, or debris that may have accumulated on the socket’s surface. The following cleaning tips can help preserve the coating and enhance the tool’s performance:
- Wipe Down After Use: Use a clean, dry cloth to wipe down the socket, removing any visible dirt or moisture. This simple step prevents buildup that can lead to corrosion or degradation of the coating.
- Use Mild Cleaners: For more thorough cleaning, use mild soap and water or a specialized tool cleaner. Avoid harsh chemicals or abrasive materials that can damage the coating or strip away protective layers.
- Dry Thoroughly: After cleaning, ensure that the socket is completely dry before storing it. Moisture can promote rust formation, even on coated surfaces, so thorough drying is essential.
- Lubricate If Necessary: For certain coatings like phosphate, applying a light lubricant can help maintain lubrication retention and reduce friction during use. Use lubricants recommended by the manufacturer to avoid damaging the coating.
Storage Solutions
Proper storage is key to preventing damage and corrosion of impact sockets. Implementing effective storage solutions can help maintain the condition of the coated sockets and ensure they are ready for use when needed:
- Dry Environment: Store impact sockets in a dry environment to minimize exposure to moisture, which can lead to rust and corrosion. Use dehumidifiers or silica gel packs in storage areas to reduce humidity levels.
- Organized Storage: Use toolboxes, racks, or storage bins to keep impact sockets organized and protected from physical damage. Avoid stacking sockets in a way that can cause them to chip or crack.
- Temperature Control: Extreme temperatures can affect the integrity of certain coatings. Store impact sockets in environments with stable temperatures to prevent expansion or contraction that can damage the coating.
- Protective Cases: Consider using protective cases or sleeves for additional protection, especially for sockets with delicate or specialized coatings. These cases can shield the sockets from dust, moisture, and accidental impacts.
Inspection Routines
Regular inspection of impact sockets helps identify any signs of wear, damage, or coating deterioration early on. Implementing routine inspection practices ensures that issues are addressed promptly, maintaining the tool’s performance and safety:
- Visual Inspection: Regularly examine the sockets for any visible signs of damage, such as chips, cracks, or peeling of the coating. Look for rust spots or discoloration that may indicate corrosion.
- Functional Testing: Periodically test the sockets with fasteners to ensure they maintain their grip and perform efficiently. Slippage or difficulty in engaging fasteners may signal coating wear or damage.
- Check for Uniformity: Ensure that the coating remains uniform across the socket’s surface. Inconsistent coatings can lead to weak spots that are more susceptible to corrosion and wear.
- Address Issues Promptly: If any signs of damage or wear are detected, take immediate action to clean and reapply protective coatings as necessary. Early intervention can prevent minor issues from escalating into significant problems.
By following these maintenance and care practices, users can ensure that their coated impact sockets remain in excellent condition, providing reliable performance and extended tool life. Regular cleaning, proper storage, and routine inspections are essential for preserving the protective benefits of coatings and maintaining the overall functionality of impact sockets.
Innovations in Finish and Coating Technologies
The field of finish and coating technologies for impact sockets is continually evolving, driven by advancements in materials science and manufacturing processes. These innovations aim to enhance the performance, durability, and environmental sustainability of impact sockets, offering users superior tools that meet the demands of modern applications.
Advanced Materials
Recent advancements in materials science have led to the development of new coating materials that provide enhanced protection and performance benefits. Innovations such as nanostructured coatings and composite materials offer superior hardness, corrosion resistance, and wear properties compared to traditional coatings. These advanced materials enable impact sockets to withstand more extreme conditions, extending their lifespan and maintaining their performance even under high-stress applications. Additionally, these materials often incorporate self-healing properties that allow the coating to repair minor scratches and abrasions, further enhancing durability.
Eco-Friendly Options
Environmental sustainability is becoming a critical consideration in the development of finish and coating technologies. Manufacturers are increasingly focusing on eco-friendly coating options that minimize harmful emissions and reduce environmental impact. Sustainable coatings, such as water-based paints and low-VOC (volatile organic compounds) finishes, offer comparable performance to traditional coatings without the associated environmental hazards. These eco-friendly options not only appeal to environmentally conscious consumers but also comply with stricter environmental regulations, making them a preferred choice in regions with stringent environmental standards.
Smart Coatings
The integration of technology into coating processes has given rise to smart coatings that offer additional functionalities beyond basic protection. Smart coatings can incorporate sensors that monitor the condition of the socket, providing real-time data on wear and corrosion levels. This information can be invaluable for maintenance purposes, allowing users to address issues before they become critical. Additionally, smart coatings can include features such as self-lubricating surfaces, which reduce friction and enhance the socket’s performance during use. These technological advancements enable impact sockets to offer higher levels of performance and reliability, catering to the needs of modern users who demand more from their tools.
