Introduction
Indeed, color plays a surprisingly vital role in the world of impact sockets. For many professionals, black is what instantly comes to mind. That standard shade helps workers quickly identify a socket as suitable for intense torque. Impact sockets often endure heavy use in environments where reliability is everything. You might be wondering how color influences daily tasks. It boils down to corrosion resistance, easy organization, and brand distinction. Whether a mechanic or an industrial buyer, selecting sockets that meet quality expectations is paramount. In that regard, black finishes have become a universal symbol of durability and unwavering performance overall.
Typical Finish: Why Black Is the Standard
Dark finishes remain the most recognized trait of impact sockets, and black oxide or black phosphate coatings are common because they help fight corrosion while preserving structural integrity. The typical black coat also cuts down on glare from overhead lighting, which matters in auto shops where bright fluorescents shine. Many professionals prefer black finishes because they can spot an impact socket in their toolbox at a glance, as these coatings appear different from silver chrome sockets used for standard hand applications. Here’s the deal: black finishes originated from a practical mindset rather than just aesthetics. Early manufacturers realized that a dull black surface resists chipping and flaking, which is essential for a socket that endures punishing torque day after day. This deeper matte hue likewise hides minor scuff marks that inevitably appear when sockets are used with high-torque wrenches. The black color becomes a hallmark of reliability, letting operators know they can push a socket harder without risking cracks. Over time, brands have embraced black phosphate or black oxide finishes for both function and familiarity. It’s become so universal that workers often expect impact sockets to be black, reinforcing a sense of trust when they grab one for tough automotive or industrial tasks.
Manufacturing Process and How It Affects Color
Impact socket manufacturing typically begins with solid steel bars that undergo precise forging, where extreme pressure shapes them into durable cylinder forms. This process lays the groundwork for hardiness, since steel’s grain structure is compressed and refined. After forging, manufacturers proceed with heat treatment to increase tensile strength. You might be wondering how these stages link to color. The heat treatment process, which often involves quenching in oil or specialized solutions, can influence the final tone if specific coatings are applied afterward. Phosphate or oxide coatings adhere more effectively when the metal surface has been heated to exact temperatures, and that results in the typical black hue. During coating, the socket’s exterior is often dipped into a chemical bath that bonds permanently with the steel, giving it extra corrosion resistance and a consistent dark finish. This synergy of forging, heat treating, and surface finishing not only boosts the socket’s functional life but also cements its signature black look. Precise engineering steps, from the initial forging to the final surface application, can alter color intensity or sheen. For instance, a phosphate bath may yield a slightly matte finish, while an oxide-based process could produce a deeper or glossier black. The core idea remains consistent: color emerges as a byproduct of well-orchestrated engineering steps.
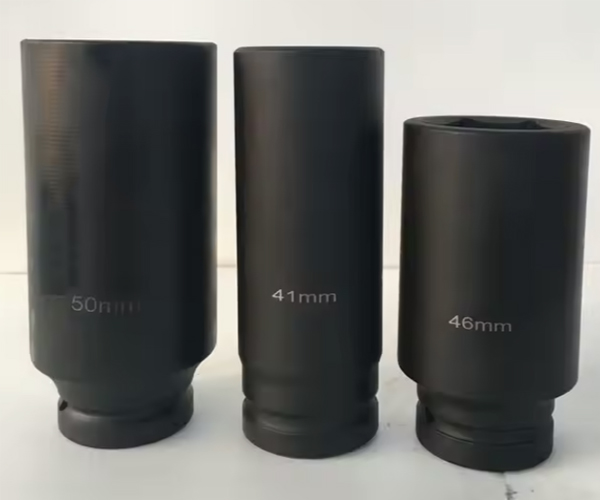
Practical Benefits of Black Impact Sockets
Professionals choose black impact sockets for more than just aesthetics. That dark finish provides a layer of corrosion protection, an especially big deal in garages or industrial plants where moisture, cleaning chemicals, and grease abound. You might be wondering if black finishes actually extend socket life. The answer is often yes, thanks to coating methods that create a protective barrier against rust or abrasion. These sockets also tend to show wear more gracefully. Scratches blend into the black surface rather than revealing glaring silver areas, which is handy when tools see constant heavy use. Another subtle perk is their low-glare appearance under bright shop lights. Chrome sockets can reflect overhead bulbs into your eyes, but black impact versions avoid that issue. Workflow efficiency improves as well because many mechanics rely on quick identification: black typically signals “safe for impact guns,” while chrome signals “manual use only.” As a result, black becomes a visual shorthand to prevent tool mix-ups or hazardous misapplications. Beyond these advantages, the finish often has a slightly textured feel that can help with grip, especially if your hands are oily or sweaty. In essence, black impact sockets marry functionality with a durable appearance that stands up to the harsh realities of automotive and industrial environments.
