What’s the Challenge?
Most individuals handling automotive repairs or industrial machinery know impact wrenches deliver powerful torque that loosens and tightens stubborn nuts and bolts far more efficiently than manual tools. Yet one crucial detail often gets overlooked: the type of socket you attach makes a world of difference. Many beginners assume any old socket will do, but that can lead to cracked tools, unsafe working conditions, and damaged fasteners.
Why Focus on Socket Choice?
You might be wondering, why not just grab a random socket and go? The truth is that impact wrenches generate far more stress on a socket than manual wrenches do, and the right socket ensures safety, longevity, and accuracy. By selecting an impact-rated socket specifically built for the tool’s intense torque and vibration, you’ll preserve both the wrench and the fasteners, ultimately saving time and money.
Building Trust with Proven Expertise
This guide walks you through everything: how impact wrenches work, why impact sockets matter, what materials and designs to look for, and how proper maintenance extends tool life. Here’s the deal, after reading this, you’ll feel confident picking sockets that handle high loads gracefully. Ready to dive in?
Understanding How an Impact Wrench Works
The Science of Torque and Impact
An impact wrench uses a rotational hammering action combined with sudden torque bursts. Unlike a manual wrench that relies on steady, continuous force, impact wrenches deliver repeated, high-intensity strikes that effectively break loose corroded or over-torqued bolts. Now listen, the internal mechanism hammers rapidly, which multiplies force and reduces the physical effort required by the user. This is why these tools excel at everything from automotive maintenance to heavy construction.
Impact Wrenches vs. Regular Wrenches
Conventional wrenches rely on continuous applied force. In contrast, an impact wrench’s hammer-and-anvil system stores energy and releases it in brief, powerful increments. This difference changes the demands placed on sockets. Standard sockets, designed for even, predictable torque, may fail under the wrench’s dynamic hammering. Guess what, that is exactly why specialized impact sockets are a must.
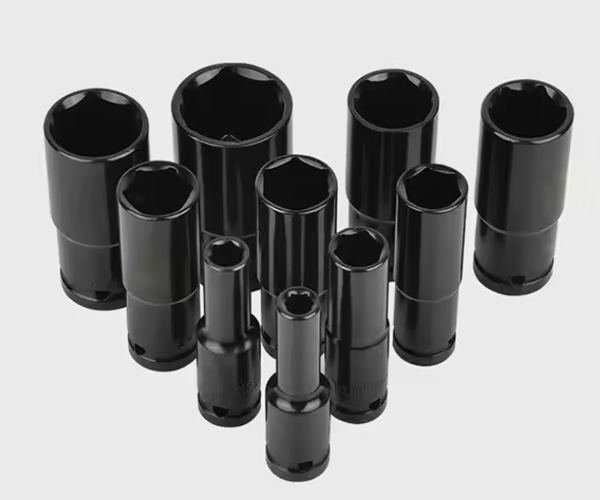
Material Stress and Socket Requirements
These abrupt, high-energy shocks mean sockets experience stress at multiple points, not just steady turning force. Impact sockets must be tougher, often made from chrome-moly steel or similar alloys, to endure these forces without fracturing. By understanding this mechanical principle, you’re better equipped to choose the proper socket that ensures both performance and safety. You might be wondering, can’t I just use any strong socket? Trust us, the internal mechanics say otherwise.
Types of Sockets: Standard vs. Impact Sockets
Defining Standard Sockets
Standard sockets are usually made from chrome-vanadium steel and coated with a polished finish. These look shiny and sleek, perfect for hand tools and everyday maintenance tasks. Here’s the deal, they are meant for steady torque rather than sudden impacts, and while they handle typical jobs fine, the shock loads from an impact wrench may cause them to crack or shatter.
The Special Features of Impact Sockets
Impact sockets are made from tougher alloys, often darker in appearance due to a black oxide or phosphate finish. They have thicker walls to absorb energy spikes and a more ductile composition that flexes slightly under stress rather than snapping. Think about it, that flexibility is a safety feature: it helps prevent fragments of metal flying around if too much force is applied.
Choosing the Right Type
You might be wondering, can a standard socket handle the occasional impact use? While it might survive one or two tries, repeated exposure risks both safety and tool longevity. Impact sockets, by design, match the torque patterns of these power tools. Ultimately, choosing an impact socket ensures consistent performance, long-term durability, and a safer working environment. Basically, sticking with impact-rated tools is the smarter path.
