INTRODUCTION TO IMPACT SOCKETS
What Are Impact Sockets?
Why Performance Matters
Who Benefits From High-Performing Impact Sockets?
Impact sockets are specially designed tools engineered to handle the intense torque and vibration produced by impact wrenches and power tools. Unlike standard sockets, these heavy-duty variants feature thicker walls and robust materials that withstand punishing conditions. You might be wondering, what sets them apart beyond toughness? Their ability to maintain structural integrity under heavy load preserves the longevity of both the socket and the fastener. This reliability matters because broken tools waste time, stall projects, and risk safety. Everyone from seasoned automotive mechanics to at-home DIY enthusiasts benefits from having impact sockets that meet or exceed high-performance standards.
UNDERSTANDING THE CORE MATERIALS AND MANUFACTURING PROCESSES
Typical Materials Used in Impact Sockets
Heat Treatment and Hardening Processes
The Importance of Quality Control in Manufacturing
To understand why certain impact sockets perform better than others, it helps to know how they’re made. Many top-tier impact sockets use chromium-molybdenum (Cr-Mo) steel or chromium-vanadium (Cr-V) alloys. These blends offer a balanced combination of strength, flexibility, and resistance against wear. Here’s the deal, top manufacturers invest heavily in raw materials that meet precise chemical compositions. By doing so, they ensure consistent hardness and elasticity.
Beyond the alloy choice, the heat treatment process transforms raw steel into a tool capable of handling intense torque. Hardening methods like through-hardening or case-hardening optimize strength at the core or surface. Tempering refines the grain structure, preventing the socket from becoming brittle. Without proper heat treatment, even the best alloy can fail when placed under stress.
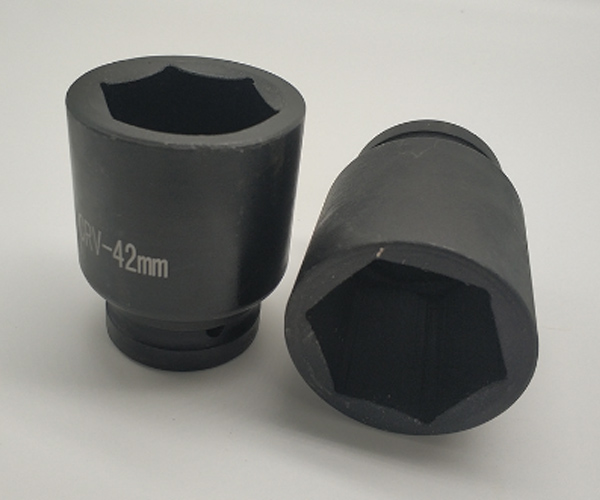
Quality control is crucial too. Reputable factories use stringent testing protocols, from hardness tests to dimensional inspections, ensuring each batch meets predetermined specifications. Guess what, reliable suppliers often hold certifications like ISO or adhere to ANSI and DIN standards. These measures confirm that every socket rolling off the production line remains uniform and dependable. When considering new suppliers, always inquire about their quality assurance standards and traceability of materials.
THE DIFFERENCE BETWEEN IMPACT SOCKETS AND STANDARD SOCKETS
Structural Differences
Material Strength and Hardness
Protecting Tools and Fasteners
Impact sockets differ from standard sockets in more ways than just appearance. A typical impact socket features thicker walls to absorb the energy delivered by high-torque impact tools, while standard sockets tend to be thinner and can crack under similar conditions. You might be wondering, what this thickness accomplishes? It spreads the load more evenly, reducing the risk of splitting or warping.
These specialized tools also come from tougher alloys. Standard sockets may use basic steel blends sufficient for hand torque, but impact versions rely on specially formulated alloys. Hardening and tempering yield surfaces that remain durable without becoming brittle. Here’s another angle, the result is a tool that flexes slightly under load rather than fracturing, saving you from sudden tool failures.
This reliability matters when protecting both the tool and the fastener. Ill-fitting or flimsy sockets can round off bolt heads or nuts, leading to frustrating extraction attempts and wasted time. Impact sockets fit snugly, grip securely, and channel torque effectively. Over time, this not only safeguards your equipment investment but also ensures that mechanical assemblies remain intact. By choosing the right impact socket, you enhance overall productivity and tool lifespan.
