Introduction
A torque wrench is a critical tool used to apply a specific amount of force (torque) to a fastener, such as a nut or bolt. Unlike regular wrenches, torque wrenches ensure that you apply the correct amount of force, preventing over-tightening or under-tightening, both of which can lead to mechanical failures. This precision is especially important in industries like automotive repair, construction, and even DIY home projects where safety and functionality depend on correctly torqued fasteners.
Whether you are a professional mechanic, a DIY enthusiast, or someone who just likes to tinker with cars or appliances at home, a torque wrench is a must-have tool in your toolbox. It’s designed to make sure that you’re applying the right amount of pressure without damaging your equipment or compromising safety. In this guide, we will walk you through user-friendly torque wrench operating instructions that are designed to make the process simple and effective, no matter your experience level.
But before we dive into the technicalities, let’s first understand the fundamentals of torque, how it works, and why it’s so important. Knowing this will help you use a torque wrench more effectively and ensure long-lasting, reliable results. We’ll also explore different types of torque wrenches, and how to choose the best one for your specific needs.
Understanding Torque: The Basics
What is Torque?
In simple terms, torque is the force that causes an object to rotate around an axis. Imagine using a wrench to tighten a bolt: when you apply pressure, you are exerting torque. The greater the force you apply, the more torque you generate. Torque is measured in units like Newton-meters (Nm) or foot-pounds (lb-ft), which essentially represent the amount of force applied over a certain distance.
For example, if you’re tightening a bolt on a car engine, the torque measurement will tell you how much force to apply to ensure the bolt is securely fastened but not overtightened. Applying too much torque could strip the bolt or damage the surrounding parts, while too little torque could result in a loose, unstable connection.
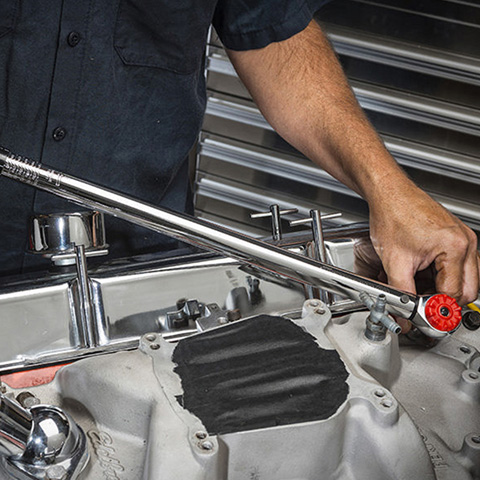
Why Torque Accuracy Matters
Torque accuracy is vital in a wide range of applications, from securing parts in a car engine to assembling furniture at home. The incorrect application of torque can lead to significant problems. Over-torquing can stretch bolts, damage parts, and lead to premature failure, whereas under-torquing leaves parts unsecured and prone to coming loose, which is a potential safety hazard. In automotive settings, for instance, improperly torqued lug nuts can cause wheels to detach while driving—posing a severe safety risk.
Torque wrenches are designed to prevent such issues by providing precision and control over the amount of force applied. This makes them essential for anyone working with fasteners that require exact torque specifications, such as mechanics, construction workers, or even DIYers who want to ensure their projects are safe and durable.
Different Types of Torque Wrenches
Before we delve into the operating instructions for torque wrenches, it’s essential to understand that not all torque wrenches are created equal. Depending on your needs, you might choose a different type of torque wrench. Here’s a breakdown of the most common types:
Click-Type Torque Wrench
The click-type torque wrench is probably the most common and user-friendly type available. It produces a distinct “click” sound when the desired torque level is reached, signaling that you should stop applying pressure. This makes it easy to use, even for beginners, as you don’t have to keep an eye on a gauge to know when you’ve applied the correct torque.
- How it works: The wrench is set to the required torque level, and when you reach that point while tightening, it will make an audible click.
- Best for: Automotive work, household repairs, and general DIY tasks.
Beam Torque Wrench
A beam torque wrench is one of the simplest types, using a calibrated scale and a pointer to display the amount of torque being applied. It doesn’t “click” like a click-type wrench, so you must keep an eye on the gauge to ensure you’ve reached the correct torque.
- How it works: As you apply force, a pointer moves across a scale to indicate the torque being applied.
- Best for: Users who prefer a more hands-on approach to torque control, and those who need a budget-friendly option.
Digital Torque Wrench
Digital torque wrenches are highly accurate and easy to use. They come equipped with a digital display that shows the exact torque being applied. Some models even store multiple torque settings and provide an audible or visual alert when the desired torque is reached.
- How it works: A digital display shows the torque level in real time, making it easier to achieve precise results.
- Best for: Professionals who require high precision and convenience, such as automotive mechanics and aerospace engineers.