Materials Used in Impact Sockets
The Alloys that Matter
Impact sockets are often forged from chrome-molybdenum steel or similarly resilient alloys. Compared to regular chrome-vanadium, chrome-moly offers superior tensile strength and improved toughness. Now listen, these alloys undergo rigorous heat treatment processes that help them maintain structural integrity under extreme torque pulses.
Heat Treatments for Durability
During manufacturing, impact sockets undergo hardening processes where they’re heated and cooled at controlled rates. This not only boosts hardness but also improves impact resistance and longevity. Here’s the deal, without such treatment, sockets would quickly deform or crack under intense repetitive shocks.
Corrosion-Resistant Finishes
Impact sockets often feature black oxide, manganese phosphate, or similar finishes to fight off rust and corrosion. This extends their service life, ensuring they remain strong, safe, and reliable. You might be wondering, what’s with the darker color? That finish isn’t just aesthetic—it’s a corrosion barrier that keeps your tools ready for action. By focusing on robust materials, carefully chosen alloys, and protective finishes, manufacturers ensure impact sockets stand up to the punishing demands of high-powered tools. Guess what, investing in quality materials pays off long-term.
Design Features of Impact Sockets
Thicker Walls and Optimal Geometry
Impact sockets have noticeably thicker walls than standard sockets. This isn’t just for show: that extra metal mass helps spread out stress, reducing the chance of splitting. Think about it, thicker walls mean greater capacity to handle sudden torque bursts without failing. Additionally, the internal geometry is fine-tuned for secure grip and proper torque distribution.
Surface Finishes That Improve Grip
The black oxide or phosphate finish does more than prevent rust; it can also provide a slightly textured surface that reduces slippage. Here’s the deal, when you’re dealing with high-torque applications, every fraction of grip matters. Slippage increases wear and can damage both the tool and the fastener.
Specialized Variants: Deep and Swivel Sockets
You might be wondering, what if I need to reach recessed fasteners or work in tight angles? That’s where deep well sockets and swivel sockets come into play. Deep sockets fit longer bolts, while swivels adjust angles to reach awkward spots. Each design refinement exists to handle the complex realities of working with high-powered tools. Ultimately, these thoughtful design features let you tackle a range of jobs efficiently and safely. Now listen, investing in specialized impact sockets expands your toolbox capabilities.
Safety Considerations
The Risks of Using Standard Sockets on Impact Tools
Standard sockets are not built to withstand the sudden jolts from an impact wrench. Using them can lead to socket shattering, sending sharp metal shards flying. Think about it, that’s dangerous not only for you but also anyone nearby.
Personal Protective Equipment
Always wear safety glasses, gloves, and sometimes even face shields when working with high-torque tools. Here’s the deal, even when using proper impact sockets, it’s best to anticipate potential failures. PPE acts as your last line of defense if something goes wrong.
Proper Fit and Torque Management
Selecting the correct socket size ensures a snug fit that prevents the fastener from rounding off. It also helps maintain stable torque application. You might be wondering, what about torque ratings and guidelines? Following the tool manufacturer’s recommendations helps avoid over-stressing sockets and bolts. Never exceed the rated capacity of your equipment. Guess what, by prioritizing safety, you ensure a smooth, hazard-free working environment and extend the life of your tools.
How to Identify an Impact Socket
Visual Cues: Color and Finish
Impact sockets typically come in a dark, matte finish rather than a shiny chrome. Now listen, if you see a glossy, polished surface, it’s likely a standard socket. The darker finish usually indicates a more ductile material and corrosion-resistant coating.
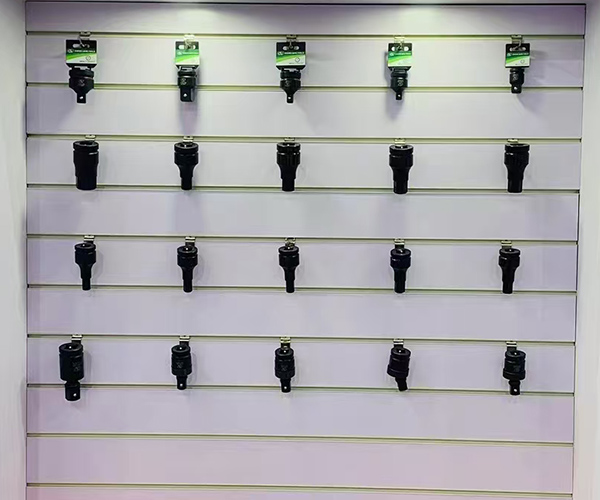
Markings and Engravings
Look for the word “Impact” or other brand-specific indicators engraved on the socket. Manufacturers know you need quick identification, so they mark these tools accordingly. You might be wondering, do I always trust color alone? While it’s a strong indicator, also rely on labeling, packaging, or product documentation to confirm.
