Introduction
When you’re working with different tools in a workshop or on a job site, choosing the right socket is essential for performance and safety. Using the wrong type can cause socket breakage, tool damage, or even serious injuries. This guide dives into one of the most common questions among tool users: What is the difference between impact sockets and regular sockets? Understanding this difference is crucial, especially for those using high-torque tools like impact wrenches or pneumatic impact tools. Not only will the right choice improve tool lifespan, but it can also ensure a safer workspace.
This post will cover everything from the basic characteristics of each socket type to the unique benefits of impact sockets over regular sockets. We’ll also explore why material choice, construction, and design are all key factors that set these two socket types apart, especially for those looking to work with heavy-duty applications. By the end, you’ll be able to make informed decisions on which sockets to use, whether you’re an enthusiast or sourcing for impact sockets imperial manufacturers.
Basics of Sockets and Their Applications
What Are Sockets?
Sockets are attachments that allow users to drive fasteners, bolts, and nuts with a ratchet, wrench, or power tool. These attachments come in various shapes and sizes to fit the specific needs of different tasks, from household repairs to industrial applications. A socket’s primary function is to grip the fastener securely, allowing the user to apply torque to tighten or loosen it. Sockets are indispensable in auto repair, heavy machinery maintenance, and even in household tasks requiring heavy-duty tools.
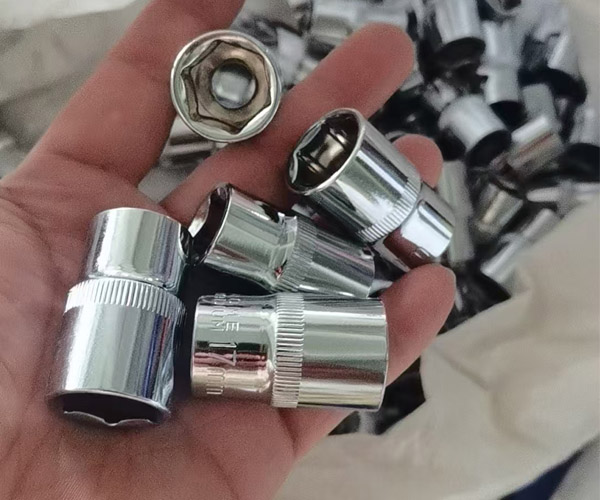
Different Types of Sockets in the Market
The most common types of sockets include impact sockets and regular sockets, but there are other specialized sockets as well, such as deep sockets, universal sockets, and extension bars. While regular sockets are typically used with hand tools, impact sockets are specifically designed to handle the stress of high-torque power tools, such as impact wrenches and pneumatic impact tools. Understanding the strengths and limitations of each socket type helps ensure that you are equipped with the right tools for the job at hand.
Impact vs. Regular Sockets: A Quick Overview
Both impact sockets and regular sockets serve to drive fasteners, but they have significant differences in construction, material, and safety features. Impact sockets, for instance, are designed for the intense, repetitive stresses exerted by power tools, while regular sockets are more suited for manual tasks. Each type offers unique benefits and should be chosen according to the task’s requirements and the tools involved.
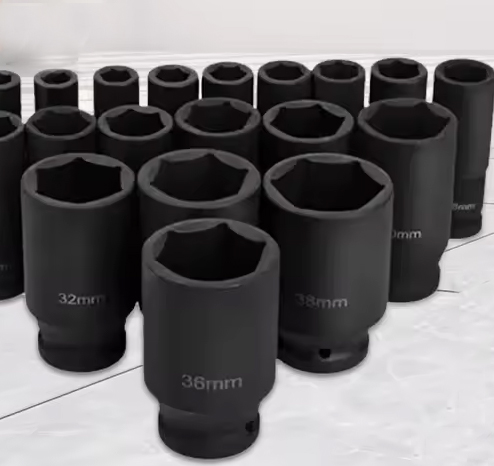
Key Differences Between Impact Sockets and Regular Sockets
Understanding the distinctions between impact sockets and regular sockets is essential when selecting the right tool for the job. Below, we break down the primary differences between these socket types in terms of material, durability, structural design, and safety.
1. Construction Material and Durability
One of the main differences between impact and regular sockets is the type of metal used in their construction, which affects their durability and suitability for specific tools.
Impact Sockets are typically made from chrome molybdenum steel, a material known for its exceptional strength and elasticity. Chrome molybdenum steel is ideal for impact sockets because it withstands high torque and intense vibrations produced by pneumatic impact tools and power wrenches. This material is more flexible under stress, which means it absorbs the impact better without cracking or breaking, even under heavy loads. The elasticity of chrome molybdenum allows impact sockets to perform well under repeated high-stress conditions, making them the preferred choice in industrial settings and professional auto repair shops.