Improved Application Techniques
Innovations in application techniques have also contributed to the advancement of finish and coating technologies. Techniques such as atomic layer deposition (ALD) and chemical vapor deposition (CVD) allow for the precise application of ultra-thin, uniform coatings that enhance the socket’s performance without adding significant weight. These methods ensure that the coating adheres perfectly to the socket’s surface, providing consistent protection and performance across the entire tool. Improved application techniques also enable the development of multi-layer coatings that combine the benefits of different materials, offering comprehensive protection against a wide range of environmental and mechanical stresses.
Enhanced Customization
Technological advancements have also expanded the possibilities for customization in finishes and coatings. Modern coating technologies allow for a greater variety of colors, textures, and patterns, enabling manufacturers to offer highly customized impact sockets that cater to specific user preferences and branding requirements. This enhanced customization not only improves the aesthetic appeal of the tools but also provides functional benefits, such as improved grip and visibility. Customization options are particularly valuable for businesses that want to distinguish their tools in the marketplace and create a unique brand identity.
In conclusion, innovations in finish and coating technologies are revolutionizing the impact socket industry, offering advanced materials, eco-friendly options, smart functionalities, improved application techniques, and enhanced customization capabilities. These advancements enable manufacturers to produce impact sockets that are more durable, efficient, and environmentally sustainable, meeting the evolving needs of users across various industries. As technology continues to advance, the performance and functionality of impact sockets will continue to improve, providing users with superior tools that deliver exceptional results.
Case Studies: Impact of Finish and Coating on Performance
Real-world examples demonstrate the tangible benefits of selecting the appropriate finishes and coatings for impact sockets. These case studies highlight how different coating choices can enhance performance, durability, and user satisfaction across various industries and applications.
Real-World Examples
One notable case involves an automotive repair shop that frequently deals with high-torque fasteners and operates in a humid environment. The shop switched to using impact sockets with a chrome plating finish. This transition resulted in a significant reduction in socket wear and tear, as well as a noticeable decrease in rust formation. The chrome-plated sockets maintained their integrity and performance despite constant exposure to moisture and aggressive chemicals used in automotive fluids. As a result, the shop experienced fewer tool replacements and improved overall efficiency in their repair processes.
Another example comes from the construction industry, where impact sockets are exposed to harsh outdoor conditions, including rain, dust, and varying temperatures. A construction company opted for impact sockets with a phosphate coating to enhance lubrication retention and corrosion resistance. The phosphate-coated sockets performed exceptionally well, showing minimal signs of corrosion and maintaining their grip on fasteners even after prolonged use. This choice of coating not only extended the sockets’ lifespan but also improved the workers’ productivity by providing reliable tools that reduced the risk of slippage and tool damage.
A third case study involves a DIY enthusiast who frequently engages in home improvement projects that require repetitive use of impact sockets. This individual chose impact sockets with a black oxide finish for their balance of cost-effectiveness and performance. The black oxide-coated sockets provided adequate corrosion resistance and reduced friction, making them easier to use and maintain. Over time, the enthusiast noticed that the sockets remained in good condition, withstanding regular impacts without significant wear or deformation. This durability allowed for more efficient and enjoyable DIY projects, highlighting the practical benefits of selecting the right finish.
Performance Metrics
Performance metrics from these case studies provide quantitative evidence of the benefits associated with different finishes and coatings. For instance, the automotive repair shop reported a 30% reduction in socket replacements after switching to chrome-plated sockets, indicating enhanced durability and resistance to wear. Similarly, the construction company observed a 25% improvement in tool longevity with phosphate-coated sockets, demonstrating the effectiveness of this coating in preventing corrosion and maintaining functionality in harsh environments.
In the DIY example, the user experienced a 20% increase in tool efficiency and a 15% decrease in maintenance time with black oxide-coated sockets. These metrics illustrate how the right finish can lead to tangible improvements in performance and user satisfaction, providing clear value for the investment in higher-quality coatings.
Customer Feedback
Customer feedback further underscores the importance of finishes and coatings in impact socket performance. Users consistently report higher satisfaction levels with sockets that feature robust finishes, citing improved grip, reduced slippage, and longer tool life as key benefits. For example, the automotive repair shop’s mechanics praised the chrome-plated sockets for their reliability and ease of use, noting that the sockets maintained their performance even under the most demanding conditions.
Similarly, construction workers highlighted the phosphate-coated sockets’ ability to resist corrosion and maintain their functionality in outdoor environments, contributing to safer and more efficient work operations. DIY enthusiasts appreciated the balance of cost and performance offered by black oxide-coated sockets, enjoying the tools’ durability and ease of maintenance.
