Introduction to Impact Socket Wholesale and Customization
Impact sockets are a specialized type of socket designed to withstand the high torque and pressure often associated with heavy-duty industrial applications. Unlike standard sockets, which are typically used for lighter tasks, impact sockets are essential for anyone using high-powered tools, such as pneumatic or electric wrenches, in tasks that require substantial force. These sockets are commonly seen in industries like automotive repair, construction, and manufacturing, where the combination of power tools and intense work demands tools that are both durable and safe to use.
The concept of customizing impact sockets has gained popularity as industries recognize the advantages of tools specifically tailored to their unique requirements. Customizing impact sockets allows businesses to create sockets that meet their precise needs—whether that involves unusual sizes, specific torque capabilities, enhanced durability, or even aesthetic details like branded colors and engravings. Customized impact sockets help companies enhance operational efficiency, meet specific compliance requirements, and reduce downtime caused by tool failure. Furthermore, purchasing impact sockets in wholesale quantities provides businesses with cost savings and consistency across their toolkits, making it an attractive option for industries that rely on these tools regularly.
In this article, we will dive deep into what makes impact sockets unique, why customization matters, and how the wholesale customization process can be leveraged by businesses to meet their specific needs. We’ll also cover the advantages of impact socket customization, outline the customization process, and discuss what to consider when choosing the right supplier for impact socket wholesale and customization services.
Understanding Impact Sockets
Impact sockets are crafted with durability and high-stress applications in mind. Unlike standard sockets, which are more suitable for hand tools, impact sockets are built to handle the sudden bursts of force generated by impact wrenches and other power tools. These sockets feature thicker walls, specialized materials, and specific designs that make them ideal for intense applications, including high-torque automotive repairs, industrial equipment maintenance, and construction projects.
What Are Impact Sockets?
Impact sockets are sockets engineered specifically for power tools that deliver high-torque output. They are designed to withstand the heavy, repetitive strikes that come from impact wrenches, drills, and other powerful equipment. This makes them a crucial component for industries where safety, efficiency, and durability are paramount. Typically made from materials like chrome molybdenum or carbon steel, impact sockets are more resilient and can absorb greater levels of torque without cracking or wearing down.
Unlike regular sockets, impact sockets are commonly coated in black oxide or phosphate to prevent corrosion and wear, which helps them maintain their strength over time. This protective coating also provides a non-reflective surface, making them easier to use in low-light environments and preventing issues like rust from diminishing their lifespan. In short, impact sockets are designed with a specialized combination of materials and structural elements to withstand the punishing conditions of high-torque applications.
Key Differences Between Impact Sockets and Standard Sockets
While impact sockets and standard sockets may appear similar at first glance, they differ significantly in terms of material, design, and intended usage. Here are some of the key distinctions:
- Material Strength: Impact sockets are generally made from tougher materials such as chrome molybdenum or high-grade carbon steel. Standard sockets, by contrast, are often made of chrome vanadium, which is less durable under high-impact conditions.
- Wall Thickness: Impact sockets have thicker walls than standard sockets, allowing them to absorb the intense forces generated by power tools without breaking. This design difference ensures that impact sockets can endure higher stress levels.
- Heat Treatment and Hardening: Many impact sockets undergo specific heat treatments to improve their strength and durability. Processes like quenching and tempering increase the hardness of impact sockets, helping them resist deformation even under high torque.
- Protective Coating: Standard sockets typically have a polished chrome finish, whereas impact sockets usually feature a black oxide or phosphate finish. These coatings not only prevent corrosion but also reduce the risk of tool slippage during operation.
Common Applications for Impact Sockets
Impact sockets are used across a range of industries where high-torque applications are common. Below are some of the most frequent applications:
- Automotive Industry: Mechanics rely on impact sockets for tasks like tire changes, suspension work, and engine repairs, where they require sockets that can withstand the high torque of power wrenches.