KEY PERFORMANCE FEATURES TO LOOK FOR
Torque Capacity and Load Resistance
Impact Resistance and Vibration Dampening
Surface Finish and Coating
When evaluating impact socket performance, focus on features that directly affect reliability and longevity. You might be thinking, “Which attributes matter most?” Start with torque capacity. High-quality impact sockets carry ratings that indicate their safe operating range. These ratings are more than just numbers; they represent the level of strain the tool can handle without cracking or deforming.
Impact resistance is also critical. Good sockets endure repeated hammering from impact wrenches, thanks to alloys that absorb shock without fracturing. Vibration dampening comes into play as well. With proper material selection and design, the socket handles the violent pounding, sparing your wrist and reducing long-term damage.
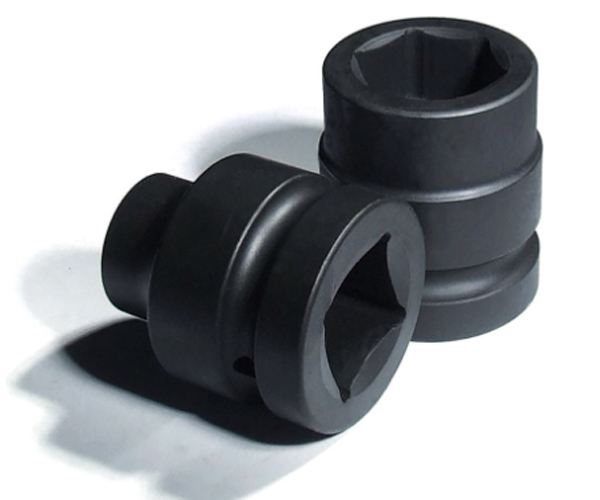
The surface finish and coating should not be overlooked. Black oxide or phosphate finishes help prevent corrosion and rust. Smooth finishes prevent micro-cracks or surface flaws that can compromise strength. Guess what, a well-coated socket lasts longer in harsh conditions and resists grease, grime, and moisture better.
By examining torque ratings, impact endurance, and protective finishes, you gauge whether a socket’s build quality aligns with your needs. Over time, investing in superior performance features translates to fewer replacements, safer working conditions, and more successful projects completed on time.
EVALUATING THE FIT AND COMPATIBILITY
Accuracy of Socket Sizing
Drive Size Compatibility
Achieving top performance hinges not only on a socket’s strength but also on how well it fits. You might be asking, why does fit matter so much? An improperly sized or poorly toleranced socket slips, rounds off fasteners, or causes erratic torque application. High-quality impact sockets maintain tight dimensional tolerances, ensuring every socket engages firmly with the intended bolt or nut.
Accuracy in sizing also means that the tool maintains consistent contact surfaces, reducing the likelihood of damage to both the socket and the fastener. This careful engineering plays a crucial role when you’re dealing with expensive machinery parts or automotive components. One slip can lead to catastrophic failures.
Drive size compatibility is another factor. Common drive sizes include 1/2″, 3/8″, and 3/4″. Matching your socket to the correct drive size ensures the impact wrench delivers force efficiently. Here’s another thing, using an oversized or undersized drive leads to wasted energy and uneven torque transfer. The result? Diminished performance and tool wear.
By carefully verifying that each socket’s sizing matches your applications, you protect your investment in both tools and machinery. Over time, fitting well with your setup boosts efficiency, prolongs tool life, and keeps projects running smoothly.
TESTING STANDARDS AND CERTIFICATIONS
Industry Standard Tests
Certified Markings and What They Mean
Third-Party Validation
Industry standards and certifications act as your guideposts in identifying trustworthy impact sockets. You might be wondering, which benchmarks matter most? Standards set by organizations like ISO, ANSI, or DIN outline testing methods and performance thresholds. These tests measure torque tolerance, hardness, and overall durability, ensuring consistent quality.
Certified markings stamped onto the socket’s surface often indicate compliance with such standards. Look for recognizable symbols, part numbers, or quality hallmarks. Guess what, these marks serve as shorthand for “This product passed rigorous scrutiny.” Without them, you risk investing in inferior tools that fail under stress.
Third-party validation adds another layer of confidence. When independent testing labs confirm a socket’s performance claims, you know it’s not just marketing hype. Reputable brands willingly share these test reports, reflecting their transparency and dedication to excellence. For buyers seeking reliable suppliers, verifying certifications and testing documents can prevent costly mistakes.
