Introduction
The world of manufacturing is evolving, and impact socket producers face relentless challenges in the global marketplace. From pricing wars to changing consumer demands, competition is fierce. For impact socket manufacturers, understanding the intricacies of global competition is no longer optional—it’s essential for survival. Businesses that adapt quickly, innovate consistently, and deliver high-quality products are the ones that thrive in this competitive environment. So, how can manufacturers succeed amidst these pressures? The answer lies in identifying the key factors driving global competition and finding actionable strategies to overcome them. Let’s dive in.
- Build strong relationships with manufacturers by maintaining open and transparent communication.
- Request samples to assess quality before committing to bulk purchases.
- Negotiate pricing based on volume while considering long-term collaboration opportunities.
- Understand the manufacturer’s capacity and lead times to align with your supply chain needs.
- Stay updated on trade policies and tariffs to avoid unexpected costs or delays.
What Are Impact Sockets and Their Role in Modern Industries?
Impact sockets are specialized tools designed to withstand high torque levels when used with impact wrenches or drivers. Unlike standard sockets, these tools are built to endure the intense force generated by power tools, making them essential in industries where durability and reliability are non-negotiable. These industries include automotive repair, aerospace manufacturing, construction, and industrial maintenance.
The unique properties of impact sockets—such as their thicker walls and use of materials like chrome-molybdenum steel—set them apart. These design elements allow them to resist wear and tear over extended periods, even under extreme conditions. For instance, automotive mechanics rely on impact sockets to loosen and tighten bolts that would be impossible to manage with traditional tools. Here’s why this matters: Industries require tools that can perform consistently without fail, making the quality of impact sockets a crucial factor in their operations.
Moreover, impact sockets are integral to safety in professional environments. Poor-quality tools can break under pressure, posing risks to workers and equipment. As global demand for precision and efficiency increases, the role of impact sockets continues to grow. Businesses depend on these tools for their reliability, and manufacturers must prioritize quality to remain competitive.
Overview of the Global Impact Socket Manufacturing Industry
The global impact socket industry is a dynamic and rapidly evolving sector. Major manufacturing hubs include China, the United States, and Germany, each contributing unique strengths to the market. China dominates with its cost-efficient production and large-scale manufacturing capabilities. In contrast, the United States and Germany lead in innovation, focusing on precision engineering and advanced materials.
Emerging markets, particularly in Southeast Asia, are also gaining traction. Countries like Vietnam and India are investing in infrastructure and technology to compete in this space. But here’s the kicker: These new players bring competitive pricing while improving quality standards, putting pressure on established manufacturers.
The industry has seen significant growth in recent years, driven by increasing industrialization and a growing emphasis on automation. Impact sockets are no longer niche tools; they are now staples in sectors ranging from automotive to aerospace. As demand rises, so does the need for manufacturers to differentiate themselves through quality, innovation, and customer service.
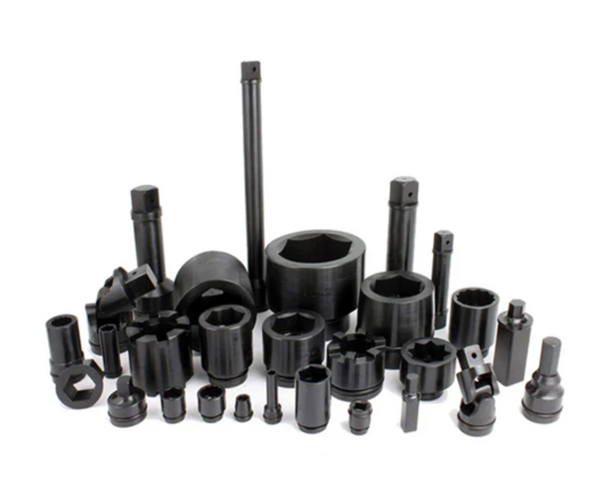
What Drives Global Competition in Impact Socket Manufacturing?
Global competition in the impact socket market is fueled by several key factors. First and foremost, cost efficiency plays a significant role. Manufacturers in low-cost regions often undercut prices, making it challenging for producers in higher-cost regions to compete. But wait, there’s more: Innovation also drives competition. Companies that invest in research and development to create stronger, lighter, and more durable tools gain a significant edge.
Consumer expectations are another driving force. Buyers demand high-quality tools at competitive prices, pushing manufacturers to improve their processes continually. Additionally, trade policies and tariffs impact competition. For instance, changes in U.S.-China trade relations have forced manufacturers to rethink their strategies, either by diversifying their supply chains or absorbing higher costs.
Finally, technological advancements have leveled the playing field. Automation and digital tools allow smaller manufacturers to compete with industry giants by improving efficiency and reducing production times. Global competition is not just about cost anymore—it’s about innovation, adaptability, and customer focus.
The Role of Technology in Increasing Global Competition
Technology is revolutionizing the impact socket manufacturing industry. Automation has streamlined production processes, reducing labor costs and improving consistency. Advanced robotics and AI-driven systems can perform tasks with precision, allowing manufacturers to scale operations efficiently. But that’s not all: Innovations in material science are also shaping the industry. For example, newer alloys and composites are making sockets more durable and lightweight.