Regular Sockets, on the other hand, are often made from chrome vanadium steel. While this material is strong and durable, it lacks the flexibility of chrome molybdenum, making it more brittle under the kind of stress that impact tools produce. Chrome vanadium steel is ideal for manual tasks that don’t require high torque or continuous use with power tools. While this material provides a sleek, polished finish, it can become vulnerable to fractures or shattering if used with impact wrenches. For this reason, regular sockets are better suited for household repairs or light-duty applications where manual torque is sufficient.
2. Structural Design and Thickness
The design and wall thickness of a socket significantly impact its ability to withstand force, especially in high-torque applications.
Impact Sockets are constructed with thicker walls—typically around 50% thicker than regular sockets. This extra thickness provides additional strength and durability, allowing the socket to withstand repeated impacts from high-torque tools like impact wrenches. The design also helps distribute the force more evenly across the socket, preventing wear or cracks. Thicker walls make impact sockets heavier, but this added weight is an advantage when working with powerful tools, as it adds stability and reduces the risk of shattering.
Regular Sockets have thinner walls, making them lighter and easier to handle when performing manual tasks. However, these thinner walls mean that regular sockets are not built to absorb the vibrations and torque produced by impact tools. Thinner walls make regular sockets less durable in high-stress conditions, limiting them to hand tools or tasks where lower torque is applied. If used with high-torque impact tools, regular sockets can crack or shatter, posing a serious safety risk to the user.
3. Coating and Finish
Sockets also differ in their finishing and coating, which affect their resistance to corrosion and ease of identification.
Impact Sockets are usually finished with a black oxide coating. This matte black finish not only provides a layer of rust resistance but also distinguishes them visually from regular sockets. The black oxide finish helps prevent corrosion caused by moisture and exposure to harsh environments, extending the life of the tool. The dark color also makes impact sockets easily identifiable in a toolbox, reducing the risk of accidentally using a regular socket for high-impact tasks.
Regular Sockets are often finished with chrome plating. This chrome finish gives regular sockets a shiny, polished look and provides a smooth surface that resists corrosion. However, chrome plating is not suitable for the high impact and repeated stress of pneumatic tools. In impact applications, the chrome finish can chip or flake, making the socket susceptible to rust and wear. The polished finish is more suitable for hand tools, offering a sleek look that many users appreciate for light-duty tasks.
4. Safety Considerations
Safety is a crucial factor when choosing between impact and regular sockets, especially in professional settings where high-powered tools are commonly used.
Impact Sockets are designed with safety in mind, built to handle the shocks and vibrations of impact tools. The thicker walls, durable materials, and black oxide finish reduce the risk of the socket cracking or shattering during use. This design significantly decreases the likelihood of injury, making impact sockets the safer choice when working with pneumatic impact tools or other high-torque equipment.
Using Regular Sockets with impact tools, however, can lead to severe safety risks. The brittle nature of chrome vanadium steel, combined with the socket’s thinner walls, increases the chance of breakage. When a regular socket shatters, it can send sharp fragments flying, potentially causing injuries or damaging nearby equipment. For this reason, it’s vital to avoid using regular sockets with any tool that produces high torque, as they are specifically designed for hand tools and lighter tasks.
What Are Impact Sockets?
Impact sockets are specialized tools designed to withstand the extreme forces and repetitive vibrations generated by impact tools, such as impact wrenches and pneumatic impact tools. Unlike regular sockets, which are designed for use with hand tools, impact sockets are optimized for heavy-duty applications.
Detailed Definition and Core Characteristics
Impact sockets are manufactured using chrome molybdenum steel, a metal with higher elasticity than the chrome vanadium steel used in regular sockets. This elasticity allows impact sockets to absorb and withstand the sudden bursts of torque that impact tools generate without cracking or deforming. In addition to their superior strength, impact sockets are designed with thicker walls, which further enhances their durability and ability to manage high-torque scenarios.
Why Use Impact Sockets?
Impact sockets are the go-to choice for any task involving high-powered tools, particularly in professional settings such as auto repair shops and industrial maintenance. The combination of their durable construction and resistance to stress makes them ideal for tasks that require deep impact sockets and other heavy-duty options. For example, when dealing with rusted or over-torqued bolts, impact sockets provide the resilience needed to complete the job safely and efficiently. Their resistance to shattering under pressure means they’re a safer option when handling difficult bolts and high-stress environments.
Types of Impact Sockets
There are several types of impact sockets, each suited to different applications. The two main varieties are standard impact sockets and deep impact sockets.
- Standard Impact Sockets: These are ideal for general tasks where the fastener is easily accessible. Standard impact sockets are typically shorter in length, allowing them to fit snugly onto fasteners without taking up too much space.
- Deep Impact Sockets: These sockets are longer, making them ideal for reaching recessed fasteners or bolts located in hard-to-reach areas. Deep impact sockets are commonly used in automotive repair, where certain bolts are located deep within an assembly. The added length allows mechanics to reach bolts that would be inaccessible with a standard socket.
