1. Introduction
When it comes to high-performance tools used in heavy-duty applications, impact sockets are essential. Unlike regular sockets, impact sockets are engineered for durability and resilience, designed specifically to withstand the rigorous demands of impact tools and pneumatic tools. Used frequently in industries such as automotive, construction, and manufacturing, these tools are critical in settings where high torque and impact forces are applied. As a result, they’re constructed from high-strength materials, such as chrome molybdenum steel, to ensure safety and durability even under extreme conditions.
Impact sockets stand out from standard sockets not only because of their materials but also due to the precision and customization options available. Many professionals find that having custom impact sockets improves productivity by providing a tailored fit and performance for specific tasks. Customization ensures that the socket’s design, size, and even material are adapted to fit unique needs, which can be invaluable in certain industries. China Customized Impact Socket Set Factory Manufacturers specialize in creating these precise, application-specific tools, offering a wide range of customization options to match the needs of varied industries. In this article, we’ll dive into how impact socket customization works, from the initial design stages to production and quality assurance.
2. Understanding the Customization Process for Impact Sockets
Customizing impact sockets is a multi-step process that starts with a thorough understanding of the client’s specific requirements. Unlike off-the-shelf tools, customized impact sockets are tailored to fit precise applications and often need to meet rigorous standards for performance and safety. This process involves initial consultations, selecting appropriate materials, and fine-tuning designs based on the intended usage and environment. Here’s a closer look at each step involved.
Initial Consultation: Setting Customization Goals
Every customization begins with a detailed consultation where the manufacturer and client discuss the project’s needs and objectives. This step is critical, as it helps factory manufacturers in China understand the unique demands the socket will face. Key questions include:
- What is the application? For instance, is the socket going to be used for high-torque automotive applications or heavy industrial use?
- What are the specific requirements? These may include the socket’s length, diameter, wall thickness, and the type of drive (e.g., square, hex).
- Are there any environmental considerations? Certain jobs may require sockets resistant to corrosion or extreme temperatures.
Understanding these aspects allows manufacturers to propose the most suitable design options and material selections. Factories specializing in impact sockets for diverse sectors such as automotive repair, manufacturing, and heavy machinery are often equipped with in-house experts who guide customers through this initial planning phase, ensuring the final product aligns perfectly with the client’s objectives.
Selecting Materials and Treatments
Material selection is a crucial element in the customization process. Most impact sockets are crafted from high-strength alloys, with chrome molybdenum steel being a popular choice due to its superior strength and impact resistance. Other materials, like vanadium steel, may be selected depending on the specific application and cost considerations.
In addition to choosing a base material, manufacturers often apply special treatments to enhance the durability and longevity of the socket. Heat treatment is one such process that significantly improves the hardness and strength of the metal. Depending on the desired finish and resistance qualities, the factory may also add surface coatings such as black oxide or phosphate, which help protect against rust and wear. These treatments are particularly important for sockets used with impact tools, as the added durability extends the tool’s life and ensures safe operation.
By carefully choosing and treating materials, manufacturers provide customized impact sockets that deliver optimal performance under specific work conditions, be it in extreme heat, heavy torque applications, or in environments prone to moisture and corrosion.
3. Design Specifications and Considerations
Creating a custom impact socket involves making precise design adjustments that can greatly influence performance, safety, and ease of use. The design phase is where each socket type, material, and feature is carefully evaluated to ensure the tool meets the client’s needs.
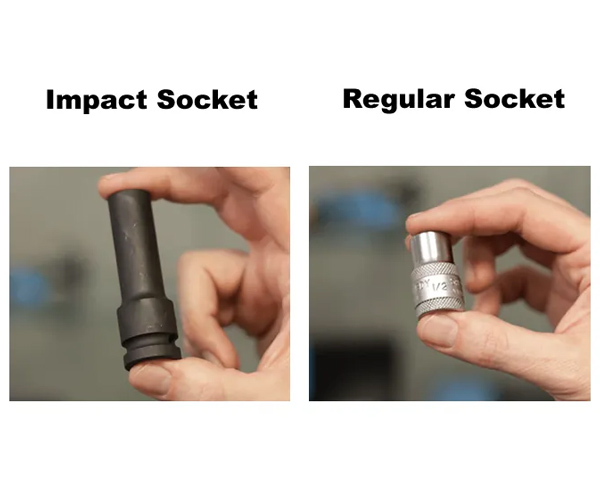
Key Design Factors for Custom Impact Sockets
The most important design factors include the socket’s size, wall thickness, drive type, and overall dimensions. For instance, drive sizes can range from smaller, 1/4-inch drives suitable for lighter applications, to larger 3/4-inch or even 1-inch drives designed to withstand heavy impact forces in industrial settings. The right drive size ensures compatibility with the client’s existing tools and provides the necessary torque for the job.