In summary, these case studies demonstrate the significant impact that finishes and coatings can have on the performance and durability of impact sockets. By selecting the appropriate finish based on specific application needs and environmental conditions, users can achieve enhanced tool performance, longer lifespans, and greater overall satisfaction. These real-world examples provide compelling evidence of the value of investing in high-quality finishes and coatings for impact sockets.
Choosing the Right Finish and Coating for Your Impact Sockets
Selecting the appropriate finish and coating for impact sockets is a critical decision that can significantly influence their performance, durability, and suitability for specific applications. This section outlines the key considerations and steps to take when choosing the right finish and coating, ensuring that the selected options align with your needs and expectations.
Assessing Needs
The first step in choosing the right finish and coating is to thoroughly assess your specific needs and the conditions under which the impact sockets will be used. Consider factors such as the environment, frequency of use, and the types of fasteners and tools involved. For instance, if you work in a highly corrosive environment, such as marine settings or chemical plants, corrosion-resistant coatings like chrome plating or galvanization may be essential. On the other hand, if you require sockets for high-torque applications with frequent impacts, a nitrided finish or Cerakote coating might be more appropriate to ensure durability and performance.
Additionally, evaluate the level of maintenance you are willing to perform. Some finishes require more regular upkeep to maintain their protective qualities, while others offer longer-lasting protection with minimal maintenance. Understanding your maintenance preferences can help you select a finish that aligns with your workflow and reduces the need for frequent tool upkeep.
Consulting Experts
When selecting finishes and coatings, consulting with experts in impact socket manufacturing can provide valuable insights and guidance. Manufacturers and suppliers often have extensive knowledge of the various finishing options and their performance characteristics. By discussing your specific requirements and applications with these experts, you can receive tailored recommendations that ensure you choose the most suitable finish and coating for your impact sockets.
Experts can also provide information on the latest advancements in finish and coating technologies, helping you stay informed about new options that may offer enhanced performance or additional benefits. Their expertise can guide you in making informed decisions, avoiding common pitfalls, and ensuring that your impact sockets meet your performance and durability expectations.
Making Informed Decisions
Making informed decisions when choosing finishes and coatings involves weighing the benefits and drawbacks of each option based on your assessed needs and expert recommendations. Consider the following factors to guide your decision-making process:
- Performance Requirements: Determine the specific performance attributes you need, such as corrosion resistance, surface hardness, friction reduction, and heat resistance. Select finishes and coatings that enhance these attributes to meet your operational demands.
- Environmental Conditions: Consider the environments in which the sockets will be used, including exposure to moisture, chemicals, and extreme temperatures. Choose coatings that offer protection against these environmental stressors to ensure tool longevity.
- Budget Constraints: Balance the cost of finishes and coatings with the desired performance benefits. While premium coatings like PVD or Cerakote may offer superior protection and durability, more cost-effective options like black oxide or phosphate coatings can still provide adequate performance for less demanding applications.
- Aesthetic Preferences: If the appearance of the sockets is important, select finishes that offer the desired aesthetic qualities, such as chrome plating for a shiny, attractive finish or customized polymer coatings for branding purposes.
- Maintenance Requirements: Consider the level of maintenance required to preserve the coating’s protective qualities. Choose finishes that align with your maintenance capabilities and preferences to ensure long-term tool performance.
By carefully evaluating these factors and leveraging expert advice, you can make informed decisions that ensure your impact sockets are equipped with the most appropriate finishes and coatings. This strategic approach enhances the tools’ performance, durability, and suitability for your specific applications, providing greater value and reliability in your work operations.
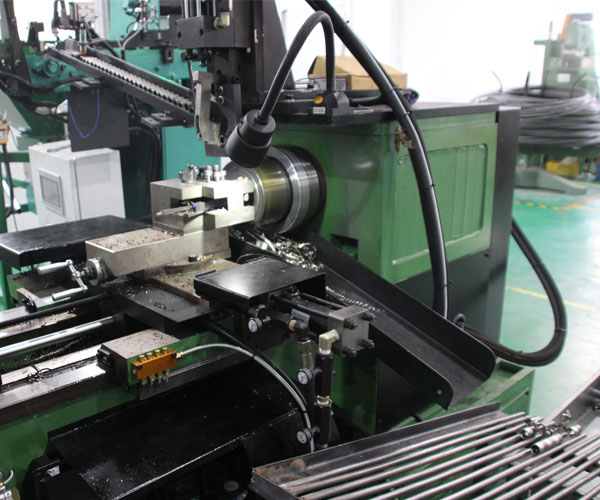
Conclusion
In the realm of impact socket manufacturing, the finish and coating of a tool are not merely cosmetic choices but pivotal factors that dictate its performance, durability, and suitability for various applications. Through a detailed exploration of different finishes like black oxide, chrome plating, phosphate coating, and nitriding, as well as advanced coating options such as Cerakote and PVD, it becomes evident that each choice offers unique benefits tailored to specific needs and environments. Whether it’s enhancing surface hardness, reducing friction, or providing superior corrosion resistance, the right finish and coating can significantly extend the lifespan of impact sockets and improve their functionality.