Packaging and Manufacturer’s Website
Check product descriptions, manuals, and manufacturer websites. Here’s the deal, reputable brands provide clear guidance, stating explicitly if their sockets are impact-rated. Confirming authenticity ensures you get the quality and performance you expect. By recognizing these markers, you avoid the guesswork and confidently equip your impact wrench with the right socket.
Common Applications and Uses
Automotive Repairs
Impact wrenches paired with impact sockets excel in changing tires, dealing with suspension components, and loosening stubborn engine bolts. Think about it, no more struggling with rusted lug nuts. The high torque of your wrench and durability of your sockets handle these tough jobs easily.
Industrial and Construction Settings
Steel framing, industrial machinery assembly, and pipeline maintenance often involve massive, tightly torqued fasteners. Impact sockets shine here, handling repetitive high-stress tasks without breaking down. You might be wondering, can they handle large infrastructure projects? Absolutely.
Home DIY Projects
Even at home, from assembling a deck to fixing a lawnmower, having an impact wrench and proper sockets saves time and frustration. Here’s the deal, they turn hours of elbow grease into a quick, controlled, and efficient process. Whether you’re a weekend warrior or a professional mechanic, these tools help complete tasks faster, safer, and with more consistent results. Guess what, once you experience the ease, you’ll never look back.
Drive Sizes and Socket Types for Impact Wrenches
Common Drive Sizes
Impact wrenches come in various drive sizes: 1/4″, 3/8″, 1/2″, 3/4″, and even 1″ drives for heavy-duty tasks. Now listen, matching your socket’s drive size to the impact wrench is critical. A mismatch wastes torque or risks tool damage.
Specialty Impact Sockets
Deep well sockets reach longer bolts, universal joints pivot around obstacles, and impact-rated adapters bridge between different drive sizes. You might be wondering, what if I need more flexibility? Investing in a set that includes extensions, swivels, and specialty shapes covers more scenarios.
Selecting the Right Profile
Consider the fastener’s shape and location. Sometimes a short socket works best in tight spaces; other times you need a deep socket to get a proper grip. Here’s the deal, having a range of socket types on hand allows you to tackle diverse tasks without improvisation. By carefully selecting drive sizes and specialized pieces, you ensure optimal performance every time. Guess what, it’s all about the right tool for the right job.
Compatibility with Different Brands and Tools
Matching Brands and Models
While sockets are generally standardized, certain brands may have slight variations in tolerances. Think about it, sticking with the same reputable brand as your impact wrench often ensures a perfect fit. However, mixing brands isn’t usually a deal-breaker if you choose quality.
Interchangeability and Quality Standards
Industry standards help ensure that most impact sockets fit universally across wrenches. Here’s the deal, as long as drive sizes match and the socket’s quality meets high-impact standards, brand mixing is acceptable. Just confirm that the socket’s rating matches your tool’s torque output.
Warranty and Reputation
You might be wondering, should I trust an unknown brand? Reputable manufacturers back their products with warranties and customer support. Reliable suppliers often test their tools extensively. Investing in well-reviewed brands ensures you get the durability and performance you pay for. Now listen, it’s about making an informed choice that keeps your operations running smoothly.
Tips for Maintaining and Caring for Impact Sockets
Cleaning and Storage
After each use, wipe down sockets to remove debris and moisture. Store them in a dry place, ideally on socket rails or in foam organizers. Here’s the deal, this simple practice prevents rust and prolongs their lifespan.
Regular Inspections
Check for cracks, chips, or deformation. If a socket shows signs of wear, retire it. You might be wondering, won’t a small chip matter? Even minor flaws compromise integrity under high torque loads.
Lubrication and Corrosion Prevention
Occasional light lubrication can keep connection points smooth. Keep sockets dry and clean to avoid corrosion. Think about it, a well-maintained set of impact sockets will serve you reliably for years, delivering consistent performance while safeguarding your investment. Guess what, caring for your tools pays dividends long-term.
Cost and Value Considerations
Price Differences Between Standard and Impact Sockets
Impact sockets may cost more, but you get enhanced durability and safety. Now listen, the initial investment pays off when you aren’t constantly replacing broken standard sockets.