Common Variations: Different Shades of Black
Although black stands out as the standard, not every impact socket sports the identical hue. Some appear matte with a softer sheen, while others feature a glossy, deeper black tone. You might be wondering why the color differs from brand to brand or even batch to batch. Coating processes can vary in temperature, chemical composition, and application technique. Phosphate coatings may produce a gritty, more matte result, whereas oxide finishes might yield a smoother, darker shade. Additionally, certain manufacturers tweak their coatings with proprietary formulas aimed at optimizing rust resistance or hardness. These modifications can cause subtle color shifts. Over time, usage also affects how the finish looks. In a busy shop, abrasive conditions may polish certain parts of the socket, brightening the surface. Alternatively, repeated exposure to oil, brake fluid, or cleaning agents can dull the finish. Sometimes, a black finish can appear slightly grayish under intense light if the surface has been scuffed repeatedly. Such variations don’t necessarily indicate a dip in overall quality, but they reflect the interplay between specific finishing methods and day-to-day wear. Ultimately, whether a socket leans toward a charcoal gray or a jet-black shine, it still belongs to the classic category of black impact tools engineered for high-torque tasks.
Other Colors on the Market (Color-Coded Impact Sockets)
Although black is widespread, color-coding has found its place among impact socket lines. Manufacturers sometimes offer sets in bright hues like red, blue, or yellow, each representing a particular socket size. You might be wondering if color-coded impact sockets match black’s durability. Often, these colored finishes involve an additional coating layer or an anodized exterior that maintains good resistance to wear. The biggest appeal lies in swift identification. Mechanics who juggle multiple sizes daily appreciate instantly grabbing the correct socket without squinting at etched labels. Color-coded systems can streamline workflow, especially in large-scale automotive or industrial environments. However, bright coatings can wear away with repeated use, exposing the underlying metal and eroding the color-coding advantage. Another consideration is compatibility with intense torque. While many color-coded sets remain fully impact-rated, verifying manufacturer claims is wise. On the plus side, color-coded sockets can reduce confusion about standard versus metric sizes. When every size has a unique color, cross-contamination or misplacement becomes less likely. In a mixed environment, black remains the typical color, but color-coding is gaining ground for those who want a more organized approach. Ultimately, color-coded impact sockets function similarly to black ones, provided they’re built to handle the same forces and tested against the same performance metrics.
The Difference Between Impact and Chrome Sockets
Some tool owners occasionally confuse chrome sockets with impact versions, but these two serve very different purposes. Chrome sockets usually shine with a polished silver appearance, and they’re commonly found in DIY or standard hand tool kits. Their plating suits lighter torque tasks, so they can handle routine bolts and nuts. Here’s another tidbit: chrome sockets typically feature thinner walls to allow easy fitment in tight spaces, which can be a liability when dealing with the violent hammering of impact tools. Impact sockets, on the other hand, rely on heavier construction, specialized heat treatments, and that hallmark black finish. This design accommodates powerful pneumatic or electric torque without fracturing. In fact, using a chrome socket on an impact gun can cause catastrophic splitting or dangerous shrapnel. People often ask if black is automatically a sign of higher strength. While black does represent an industry standard, what truly matters is the grade of steel, forging process, and heat-treat consistency. The torque rating is higher for impact versions, and their distinct color helps mechanics immediately see which socket belongs on an air gun or electric impact wrench. Ultimately, black impact sockets are built tough and safe for power tools, while chrome serves routine manual tasks requiring minimal torque.
How Color Aids in Tool Organization
Organization is crucial in busy workshops, and color helps mechanics or technicians quickly separate impact sockets from regular sockets. You might be wondering how that translates into daily efficiency. When sockets lie scattered in a drawer, one quick look at the dark surfaces reveals which ones can handle heavy torque. This reduces the likelihood of mixing up tools that could shatter if used incorrectly on high-powered impact guns. Color also extends beyond black. Some shops use a system that pairs colored trays or rails with black sockets, adding an extra layer of classification. Even within black-finished sets, users might rely on engraved size numbers or color-coded rings to further distinguish metrics from standard measurements. That layering of visual cues speeds up tool selection, preventing frustrating rummaging. In large operations, time is money, so streamlined organization fosters better productivity and fewer mistakes. Furthermore, distinct colors can also segment sockets by brand or torque rating. This approach helps multi-brand shops keep track of which sockets belong to which supplier or which rating best fits certain jobs. Ultimately, color plays a subtle but vital role in an environment where staff often rely on quick visual references. It’s a functional code that bolsters safety, cuts down on confusion, and keeps workflow steady.
Are There Specific Industry Standards for Impact Socket Color?