Another essential consideration is wall thickness, which directly impacts the socket’s strength and durability. Thicker walls provide greater resistance to splitting under impact, but may not fit in tighter spaces, especially for deep sockets used on recessed fasteners. Balancing wall thickness with accessibility requirements is key in creating a practical, effective tool.
Specialized Design Features
To further enhance functionality, manufacturers may incorporate specialized design features into customized impact sockets. Deep sockets or thin-wall sockets are common requests, especially in automotive work where bolts may be hard to reach. Thin-wall sockets provide a tighter fit for recessed or enclosed bolts without sacrificing too much strength, while deep sockets are ideal for accessing bolts set farther into a structure.
Additionally, clients may request sockets with hex or star-shaped configurations, depending on the type of fasteners used in their projects. Some customization projects include safety-focused features, like locking pins or anti-slip grooves that help prevent accidental slipping or disengagement, which can be crucial in high-torque applications where tool safety is paramount.
4. Manufacturing Techniques in Socket Customization
Once the design is finalized, the socket moves to the manufacturing phase, where precise techniques bring the customizations to life. The two primary manufacturing methods for impact sockets are forging and casting, though CNC machining and other precision methods are also frequently used.
Forging and Casting
Forging is often preferred for impact sockets due to its strength benefits. In this process, the metal is heated and shaped using a hammer or press, creating a socket with a tightly packed grain structure. Forged sockets are highly durable and impact-resistant, making them ideal for high-torque applications.
Alternatively, casting involves pouring molten metal into a mold to form the socket. While casting is typically more cost-effective, it may not offer the same level of durability as forging, especially for heavy-duty applications. However, for certain designs or lower-impact applications, casting may be an ideal choice due to its flexibility and lower production costs.
Precision Machining and Finishing
After the initial forging or casting, sockets are often machined to ensure precise tolerances and a smooth finish. CNC machining is commonly used to achieve exact dimensions and fine details, allowing for features like intricate grooves or specific drive configurations.
Finally, customized impact sockets are finished with surface treatments that add durability and protect the tool against wear and corrosion. Options such as black oxide and phosphate coatings not only improve appearance but also add a layer of protection, making these tools better suited for prolonged use in demanding conditions.
Quality Control and Testing
Quality assurance is a critical aspect of custom socket manufacturing. Each socket undergoes load testing, hardness testing, and fatigue testing to verify that it meets industry standards and can safely withstand the specified loads. Leading manufacturers often adhere to ISO and ANSI standards to guarantee that their sockets deliver consistent quality, reliability, and safety. By rigorously testing each tool, factories ensure that the final product not only meets but exceeds client expectations.
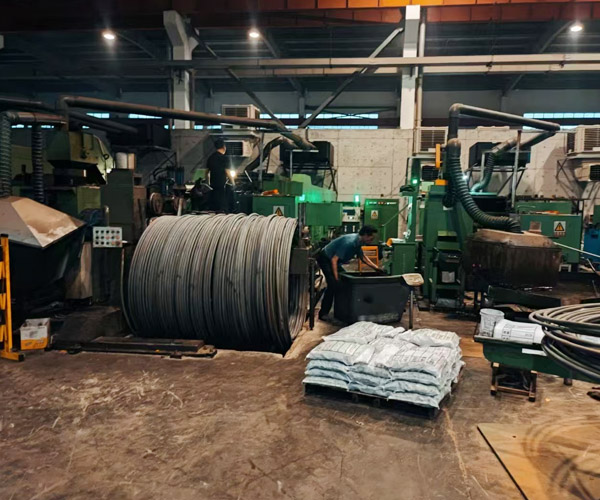
5. Types of Customizations Available
When it comes to impact socket customization, the possibilities are nearly endless. Here are some of the most commonly requested customizations that China Customized Impact Socket Set Factory Manufacturers offer to meet diverse application requirements.