By factoring in industry standards and independent testing, you sidestep guesswork. Think of these benchmarks as your North Star—guiding you toward sockets that have proven their worth. Armed with certification knowledge, you make informed decisions, selecting tools that perform consistently in the field.
ASSESSING DURABILITY AND LONGEVITY
Signs of Wear and When to Replace
The Role of Regular Maintenance
Long-Term Cost Savings
Evaluating how an impact socket performs involves more than just initial specs; you must understand its durability and how long it lasts. Over time, even the toughest sockets can show signs of wear. You might be asking, how do I spot these signs? Look for cracks, chips, or visible deformations, especially near the drive end. If a socket no longer fits snugly or begins slipping, it might be time to retire it.
Regular maintenance extends the tool’s life. Cleaning sockets after each use removes debris that could induce corrosion or pitting. A light coat of oil prevents rust buildup, and proper storage in dry environments shields them from moisture. Here’s another angle, just a little care can add years to their service life.
Longevity directly translates into cost savings. While top-tier sockets might command a higher initial price, their ability to last longer without replacements compensates over time. Frequent replacements, tool downtime, and lost productivity harm your bottom line. Investing in quality from the start means you won’t constantly worry about sockets failing at critical moments.
By recognizing wear signs, practicing maintenance, and choosing durable tools, you ensure stable performance that supports efficiency and safety on every project.
ERGONOMICS AND USABILITY
Design Features That Enhance User Comfort
Weight Distribution and Balance
Reducing User Fatigue
While performance and durability often dominate the conversation, ergonomics matter just as much. You might be wondering, why does ergonomic design matter for impact sockets? Tools that handle intense torque must be comfortable to operate, especially during long hours. Good ergonomics reduce strain on wrists and arms, preventing injuries and fatigue.
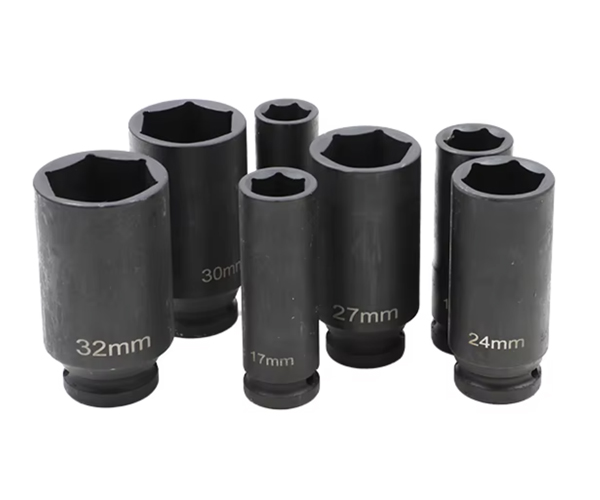
Design features such as knurled surfaces or contouring help users maintain a secure grip, even with oily gloves. A secure hold ensures accurate alignment and steady torque application. Balanced weight distribution also prevents the tool from feeling cumbersome. Here’s the deal, overly heavy sockets might appear robust, but they’ll quickly tire your hand. On the other hand, too light a socket may lack the mass needed to stabilize the application of torque.
By striking the right balance, top-notch socket manufacturers deliver tools that feel natural to use. When operators are comfortable, they apply torque more consistently, reduce mistakes, and maintain productivity. Over time, improved ergonomics translates into fewer injuries, less downtime, and smoother workflows. From automotive repair to production lines, ergonomic impact sockets help keep the workforce healthier and more efficient day after day.
CUSTOMIZATION AND OEM CAPABILITIES
Why Consider Custom or OEM Sockets?
Branding and Specialty Requirements
Working With Manufacturers on Custom Specs
Not all projects align with off-the-shelf solutions. You might be thinking, “What if I need something unique?” That’s where custom and OEM capabilities step in. Some manufacturers offer tailored alloys, specialized finishes, or drive sizes that cater to niche applications. Need a socket for a high-temperature environment or a specialized industrial fastener? OEM services can make that a reality.
Branding opportunities also come into play. Adding your company logo, color-coding sets for easy identification, or incorporating special packaging can turn an ordinary socket into a signature product. Here’s another thing, these small customizations help differentiate your brand, fostering loyalty among customers who appreciate attention to detail.
Communicating with manufacturers about custom specs requires clarity and patience. Provide detailed requirements, including torque ratings, material preferences, and performance goals. Reputable OEM partners will advise on feasibility and recommend adjustments. Through open dialogue, you ensure the final product matches expectations perfectly.
