Introduction
In the world of tools, the quality of a socket set can make all the difference in ensuring efficient and safe work. Whether you’re a professional mechanic, a DIY enthusiast, or somewhere in between, having a reliable socket set is essential. Socket set manufacturers understand the critical role their products play in various applications, from automotive repairs to construction projects. Hence, they invest significant resources into producing high-quality socket sets that meet rigorous standards.
Why Quality Matters in Socket Sets
Quality in socket sets is not just about having a shiny finish or a well-known brand name. It encompasses a range of factors that ensure durability, precision, and safety. Here’s why quality should be a top priority:
- Durability: High-quality socket sets are made from robust materials that can withstand high torque and heavy use without deforming or breaking.
- Precision: Accurate sizing and fit are crucial for preventing slippage and damage to fasteners.
- Safety: Inferior socket sets can fail under pressure, posing a risk to users and their projects.
How Manufacturers Ensure Quality
To produce high-quality socket sets, socket set manufacturers follow stringent processes and standards. These steps ensure that each set not only meets but exceeds customer expectations. Here’s a closer look at what goes into making a top-tier socket set:
- Material Selection: The choice of materials is the first step in manufacturing high-quality socket sets. Manufacturers opt for high-grade steel, such as chrome vanadium or chrome molybdenum, which offers excellent strength and resistance to wear and tear.
- Manufacturing Techniques: Advanced manufacturing techniques like forging and precision machining are employed to create durable and accurately sized sockets. Forging, in particular, enhances the strength and grain structure of the metal, making it more resilient.
- Heat Treatment: Heat treatment processes such as quenching and tempering are used to further enhance the strength and durability of the sockets. This process ensures that the sockets can handle high levels of torque without cracking or breaking.
- Surface Treatment: To protect against corrosion and rust, manufacturers apply various surface treatments like chrome plating or black oxide finishes. These treatments not only enhance the longevity of the sockets but also give them a professional appearance.
- Quality Control: Rigorous quality control measures are in place to inspect and test each socket set. This includes checking for proper sizing, hardness, and overall integrity. Manufacturers adhere to industry standards and certifications to ensure consistency and reliability.
Identifying High-Quality Socket Sets
When evaluating socket sets, consumers should consider several key indicators of quality. Here are some tips to help you identify a high-quality socket set:
- Material and Build Quality: Look for socket sets made from high-grade materials such as chrome vanadium steel. Check for signs of solid construction and robust build.
- Finish and Coating: High-quality socket sets often have a smooth, polished finish or a protective coating to prevent rust and corrosion.
- Precision and Fit: Ensure that the sockets fit snugly onto fasteners without any wobble. Precision-engineered sockets will have tight tolerances for a perfect fit.
- Brand Reputation: Established socket set manufacturers typically have a track record of producing reliable and high-quality tools. Researching brand reputation can provide insights into the quality of their products.
- Warranty and Support: A comprehensive warranty indicates the manufacturer’s confidence in their product. Look for socket sets that come with a solid warranty and good customer support.
By understanding the factors that contribute to high-quality socket sets, consumers can make informed decisions and invest in tools that will provide long-lasting performance and safety.
Understanding Socket Sets
Socket sets are indispensable tools for both professional mechanics and DIY enthusiasts. A socket set consists of various components that work together to perform a range of tasks. Understanding the basic components and types of socket sets is crucial for selecting the right set for your needs.
Overview of Socket Sets
A socket set typically includes:
- Sockets: These are the primary components of a socket set. They come in various sizes and types to fit different bolts and nuts.
- Ratchets: A ratchet is a handle with a mechanism that allows for the turning of a socket in one direction without moving back in the opposite direction, making it easier to tighten or loosen fasteners.
- Extensions: These are used to extend the reach of the socket, making it possible to access bolts in hard-to-reach places.
- Adapters: Adapters allow sockets to be used with different drive sizes.