When to Choose Impact Sockets
The primary consideration for choosing impact sockets is the tool you’re using. If you are working with high-torque tools, such as an impact wrench or any pneumatic impact tool, impact sockets are a necessity. Their robust construction and black oxide finish provide both durability and corrosion resistance, making them well-suited for frequent, intense use. Whether you’re a professional mechanic or a DIY enthusiast, impact sockets are a worthwhile investment if you frequently work with high-powered tools.
What Are Regular Sockets?
Regular sockets, also known as hand sockets, are designed for use with manual tools such as ratchets and socket wrenches. They’re optimized for tasks that don’t require the high torque output of power tools, making them ideal for household and light-duty applications.
Definition and Typical Uses
Regular sockets are constructed from chrome vanadium steel, a material that is durable yet more brittle than chrome molybdenum. While regular sockets are strong enough to handle manual torque, they are not built to endure the intense vibrations and torque generated by power tools. The chrome finish on regular sockets provides a sleek, corrosion-resistant surface that makes them easy to clean and maintain, but this finish is not intended to withstand impact forces.
Best Situations for Regular Sockets
Regular sockets excel in settings where hand tools are sufficient, such as light home repairs or general maintenance. They’re particularly useful for tasks that involve low torque, where the added durability of impact sockets is not necessary. For example, regular sockets are perfect for assembling furniture, performing light vehicle maintenance, or tackling small household projects. Their thinner walls and polished finish make them easy to handle for these kinds of tasks, providing an ergonomic advantage over impact sockets.
Limitations of Regular Sockets with Power Tools
One of the primary limitations of regular sockets is their inability to withstand the force of high-powered tools. Using regular sockets with tools like impact wrenches can lead to socket shattering, which poses both safety risks and potential damage to the tool. In high-stress applications, the chrome finish on regular sockets can chip or flake, reducing their lifespan and exposing them to corrosion. For these reasons, regular sockets should be reserved for hand tools, as they lack the structural integrity needed for impact tasks.
Practical Use Cases: When to Use Each Type
Impact Socket Use Cases
Impact sockets are ideal for scenarios where heavy-duty tools are necessary. Common applications include automotive repairs, industrial maintenance, and other settings where high torque is frequently applied. For example, mechanics often use impact sockets with air tools to remove rusted or tightly fastened bolts. The thick-walled design and resilient chrome molybdenum material allow impact sockets to handle the repeated forces produced by power tools, reducing the risk of breakage and improving safety.
Regular Socket Use Cases
Regular sockets are better suited for light-duty applications that involve hand tools. Household repairs, furniture assembly, and light vehicle maintenance are all examples where regular sockets perform well. In these situations, regular sockets provide an ergonomic advantage, as their lighter weight and chrome finish make them easier to handle for extended periods.
Consequences of Using the Wrong Socket
Using the wrong socket for the job can lead to various risks. When regular sockets are used with impact tools, there is a significant risk of the socket breaking, which can lead to injuries from flying debris. Additionally, using impact sockets for tasks that require only light manual torque can result in unnecessary wear on the socket. Therefore, choosing the appropriate socket for each task not only ensures safety but also prolongs the life of your tools.
Choosing the Right Socket for Your Needs
Selecting the correct socket type depends on several factors, including the tools being used, the torque required, and the nature of the task. For example, if you frequently work with high-torque impact tools, impact sockets are essential for safety and durability. Conversely, if your tasks involve only manual hand tools, regular sockets are likely the more cost-effective and practical choice.
Budget Considerations
The material and construction differences mean that impact sockets often come at a higher price than regular sockets. While impact sockets are an investment, especially for professionals, the additional cost is justified by the increased durability and safety they provide. For occasional users, however, regular sockets may be sufficient for most household tasks, offering a more budget-friendly option.
What to Look for When Buying Sockets
When purchasing sockets, consider the quality of the material, the type of finish, and the manufacturer’s reputation. For those working with impact sockets imperial manufacturers, opting for trusted brands ensures that the socket can handle high-torque tasks safely and reliably. Look for warranties or guarantees, as these often reflect a manufacturer’s confidence in the product’s durability.
