In today’s competitive business world, choosing the right manufacturing partner is crucial for success. For businesses in need of high-quality hand tools, a custom hand tools factory provides an efficient solution. By partnering with such a factory, businesses can get tailored tools that meet their specific needs, ensuring their products are built to last and stand out in the market. This article delves into the advantages, processes, and benefits of working with a custom hand tools factory, particularly focusing on OEM solutions that offer personalized manufacturing.
1. What Are Hand Tools Factories?
Let’s begin with the basics. What exactly is a hand tools factory? A hand tools factory is a specialized manufacturing facility dedicated to producing a wide range of hand tools. These tools can vary from basic household products to more specialized tools for professionals in fields like automotive repair, construction, or woodworking. But here’s the kicker—many factories also offer customized solutions, allowing businesses to create tools that reflect their brand’s identity.
A typical hand tools factory uses a variety of machines and skilled labor to produce high-quality tools. These tools are made using durable materials, ensuring they meet industry standards and the needs of both professionals and DIY enthusiasts. The key to understanding a hand tools factory is recognizing that it’s not just about mass production. Customization plays a significant role in the production process. So, businesses that require unique, branded tools find great value in working with these factories.
Another important factor is the factory’s ability to scale production according to demand. Whether you need small batches of specialized tools or large orders for a retail launch, hand tools factories can adjust their processes to meet your specifications. Let’s break down some of the essential elements of a hand tools factory’s operations and its importance in the market.
Feature | Description | Benefits |
---|---|---|
Types of Tools | Includes DIY tools, automotive tools, woodworking tools, etc. | Versatility and customization |
Production Capacity | Varies from small to large scale manufacturing | Flexibility for different business needs |
Materials Used | High-quality metals, plastics, and composites | Ensures durability and performance |
Customization Options | OEM solutions for branding, design, and function | Tailored to specific brand needs |
2. Why Should You Choose an OEM Hand Tools Factory?
What makes an OEM hand tools factory stand out from regular manufacturing partners? OEM (Original Equipment Manufacturer) factories focus on creating tools based on the buyer’s design specifications. That means they can produce hand tools that not only meet quality standards but also reflect the unique needs of your business. Ready for the good part? OEM manufacturing offers immense flexibility, especially for businesses looking to strengthen their brand identity.
OEM factories allow companies to create custom-designed tools, adding specific features that align with their target market’s needs. For example, a DIY tool brand might want to include ergonomic handles or a unique color scheme that sets their tools apart from competitors. By working with an OEM hand tools factory, you ensure that every tool that comes off the production line is tailored to your exact specifications. This is where it gets interesting—the ability to scale this process for larger orders makes it an ideal option for companies looking to enter retail spaces with a product that’s all their own.
What’s more, OEM solutions often include detailed support throughout the manufacturing process. This includes everything from design consultation to post-production quality checks. The goal is to make sure that the final product not only meets the business’s needs but also impresses consumers. Let’s take a closer look at some of the benefits of choosing an OEM hand tools factory.
Benefit | Description | Example Use Case |
---|---|---|
Customization | Tailor the design, function, and branding of the tools | Unique colors, designs, ergonomics |
Expertise | Access to specialized knowledge and design input | Professional-grade tools for automotive repair |
Scalability | Easily scale production for different volumes | Launching a new product in retail stores |
Cost Efficiency | Competitive pricing with optimized production costs | Reducing costs with high-volume production |
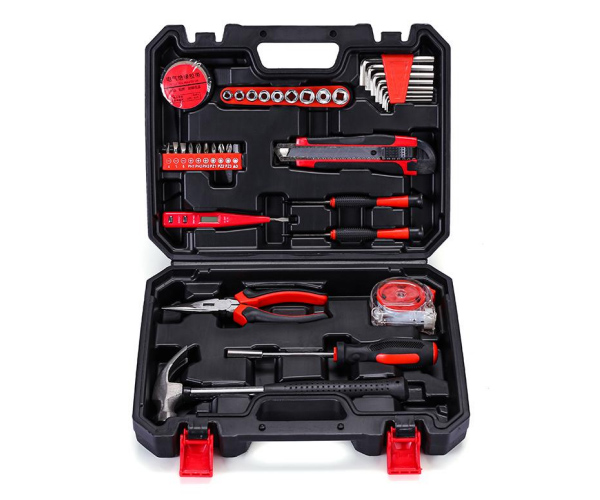
3. How Does a Hand Tools Factory Operate?
Now that we’ve covered the basics, how exactly does a hand tools factory operate? The process begins with sourcing raw materials, such as high-grade metals, composites, and plastics. These materials are then molded, cut, and shaped using a variety of machines, including CNC (Computer Numerical Control) machines, injection molding, and stamping presses. But here’s the kicker—automation plays a huge role in increasing efficiency while ensuring high quality.