Components of a Socket Set
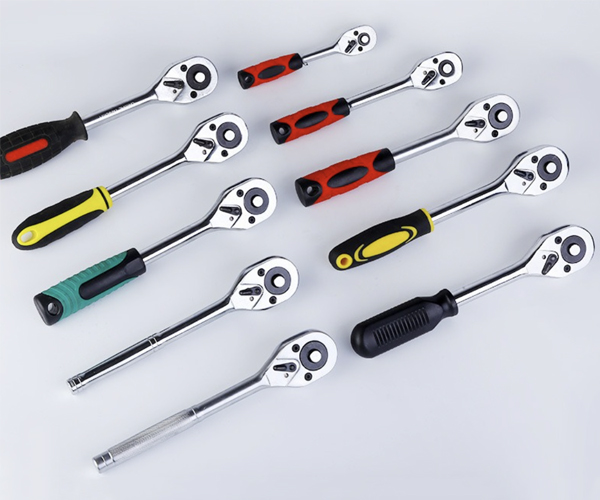
The sockets themselves are the most critical part of any socket set. They are typically made from high-strength materials like chrome vanadium steel to ensure durability and performance. Sockets come in various sizes to fit different fasteners:
- Metric Sockets: These sockets are measured in millimeters and are commonly used in automotive and machinery repairs.
- SAE Sockets: Measured in inches, SAE sockets are typically used in American-made vehicles and equipment.
There are also different types of sockets based on their design and use:
- Standard Depth Sockets: These are the most common and are used for general purposes.
- Deep Sockets: These are longer and are used to reach bolts that are recessed or where the bolt extends beyond the nut.
- Impact Sockets: Made from thicker and more resilient materials, impact sockets are designed to withstand the high torque of impact wrenches.
Types of Socket Sets
Understanding the various types of socket sets can help you choose the best one for your needs. Some common types include:
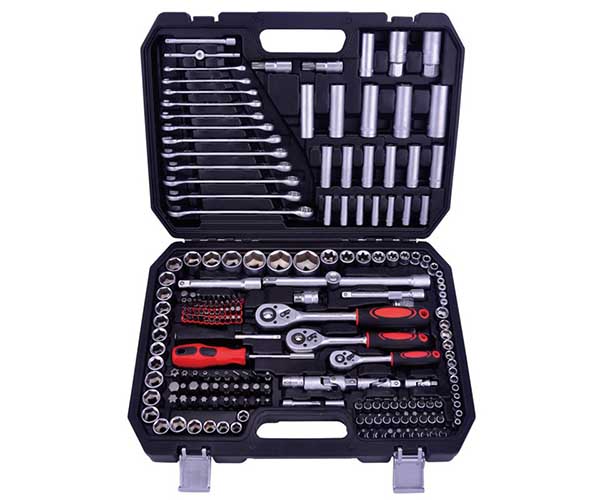
- Mechanic’s Socket Sets: These comprehensive sets include a wide range of socket sizes and types, ratchets, and extensions, designed for professional mechanics who need a versatile and reliable tool set.
- Automotive Socket Sets: Specifically tailored for automotive repair, these sets often include both metric and SAE sizes and may feature specialized tools like spark plug sockets.
- Household Socket Sets: These are smaller sets designed for general household repairs and DIY projects. They usually include the most common socket sizes and a basic ratchet.
A socket set manufacturer focuses on producing these essential tools with precision and quality. They ensure that each component meets rigorous standards to provide reliability and longevity. A reputable socket set manufacturer will often offer a warranty and provide detailed information about the materials and manufacturing processes used in their socket sets.
Choosing the Right Socket Set
When selecting a socket set, consider the following factors:
- Material Quality: Look for sets made from high-grade materials like chrome vanadium steel, which offer durability and resistance to wear and corrosion.
- Range of Sizes: Ensure the set includes a comprehensive range of socket sizes to handle various tasks.
- Ratchet Mechanism: A high-quality ratchet with a fine-tooth mechanism allows for smoother and more precise operation.
- Accessories: Additional tools like extensions and adapters can enhance the versatility of the socket set.
In conclusion, a well-chosen socket set from a reputable socket set manufacturer can significantly improve efficiency and ease in performing mechanical tasks. By understanding the components and types of socket sets, you can make an informed decision that meets your specific needs. Whether you are a professional mechanic or a DIY enthusiast, investing in a high-quality socket set is essential for successful and efficient work.
Key Quality Indicators
Identifying the key quality indicators of a high-quality socket set involves a comprehensive understanding of the materials, manufacturing processes, finishes, and precision used by reputable socket set manufacturers. Here are the critical aspects to consider:
Material Quality
- High-Grade Steel: The backbone of any high-quality socket set is the use of superior materials. Look for sets made from high-grade steel, such as chrome vanadium or chrome molybdenum. These materials offer excellent strength, durability, and resistance to wear and tear.