Long-Term Savings
Quality impact sockets last longer under high-stress conditions. You might be wondering, what’s cheaper: buying multiple standard sockets over time or one durable impact set upfront? The latter usually proves more economical.
Balancing Quality and Budget
When starting out, prioritize frequently used sizes if a full set feels expensive. Over time, expand your collection. Here’s the deal, investing in key sizes ensures you always have the right tool for critical jobs. By weighing initial cost against long-term reliability, you find the sweet spot that meets both your performance needs and budget constraints. Guess what, reliable tools are never a regret.
Troubleshooting Common Issues
Slipping or Rounding Fasteners
If your socket slips, verify you’re using the correct size and type. Think about it, a worn or incorrect socket can damage the fastener head.
Identifying When It’s Time to Upgrade
You might be wondering, how do I know it’s time for new sockets? Look for signs of wear like cracks, rust, or chipped edges. If your current sockets fail repeatedly, consider upgrading to higher quality, impact-rated sets.
Adjusting Torque and Technique
Sometimes trouble comes from user technique or incorrect torque settings rather than the socket itself. Here’s the deal, follow torque specifications, use proper lubrication, and ensure your impact wrench is in good working order. Resolve these issues, and you’ll have a smoother, more efficient workflow that prevents unnecessary damage. Now listen, troubleshooting often leads to improved practices and better results.
Alternative Solutions and When Not to Use an Impact Socket
Knowing the Limits of Impact Sockets
While impact sockets handle tough jobs, they’re not always necessary. Think about it, for simple, low-torque tasks with a handheld ratchet, standard sockets suffice.
Manual Torque Wrenches and Breaker Bars
In situations requiring precise torque control or delicate components, a manual torque wrench provides exacting force levels. You might be wondering, what if I’m dealing with extremely tight fasteners that don’t respond well to impact force? A breaker bar, applying steady manual leverage, might be a safer or more controlled choice.
Specialized Tools for Specific Tasks
At times, other specialized tools outperform impact wrenches altogether. Here’s the deal, always match the tool to the job, and don’t rely solely on impact sockets for every scenario. By understanding their limitations, you ensure you’re not misusing these tools where a gentler or more precise approach would be better. Guess what, versatility matters.
Conclusion and Final Recommendations
Summarizing Key Points
Choosing the right socket for an impact wrench isn’t just about compatibility; it’s about safety, efficiency, and protecting your investment. You might be wondering, did we cover everything? We explored the science behind impact wrenches, the necessity of impact-rated sockets, their design features, and proper maintenance.
Emphasizing the Main Message
Here’s the deal, using an impact-rated socket ensures you get the best performance out of your impact wrench while minimizing risks. With the right sockets, you maintain reliable torque delivery, avoid damaged fasteners, and keep your work environment safer.
Actionable Takeaway and Emotional Connection
Now that you know what to look for, why not invest in quality impact sockets and enhance your workflow? Guess what, this decision brings peace of mind and confidence to every task. By making informed choices, you nurture trust in your tools, building a more productive and satisfying work experience.
FAQ
What makes an impact socket different from a standard socket?
Impact sockets use tougher alloys like chrome-moly steel and have thicker walls. These design differences let them handle the sudden shocks and high torque of impact wrenches without fracturing.
Can I use standard sockets on my impact wrench for small jobs?
You might be wondering, is it okay just once in a while? While you might get away with it occasionally, it’s risky. Standard sockets can crack under impact forces, posing a safety hazard and potentially damaging tools and fasteners.
How do I maintain my impact sockets?
Clean them after each use, store them in a dry place, and inspect regularly for wear or damage. Replacing worn sockets promptly ensures consistent, safe performance.
Are impact sockets more expensive than regular ones?
They often cost a bit more, but the investment pays off through their durability, longer lifespan, and reduced replacement costs. Here’s the deal, you save money long-term by avoiding frequent replacements.
Do I really need special finishes and coatings?
Yes. The black oxide or phosphate finishes protect sockets from corrosion and improve grip. This helps maintain their structural integrity, ensuring reliable performance and safety with every use.
Ready to elevate your tool selection?
Connect with KOLARWIN TOOLS today. Whether you need high-quality hand tools, specialized automobile repair kits, or customized woodworking solutions, we’re here to deliver on your unique requirements. Contact us now at info@kolarwin.com to discuss your OEM needs, request product samples, or learn more about our competitive pricing and reliable global shipping. Let’s build a partnership that drives long-term success.