Introduction
Have you ever found yourself wondering if it’s safe to use your regular socket with an impact wrench? Whether you’re a DIY enthusiast or a professional in the industry, using the right tools is crucial for both efficiency and safety. Regular sockets are commonly used with hand tools like ratchets, but what about pairing them with an impact wrench? Here’s the deal: while it may seem convenient to use any socket you have on hand, doing so can lead to problems, including broken sockets, damaged fasteners, and potential safety hazards. In this article, we’ll explore why using a regular socket on an impact wrench is not recommended, the differences between regular and impact sockets, and how you can ensure you’re using the right tools for the job.
What Is an Impact Wrench?
What Is an Impact Wrench?
An impact wrench, also known as a power wrench, is a tool that provides high torque output with minimal exertion from the user. Unlike traditional wrenches, an impact wrench uses a hammering mechanism inside the tool to apply force to the fastener. The high-speed hammering action makes it easier to loosen or tighten nuts and bolts that require significant torque, like those found on vehicle wheels, machinery, or heavy-duty construction equipment. Impact wrenches are often used in both industrial and automotive applications because of their ability to perform tasks quickly and with high force, reducing the amount of manual labor needed.
How Does an Impact Wrench Work?
The internal mechanism of an impact wrench consists of a motor, which drives a rotating hammer inside the tool. The hammer hits an anvil, which, in turn, applies force to the socket connected to the fastener. The rapid blows make it easier to turn the fastener without the user having to apply as much force, allowing you to tackle tough, high-torque jobs in a fraction of the time it would take with manual tools.
What Is a Regular Socket?
Understanding Regular Sockets
Regular sockets are basic hand tools used to tighten or loosen nuts, bolts, or fasteners. Made from materials like chrome vanadium steel, regular sockets are designed to withstand moderate force. They’re used in conjunction with ratchets, providing a stable and reliable way to handle smaller to medium-sized fastening jobs. A regular socket fits into the square drive of the ratchet, and when the user rotates the ratchet, it turns the socket, allowing for easy manipulation of fasteners.
Types of Regular Sockets
There are several types of regular sockets based on their design and intended use. Shallow sockets are typically used for bolts with ample clearance, while deep sockets are designed for recessed fasteners or bolts with longer threads. Regular sockets come in both metric and imperial sizes, ensuring compatibility with a variety of fastener types.
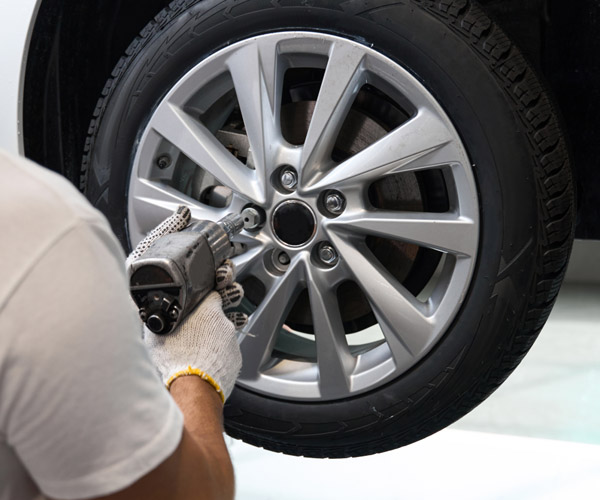
Impact Wrench vs. Regular Wrench: Key Differences
Power and Torque: Why Impact Wrenches Are Different
One of the primary differences between an impact wrench and a regular wrench is the torque they can apply. An impact wrench delivers significantly higher torque, often exceeding 300 lb-ft in many models. This high torque makes it ideal for heavy-duty applications like car repair, where you may need to break loose rusted or tightly secured bolts. On the other hand, a regular wrench, especially a hand ratchet, can apply much less torque, making it suitable for light-duty tasks like assembly and disassembly of smaller components.
Speed vs. Control: Understanding the Benefits of Each Tool
An impact wrench operates at much higher speeds compared to a manual wrench. While this makes it efficient for removing fasteners quickly, it also means that the user has less control over the tool. This lack of control can be advantageous in certain situations, like quickly removing a wheel nut, but may be a disadvantage when you need precision. In contrast, a regular wrench provides more control, making it ideal for delicate jobs, where precision and accuracy are key.
Can You Use a Regular Socket on an Impact Wrench?
The Answer: Yes, But With Caution
The short answer is yes, you can technically use a regular socket on an impact wrench, but it’s not recommended. Regular sockets are not designed to handle the extreme torque and hammering action produced by an impact wrench. If you use a regular socket, it can crack, warp, or even break under the pressure. While some regular sockets may hold up to light-duty impact use, this is not guaranteed, and using the wrong socket could lead to injury, broken tools, or damaged fasteners.
What Could Go Wrong?
Using a regular socket with an impact wrench could result in several issues. The most common problem is socket failure. Impact wrenches deliver high torque in rapid bursts, which can cause regular sockets to crack, split, or even shatter. This is especially true for sockets made from materials not built for high-stress environments. If the socket fails during use, you risk causing injury or damaging the fastener.