Size and Length Customizations
Clients often require specific socket lengths to accommodate unique fasteners or hard-to-reach bolts. Deep sockets are frequently customized for clients in the automotive and construction sectors, where bolts are often recessed or extended within equipment. Customizing the socket diameter and length enables the client to access fasteners without compromising on strength or stability.
Surface Finish and Coatings
Surface coatings are another common area of customization. Coatings such as black oxide or zinc plating are ideal for impact sockets that will encounter high humidity or corrosive substances. These finishes not only prevent rust but also provide a smooth surface that reduces friction during use, thereby extending the life of the socket.
Drive Type and Configuration Adjustments
Clients may require specific drive types and configurations to match the tools they use. For instance, square or hex drive types can be customized to ensure a tight fit with impact wrenches or pneumatic tools. For specialized applications, some clients request angled or offset drives that allow for greater flexibility and access in confined spaces.
6. Specialized Impact Socket Applications and Custom Requirements
Custom impact sockets are often essential in industries with unique application needs. Here’s how customized solutions benefit sectors like automotive, oil and gas, and construction.
Automotive and Heavy Machinery
In the automotive industry, impact sockets must endure high torque levels when loosening or tightening bolts on engines, tires, and heavy machinery. Custom sockets designed for high impact resistance are necessary to avoid cracks and splits. Chrome molybdenum steel is often the preferred material here, as it can handle the demanding conditions associated with automotive work. Custom sockets in this sector may also require additional length or unique shapes, like star-shaped sockets, for compatibility with vehicle-specific fasteners.
Oil, Gas, and Mining Sectors
Sockets used in oil, gas, and mining applications face some of the harshest environments. Corrosion resistance is key, as these sockets are frequently exposed to moisture, chemicals, and high-pressure conditions. Factories specializing in this sector prioritize custom materials and coatings that prevent rust and withstand heavy use. Custom sockets for this industry are typically designed with robust thickness and are often treated with high-performance finishes like phosphate to enhance durability.
Construction and Industrial Use
In construction and other industrial settings, impact sockets are used with pneumatic tools for assembly and repair tasks. Customization for this sector often focuses on durability and compatibility with large, high-powered tools. Custom sockets may include deep sockets or thin-wall designs to address the variety of fasteners encountered in large-scale construction projects.
7. Cost Factors in Impact Socket Customization
The cost of customized impact sockets varies significantly based on several factors, from material selection to design complexity. Here are some of the main cost considerations:
Material and Design Complexity
The choice of material has a major impact on cost, with options like chrome molybdenum steel generally being more expensive than standard steel due to its superior strength and durability. Additionally, complex designs involving unique shapes, intricate features, or specialized drive types increase manufacturing costs, as they require more time and precision to produce.
Manufacturing Method and Finishing
As mentioned, forging is more expensive than casting but provides greater durability. Likewise, additional processes such as CNC machining, heat treatment, and surface finishing all contribute to the final cost of the custom socket. Each treatment adds a layer of durability, so clients need to weigh these options based on the anticipated lifespan and application demands.
Volume and Lead Time
Manufacturers often offer discounted rates for bulk orders, making it more economical for clients to order larger quantities of custom impact sockets. However, if a client requires expedited production, they may face higher costs due to the need for prioritized manufacturing and testing.
8. Quality Assurance in Custom Impact Sockets
Quality assurance is paramount in custom impact socket manufacturing. Clients rely on manufacturers to provide safe, reliable tools that won’t fail under pressure. Leading manufacturers implement stringent testing procedures to ensure compliance with industry standards.
Testing and Compliance Standards
Impact sockets are tested for hardness, load tolerance, and wear resistance. Many manufacturers adhere to recognized standards such as ISO and ANSI, ensuring that each socket meets a baseline of quality and durability. Testing may include tensile strength tests to ensure the socket can withstand the intended force and impact resistance tests to assess its performance in high-impact applications.