Color isn’t governed by a universal regulation that says all impact sockets must appear black. Still, black quickly emerged as the go-to choice, partly due to standard finishing practices. You might be wondering if official bodies like ANSI or ISO specify color requirements. These standards often address dimensions, material compositions, and performance criteria rather than strict color mandates. In other words, they focus on how well a socket can handle torque or how the drive end should fit an impact wrench. Since black phosphate or black oxide coatings have proven effective for corrosion resistance and identification, most manufacturers adopted them as an unofficial norm. Occasionally, specialized fields like aviation or petrochemical maintenance might request a more unique finish to meet internal color-coding policies. However, those preferences generally don’t rise to the level of formal industry-wide standards. Customers who purchase in large volumes can sometimes request custom finishes, meaning black remains typical but not absolutely mandatory. In practice, you’ll rarely see professional-level impact sockets that aren’t black unless they’re part of a color-coded system. That’s because black coatings do more than look tough. They also help dissipate frictional heat and reduce glare. Ultimately, color choices remain a mix of tradition, practicality, and marketplace expectations rather than regulatory obligation.
Potential Coating Methods That Influence Color
The type of coating used on impact sockets greatly affects both appearance and performance. Phosphate coatings, for instance, generate that classic matte black tone while adding a protective layer against rust. You might be wondering if oxide coatings differ significantly. Oxide processes can produce a darker, sometimes shinier finish, and they often offer excellent corrosion protection as well. Manufacturers sometimes apply additional sealants or oils that enhance surface resilience, which can darken or lighten the color slightly. Beyond phosphate and oxide, some brands experiment with polymer-based or ceramic-based coatings that promise heightened scratch resistance. However, these specialized finishes tend to cost more. Paint-based options also exist but are less common for heavy-duty impact sockets, because repeated exposure to torque can chip paint. Another factor is coating thickness. A thicker film can influence how crisp the size markings appear or slightly alter the tool’s final weight. Thinner finishes might show wear quicker, yet they reduce the risk of dimension changes that hinder fitment. Each approach strives to balance corrosion defense, longevity, and consistent coloration. While black remains the frequent end result, the underlying method can yield subtle differences in shade, texture, and reflectivity. Ultimately, the chosen coating aims to complement heat treatment and forging processes, ensuring the socket can withstand punishing torque without sacrificing protective benefits.
Common Misconceptions About Impact Socket Colors
One widespread myth states that any black socket automatically qualifies as “impact-rated.” You might be wondering if that’s always true. Not every black-coated tool can handle the hammering force of an impact wrench. Some lower-quality manufacturers simply adopt a dark finish to appear professional, though the underlying steel and heat treatment might be subpar. Another misconception involves color-coded or chrome-like finishes that might lead folks to believe those sockets are weaker. In reality, some premium lines offer color-coded sets that are fully impact-capable. The real determinant is the steel grade, forging method, and specialized heat treatment. People also assume that black finishes never chip or fade, but daily use can erode even robust coatings, especially under harsh torque or repeated contact with metal edges. A different misunderstanding centers on black color as a sign of universal standardization. Actually, no official directive forces every manufacturer to produce black sockets. It’s merely a functional and historical preference in the industry. Some also believe black is only about aesthetics. In truth, black oxide or phosphate processes serve functional purposes such as corrosion control and reduced glare. Ultimately, verifying manufacturer specs and torque ratings remains more critical than color alone. Appearances can be misleading, so it’s vital to look deeper than just a dark surface.
Longevity and Wear: Does the Color Fade?
Impact sockets, by design, endure repeated heavy use under high torque, which can lead to normal wear on their coating. You might be wondering if black finishes fade quicker than more colorful coatings. In many cases, black oxide or phosphate treatments hold up remarkably well, especially if users store and maintain sockets properly. Over time, though, abrasive contact with bolts, wrenches, or other tools can cause gradual thinning of the surface layer. While the socket’s structural integrity won’t necessarily be compromised by minor scuffing, the coating might appear lighter or develop small shiny spots. Corrosive environments accelerate fading. Exposure to moisture, chemicals, and grime increases the likelihood of rust patches forming if the protective layer wears away. Regular cleaning and light oiling can slow this process, preserving the color for a longer period. Some mechanics appreciate the “battle-worn” look of well-used black sockets, believing it reflects the quality and frequency of work performed. However, brand new or rarely used sockets can keep their deep black finish for years. The important takeaway is that color fading doesn’t automatically equate to performance loss. Even if the black hue softens to a gunmetal gray, the tool can remain fully functional, provided it’s been maintained and built to robust impact specifications.
Specialty Impact Sockets: Are They Always Black?