Why It’s Not Ideal to Use Regular Sockets
Regular sockets are made with thinner walls and are designed for slower, steady hand torque. The high-impact hammering of an impact wrench subjects regular sockets to forces they aren’t designed to handle. This can result in sockets that wear down prematurely, as well as an increased likelihood of accidents or breakages.
Why Are Impact Sockets Different?
Material Composition: The Strength of Impact Sockets
Impact sockets are designed with special materials like chrome molybdenum or chrome vanadium steel, which are both highly durable and resistant to wear. These materials are much stronger than the steel used in regular sockets, allowing impact sockets to absorb and distribute the force generated by impact wrenches.
Design Features: How Impact Sockets Are Built to Last
In addition to being made of stronger materials, impact sockets also have thicker walls compared to regular sockets. This added thickness helps them resist the force generated by impact wrenches, allowing them to absorb the shock rather than cracking or breaking. Impact sockets are also typically black or have a matte finish, which indicates that they are heat-treated to further enhance their durability and resistance to impact.
Durability: Why Impact Sockets Are Worth the Investment
Impact sockets are designed to withstand the high-stress environment that comes with using an impact wrench. They’re made to last longer and take more punishment than regular sockets. Investing in high-quality impact sockets ensures that you won’t have to replace them frequently, making them a better long-term choice for professionals and DIYers who use an impact wrench regularly.
The Risks of Using a Regular Socket on an Impact Wrench
Socket Cracking and Failure
As mentioned earlier, one of the main risks of using regular sockets on an impact wrench is that they can crack or fail due to the excessive force applied by the wrench. The rapid bursts of force put a lot of stress on the material, which isn’t designed to handle such pressures. If a regular socket cracks or shatters during use, not only will you need to replace the socket, but there’s also a safety risk involved.
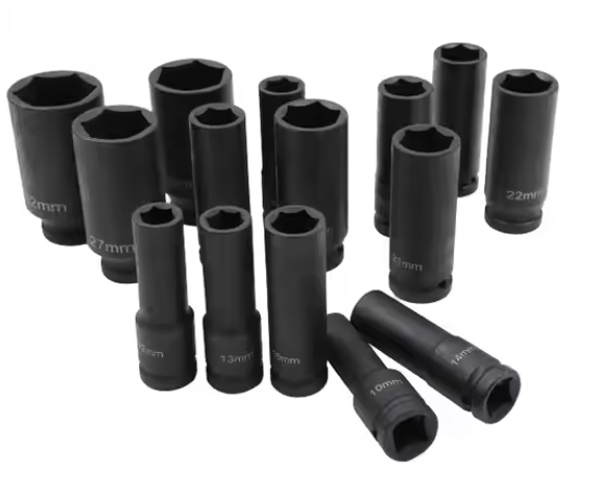
Safety Hazards: The Danger of Using Regular Sockets
When a regular socket breaks, the sharp edges can pose a serious safety hazard. The fragments of a broken socket can fly off at high speeds, potentially causing injuries. This is especially dangerous if the impact wrench is being used in a workshop or industrial environment, where workers are in close proximity to each other.
Damage to the Bolt or Nut
Another issue with using a regular socket is that it may not grip the fastener properly. If the socket fails to fit snugly on the bolt or nut, you risk stripping the fastener, making it difficult or impossible to remove. Stripping bolts can lead to costly repairs or replacements, making it essential to use the right socket to avoid unnecessary damage.
What Happens When You Use a Regular Socket on an Impact Wrench?
Detailed Breakdown of the Process
When you attach a regular socket to an impact wrench and begin using it, the hammering action of the wrench generates high-torque pulses that are transferred to the socket. Since regular sockets are not made to absorb such impacts, they will begin to show signs of stress, such as cracking or warping. Over time, the socket will weaken, and you may notice that it no longer fits snugly onto the fastener.
Real-World Examples
There are numerous real-world examples of people who have used regular sockets with impact wrenches and experienced problems. One such example involves a professional mechanic who used a regular socket on a high-torque impact wrench to remove a rusted bolt. The socket cracked under the pressure, causing the mechanic to lose time and money. The repair cost was high because the damaged fastener had to be replaced, and the broken socket had to be disposed of.
Is It Ever Safe to Use a Regular Socket on an Impact Wrench?
Exceptions to the Rule
In some cases, using a regular socket on an impact wrench might be acceptable. If you’re working on light-duty projects, such as hand-tightening fasteners, the risks are minimized. For low-torque jobs, a regular socket may handle the impact, but this is not ideal for high-stress applications. Always check the manufacturer’s guidelines to ensure you’re using the correct socket.
Low-Impact Jobs: When It’s Safe to Use Regular Sockets
Low-impact jobs, such as tightening bolts that don’t require much force, may allow for the use of regular sockets. In these cases, the socket will not experience the intense hammering that could cause it to fail. However, even for low-impact jobs, it’s recommended to use impact sockets when possible to avoid unexpected damage.