- Construction and Heavy Machinery: Construction workers and equipment technicians use impact sockets to handle bolts and fasteners on heavy machinery. In these environments, the durability of impact sockets is essential due to the high demands placed on the tools.
- Manufacturing and Industrial Applications: In factories and production facilities, impact sockets are essential for the maintenance and assembly of machinery. Their durability and resistance to wear make them ideal for frequent use in industrial settings.
Impact sockets have become an industry standard in any application where traditional sockets may fail under heavy use. The growing demand for customization in this area is driven by the need for tools that not only withstand rigorous use but are also tailored to the specific requirements of different industries.
Reasons to Customize Impact Sockets
Customized impact sockets offer a range of advantages that extend beyond what standard options can provide. The decision to customize impact sockets is often motivated by the need for enhanced performance, cost savings, and even branding opportunities. Here are some of the most common reasons why businesses choose to invest in custom impact sockets.
Performance Enhancements
One of the key reasons for customizing impact sockets is to achieve superior performance tailored to specific needs. Customizing allows for improvements in areas such as durability, torque resistance, and wear tolerance, ensuring that the tool performs optimally in challenging environments. With custom impact sockets, companies can specify attributes like material strength, wall thickness, and coating options, creating a socket that can handle intense applications without risking deformation or breakage. For industries that rely on heavy-duty tools, these performance enhancements help reduce downtime and increase productivity.
Meeting Specific Industry Standards and Regulations
Certain industries operate under strict regulatory standards, and customized impact sockets can be designed to comply with these requirements. For instance, custom sockets can be manufactured to meet ANSI, ISO, or DIN standards, ensuring that they are both safe and reliable for industry-specific applications. Industries like aerospace, automotive manufacturing, and heavy equipment maintenance benefit greatly from custom tools that meet or exceed regulatory standards, providing assurance that their tools will perform reliably in high-stakes applications.
Optimizing Cost and Longevity
Though customized sockets might involve a higher initial cost, they often result in significant savings over time. By selecting high-quality materials and specialized designs, businesses can increase the lifespan of their tools, reducing the need for frequent replacements and repairs. This durability is especially valuable in industries where tool wear and tear are common. A well-designed custom impact socket can withstand harsh conditions and high-torque applications, ultimately providing a better return on investment compared to standard options.
Branding and Custom Aesthetic Options
For companies that prioritize branding, customization allows for aesthetic enhancements, such as adding logos, specific color schemes, or engravings to the tools. Branded impact sockets not only reflect a company’s identity but also help improve organization in the workplace by making tools easily identifiable. Some companies choose custom colors for impact sockets to help distinguish between sizes, types, or departments, making it easier to organize and locate the right tool when needed.
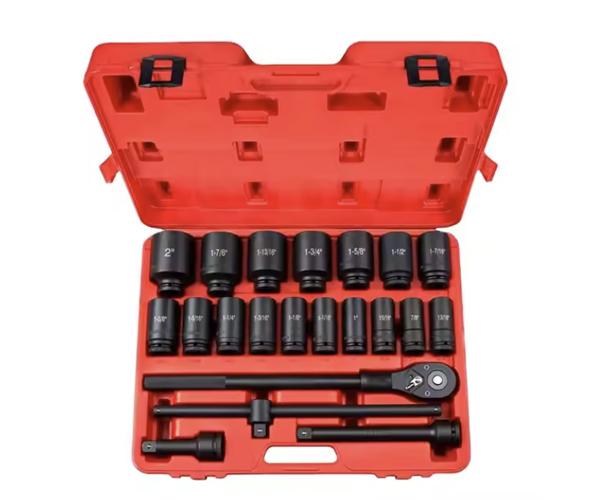
Types of Impact Socket Customizations Available
The customization options for impact sockets go beyond simple size adjustments. Businesses can select from a range of features to ensure that their sockets are optimized for specific applications. Here are the primary types of customizations available for impact sockets:
Material Customization
The choice of material for an impact socket significantly influences its performance, durability, and cost. Different materials offer distinct advantages depending on the application. Chrome molybdenum and carbon steel are popular choices due to their strength and resistance to deformation. Some clients may request specific alloys to balance durability with cost-effectiveness.