The next step in the operation is assembly. After the parts are produced, they are meticulously assembled by skilled workers. This stage can involve adding ergonomic handles, installing mechanisms for adjustable features, or affixing safety components. Quality control tests are conducted throughout each stage of the process to ensure the tools meet the factory’s high standards. What’s the real story? The entire process involves multiple layers of checks, from material quality to final assembly, all aimed at delivering tools that will stand the test of time.
Additionally, the final products undergo rigorous testing. This can include stress tests to ensure durability, precision testing for functionality, and safety assessments to comply with industry standards. The goal is to ensure that every tool produced is not only functional but also safe for the user. Let’s now look at how these processes come together to deliver high-quality, reliable hand tools.
Step | Description | Importance |
---|---|---|
Material Sourcing | High-quality raw materials are sourced from trusted suppliers | Ensures durability and performance |
Manufacturing | Tools are made using precision equipment and skilled labor | Guarantees high-quality products |
Assembly | Final assembly of all parts and components | Ensures tool functionality and safety |
Quality Control | Comprehensive testing for durability and safety | Confirms compliance with standards |
4. What Types of Hand Tools Can Be Manufactured by a Factory?
Wondering about the variety of hand tools a factory can produce? The types of tools produced by a hand tools factory are incredibly diverse. Whether you need general hand tools, specialized tools, or branded tools, the factory can manufacture products suited for any need. Ready for the good part? Factories can produce anything from screwdrivers and pliers to hammers, saws, and wrenches, making them a one-stop solution for many businesses.
Customization is where the factory really shines. Tools can be designed for specific tasks, such as automotive repair, home improvement, or woodworking. This allows businesses to offer specialized products that cater to a niche market. For instance, a woodworking tool manufacturer may want to produce chisels with specially designed handles for enhanced grip. Alternatively, a DIY brand might need compact, multi-functional tools for space-saving storage. This is where the customization and expertise of the hand tools factory come into play, ensuring that each tool is crafted to meet the exact requirements.
The possibilities for custom hand tools are virtually endless. Whether you need standard hand tools with a specific brand or entirely new tools designed for a unique application, a factory has the capability to bring your ideas to life. Let’s dive deeper into some of the types of tools that hand tools factories specialize in producing.
Type of Tool | Description | Examples |
---|---|---|
General Hand Tools | Basic tools used for a variety of household and DIY tasks | Hammers, screwdrivers, pliers |
Specialized Tools | Tools designed for specific trades or applications | Automotive repair tools, woodworking tools |
Custom Tools | Tools designed to meet specific business or branding needs | Branded tools, unique designs |
Multi-functional Tools | Tools designed for versatility and space-saving | Compact tool sets, portable kits |
5. How Can a Custom Hand Tools Factory Benefit Your Brand?
What’s the real advantage of working with a custom hand tools factory? The biggest benefit is the ability to produce hand tools that are specifically tailored to your brand. Imagine having a set of tools that not only perform exceptionally but also carry your unique branding and design. Ready for the good part? Custom tools enhance your brand’s identity, giving your customers something special that can’t be found elsewhere.
The customization process goes beyond just design. It also involves functionality. You can work closely with the factory to develop tools that meet the exact needs of your target market. Whether you’re designing a tool for professionals or DIY enthusiasts, the factory can modify the shape, size, and features to match the intended use. For example, if you’re launching a tool set for professionals, you may want to incorporate features like non-slip grips, higher durability, or unique tool materials to set your brand apart from the competition. This is where it gets interesting—the ability to fully control the design and functionality of your products is a key differentiator in the market.