- Impact-Resistant Alloys: For applications requiring heavy-duty performance, impact-resistant alloys are crucial. These materials can withstand high torque and impact without deforming, ensuring longevity and reliability.
Manufacturing Process
- Forging vs. Casting: The method used to produce the sockets can significantly affect their quality. Forged sockets are typically stronger and more durable than cast ones. The forging process involves shaping the metal using compressive forces, which aligns the grain structure and enhances the socket’s strength.
- Heat Treatment: A critical step in the manufacturing process is heat treatment, which involves heating and cooling the metal to alter its physical and mechanical properties. This process increases the hardness and toughness of the sockets, making them more resistant to wear and deformation.
- Precision Machining: High-quality sockets are precisely machined to ensure accurate dimensions and tight tolerances. This precision is crucial for a snug fit on fasteners, reducing the risk of slipping and rounding off corners.
Finish and Coating
- Chrome Plating: Many socket set manufacturers use chrome plating to provide a protective layer against corrosion and rust. This shiny finish not only enhances the aesthetic appeal but also extends the life of the sockets.
- Black Oxide Coating: For those who prefer a matte finish, black oxide coating offers an alternative. This coating provides a degree of corrosion resistance and reduces glare, which can be advantageous in certain work environments.
- Corrosion Resistance: Ensuring the sockets have a robust coating to protect against corrosion is essential, especially for those used in harsh environments. Quality coatings can prevent rust and prolong the tool’s lifespan.
Fit and Tolerance
- Tight Fit: A key indicator of a high-quality socket is its ability to fit snugly on fasteners. Loose-fitting sockets can slip, causing damage to both the tool and the fastener. Precision in manufacturing ensures that sockets have tight tolerances, leading to a secure fit.
- Accurate Sizes: Consistency in size accuracy is vital. High-quality socket set manufacturers ensure their products meet exact specifications, providing reliability and performance.
Manufacturer Testing Procedures
- Load Testing: High-quality socket set manufacturers conduct rigorous load testing to ensure their sockets can handle the specified torque without failure. This testing simulates real-world conditions and stresses the sockets to their limits.
- Torque Testing: Another essential test is torque testing, which measures the amount of rotational force a socket can withstand. This ensures the socket can perform under the pressure of high-torque applications without cracking or deforming.
- Durability Tests: Comprehensive durability tests are performed to assess the overall longevity of the sockets. These tests can include repeated use simulations and exposure to harsh conditions to ensure the sockets maintain their integrity over time.
Industry Standards and Certifications
- ISO Standards: Compliance with ISO standards indicates that the manufacturer adheres to international quality management and assurance protocols. This certification ensures that the sockets meet global quality and performance standards.
- ANSI/ASME Compliance: Sockets that comply with ANSI (American National Standards Institute) and ASME (American Society of Mechanical Engineers) standards have undergone stringent testing and evaluation. This compliance is a hallmark of quality, indicating that the sockets are safe, reliable, and suitable for professional use.
In summary, when evaluating socket sets, consider the material quality, manufacturing processes, finishes, fit, and adherence to industry standards. Reputable socket set manufacturers will ensure their products meet these high-quality indicators, providing tools that are durable, reliable, and effective for a wide range of applications.
Testing and Certification
Testing and certification are critical components in ensuring that socket sets meet the highest standards of quality and performance. For any socket set manufacturer, rigorous testing protocols and adherence to industry certifications are essential to guarantee the reliability and safety of their products.
Manufacturer Testing Procedures
To achieve and maintain high-quality standards, socket set manufacturers implement a variety of testing procedures throughout the production process:
- Load Testing: This involves applying maximum torque to the sockets and ratchets to ensure they can withstand high-stress conditions without failure. Load testing is crucial for determining the durability and strength of the tools under extreme use.
- Torque Testing: Torque testing measures the ability of a socket to maintain its shape and functionality when subjected to rotational force. This test helps in verifying that the sockets can handle the specified torque levels without cracking or deforming.
- Durability Tests: Manufacturers conduct long-term durability tests to simulate extended usage scenarios. These tests help in assessing the wear and tear of the sockets and ensure that they remain functional after prolonged use.
Industry Standards and Certifications
Adherence to industry standards and obtaining relevant certifications is a testament to a socket set manufacturer‘s commitment to quality. Some of the key certifications and standards include:
- ISO Standards: The International Organization for Standardization (ISO) sets global standards for various industries, including tool manufacturing. Compliance with ISO standards ensures that the socket sets meet international quality and safety benchmarks.