Hydraulic and Pneumatic Torque Wrenches
These are specialized torque wrenches often used in industrial settings for heavy-duty applications. Hydraulic torque wrenches use hydraulic pressure to generate torque, while pneumatic torque wrenches use compressed air. Both are capable of applying large amounts of torque, often required in construction or manufacturing.
- How they work: Hydraulic wrenches use fluid power, and pneumatic wrenches use compressed air to achieve high levels of torque.
- Best for: Heavy machinery, industrial applications, and construction work requiring extremely high torque levels.
Choosing the Right Torque Wrench for Your Needs
Factors to Consider
When selecting the best torque wrench for your needs, there are several factors to keep in mind. Different applications call for different levels of precision, ease of use, and durability.
- Precision and Accuracy: Some tasks, like automotive work, demand precise torque measurements. In such cases, a digital or click-type wrench is ideal because of their accuracy. For simpler, less critical tasks, a beam torque wrench may suffice.
- Frequency of Use: How often do you plan to use the tool? For professionals using a torque wrench daily, investing in a high-quality model with excellent durability and a long lifespan is essential. For occasional DIY use, a more affordable option might do the trick.
- Torque Range: Different wrenches have different torque capacities. Ensure that the wrench you choose covers the torque range you need for your work. For example, torque wrenches with a lower torque range (5-50 Nm) are suitable for small fasteners, while those with a higher range (up to 200 Nm or more) are required for heavier tasks like automotive repair.
- Budget Considerations: While it’s tempting to go for the most affordable option, keep in mind that a reliable, well-calibrated torque wrench is a long-term investment. It’s often worth spending a little more on a trusted brand to avoid accuracy issues down the line.
Top Recommendations for Beginners
- TEKTON Click Torque Wrench: A beginner-friendly tool that’s simple to use and highly affordable. It’s suitable for small to medium-sized tasks around the home or on your vehicle.
- Craftsman Beam Torque Wrench: A reliable and affordable option for those who don’t mind manually reading the torque scale.
- GearWrench Digital Torque Wrench: Ideal for those who want precision and an easy-to-read display. It’s a bit pricier but offers greater accuracy and convenience.
Common Torque Wrench Brands
When it comes to reliability and performance, there are several well-known brands that have earned a strong reputation in the torque wrench market:
- Snap-On: Known for producing professional-grade tools, Snap-On wrenches are a top choice for mechanics and industrial workers.
- Tekton: Offers affordable yet reliable torque wrenches for beginners and DIY enthusiasts.
- Craftsman: A trusted name in the industry, offering both manual and digital torque wrenches suitable for various applications.
Now that we have a better understanding of what torque is, why it’s important, and the different types of torque wrenches available, let’s move on to the detailed step-by-step torque wrench operating instructions that will ensure you get the best results from your tool.
How to Read and Set Your Torque Wrench
Using a torque wrench effectively starts with understanding how to read and set the tool for the desired torque. Different types of torque wrenches have slightly varied methods for adjusting and reading the torque setting, but the principles are generally the same.
Setting the Desired Torque
For most click-type and digital torque wrenches, setting the desired torque is a straightforward process. Follow these steps:
- Determine the Required Torque: Before using your torque wrench, you need to know the exact torque specification for the fastener you’re tightening. This information is usually found in the equipment manual or manufacturer’s specifications. For example, car wheel lug nuts often need to be tightened to around 80-100 lb-ft, depending on the vehicle.
- Adjust the Torque Setting: On a click-type wrench, you’ll find a calibrated scale on the handle, often marked with both Nm (Newton meters) and lb-ft (foot-pounds). To adjust the torque, rotate the handle until the desired value lines up with the reference line. For a digital wrench, you simply select the torque setting using buttons, and the torque value is displayed on the screen.
- Lock the Setting: Many wrenches come with a locking mechanism to prevent accidental changes to the torque setting. Once you’ve set the desired torque, make sure to lock it in place by tightening the knob or turning the locking mechanism.
- Recheck the Setting: It’s a good practice to double-check your torque setting before starting your work. This ensures accuracy and reduces the risk of mistakes.
Understanding Torque Units
Torque is usually measured in Newton meters (Nm) or foot-pounds (lb-ft). Knowing how to convert between these units can be helpful, especially if you’re working with international equipment that uses different units. Here’s a quick conversion guide:
- 1 Nm = 0.73756 lb-ft
- 1 lb-ft = 1.35582 Nm
For example, if the manual specifies a torque of 40 lb-ft, you can convert it to Nm using this formula: 40lb-ft×1.35582=54.23Nm.
This conversion is especially useful when working with tools or vehicles that specify torque values in different units. You can also use a torque conversion chart or calculator to quickly make these conversions without doing the math manually.
Step-by-Step Guide to Using a Torque Wrench
Now that your torque wrench is set correctly, it’s time to use it. Here’s a detailed guide to help you apply torque properly and avoid common mistakes.