Furthermore, custom hand tools can be used for marketing purposes. For businesses that want to make a strong impression, customized tools can be given as promotional items or sold as exclusive sets. Not only does this attract customers, but it also strengthens brand loyalty. Let’s break down the advantages of custom hand tools and how they can elevate your brand.
Advantage | Description | Example Use Case |
---|---|---|
Brand Differentiation | Customized tools set your brand apart from competitors | Unique designs and features |
Customer Engagement | Personalized tools improve customer loyalty | Exclusive promotional items |
Market Positioning | Custom tools allow you to target niche markets effectively | Tools tailored to specific industries or applications |
Competitive Advantage | Custom tools give you an edge in a crowded marketplace | High-quality, unique products |
6. What Are the Benefits of Working With an Experienced Hand Tools Factory?
So, why should you choose to work with an experienced hand tools factory? The benefits are clear. Experienced manufacturers have years of knowledge and skill, which translate into better quality products and smoother operations. But here’s the kicker—having an experienced factory partner means you’ll have access to the latest technology, improved production techniques, and a more efficient workflow.
An experienced hand tools factory knows exactly how to handle all aspects of production. From sourcing the best materials to ensuring precise production processes, they know what it takes to create a durable, reliable tool. They’ve also developed relationships with suppliers and vendors, which can lead to better pricing and faster turnaround times. What’s the real story? When you work with a factory that has extensive experience, you benefit from all these advantages, reducing risks and increasing the chances of success.
What sets an experienced factory apart is not just their ability to make tools, but their ability to understand your specific needs and offer solutions that match. They can guide you through the customization process and help you make informed decisions about design and functionality. This ensures that the final product aligns with your brand’s identity and meets the requirements of your target audience. Let’s explore some of the key benefits of working with a seasoned hand tools factory.
Benefit | Description | Example Use Case |
---|---|---|
Industry Expertise | Knowledge of industry standards, trends, and regulations | Crafting tools that meet regulatory standards |
Efficient Production | Streamlined processes and faster lead times | Quick turnaround for large orders |
Established Supplier Network | Reliable sources for quality materials and components | Better pricing and material consistency |
Innovation and Technology | Ability to incorporate the latest technology into manufacturing | Producing high-tech, ergonomic tools |
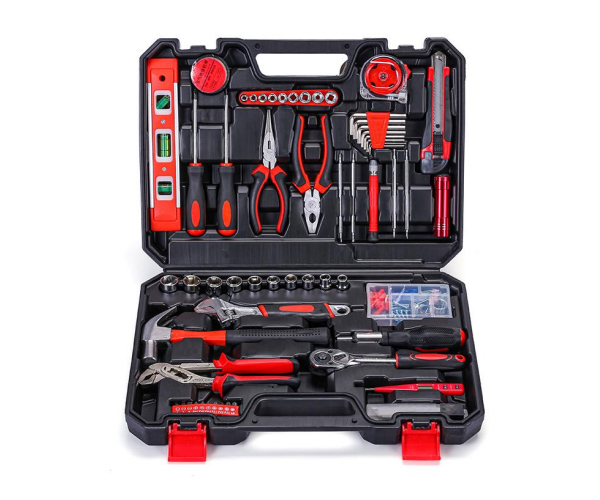
7. How Do Hand Tools Factories Ensure Product Quality?
When you purchase hand tools from a factory, you want to know that they will stand the test of time. Here’s where quality control becomes crucial. How do hand tools factories ensure that the products they produce are of the highest quality? The answer lies in their rigorous quality control systems. These systems ensure that each tool meets the specifications, performs optimally, and is safe to use. Ready for the good part? Factories use a combination of automated testing and manual inspections to verify quality at every stage of production.
Quality control begins with sourcing raw materials. Factories only use high-grade materials, ensuring that each tool is built to last. After the raw materials are processed and shaped into tools, they undergo a series of tests. These tests include strength testing, durability assessments, and functionality checks. Factories also perform final inspections on every batch before shipping out the products, ensuring they meet the required standards. But here’s the kicker—factories often work with independent third-party testers to verify the quality of their products, giving you added peace of mind.