Smart manufacturing and IoT (Internet of Things) are other game-changers. IoT-enabled devices can monitor machinery in real-time, predicting maintenance needs and minimizing downtime. This technology improves efficiency and ensures that production lines operate at peak performance.
Moreover, 3D printing is beginning to play a role in prototyping and small-batch manufacturing. This technology allows for faster turnaround times and customization, meeting the growing demand for personalized products. As technology continues to advance, manufacturers that embrace these innovations will maintain a competitive edge in the global market.
Challenges Facing Manufacturers in a Globally Competitive Market
Manufacturers face numerous challenges in today’s competitive environment. Rising raw material costs are a significant concern. The prices of steel and other essential materials have fluctuated dramatically, impacting profit margins. And here’s the problem: Balancing cost and quality is no easy feat. Manufacturers must ensure their products meet high standards while remaining affordable.
Supply chain disruptions, often caused by geopolitical tensions or natural disasters, further complicate matters. Delays in material delivery can halt production, leading to missed deadlines and dissatisfied customers. Additionally, changing consumer expectations demand constant innovation. Buyers expect tools that are not only durable but also eco-friendly and customizable.
Effective communication is another challenge, especially for manufacturers offering OEM services. Misunderstandings regarding specifications or lead times can damage relationships with clients. To succeed, manufacturers must address these challenges head-on by improving their processes, investing in technology, and building resilient supply chains.
How Do Global Trade Policies Impact Impact Socket Manufacturers?
Trade policies have a profound effect on the impact socket industry. Tariffs, for example, can significantly increase production costs, making it harder for manufacturers to compete on price. Recent trade wars have disrupted supply chains, forcing businesses to seek alternative markets or suppliers. Here’s why it matters: Manufacturers that rely heavily on exports are particularly vulnerable to these changes.
Free trade agreements, on the other hand, can create opportunities by reducing barriers to entry in foreign markets. These agreements enable manufacturers to expand their reach and build relationships with international clients. However, navigating the complexities of trade policies requires expertise and careful planning.
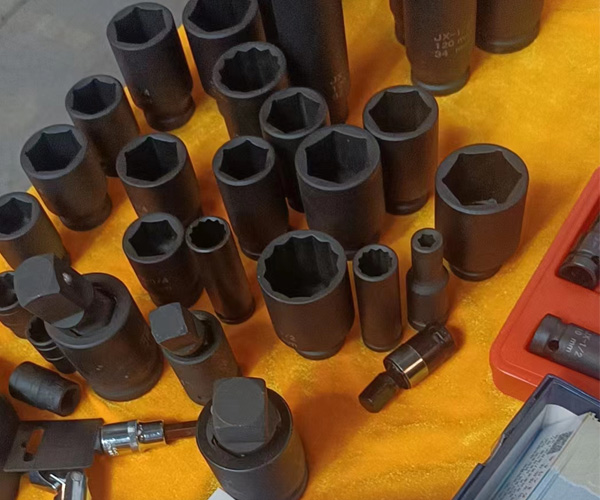
Understanding the nuances of these policies is crucial for manufacturers looking to stay competitive. Businesses must remain informed about changes in regulations and adapt their strategies accordingly. By doing so, they can minimize risks and capitalize on new opportunities in the global market.
Price Wars: The Impact on Manufacturers’ Profit Margins
Price wars are a common consequence of global competition, and their impact on profit margins can be devastating. Manufacturers often feel compelled to lower their prices to stay competitive, but this approach can lead to a race to the bottom. Here’s the kicker: Consistently slashing prices is not a sustainable strategy. It can erode profitability and compromise product quality.
Balancing affordability with quality is critical. Manufacturers must find ways to optimize their operations, whether through automation, bulk purchasing of materials, or streamlining supply chains. Additionally, offering value-added services, such as OEM customization or extended warranties, can justify higher prices and attract discerning clients.
Instead of engaging in price wars, some manufacturers focus on building strong relationships with clients. Long-term partnerships often lead to repeat business and referrals, providing a more stable revenue stream. By prioritizing quality and customer satisfaction, manufacturers can maintain healthy profit margins without sacrificing their competitive edge.
FAQ Section
What makes impact sockets different from standard sockets?
Impact sockets are designed to withstand high torque levels and are made from durable materials like chrome-molybdenum steel. They are thicker and stronger than standard sockets, making them ideal for heavy-duty applications.
How has global competition changed the impact socket industry?
Global competition has increased the demand for cost-efficiency, innovation, and quality. Manufacturers must adapt to changing consumer expectations and leverage technology to stay competitive.
What are the benefits of OEM services in manufacturing?
OEM services allow clients to customize products to their specifications, enhancing brand differentiation and customer satisfaction.
How can small manufacturers compete with global giants?
Small manufacturers can focus on niche markets, prioritize quality, and build strong client relationships to differentiate themselves from larger competitors.
What role does sustainability play in manufacturing today?
Sustainability is becoming increasingly important as consumers and regulators demand eco-friendly practices. Manufacturers adopting green initiatives gain a competitive advantage in the global market.