How to Tell if a Socket Is Impact-Ready
Visual Indicators of Impact Sockets
To identify an impact socket, look for specific visual cues. Impact sockets are typically darker in color, with many having a black oxide or matte finish. You may also see markings on the socket, such as “IMPACT” or a symbol indicating that it’s specifically designed for high-torque applications. These markings help you differentiate impact sockets from regular sockets.
Certification Marks
Impact sockets often feature certification marks that indicate they meet industry standards. For instance, some sockets are stamped with the manufacturer’s name or logo, as well as a “for impact use” label. Always choose a socket with these indicators to ensure that it will hold up under the force of an impact wrench.
The Role of Socket Size and Fit
Socket Size Matters
Choosing the correct socket size is critical when using an impact wrench. A socket that doesn’t fit properly on the fastener can slip off or cause damage to the bolt or nut. Always verify the size of the socket before using it with an impact wrench.
Common Socket Sizes for Impact Wrenches
Impact wrenches are typically used with a range of socket sizes, from 1/4-inch to 1/2-inch and 3/4-inch. For automotive and construction applications, the most common sizes are 3/8-inch and 1/2-inch drive sockets, which provide a good balance of torque and ease of use.
Best Practices for Using an Impact Wrench
Socket Selection Tips
To get the best performance from your impact wrench, always use the correct socket size and type. Select an impact-rated socket that matches the size of your fastener and is designed to handle high torque. Avoid using regular sockets or low-quality brands that aren’t built for heavy-duty work.
Proper Tool Maintenance
Impact wrenches and sockets require proper maintenance to ensure they perform well and last a long time. Regularly inspect your sockets for signs of wear, cracks, or chips. Keep your impact wrench clean and lubricated to prevent mechanical failure.
Safety Precautions
Always use the correct personal protective equipment (PPE) when using an impact wrench. Wear safety goggles and gloves to protect yourself from flying debris or broken socket fragments. Make sure to also check your impact wrench and sockets for damage before use.
What Are the Alternatives to Regular Sockets?
Impact Socket Sets
If you regularly use an impact wrench, investing in a high-quality impact socket set is a smart choice. These sets are designed to withstand the force generated by impact wrenches and provide a reliable solution for all your high-torque applications. Many sets come with a variety of sizes and types to cover all your needs.
Multi-Use Tools
There are also multi-use tools that offer compatibility with both regular hand wrenches and impact wrenches. These tools are versatile and can help you tackle a wide range of jobs without having to switch between different tools or socket types.
How Much Does It Cost to Buy Impact Sockets?
Price Range of Impact Sockets
Impact sockets come in various price ranges, depending on the brand and quality. Entry-level sets can start around $20, while high-end sets can cost upwards of $200. While price isn’t everything, it’s important to choose a set that balances affordability with durability.
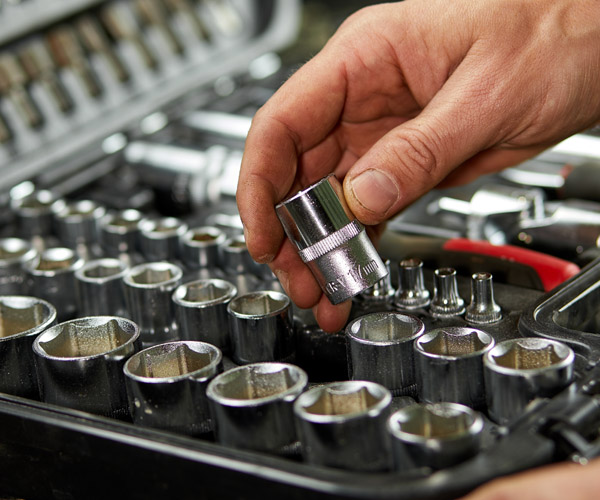
Long-Term Value
Investing in high-quality impact sockets may seem like a significant upfront cost, but in the long run, they are worth the investment. A good set will last for years, withstand high-impact use, and prevent the cost of replacing broken or damaged tools.
Impact Wrench Myths and Misconceptions
Common Misunderstandings
One common misconception is that impact wrenches are too powerful for certain jobs. In reality, impact wrenches are designed for both light and heavy-duty tasks when used with the correct socket. Another myth is that all wrenches are interchangeable, but as we’ve discussed, using the wrong socket can lead to major issues.
Impact Wrench Use in Automotive Work
Impact wrenches are indispensable in automotive repair and maintenance. From removing lug nuts to tightening bolts, these tools save time and effort. However, it’s essential to understand when and how to use them properly, especially when selecting the right socket.
Conclusion
Using a regular socket on an impact wrench might seem tempting, but the risks outweigh the benefits. Regular sockets are simply not built to handle the high torque and rapid hammering that impact wrenches deliver. By choosing impact-rated sockets, you ensure your tools perform at their best, without risk of damage to your fasteners or the tool itself. Always check for proper socket sizes and invest in quality gear for long-term durability and safety. Don’t compromise on safety—ensure you’re using the right tools for the job every time.