What’s the real story? Quality control isn’t just about meeting standards; it’s about exceeding them. By working with a hand tools factory that prioritizes quality at every step, you can be sure that your tools will meet the highest expectations. Let’s dive deeper into how quality control works within a hand tools factory.
Quality Control Stage | Description | Importance |
---|---|---|
Material Selection | High-quality raw materials are selected based on durability and functionality | Ensures product longevity and strength |
In-Process Inspections | Continuous monitoring of tools during manufacturing | Prevents defects and ensures consistency |
Performance Testing | Tools undergo stress, durability, and functionality tests | Ensures tools perform as expected |
Final Inspections | Final checks before shipment to confirm compliance with standards | Guarantees product quality and safety |
8. What Is the Role of Innovation in Hand Tools Manufacturing?
When it comes to hand tools manufacturing, innovation is key to staying competitive. So, how does innovation impact hand tools production? The role of innovation is multifaceted, from introducing new designs to incorporating cutting-edge materials and technologies. But here’s the kicker—innovation in tool design not only enhances usability but also improves safety and performance.
Innovative hand tools are more than just new designs; they often feature advancements in ergonomics, durability, and functionality. For instance, the use of lightweight materials like carbon fiber or high-strength composites has allowed manufacturers to create tools that are both sturdy and easy to use. What’s the real story? Innovation is at the heart of creating tools that meet modern needs, whether that’s reducing hand strain, enhancing precision, or improving safety features.
As the market for hand tools evolves, manufacturers continue to push the boundaries of design. Tools are getting smarter with the integration of technology, such as built-in sensors to measure torque or Bluetooth connectivity to sync with mobile apps. This is where it gets interesting—the integration of digital technology is revolutionizing the way we use hand tools. Let’s explore how innovation is shaping the future of hand tools manufacturing.
Innovation Focus | Description | Example Use Case |
---|---|---|
Ergonomics | Design changes to reduce strain and improve comfort | Tools with padded, non-slip handles |
Materials | The use of new, lightweight, and durable materials | Carbon fiber drills and wrenches |
Digital Integration | Incorporating smart technologies in tools | Bluetooth-enabled torque wrenches |
Safety Features | Adding advanced safety mechanisms to tools | Anti-slip handles and safety locks |
9. How to Choose the Right Hand Tools Factory for Your Business?
Choosing the right hand tools factory can make all the difference in your business’s success. But how do you find the best partner? Ready for the good part? The right factory can help you meet your business goals, whether you need to produce custom tools, streamline production, or ensure high quality.
Start by evaluating the factory’s reputation and experience. Look for a factory that specializes in the types of hand tools you need and has a proven track record of delivering high-quality products. What’s the real story? Working with a factory that understands your industry’s demands and your target market’s needs will set you up for success.
Next, consider the factory’s production capabilities. Do they have the equipment and workforce to scale with your needs? Can they handle large orders or provide the flexibility for smaller, custom runs? And don’t forget to evaluate their communication skills—working with a factory that’s responsive and transparent will make the entire process easier and more efficient. Let’s break down some of the key factors to consider when choosing the right hand tools factory for your business.
Factor | Description | Why It Matters |
---|---|---|
Experience | How long the factory has been in the hand tools manufacturing industry | Expertise and proven track record |
Capabilities | The ability to handle large or small orders, and offer customization | Flexibility and scalability |
Reputation | Customer reviews, case studies, and certifications | Trustworthiness and reliability |
Communication | Responsiveness and clarity in dealing with business requirements | Smooth collaboration and efficient processes |
10. What Are the Common Challenges in Hand Tools Manufacturing?
Let’s face it—no industry is without its challenges. What are the common hurdles faced in hand tools manufacturing? Ready for the good part? Most challenges can be mitigated with the right processes and partnerships. However, understanding these obstacles is key to overcoming them.
One of the most common challenges is production delays. Whether it’s due to supply chain issues, labor shortages, or equipment malfunctions, delays can disrupt the entire manufacturing timeline. What’s the real story? It’s essential to work with a factory that has contingency plans in place and can handle unexpected setbacks.
Another challenge is quality assurance. With so many variables at play—from raw materials to manufacturing processes—ensuring consistency can be difficult. That’s why quality control is so important. Factories need to have strict testing protocols to catch any defects early on. Let’s explore some of the typical challenges in hand tools manufacturing and how they can be addressed.