By embracing customization, you create tools aligned precisely with your needs. This not only solves performance challenges but also offers a marketing advantage. Custom impact sockets reflect your brand’s values and craftsmanship, making your offerings stand out amid the competition.
COMPARING DIFFERENT BRANDS AND SUPPLIERS
What Sets Reputable Brands Apart?
Price vs. Quality
Conducting Supplier Assessments
With so many options available, evaluating impact socket suppliers can feel overwhelming. You might be wondering, what separates a reputable brand from a lackluster one? Trusted names invest in consistent quality control, openly share test data, and stand behind their products with warranties. They also have solid track records and positive customer feedback.
While price is a key consideration, never let it overshadow quality. Low-cost sockets may tempt buyers on tight budgets, but they often compromise on materials or workmanship. Guess what, spending slightly more upfront for a reputable brand can save money and headaches later. A reliable socket reduces failures, downtime, and maintenance costs, boosting long-term return on investment.
Supplier assessments help narrow the field. Ask for references and test reports. Inquire about lead times, communication responsiveness, and their willingness to accommodate custom requests. If possible, visit factory sites or request factory tour videos to see their operations firsthand. Observing their processes validates claims of quality assurance and ethical sourcing.
By comparing brands, weighing price against quality, and conducting thorough supplier assessments, you establish confidence in your decision. Ultimately, choosing a trustworthy partner leads to smoother operations, higher efficiency, and better outcomes.
COMMON MISCONCEPTIONS ABOUT IMPACT SOCKETS
Myth: More Expensive Means Better
Myth: Any Steel Alloy Is Good Enough
Myth: All Finishes Are the Same
Despite widespread information, misconceptions persist around impact sockets. You might be wondering, do higher prices always guarantee superior quality? Price can reflect research, materials, and certifications, but not always. Some lesser-known brands deliver exceptional performance at fair costs. Judge sockets by tangible factors—test results, certifications, and real-world feedback—not just price tags.
Another misconception involves the assumption that any steel alloy suffices. In reality, different alloys exhibit distinct hardness, toughness, and corrosion resistance. Here’s another angle, selecting the right alloy matters. High-grade materials stand up better under relentless hammering, while inferior metals might fail prematurely.
Lastly, finishes are not all equal. Some coatings merely look good while offering minimal protection, while advanced finishes resist rust, reduce friction, and enhance tool longevity. Believing all finishes behave identically can lead to choosing subpar coatings that compromise durability.
By challenging these myths, you can make more informed decisions. Instead of relying on price alone, evaluate performance criteria. Instead of assuming all alloys or finishes perform equally, consider the science and testing behind them. Dispel misconceptions and you’ll find impact sockets that truly match your requirements.
PRACTICAL TIPS FOR HANDS-ON EVALUATION
Field Testing Methods
Visual Inspection Checklist
Torque Testing and Comparisons
While technical specs and certifications guide your choice, nothing beats hands-on evaluation. You might be thinking, how do I test these sockets myself? Start with field testing. Use them on actual jobs, applying varying levels of torque to see how they respond. Observe if the socket maintains its shape and if the fasteners remain intact. Real-world trials reveal subtle nuances overlooked by data sheets.
A visual inspection also helps. Check for cracks, chipped edges, or uneven finishes. A clean, uniform appearance often indicates careful manufacturing. Here’s the deal, a meticulous glance helps catch early signs of potential failures before they become costly problems.
Torque testing provides another layer of insight. Compare sockets by applying consistent torque with calibrated tools. Monitor if any begin to slip or deform at lower-than-expected thresholds. This provides quantitative data you can trust.
By combining field tests, visual checks, and torque comparisons, you build a more complete picture of a socket’s performance. This hands-on approach confirms whether the specs align with reality. Over time, these practical evaluations help refine your selection process, ensuring every investment in impact sockets brings tangible value to your projects.
MAINTENANCE AND CARE FOR PROLONGED PERFORMANCE
Proper Cleaning and Storage
Routine Inspections and Replacements
Extending Lifespan Through Correct Usage
Once you’ve selected quality impact sockets, proper care ensures they keep performing. You might be wondering, how do I maintain them effectively? Begin by cleaning sockets after every use. Wipe away grease, dirt, or metal shavings before they settle into crevices. Removing contaminants prevents corrosion and ensures a smooth mating surface.