- Chrome Molybdenum (CrMo): Known for its exceptional strength, CrMo is a preferred choice for impact sockets used in heavy-duty environments, where resilience against deformation is crucial.
- Carbon Steel: An affordable alternative that still provides good durability, making it suitable for moderate impact applications.
Size and Shape Adjustments
One of the most common reasons for customizing impact sockets is to accommodate unique sizes or shapes not available in standard options. Custom sizing ensures that each socket fits precisely with its intended fastener, which can be crucial in industries like aerospace or construction where non-standard bolts are frequently used. Options for custom lengths, wall thickness, and drive types are also available, allowing businesses to create tools that meet specific needs, such as reaching bolts in tight spaces or handling large, specialized fasteners.
Drive and Connection Customization
Drive sizes and connection types can also be customized to meet unique application requirements. Standard drive sizes like 1/4″, 1/2″, and 3/4″ are commonly available, but some applications require non-standard drive connections or special adapters. Custom drive connections ensure that the socket can be securely attached to power tools, enhancing safety and efficiency. This is particularly beneficial in industries where specific tool configurations are necessary for specialized machinery.
Surface Finish Options
The surface finish of an impact socket plays a critical role in its performance and durability. Coatings such as black oxide, phosphate, and custom-colored finishes can enhance corrosion resistance, improve grip, and provide additional protection against wear. Custom colors also allow companies to differentiate sockets by size or application, making it easier to organize and identify tools in fast-paced work environments. Popular finishes include:
- Black Oxide: Offers corrosion resistance and a non-reflective surface, ideal for use in high-impact applications.
- Phosphate Coating: Similar to black oxide but with added durability, providing enhanced resistance to chipping and surface wear.
- Custom Colors: Branded colors or color-coded sockets for tool organization and quick identification.
Heat Treatment and Hardening Options
Heat treatment is a vital step in ensuring the durability of impact sockets. By customizing heat treatment processes such as quenching, tempering, or annealing, manufacturers can create sockets that withstand high levels of torque and stress without cracking or warping. Custom heat treatments offer a balance between hardness and toughness, ensuring that the socket can endure repeated impacts over time.
Branding and Engraving
Companies often choose to add unique branding to their impact sockets, including logos, serial numbers, and labels for tracking and inventory management. This customization adds a professional touch to the toolset, enhances brand recognition, and helps prevent theft or loss. Engraving and embossing are also useful for labeling socket sizes, making it easier to identify the correct tool during a job.
Set and Packaging Customization
In addition to customizing the sockets themselves, companies can also request specific packaging options. Custom toolkits or socket organizers help businesses maintain organization and efficiency by keeping tools sorted and accessible. Personalized cases, with branded logos and color-coded interiors, add an extra level of professionalism and make tools easier to manage in large operations.
The Impact Socket Customization Process
The customization of impact sockets follows a detailed, step-by-step process that ensures each tool meets the precise specifications of the client. Below is an outline of the typical stages involved in customizing impact sockets.
Step 1: Consultation and Requirement Analysis
The process begins with a comprehensive consultation where the client discusses their needs with the supplier. During this phase, the supplier gathers information on the intended application, specific size requirements, material preferences, and any regulatory standards that need to be met. This step is essential for defining the project’s scope and ensuring that all customization requirements are understood.
Step 2: Design and Prototyping
Once the initial requirements are set, the design team creates a digital model of the socket using CAD software. This digital model allows the client to visualize the socket’s design and make any necessary adjustments before production begins. In some cases, a prototype may be created using 3D printing or other rapid prototyping techniques. This helps ensure the socket fits correctly and performs as expected in its intended environment.