- ANSI/ASME Compliance: The American National Standards Institute (ANSI) and the American Society of Mechanical Engineers (ASME) establish standards specifically for tools and equipment. Sockets and ratchets that comply with ANSI/ASME standards have undergone rigorous testing and are guaranteed to meet high-performance criteria.
- CE Marking: For manufacturers exporting to Europe, the CE marking indicates conformity with health, safety, and environmental protection standards. It is a mandatory certification for products sold within the European Economic Area (EEA).
Manufacturer’s Perspective on Quality
From the manufacturer’s standpoint, maintaining high-quality standards involves a continuous process of design innovation, quality control, and customer feedback integration.
- Design and Innovation: A focus on research and development (R&D) allows manufacturers to innovate and improve socket set designs. This includes the development of ergonomic handles, stronger materials, and more efficient manufacturing processes.
- Quality Control Measures: Implementing stringent quality control measures is vital for a socket set manufacturer. This involves in-process inspections during production, final inspections before packaging, and random sampling to ensure consistency.
- Customer Feedback and Continuous Improvement: Manufacturers value customer feedback as it provides insights into real-world performance and areas for improvement. Regularly updating designs and addressing customer concerns helps in maintaining high standards and customer satisfaction.
Practical Tips for Consumers
Understanding the testing and certification processes can help consumers make informed decisions when purchasing socket sets. Here are some practical tips:
- Evaluating Socket Sets Before Purchase: Look for certification marks like ISO, ANSI, ASME, and CE on the packaging or product itself. These marks indicate that the socket set has passed rigorous testing standards.
- Understanding Manufacturer Warranties: A comprehensive warranty is a good indicator of the manufacturer’s confidence in their product. Check the terms of the warranty to understand what is covered and for how long.
- Maintenance Tips for Longevity: Proper maintenance is key to ensuring the longevity of your socket set. Regularly clean the sockets, store them in a dry place, and apply lubrication to moving parts to prevent rust and wear.
By paying attention to these details, consumers can ensure they are purchasing high-quality socket sets that will perform reliably and last for years. This knowledge empowers them to select products that not only meet but exceed their expectations, backed by the rigorous standards set by reputable socket set manufacturers.
Manufacturer’s Perspective on Quality
When it comes to producing high-quality socket sets, a reputable socket set manufacturer emphasizes several critical aspects that ensure the reliability and durability of their products. Here’s an in-depth look at how leading manufacturers approach quality:
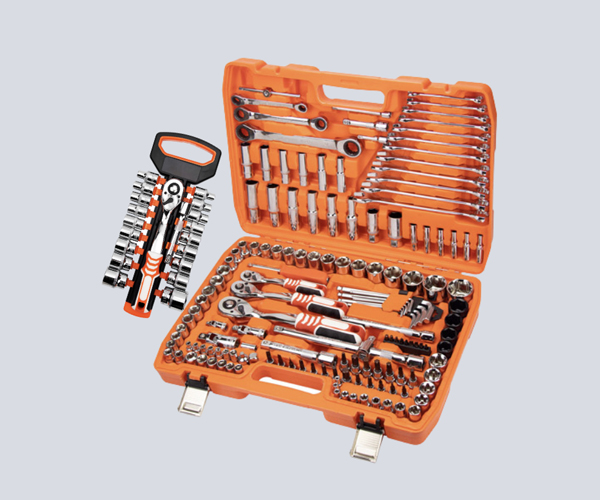
Design and Innovation
- Research and Development (R&D): Top manufacturers invest heavily in R&D to innovate and improve socket set designs. This involves creating new features that enhance usability and performance.
- Ergonomics: Designing socket sets that are comfortable to use, reducing user fatigue, and improving efficiency. This includes the shape of the handles, the grip, and the ease of switching sockets.
- Material Selection: Using high-quality materials such as chrome vanadium and other impact-resistant alloys ensures that socket sets can withstand heavy use and extreme conditions.
Quality Control Measures
- In-Process Inspections: During the manufacturing process, socket sets are inspected at multiple stages. This helps in catching defects early and maintaining consistent quality.
- Final Inspections: Before packaging, each socket set undergoes rigorous final inspections to ensure they meet the company’s quality standards. This includes checking for accurate sizing, proper fit, and flawless finish.
- Quality Assurance Protocols: Implementing stringent quality assurance protocols ensures that every socket set leaving the factory is reliable and performs well under stress.