Challenge | Description | Solution |
---|---|---|
Production Delays | Delays caused by supply chain issues or manufacturing setbacks | Strong contingency plans and efficient logistics |
Quality Assurance | Ensuring consistency and reliability in the final product | Rigorous testing and inspections |
Labor Shortages | Shortage of skilled labor impacting production timelines | Investment in training and automation |
Supply Chain Issues | Disruptions in material supply affecting production schedules | Diversifying suppliers and inventory management |
11. How Can a Hand Tools Factory Support Your Business Growth?
When you partner with a hand tools factory, you’re not just getting products—you’re gaining a partner in your business growth. So, how does a hand tools factory support your growth? The right factory helps scale production, reduce costs, and improve product offerings, all of which contribute to the success of your business.
A reliable factory ensures that you can meet demand as your business grows. Whether you’re expanding into new markets or launching new products, your factory should be able to keep up with increased production needs. Ready for the good part? A strategic partnership with a hand tools factory allows you to focus on marketing, sales, and other aspects of growth while they handle production.
Additionally, a factory that offers customization gives you the opportunity to introduce new products that align with changing market trends. This can open up new revenue streams and help you stay ahead of the competition. Let’s take a closer look at how a hand tools factory supports your business growth.
Growth Support | Description | How It Helps Business Growth |
---|---|---|
Scalable Production | Ability to increase production capacity based on demand | Meets growing market demand |
Customization | Tailored solutions for new product lines | Keeps your product offering fresh and relevant |
Cost Efficiency | Optimized manufacturing processes to reduce costs | Increases profitability |
Product Innovation | Ability to develop innovative products based on market needs | Opens new revenue opportunities |
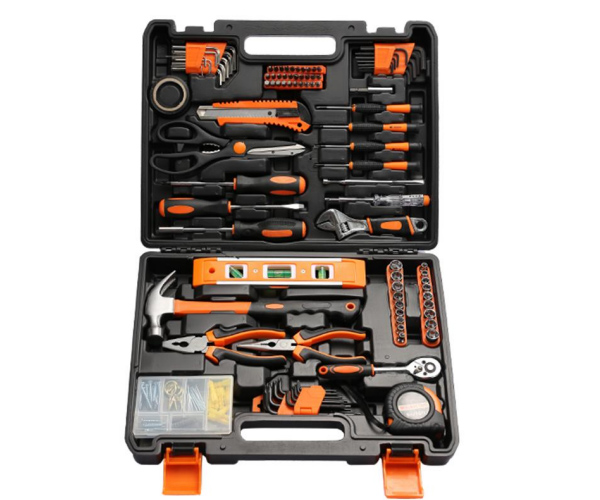
12. How Does Customization Improve the Appeal of Hand Tools for Consumers?
Customization is one of the key advantages of working with a hand tools factory. But how does customization enhance the appeal of hand tools? Ready for the good part? Customization allows businesses to create tools that are perfectly aligned with the needs of their target audience, making them more desirable to consumers.
Consumers today want products that cater to their specific needs. Whether it’s the design, size, or function of the tool, offering a customized product allows businesses to tap into niche markets. What’s the real story? Custom hand tools give businesses the ability to stand out in a crowded market and create products that consumers are more likely to purchase.
Let’s explore how customization helps increase the appeal of hand tools and why it matters for your business. Customization allows you to create tools that solve specific problems or offer features that competitors’ tools lack. For instance, a tool designed with a unique grip for comfort or a multi-functional feature that increases versatility will appeal to consumers looking for innovative solutions. Let’s look at the impact of customization on hand tools in more detail.
Customization Benefit | Description | Example Use Case |
---|---|---|
Unique Designs | Offering tools with distinctive designs or features | Tools with ergonomic handles or unique colors |
Functionality | Tailoring tools to perform specific tasks or provide extra features | Multi-purpose tools for home improvement |
Market Differentiation | Creating tools that are different from what competitors offer | Niche tools for specific industries |
Consumer Loyalty | Custom tools that cater to consumer preferences boost brand loyalty | Exclusive sets or promotional tools |
13. What Are the Costs Involved in Working With a Hand Tools Factory?
When it comes to working with a hand tools factory, cost is always a consideration. So, what are the costs involved in manufacturing hand tools? Ready for the good part? The cost of production varies depending on several factors, including the type of tools, materials, and the level of customization required.