Ensuring Longevity and Performance
In addition to quality testing, regular maintenance and inspection are essential to extending the lifespan of impact sockets. Clients are advised to inspect sockets periodically for any signs of wear or damage and follow recommended maintenance practices. Custom impact sockets designed with high-quality materials and tested for durability are more likely to provide long-term performance, even under demanding conditions.
9. Steps to Order Custom Impact Sockets
Ordering customized impact sockets involves a few key steps to ensure clients receive the product they need.
Preparing a Customization Request
Clients should provide detailed information on their specifications, including the intended application, required dimensions, and any unique requirements. This initial step sets the stage for a smooth customization process and allows the manufacturer to understand precisely what the client needs.
Communicating with Manufacturers
Clear communication with manufacturers is crucial. Clients should discuss all aspects of the customization, from material choices to design preferences. Reputable manufacturers will guide clients through this process, helping to clarify specifications and suggesting improvements based on their experience.
Timeline and Delivery Expectations
Customization often takes longer than standard production, so clients should inquire about lead times and plan their orders accordingly. While expedited options are sometimes available, clients should consider allowing ample time for production to avoid delays.
10. Choosing the Right Supplier for Customized Impact Sockets
Selecting the right supplier for customized impact sockets can make a significant difference in the quality and reliability of the final product.
Assessing Supplier Capabilities
Clients should evaluate the supplier’s experience, technical expertise, and facility capabilities. A reliable factory will be transparent about their manufacturing process and provide references or examples of past projects.
Reviewing Case Studies and Customer Feedback
Researching past customer feedback can provide insights into the supplier’s reliability, quality standards, and customer service. Clients may also ask for case studies that showcase the manufacturer’s experience with similar projects.
Ensuring Post-Purchase Support and Warranties
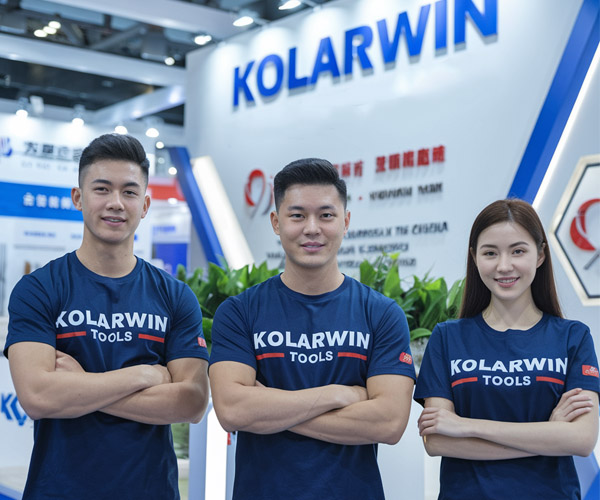
Many manufacturers offer warranties or after-sales support for custom sockets. Clients should review warranty options and inquire about the availability of replacement parts, repairs, and ongoing support.
11. Conclusion: Benefits of Custom Impact Sockets
Customized impact sockets offer a range of benefits that make them indispensable for specialized tasks. From increased durability to precise fit and performance, custom sockets are a worthwhile investment for professionals in heavy-duty fields. When working with reputable China Customized Impact Socket Set Factory Manufacturers, clients receive a product that not only meets but often exceeds their expectations, providing enhanced efficiency, safety, and longevity.
Ready to Customize Your Impact Sockets?
At KOLARWIN, we specialize in creating durable, precision-engineered impact sockets tailored to meet the toughest demands. Whether you need custom dimensions, special coatings, or unique socket designs, our team at KOLARWIN is here to provide high-quality, customized solutions for all your industrial needs. Trusted by professionals across North America, Europe, and Asia, we’re committed to delivering reliable, high-performance tools with fast, efficient service.
Contact us today to discuss your customization requirements, request a quote, or learn more about our comprehensive socket manufacturing options. Let’s equip your team with the tools they need for success!
Visit us at WWW.KOLARWIN-TOOLS.COM or reach out info@kolarwin.com directly.