Customer Feedback and Continuous Improvement
- Listening to Customers: Feedback from end-users is invaluable. Manufacturers analyze customer reviews and feedback to understand what works well and what needs improvement.
- Iterative Improvements: Based on customer feedback, manufacturers make iterative improvements to their products. This might involve tweaking designs, using better materials, or improving manufacturing processes.
- Field Testing: Before finalizing a design, manufacturers often conduct extensive field testing. This involves real-world testing by professionals to ensure that the socket sets can handle practical, everyday tasks.
Advanced Manufacturing Techniques
- Precision Machining: High-precision machining ensures that each component of the socket set fits perfectly. This reduces wear and tear and extends the life of the tools.
- Heat Treatment: Applying proper heat treatment processes to strengthen the metal components. This increases the durability and performance of the socket sets.
- Coating and Finishing: Using advanced coating and finishing techniques like chrome plating and black oxide coating to protect against corrosion and wear.
Industry Standards and Certifications
- Compliance with Standards: Ensuring that all socket sets comply with international standards such as ISO, ANSI, and ASME. Compliance guarantees that the tools meet minimum quality and safety requirements.
- Certification Processes: Obtaining certifications from reputable organizations to demonstrate adherence to industry standards. This adds an extra layer of credibility and trustworthiness.
Practical Insights from Manufacturers
- Material Testing: Conducting thorough material testing to select the best alloys that provide strength and durability.
- Design Optimization: Continuously optimizing design elements to improve functionality and user experience.
- Manufacturing Excellence: Striving for manufacturing excellence through the adoption of best practices and cutting-edge technologies.
By focusing on these aspects, a socket set manufacturer can produce tools that are not only high-quality but also reliable and long-lasting. This commitment to quality helps build trust with consumers and establishes the manufacturer as a leader in the industry.
Practical Tips for Consumers
When evaluating socket sets for purchase, it is essential to consider various factors to ensure you invest in a high-quality product that meets your needs. Here are some practical tips for consumers, focusing on insights from a socket set manufacturer perspective:
- Checking for Certifications:
- Look for certifications from recognized industry bodies like ISO, ANSI, and ASME. These certifications indicate that the socket set meets specific quality standards and has undergone rigorous testing.
- Ensure that the socket set manufacturer adheres to these standards, which guarantees that the products are reliable and safe to use.
- Inspecting Materials and Finish:
- High-quality socket sets are typically made from high-grade steel, such as chrome vanadium or chrome molybdenum. These materials are known for their durability and strength.
- Check for a smooth, even finish on the sockets. Chrome plating or black oxide coating helps prevent rust and corrosion, extending the life of your tools.
- Avoid socket sets with visible defects, rough edges, or inconsistent finishes, as these can be signs of poor manufacturing quality.
- Reading Reviews and Recommendations:
- Customer reviews can provide valuable insights into the performance and durability of a socket set. Look for reviews that mention long-term use and how well the tools have held up over time.
- Professional reviews from tool enthusiasts and experts can also offer detailed evaluations of different socket sets, helping you make an informed decision.
- Understanding Manufacturer Warranties:
- A comprehensive warranty is a strong indicator of the manufacturer’s confidence in their product. Look for warranties that cover defects in materials and workmanship.
- Understand the terms of the warranty, including the duration and what is specifically covered. A good warranty can provide peace of mind and protect your investment.
- Evaluating Fit and Tolerance:
- Precision is crucial in socket sets. Ensure that the sockets fit snugly onto the fasteners without excessive play. A loose fit can lead to rounded corners on nuts and bolts, reducing their usability.
- Check if the socket set manufacturer highlights their manufacturing process, specifically mentioning how they achieve tight tolerances and precise fits.
- Maintenance Tips for Longevity:
- Proper storage is essential to keep your socket set in good condition. Use the provided case or a dedicated tool chest to prevent damage and loss of individual pieces.
- Regularly clean your sockets and ratchets to remove dirt, grease, and debris. This maintenance helps prevent rust and ensures smooth operation.
- Lubricate moving parts, such as ratchets, with a light oil to keep them functioning properly. Avoid using excessive force that can damage the tools or reduce their lifespan.
- Avoiding Misleading Marketing Claims:
- Be cautious of marketing that makes exaggerated claims about the socket set’s capabilities. Look for specific, verifiable information rather than vague promises.
- A reputable socket set manufacturer will provide detailed specifications and testing results to back up their claims.