Step 3: Material Sourcing and Quality Control
High-quality materials are essential for creating durable, impact-resistant sockets. Manufacturers carefully source materials like chrome molybdenum or carbon steel, and conduct quality control checks to ensure that each batch meets the specified standards. This stage is crucial for preventing defects and ensuring the final product’s longevity.
Step 4: Manufacturing Process
The manufacturing process for custom impact sockets involves several key stages:
- Forging and Machining: The raw materials are forged into the initial shape, then machined to meet precise dimensions.
- Heat Treatment: The sockets are subjected to specific heat treatments to enhance their strength and resilience.
- Coating Application: Finally, a protective coating (e.g., black oxide or phosphate) is applied to resist corrosion and improve performance.
Each step is monitored to maintain consistency and quality, ensuring the socket meets all customization requirements.
Step 5: Final Quality Testing
Before the sockets are shipped, they undergo rigorous quality testing to verify that they meet the client’s specifications and any industry standards. Common tests include torque strength testing, impact resistance trials, and thermal stability assessments. Quality testing is essential to ensure that each socket performs reliably under high-stress conditions.
Step 6: Delivery and After-Sales Support
Once the sockets pass quality testing, they are packaged and delivered to the client. A reliable supplier also provides after-sales support, which may include maintenance advice, troubleshooting, and assistance with any issues that arise. This support ensures that clients are fully satisfied with their customized sockets and that they receive the guidance they need to maintain optimal tool performance.
Factors to Consider in Impact Socket Customization
Impact socket customization offers many advantages, but several factors need to be considered to achieve the best results. Customizing impact sockets requires an understanding of the application environment, material performance, cost considerations, and supplier reliability. Here’s a breakdown of the most important factors to keep in mind when customizing impact sockets.
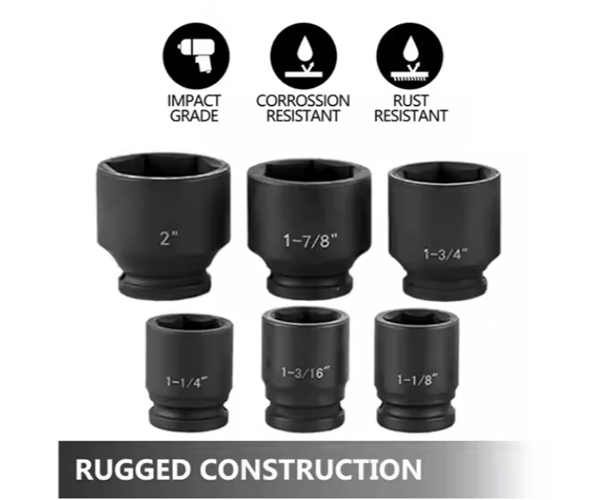
Material Strength and Durability
One of the most critical factors in impact socket customization is the material used. Material selection directly affects the socket’s strength, durability, and suitability for specific applications. Chrome molybdenum and carbon steel are popular materials for impact sockets due to their ability to withstand high torque without deformation. However, the choice of material depends on the specific demands of the job.
- Chrome Molybdenum (CrMo): Known for its high tensile strength, CrMo is ideal for heavy-duty applications where durability is paramount.
- Carbon Steel: An economical option that still provides good strength for moderate applications, though it may not be as durable as CrMo under extreme pressure.
Each material type offers unique properties that suit different working conditions, so choosing the right one is crucial to optimizing performance.
Torque and Stress Requirements
Impact sockets are subjected to extreme forces, especially in applications that involve power tools like pneumatic wrenches. When customizing sockets, it’s essential to consider the torque levels they will need to handle. In industries like automotive repair or heavy machinery maintenance, where high torque is common, sockets must be capable of enduring repetitive impacts without fracturing. This is where adjustments in wall thickness, heat treatment, and material choice come into play, ensuring that the socket can manage these high-stress conditions reliably over time.