The initial setup cost can be higher if you’re designing custom tools, especially if you need specialized machinery or materials. However, as you scale production, the cost per unit typically decreases, making it more cost-effective in the long run. What’s the real story? Working with a hand tools factory often results in a lower cost per tool when compared to in-house production, especially if you’re making large volumes.
Let’s break down the costs involved in working with a hand tools factory, from material sourcing to production. We’ll also look at how long-term relationships with manufacturers can reduce costs over time.
Cost Component | Description | Impact on Overall Cost |
---|---|---|
Setup Costs | Initial costs to design and set up the production process | Higher upfront cost for custom designs |
Material Costs | Cost of raw materials used in tool production | Affects overall product cost |
Labor Costs | Wages for workers involved in production and assembly | Affects pricing per unit |
Production Volume | Cost per unit decreases with larger orders | Economies of scale reduce cost |
14. How Can You Build a Strong Relationship With Your Hand Tools Factory?
Building a strong relationship with your hand tools factory is essential for a successful partnership. So, how do you ensure a solid working relationship with your factory? Ready for the good part? Clear communication, mutual respect, and aligned goals are key to ensuring your relationship thrives.
Open communication is the foundation of any successful partnership. Discuss your requirements clearly, set expectations, and maintain a continuous dialogue throughout the manufacturing process. What’s the real story? Regular check-ins and updates will help prevent issues down the road and ensure that your needs are met.
Building trust is also crucial. Choose a factory that you can rely on to deliver quality products on time. Let’s take a look at some practical tips for fostering a strong relationship with your hand tools factory.
Relationship Building Tip | Description | How It Helps |
---|---|---|
Open Communication | Regular updates and transparent discussions | Prevents misunderstandings and delays |
Setting Expectations | Define clear goals, timelines, and requirements | Ensures both parties are aligned |
Trust Building | Foster trust by meeting deadlines and delivering quality products | Strengthens long-term collaboration |
Feedback and Improvement | Provide constructive feedback for better outcomes | Helps improve processes over time |
15. What Are the Future Trends in the Hand Tools Manufacturing Industry?
What does the future hold for the hand tools industry? Ready for the good part? Innovation is driving the industry forward, with new technologies and design philosophies emerging all the time. From automation to sustainable practices, the future of hand tools manufacturing is all about efficiency, quality, and meeting consumer demands.
Technologies like 3D printing and robotics are beginning to play a larger role in manufacturing, allowing for greater customization and faster production times. What’s the real story? The future of hand tools is not just about producing tools faster but about producing them smarter. Sustainable practices are also becoming more important, as consumers increasingly demand eco-friendly products. Let’s dive into some of the key trends shaping the future of the hand tools manufacturing industry.
Trend | Description | Future Implications |
---|---|---|
3D Printing | Use of 3D printing to create more customized, complex designs | Greater design flexibility |
Automation | Increasing reliance on automation for precision and speed | Faster production times and lower costs |
Sustainability | Focus on using eco-friendly materials and reducing waste | Increased demand for green products |
Smart Tools | Integration of smart technology in hand tools | Tools that improve user efficiency and safety |
FAQ Section
Q1: What is a hand tools factory?
A hand tools factory is a facility dedicated to producing a variety of hand tools, ranging from general household tools to specialized equipment for professionals.
Q2: How does OEM manufacturing work in hand tools factories?
OEM manufacturing involves designing and producing tools according to the buyer’s specifications, allowing businesses to create unique, branded products.
Q3: Why should I choose a custom hand tools factory for my brand?
Custom hand tools factories offer tailored solutions that enhance your brand’s identity and ensure the products meet your market’s needs.
Q4: How does a hand tools factory ensure the quality of its products?
A hand tools factory uses quality control systems, high-grade materials, and rigorous testing to ensure the durability and functionality of its products.
Q5: What are the benefits of partnering with an experienced hand tools factory?
Partnering with an experienced factory provides access to expertise, high-quality manufacturing, scalability, and custom solutions that support your brand’s growth.