- Identifying Cheap Imitations:
- Low-cost socket sets can be tempting, but they often compromise on quality. These sets might be made from inferior materials that are prone to breaking or wearing out quickly.
- Ensure that the socket set you purchase is from a recognized and reputable socket set manufacturer. Authenticity can often be verified through the manufacturer’s website or customer service.
By following these tips, you can confidently select a high-quality socket set that will serve you well for years to come. Investing in tools from a reputable socket set manufacturer ensures that you get the best value for your money, with reliable performance and durability.
Common Pitfalls to Avoid
When purchasing socket sets, many consumers fall prey to several common pitfalls that can lead to dissatisfaction and wasted money. Recognizing and avoiding these traps can ensure that you get a high-quality product that meets your needs and lasts for years. Here are some key pitfalls to watch out for:
Misleading Marketing Claims
Socket set manufacturers often use marketing language designed to make their products appear more appealing than they might be. It’s essential to look beyond the hype and examine the actual specifications and reviews.
- Bold Claims Without Evidence: Be wary of manufacturers that make bold claims about the superiority of their socket sets without providing concrete evidence or certifications to back them up. Look for third-party reviews and certifications that validate these claims.
- Buzzwords Without Substance: Terms like “premium,” “industrial grade,” and “professional quality” are frequently used but can be meaningless without context. Always check what these terms mean in the context of the specific product.
Cheap Imitations
One of the biggest risks when buying socket sets is encountering low-cost, low-quality imitations. These products might look similar to high-quality sets but fail to meet the same standards of durability and performance.
- Too Good to Be True Pricing: If a socket set is significantly cheaper than comparable products from reputable socket set manufacturers, it’s likely an imitation. Quality materials and manufacturing processes cost money, and extremely low prices often indicate cost-cutting on essential aspects.
- Lack of Brand Reputation: Established brands have reputations to uphold and are less likely to sell subpar products. Lesser-known brands or generic products should be approached with caution unless they have verifiable positive reviews.
Overlooking Material Quality
The materials used in socket sets play a crucial role in their performance and durability. Inferior materials can lead to premature wear and even safety hazards.
- Unknown Material Composition: High-quality socket sets are typically made from chrome vanadium steel or other high-strength alloys. If the manufacturer does not specify the material composition, it’s a red flag.
- Poor Finish: The finish on a socket set not only impacts its appearance but also its resistance to rust and corrosion. Ensure that the set has a proper finish, like chrome plating or black oxide, which offers protection against the elements.
Ignoring Certifications and Standards
Certifications and adherence to industry standards are strong indicators of a socket set’s quality. Skipping this verification step can result in purchasing substandard tools.
- Lack of ISO or ANSI/ASME Certification: Trusted socket set manufacturers will have their products certified by international standards organizations like ISO or meet ANSI/ASME standards. These certifications ensure the tools have been tested for quality and safety.
- Missing Warranty Information: Quality manufacturers stand by their products with warranties. If a socket set does not come with a warranty or has an unusually short warranty period, it may be a sign of lower quality.
Not Checking Reviews and Feedback
Customer reviews and feedback provide valuable insights into the actual performance and durability of a socket set. Ignoring these can lead to poor purchasing decisions.
- Ignoring Negative Reviews: Pay attention to the negative reviews as much as the positive ones. Consistent issues reported by multiple users are likely to be genuine problems with the product.
- Falling for Fake Reviews: Be cautifous of overly positive reviews that seem generic or repetitive. Genuine reviews will often provide specific details about the product’s performance.
Overlooking the Fit and Tolerance
The precision with which a socket fits the fastener is critical for its effectiveness and longevity. Poor fit can lead to slippage and rounded fasteners.
- Inconsistent Sizing: Ensure that the socket set has precise sizing and tight tolerances. Socket set manufacturers who prioritize quality will have rigorous quality control processes to ensure each piece meets exact specifications.
- Lack of Flexibility in Set Options: High-quality socket sets often come with a variety of sizes and types to accommodate different tasks. A limited selection can be a sign of lower quality or a lack of specialization.
By being mindful of these common pitfalls, consumers can make more informed decisions and select socket sets that truly offer the best value for their money. Remember, a little extra diligence in the selection process can go a long way in ensuring you purchase a high-quality, durable, and reliable socket set.