Cost Considerations
While customized impact sockets offer significant advantages, they also come with higher upfront costs compared to standard sockets. Material, manufacturing techniques, and the level of customization all influence the cost. Companies must weigh the initial investment against long-term benefits, such as extended socket life, reduced replacement frequency, and increased operational efficiency. Many companies find that the benefits of reduced maintenance costs and improved tool performance more than offset the initial expense.
Lead Time and Production Capacity
Custom orders often require longer lead times than standard sockets, as each customization process involves design, prototyping, and manufacturing stages. Companies should plan for these timeframes when placing large orders, especially if the sockets are needed for a specific project or production schedule. It’s essential to communicate with the supplier to understand expected production times and ensure that customized sockets will be delivered on time.
Supplier Reliability and Expertise
Choosing the right supplier is critical for successful impact socket customization. A reliable supplier will not only provide quality products but will also have the expertise to recommend the best options for each application. It’s important to select a supplier with a proven track record in customization and a commitment to quality control. Look for suppliers with industry certifications and a history of positive customer feedback to ensure that they can deliver the quality and precision required for customized impact sockets.
Key Advantages of Wholesale Impact Socket Customization
Purchasing impact sockets in wholesale quantities offers several benefits, particularly for businesses that rely on these tools daily. By opting for wholesale customization, companies can take advantage of cost savings, consistent quality, and access to a wider range of customization options. Below are the key advantages of impact socket wholesale customization.
Cost Efficiency for Bulk Orders
Wholesale orders allow businesses to benefit from reduced per-unit costs, making it more affordable to invest in high-quality, customized tools. For industries that use impact sockets frequently, buying in bulk helps lower overall expenses and ensures that tools are readily available when needed. Additionally, suppliers often provide discounts for larger orders, further reducing costs and enabling companies to maximize their budget.
Consistency in Quality Across Large Orders
With wholesale customization, companies can maintain consistent quality standards across their entire toolkit. This uniformity is crucial in industries where variations in tool quality could impact safety or performance. By partnering with a reputable supplier, businesses can ensure that every socket meets the same standards, reducing the risk of tool failure and enhancing overall reliability. Consistent quality also simplifies tool maintenance and helps prevent issues associated with using mismatched tools.
Flexibility in Product Range and Options
Ordering impact sockets wholesale provides access to a broader range of customization options. Companies can specify different sizes, drive types, coatings, and packaging configurations based on their specific needs. This flexibility allows businesses to create a comprehensive toolkit that meets all of their application requirements, from heavy-duty industrial tasks to precise mechanical work. Wholesale customization also enables companies to experiment with new designs or materials to find the best solutions for their operations.
Streamlined Supply Chain and Logistics
Wholesale orders simplify the supply chain by consolidating the ordering, customization, and delivery processes. Businesses can work with a single supplier to manage large quantities of customized tools, ensuring a more streamlined approach to procurement. This one-stop solution reduces the complexity of sourcing and managing inventory, which is especially advantageous for large companies that need to keep their toolkits fully stocked and ready for immediate use.
Quality Assurance in Custom Impact Sockets
Quality assurance is vital for ensuring that custom impact sockets meet the demands of high-stress applications. In industries where safety and reliability are top priorities, thorough testing and certification are essential to guarantee that each socket performs as expected. Here’s an overview of quality assurance in the context of customized impact sockets.
Importance of Quality Control in Customized Products
Quality control is essential in customized impact sockets because these tools are often subjected to intense forces that could lead to damage or wear over time. A well-defined quality control process ensures that each socket meets the client’s specific requirements and performs reliably in challenging environments. High-quality custom sockets reduce the risk of accidents, tool failure, and costly downtime, providing businesses with greater confidence in their tools.
Testing Procedures and Standards
Various testing methods are used to evaluate the performance of custom impact sockets. These tests measure factors like torque strength, impact resistance, and thermal stability, ensuring that each socket can handle its intended application. Common testing procedures include:
- Torque Strength Testing: Verifies the socket’s ability to withstand high-torque applications without cracking or deforming.
- Impact Resistance Testing: Assesses the socket’s durability under repeated impact conditions, simulating the forces generated by power tools.