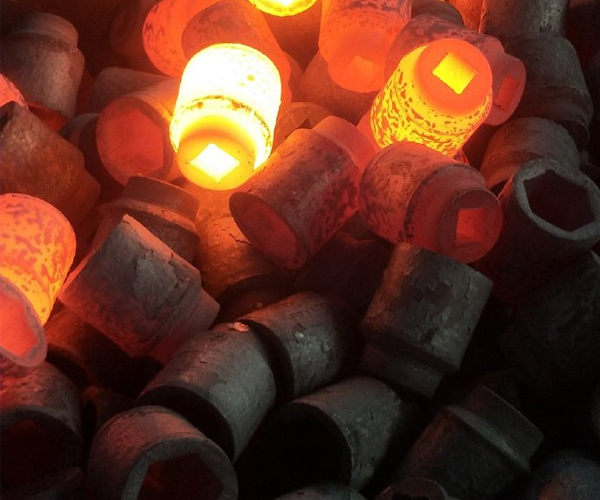
Safety Tips and Best Practices for Socket Usage
Safety Guidelines for Using Impact Sockets
When using impact sockets, ensure they are properly secured and check for any signs of wear or damage. Impact sockets should only be used with compatible tools, as they are specifically designed to handle the stress of high-torque applications.
Using Regular Sockets Safely
Avoid using regular sockets with any tool that generates significant torque. Instead, stick to manual tools and regularly inspect your sockets for signs of damage, especially if they are used frequently.
Maintaining Your Sockets for Longevity
To maximize the lifespan of your sockets, clean them after each use and store them in a dry place. Regular inspection and proper storage can prevent rust and other forms of wear, extending the usability of both impact and regular sockets.
Frequently Asked Questions (FAQ)
Can You Use Impact Sockets on Regular Wrenches?
Yes, impact sockets can safely be used on regular, manual wrenches, ratchets, and hand tools. In fact, many professionals and DIY users do this when they need the extra durability that impact sockets provide. While impact sockets are specifically designed for high-torque power tools, they are perfectly compatible with manual tools due to their construction from chrome molybdenum steel and their thicker walls. Using impact sockets with hand tools can actually extend the socket’s lifespan by subjecting it to less force than it was designed to handle.
Why Are Impact Sockets Black?
Impact sockets are typically finished with a black oxide coating, giving them their distinctive matte black appearance. This coating serves two main purposes: it provides a layer of rust resistance and distinguishes impact sockets from chrome-plated regular sockets at a glance. The black oxide finish resists corrosion better than a polished chrome finish and helps reduce glare when working under bright lights, which can be especially useful in workshops and industrial settings. This finish also serves as a visual reminder that these sockets are designed for heavy-duty use with impact tools.
How Long Do Impact Sockets Last Compared to Regular Sockets?
The lifespan of impact sockets generally exceeds that of regular sockets when used in high-torque or heavy-duty applications. Impact sockets are made from more resilient materials (like chrome molybdenum) and are built with thicker walls, making them less susceptible to cracking, especially when used with pneumatic impact tools and other high-stress applications. Regular sockets, made from chrome vanadium steel, can last just as long as impact sockets if used solely with hand tools in low-stress environments. However, when regular sockets are used incorrectly with impact tools, their lifespan can be drastically shortened, often resulting in damage or breakage after minimal use.
What Risks Are Involved in Using a Regular Socket with an Impact Tool?
Using regular sockets with impact tools can lead to several safety and durability issues. Regular sockets are made from brittle chrome vanadium steel, which cannot absorb the repeated high-torque shocks produced by impact tools. This can cause the socket to crack, shatter, or even explode under stress, which not only damages the tool but also creates a significant safety hazard from flying debris. Additionally, the chrome plating on regular sockets can chip or flake off when exposed to intense vibrations, reducing their corrosion resistance and making them unsuitable for heavy-duty tasks. To avoid these risks, it is crucial to use impact sockets specifically designed to handle the forces of impact tools.
How Can I Tell if a Socket is Impact-Grade?
Identifying an impact-grade socket is usually straightforward. Impact sockets are commonly finished in a matte black color due to their black oxide coating, setting them apart visually from the shiny chrome finish of regular sockets. Additionally, impact sockets tend to be heavier and have thicker walls than regular sockets, which you can often feel in your hand. Some impact sockets may also be explicitly labeled as “impact” by the manufacturer. When in doubt, the black oxide finish and thicker construction are the clearest indicators that a socket is impact-grade and suitable for high-torque applications.
Conclusion
Selecting the right socket type based on the tools and tasks at hand is crucial for safety, efficiency, and tool longevity. By understanding the differences in material, design, and appropriate use cases, you can make informed decisions to achieve better results and a safer workspace.
Ready to Upgrade Your Tools?
Choosing the right socket can make all the difference in both performance and safety. At KOLARWIN, we specialize in high-quality impact sockets, hand tools, and car repair tools tailored for professional and DIY use. Whether you’re in need of durable impact sockets imperial or reliable chrome vanadium regular sockets, our products are built to handle the demands of any job.
Explore Our Range Today!
Visit our website and to browse our full range of impact sockets and other essential tools. With competitive pricing and worldwide shipping, we’re ready to supply you with the tools you need for high performance and reliability. Reach out to us for customized branding, OEM services, and bulk purchasing options.
Choose KOLARWIN for tools that don’t just get the job done—they do it right.