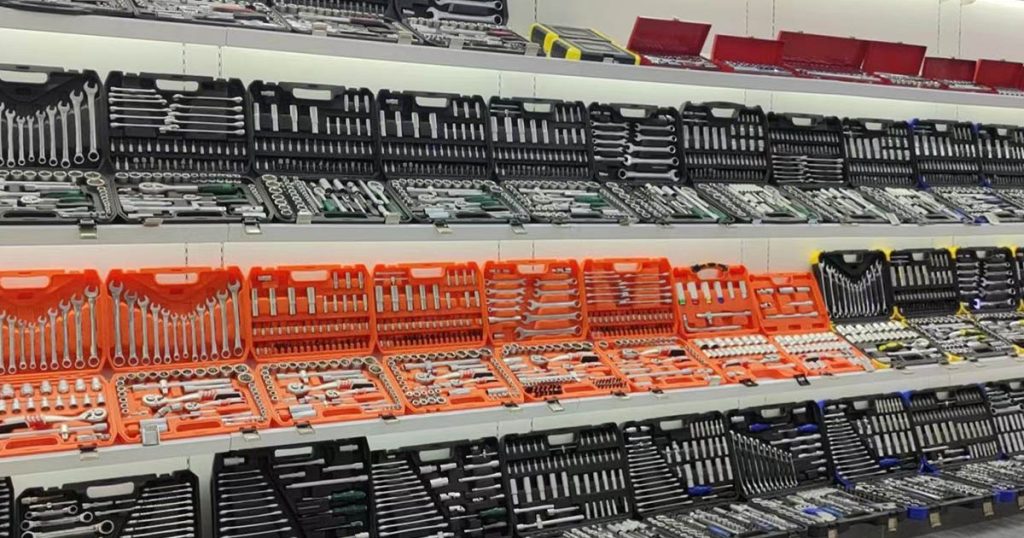
Conclusion
Recap of Key Points:
- The importance of material quality, including the use of high-grade steel and chrome vanadium, which ensures durability and strength in socket sets.
- Understanding the manufacturing process, such as forging versus casting and heat treatment, which contributes to the overall quality and precision of the socket sets.
- The role of finish and coating, including chrome plating and black oxide, which protect against corrosion and wear.
- The significance of fit and tolerance, ensuring that sockets fit tightly and accurately to prevent slippage and damage.
Final Thoughts: Choosing a high-quality socket set is not just about picking the most expensive option on the shelf. It’s about understanding the intricate details that go into manufacturing these essential tools and recognizing the hallmarks of quality. A reputable socket set manufacturer will prioritize material quality, precision manufacturing processes, rigorous testing, and customer feedback to deliver a product that stands the test of time.
Here are a few final tips to ensure you make an informed purchase:
- Research the Manufacturer:
- Look for manufacturers with a proven track record in the industry.
- Check for certifications and adherence to industry standards like ISO and ANSI/ASME.
- Consider manufacturers known for innovation and continuous improvement.
- Inspect the Product:
- Examine the materials used, looking for high-grade steel or alloys.
- Check the finish and coating for signs of quality, such as smooth chrome plating or black oxide.
- Ensure the sockets have a precise fit and feel durable.
- Read Reviews and Testimonials:
- Look for feedback from other customers who have used the product.
- Pay attention to any recurring issues or praises in the reviews.
- Consider the Warranty:
- A good warranty indicates that the manufacturer stands behind their product.
- Look for comprehensive warranties that cover a reasonable period and include clear terms.
- Maintenance and Care:
- Proper storage and regular cleaning can extend the life of your socket set.
- Follow any maintenance guidelines provided by the manufacturer.
By following these tips and understanding what makes a high-quality socket set, you can make a purchase that not only meets your immediate needs but also provides long-term value and reliability. Remember, the right tools can make all the difference in your projects, and investing in quality is always a wise decision.
In conclusion, a reliable socket set manufacturer ensures that their products undergo stringent quality control and testing procedures, use superior materials, and incorporate feedback from their customers to continually improve their offerings. This attention to detail and commitment to excellence is what sets the best manufacturers apart and ensures that their socket sets can handle the demands of both professional and DIY applications. Making an informed choice based on these factors will help you select a socket set that you can rely on for years to come.
FAQs on Socket Set Manufacturer
What are good quality socket sets?
Good quality socket sets are made from high-grade materials such as chrome vanadium or chrome molybdenum steel, which offer excellent durability and corrosion resistance. They are manufactured with precision to ensure a perfect fit and feature a high-quality finish like chrome plating or black oxide. Reliable socket sets often come with comprehensive warranties and are certified by industry standards such as ISO or ANSI/ASME.