- Thermal Stability Testing: Checks the socket’s resilience to temperature changes, which is especially important for applications that involve extreme heat or cold.
These testing procedures confirm that each socket meets industry standards, ensuring that customized tools perform reliably under high-stress conditions.
Common Certifications for Impact Sockets
Industry certifications play a critical role in establishing the quality and reliability of impact sockets. Certifications from organizations like ANSI, ISO, and DIN indicate that the sockets meet established safety and performance standards. For companies in regulated industries, certification provides assurance that their tools comply with necessary guidelines, enhancing safety and reliability. Certifications are also an indicator of a supplier’s commitment to quality, which is essential when selecting a manufacturer for customized impact sockets.
Quality Assurance for Bulk Orders
Quality assurance is especially important for bulk orders, as consistency across a large quantity of sockets is crucial. Suppliers often implement third-party testing or use advanced quality control methods to ensure that each socket meets the same high standards. This level of quality assurance is invaluable for companies ordering wholesale impact sockets, as it guarantees that each tool in the order will perform as expected and meet the required specifications.
Case Studies: Real-World Examples of Custom Impact Sockets in Action
Understanding how different industries benefit from customized impact sockets can highlight the practical advantages of customization. Below are real-world examples of how custom impact sockets have enhanced efficiency, safety, and productivity for various companies.
Case Study 1: Automotive Workshop with Customized Socket Sets
An automotive repair company specializing in high-performance vehicles required impact sockets tailored to unique torque requirements and specific vehicle models. By customizing their socket sets, they created tools optimized for the high-torque applications frequently encountered in engine and suspension work. The custom sockets provided better grip, reduced wear, and improved safety for technicians, leading to faster and more efficient repairs.
Case Study 2: Heavy Machinery Maintenance in Construction
A construction firm that maintains heavy machinery needed impact sockets capable of handling the large bolts and extreme torque levels associated with construction equipment. The company partnered with a supplier to create custom sockets that fit the unique fasteners used in their machinery. This customization reduced the time spent searching for compatible tools, improved efficiency, and minimized the risk of damage to bolts and fasteners.
Case Study 3: Manufacturing Plant with High-Volume Custom Needs
A manufacturing plant required impact sockets for its assembly line, where tools are used continuously throughout the day. Customizing the sockets for enhanced durability and ergonomic design allowed the plant to reduce downtime caused by tool failure. The custom tools also improved worker comfort and safety, leading to a more efficient and productive work environment.
Case Study 4: Emergency Response and Rescue Services
Emergency response teams needed impact sockets designed for fast, reliable use in high-stress situations. By customizing the sockets for quick access and durability, these teams could perform their tasks more efficiently. Custom finishes were added to increase visibility in low-light conditions, and specialized drives were incorporated to ensure compatibility with their existing rescue tools.
Common Challenges and Solutions in Impact Socket Customization
While impact socket customization offers numerous benefits, it also presents unique challenges. Here are some common obstacles businesses may face during the customization process, along with potential solutions.
Balancing Cost and Quality
Customization often leads to higher initial costs, so finding a balance between quality and affordability is essential. Businesses can work with suppliers to explore alternative materials or adjust design specifications to reduce costs without compromising performance. For example, choosing a slightly less expensive material that still meets durability requirements can make customization more cost-effective.
Managing Lead Times
Customized sockets require more time to produce than standard sockets, as they involve additional design and manufacturing steps. To manage lead times effectively, businesses should plan their orders well in advance and maintain open communication with their supplier. Selecting a supplier with a track record of timely delivery is also essential for meeting project deadlines.
Technical Limitations
Certain customization requests may not be feasible due to technical limitations in materials, sizing, or design. Working closely with the supplier to understand these limitations can help businesses make informed choices about their customization options. In cases where a specific design is impractical, the supplier may suggest alternative solutions that achieve similar results.