Storage also matters. Keep sockets dry and in designated storage racks or trays. Organized storage makes selecting the correct socket size easier and protects them from banging against each other. Here’s another thing, a bit of preventive maintenance—like adding a thin layer of protective oil—reduces rust over time.
Conduct periodic inspections. If you spot cracks, distortions, or signs of wear, remove that socket from service to avoid catastrophic failure. Replacing sockets at the right time prevents accidents and prolongs the life of your entire tool set.
Finally, use your sockets correctly. Avoid pushing them beyond their rated torque capacity or using them with underpowered tools. Gentle handling and adherence to guidelines ensure they deliver reliable performance year after year. With the right balance of care, you enjoy longer service life, better results, and greater peace of mind.
CASE STUDIES AND REAL-WORLD EXAMPLES
Success Stories from Automotive Repair Shops
Industrial Maintenance Scenarios
Before-and-After Comparisons
Nothing illustrates the importance of evaluating impact socket performance better than real-world examples. You might be thinking, how do professionals benefit? Take an automotive repair shop that invests in premium impact sockets. Mechanics find tasks easier, bolts come off smoothly, and downtime decreases. In time, customer satisfaction rises because jobs finish faster, vehicles leave on schedule, and no one complains about broken tools.
Industrial maintenance crews rely on robust sockets too. Imagine a manufacturing plant performing routine equipment overhauls. Cheap, substandard sockets strip critical fasteners and cause delays. Switching to higher-grade options solves these headaches. Here’s another deal, reduced breakdowns translate to fewer expensive shutdowns, improving the plant’s bottom line.
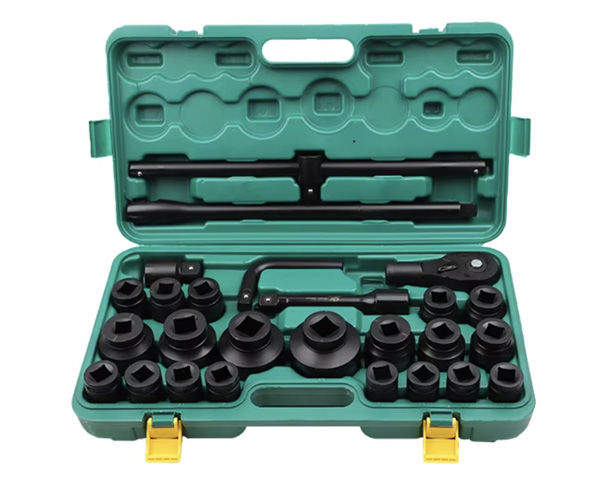
Before-and-after comparisons highlight tangible differences. Shops that once struggled with rounding bolts or damaged sockets find relief after upgrading. With better torque capacity, improved finishes, and certified quality, their workflow becomes smoother. The result? Savings in time, money, and frustration.
By studying these stories, you see how impact socket evaluations directly impact productivity and reliability. Real users validate the theory: choosing well-made tools sets you on a path toward sustained success, better customer experiences, and long-term growth.
CONCLUSION AND FINAL RECOMMENDATIONS
Evaluating impact socket performance involves considering materials, design, testing standards, and real-world feedback. By focusing on torque capacity, fit, and finish, you ensure the right tool for the job. You might be asking, what now? Seek reputable suppliers who back their products with certifications and transparent testing. Careful maintenance and proper usage further extend tool life. Over time, this approach delivers consistent results, fewer headaches, and better outcomes. Remember, each decision shapes your toolbox’s reliability. Invest wisely, choose quality, and enjoy smoother, safer, and more efficient work environments. Your success depends on it.
FAQ
Q: How do I verify if my impact socket meets industry standards?
A: Look for markings indicating ANSI or ISO compliance. Reputable suppliers provide test reports or certifications.
Q: Can I use standard sockets with an impact wrench?
A: It’s not recommended. Impact sockets are specifically designed to handle the intense torque and vibrations from impact tools.
Q: How often should I replace my impact sockets?
A: Inspect sockets regularly. If you notice signs of wear, cracks, or deformation, replace them immediately.
Q: Are custom finishes worth considering?
A: Yes, custom finishes can enhance durability, corrosion resistance, and even help with brand differentiation.
Q: Do I need expensive sockets to ensure quality?
A: Not necessarily. Evaluate specs, certifications, and user feedback. Some reasonably priced brands offer exceptional quality.