Specialty impact sockets cater to unique tasks or industries, such as extra-deep sockets for industrial machinery or thin-walled versions for tight automotive spaces. You might be wondering if those specialized variants always stick to the black finish. In many cases, yes, because black coatings provide consistent corrosion resistance and a recognizable aesthetic that signals “impact-rated.” However, certain niche applications demand alternative coatings or custom finishes. For instance, some aerospace maintenance teams prefer color-coded sets for rapid size recognition in time-critical scenarios. In the oil and gas sector, companies might request extra corrosion protection that modifies the socket’s shade or even adds a partial topcoat. Such modifications serve a specific need rather than an industry-wide standard. Though black remains the dominant color, occasional outliers exist to meet specialized demands. Another factor is brand image. Some high-end tool manufacturers experiment with unique shades of black or a subdued gray for marketing distinct product lines. Either way, the underlying material—usually chrome molybdenum steel—and robust forging processes remain essential for maintaining the torque tolerance required of impact tools. Whether these sockets exhibit a classic black sheen, a slightly tinted finish, or a custom-coded color, they all aim to balance reliability and performance in harsh working conditions.
Practical Tips for Choosing an Impact Socket Based on Color
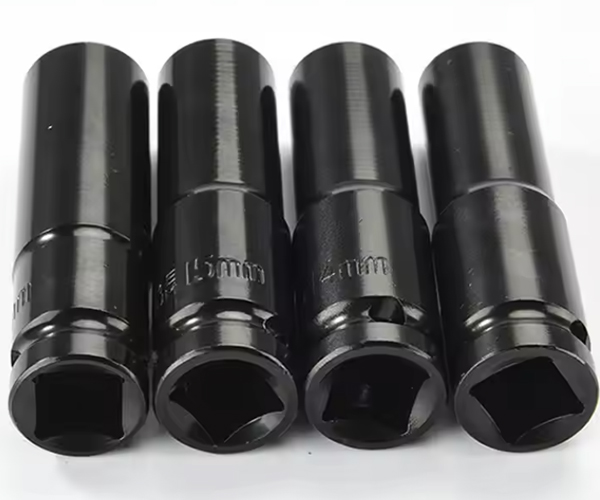
When shopping for impact sockets, many buyers gravitate to black because it’s a long-established visual clue for high-torque tools. Still, color alone shouldn’t be your only criterion. You might be wondering what else to consider. First, always check if the manufacturer or seller specifies “impact-rated” or provides official certifications. If you prefer color-coded sets for faster size selection, be sure to confirm that the color overlay can withstand heavy torque without peeling or flaking. Examine brand reputation too. If a manufacturer is known for forging superior chrome molybdenum steel and performing thorough heat treatments, their black or color-coded sockets will likely hold up well. Another tip involves reading user reviews or professional forums to confirm the finishes last under real-world shop conditions. Also, consider how clearly the size markings stand out from the socket’s color. Some brands etch numbers that can be read easily, while others rely on painted markings that fade quickly. If you work in environments with bright overhead lighting, a matte black socket might help reduce reflections. Finally, think about your toolbox organization. Brightly colored or consistently black sockets can both fit well if you maintain a labeling system. In short, color offers quick identification, but verifying the steel grade and torque capacity is crucial to ensure long-term performance.
Conclusion
Selecting the right color for your impact socket can streamline your workflow, reduce mistakes, and keep tools protected in rugged settings. Black has become the go-to choice because of its proven protective qualities, industry tradition, and practical benefits such as anti-glare and corrosion resistance. You might be wondering what to do next. The smartest approach is to balance aesthetics with fundamental factors like steel quality, forging methods, and brand reliability. Whether you stick with black or opt for color-coded versions, look for impact ratings and manufacturer details. That way, you’ll secure dependable sockets that stand up to everyday or professional demands.
If a bright color socket is automatically weaker? Not necessarily. Some top-tier manufacturers produce color-coded sets that maintain full impact capabilities. Always verify torque ratings and steel composition first.
People often ask if black coatings chip or fade quickly. Over time, the finish may wear away in high-contact areas, but moderate maintenance like routine oiling helps preserve the coating.
Another question is whether all black sockets are safe for impact use. Not every black tool meets impact standards. Some brands might color their sockets black without proper heat treatment or forging. Double-check the manufacturer’s product specifications to confirm genuine impact capability.
You might be curious about mixing black impact sockets with color-coded ones in the same set. That strategy is fine if each socket meets your torque and dimensional requirements Just remember to label or store them in a way that’s easy for your team to identify.
Finally, shoppers ask how to confirm an impact socket’s authenticity. Reputable brands provide standardized markings or etched labels indicating size, rating, and sometimes batch codes. Look for consistent finishes, crisp engravings, and robust packaging to avoid knockoff products.