Ensuring Compatibility with Existing Equipment
Customized impact sockets must be compatible with existing equipment to ensure smooth operation. This is especially important for non-standard sizes or drive configurations. Testing prototypes and consulting with the supplier about compatibility can help prevent issues down the line.
Choosing the Right Supplier for Wholesale Custom Impact Sockets
Selecting the right supplier is crucial to the success of any impact socket customization project. The supplier’s expertise, reliability, and quality assurance practices all play a role in ensuring that the final product meets expectations. Here’s what to consider when choosing a supplier for custom impact sockets.
Key Factors in Selecting a Supplier
When evaluating potential suppliers, companies should consider factors such as the supplier’s experience, certifications, and ability to meet customization requirements. A supplier with a strong track record in impact socket manufacturing will be better equipped to handle complex customization projects and provide insights into the best materials and designs for specific applications.
Questions to Ask Potential Suppliers
- What certifications do you hold? Ensure that the supplier has relevant industry certifications for quality and safety.
- What quality control processes do you follow? A reliable supplier should have strict quality control measures in place to guarantee consistency.
- What is your production capacity? Verify that the supplier can handle the order size and meet deadlines.
- Can you provide references or case studies? Reviewing past projects can give insight into the supplier’s expertise and reliability.
Tips for Evaluating Supplier Reliability
To ensure that a supplier is dependable, companies can look for signs of reliability, such as positive reviews, industry partnerships, and a reputation for on-time delivery. Companies should also consider visiting the supplier’s facility or requesting a virtual tour to evaluate their manufacturing processes and quality assurance protocols.
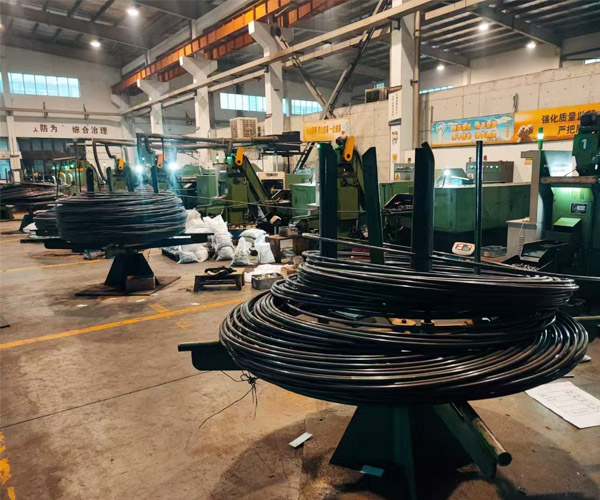
Conclusion
Impact socket customization offers numerous advantages for industries that require tools tailored to specific needs, whether for enhanced performance, cost savings, or brand recognition. Customizing impact sockets allows businesses to create tools optimized for their unique applications, providing a level of precision and durability that standard sockets cannot match. When ordered in wholesale quantities, customized sockets also offer significant cost savings and ensure consistent quality across a company’s toolkit.
For companies considering custom impact sockets, partnering with a reliable supplier is key to achieving successful results. By considering factors like material selection, customization options, and quality assurance processes, businesses can ensure that their customized tools meet the highest standards. Whether used in automotive repair, heavy machinery maintenance, or industrial manufacturing, custom impact sockets provide the strength, reliability, and functionality needed to keep operations running smoothly and efficiently.
Ready to Elevate Your Toolset with Customized Impact Sockets?
At KOLARWIN, we specialize in wholesale impact socket customization tailored to meet the unique demands of your industry. With our high-quality materials, advanced customization options, and strict quality assurance processes, we deliver tools that don’t just perform but exceed expectations in durability, precision, and reliability.
Whether you’re looking for impact sockets with specific sizes, drive types, materials, or unique branding, our team is ready to partner with you from design to delivery. Get in touch with us today to discuss your customization needs and experience the advantages of a personalized toolset that powers your work with efficiency and confidence.
Contact KOLARWIN today to get started on your customized impact socket solution!