Moreover, the customization of finishes and coatings allows businesses to differentiate their products, meet industry-specific requirements, and optimize performance based on unique operational demands. Innovations in coating technologies continue to push the boundaries, offering eco-friendly options, smart coatings, and improved application techniques that cater to the evolving needs of users. Real-world case studies further illustrate the tangible benefits of selecting appropriate finishes and coatings, demonstrating enhanced tool performance, reduced maintenance, and increased user satisfaction.
As you consider the best finish and coating options for your impact sockets, assessing your specific needs, consulting with industry experts, and making informed decisions based on performance requirements and environmental conditions are crucial steps. By investing in high-quality finishes and coatings, you not only ensure the reliability and efficiency of your tools but also gain a competitive edge in the market with products that stand the test of time.
Embrace the advancements in finish and coating technologies to equip yourself with impact sockets that deliver exceptional performance and durability. Let the right finish and coating be the foundation of your tool’s success, providing you with the confidence and reliability needed to tackle any high-torque challenge with ease and precision.
FAQ Section
What is the best coating for preventing rust on impact sockets?
Chrome plating is one of the best coatings for preventing rust on impact sockets due to its excellent corrosion resistance and protective barrier against moisture and oxygen. Additionally, galvanization provides robust rust protection by applying a layer of zinc, which acts as a sacrificial anode to protect the underlying steel from rusting.
How does black oxide compare to chrome plating in terms of durability?
Black oxide is more cost-effective and provides basic corrosion resistance and friction reduction, making it suitable for less demanding environments. However, chrome plating offers superior durability and corrosion resistance, making it better suited for harsh environments and high-torque applications where enhanced protection is essential.
Can coated impact sockets withstand high torque applications?
Yes, coated impact sockets, especially those with finishes like nitriding or PVD coatings, are designed to withstand high torque applications. These coatings enhance surface hardness and wear resistance, ensuring that the sockets maintain their integrity and performance under intense use.
Are there eco-friendly coating options available for impact sockets?
Yes, there are eco-friendly coating options available, such as water-based paints and low-VOC finishes. These coatings offer comparable performance to traditional coatings while minimizing harmful emissions and reducing environmental impact, making them a sustainable choice for environmentally conscious users.
How often should I maintain the finish on my impact sockets?
Regular maintenance is recommended to preserve the finish on impact sockets. This includes wiping down the sockets after each use, using mild cleaners for thorough cleaning, ensuring they are thoroughly dried before storage, and applying light lubrication if necessary. Periodic inspections should be conducted to check for any signs of wear or damage to the coating.
What factors should I consider when choosing a coating for my impact sockets?
When choosing a coating for impact sockets, consider factors such as performance requirements (corrosion resistance, surface hardness, friction reduction), environmental conditions, budget constraints, aesthetic preferences, and maintenance requirements. Evaluating these factors will help you select the most suitable coating for your specific needs.
Do different coatings affect the weight of impact sockets?
Yes, different coatings can affect the weight of impact sockets. Coatings like galvanization and chrome plating add more weight compared to lighter options like polymer coatings. It’s important to consider the impact on tool balance and ease of use when selecting a coating, especially for applications requiring prolonged use.
How do coatings influence the grip and handling of impact sockets?
Coatings can enhance the grip and handling of impact sockets by providing smoother surfaces that reduce friction and prevent slippage. Some coatings, like polymer finishes, may offer additional texturing that improves grip, making the sockets easier to handle and reducing the risk of accidental drops or slips during use.
Can I customize the finish of my impact sockets for my brand?
Absolutely. Customizing the finish of impact sockets is a common practice for branding purposes. Manufacturers can apply unique colors, engravings, or specialized coatings that reflect your brand’s identity, making your tools easily recognizable and distinguishing them from competitors’ products.
What innovations are emerging in coating technologies for impact sockets?
Emerging innovations in coating technologies for impact sockets include smart coatings with integrated sensors for monitoring tool condition, eco-friendly coatings that reduce environmental impact, and advanced materials like nanostructured and composite coatings that offer enhanced durability and performance. Additionally, improved application techniques such as atomic layer deposition (ALD) and chemical vapor deposition (CVD) are enabling more precise and uniform coatings, further advancing the capabilities of impact sockets.