What should I look for in a socket set?
When selecting a socket set, consider the following factors:
- Material: High-grade steel (e.g., chrome vanadium) for durability.
- Finish: Corrosion-resistant coatings like chrome plating.
- Size Range: A variety of socket sizes to cover different applications.
- Drive Size: Ensure compatibility with your tools (e.g., 1/4″, 3/8″, 1/2″).
- Inclusions: Additional tools like ratchets, extensions, and adapters.
- Brand Reputation: Established manufacturers with good customer reviews.
- Warranty: Comprehensive warranties indicating confidence in product quality.
What is the best socket manufacturer?
The best socket manufacturer depends on your specific needs and preferences. However, some top-rated brands known for their quality and reliability include:
- Snap-on: Renowned for premium quality and lifetime warranty.
- Craftsman: Known for affordability and decent quality.
- Matco Tools: Offers high-quality tools with excellent customer support.
- Gearwrench: Provides innovative designs and good value for money.
- DeWalt: Known for durable, impact-rated sockets suitable for heavy-duty use.
How do I know if my socket is impact-rated?
Impact-rated sockets are designed to withstand the high torque and vibration of impact tools. You can identify an impact-rated socket by the following characteristics:
- Material: Typically made from chrome molybdenum or high-strength alloy steel.
- Finish: Usually have a black oxide or phosphate finish instead of chrome.
- Markings: Clearly labeled as “impact” on the socket or packaging.
- Thickness: Thicker walls compared to standard sockets to handle higher stress.
What is an impact-rated socket?
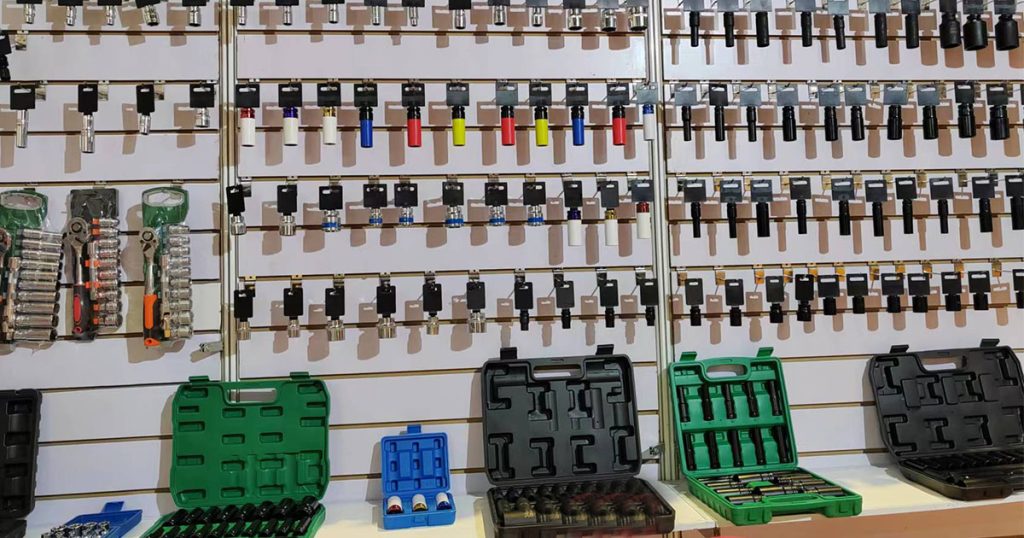
An impact-rated socket is a type of socket designed specifically for use with impact wrenches and drivers. These sockets are made from stronger materials like chrome molybdenum steel to endure the high torque and vibrations produced by impact tools. They feature thicker walls and a durable black oxide coating to prevent corrosion and enhance longevity.
What is the standard socket rating?
Standard socket ratings refer to the specifications and tolerances that sockets must meet to ensure safety and performance. These ratings include:
- Drive Size: Common sizes are 1/4″, 3/8″, 1/2″, 3/4″, and 1″.
- Material Strength: Must comply with industry standards like ANSI/ASME.
- Torque Rating: The maximum amount of torque the socket can handle without failing.
- Size Accuracy: Ensures the socket fits securely on fasteners without slipping.
Understanding these aspects can help you choose the right socket set and manufacturer, ensuring you get a reliable and high-quality tool for your needs.