Pre-Use Preparation
Before using a torque wrench, it’s crucial to inspect it to ensure it’s in good working condition. Follow these steps:
- Inspect the Torque Wrench: Check the wrench for any visible signs of wear or damage, such as cracks, dents, or rust. Make sure the handle, ratchet, and locking mechanism are functioning properly.
- Check Calibration: If you haven’t used the wrench for a while, or if it has been dropped, make sure it is properly calibrated. Torque wrenches that are out of calibration may provide inaccurate readings, which could lead to over-tightening or under-tightening.
- Clean the Wrench: Before using the wrench, wipe it down with a clean, dry cloth to remove any dust or grime that may have accumulated. Avoid using harsh chemicals, as they could damage the tool.
Proper Grip and Handling
When using a torque wrench, your grip and body posture can make a significant difference in the accuracy and safety of the job. Follow these tips:
- Grip the Handle Firmly: Always hold the torque wrench by the handle. Most wrenches are calibrated to work accurately when pressure is applied only to the handle. Avoid gripping the head or the shaft of the wrench, as this can affect the applied force.
- Position Yourself Correctly: Stand directly in front of the fastener and the torque wrench. Keep your arms straight and apply force evenly. Avoid jerky or rapid movements, as these can cause inaccurate readings.
- Maintain a Steady Pressure: Apply consistent pressure when tightening fasteners. If you stop or hesitate, you may apply uneven force, leading to incorrect torque.
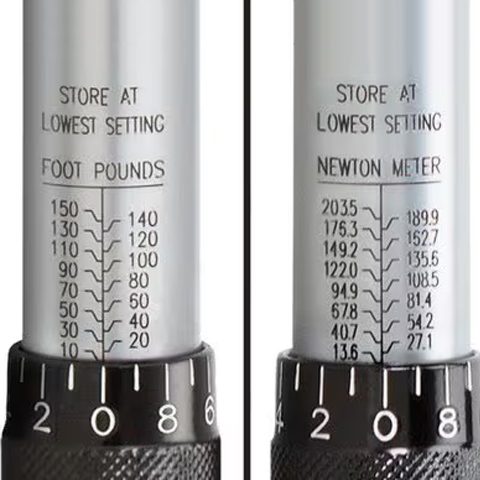
Tightening Fasteners
Once you’ve positioned yourself and the torque wrench correctly, it’s time to begin tightening the fastener.
- Apply Pressure Evenly: Start applying pressure to the wrench slowly and steadily. Do not rush this process, as it’s essential for accurate torque application.
- Listen for the Click: For a click-type torque wrench, you will hear or feel a distinct “click” when the desired torque is reached. This is your signal to stop applying pressure immediately.
- Digital Torque Wrench Alerts: For digital wrenches, you’ll either see a visual alert (such as a blinking light) or hear an audible beep when you’ve reached the correct torque.
- Avoid Over-Tightening: Once you hear the click or receive the alert, stop applying pressure. Continuing to tighten beyond this point can damage the fastener or the parts you are working on.
Post-Use Instructions
After using your torque wrench, it’s important to follow these steps to ensure the tool remains in good working condition for future use:
- Reset the Wrench: For click-type torque wrenches, always reset the wrench to its lowest setting before storing it. This prevents the internal spring mechanism from becoming fatigued over time.
- Clean the Wrench Again: Wipe down the wrench with a clean, dry cloth to remove any dirt, oil, or debris. Proper cleaning ensures that the tool remains free of contaminants that could affect its performance.
- Store Properly: Store your torque wrench in a dry, cool place, away from direct sunlight and moisture. Many torque wrenches come with a storage case, which helps protect the tool from environmental damage.
Common Mistakes and How to Avoid Them
Using a torque wrench may seem simple, but several common mistakes can lead to inaccurate torque application or damage to the wrench itself. Here’s how to avoid them:
Over-Tightening and Under-Tightening
One of the most common mistakes is either over-tightening or under-tightening fasteners. This often happens when users don’t stop after the wrench clicks or when they apply inconsistent pressure.
- Over-Tightening: Continuing to apply pressure after the wrench clicks can result in stripped threads, damaged fasteners, or cracked components.
- Under-Tightening: Not applying enough torque can lead to loose fasteners, which can cause mechanical failures or safety hazards. Always check the torque specification and ensure you reach the correct level.
Misreading the Torque Setting
Another common issue is misreading the torque setting, especially on manual or beam-type torque wrenches.
- Solution: Double-check your torque setting before beginning any work. For digital wrenches, ensure the display shows the correct units (Nm or lb-ft), and for click-type wrenches, confirm the torque setting by lining up the scale correctly.
Not Resetting After Use
Failing to reset the torque wrench to its lowest setting after use can damage the internal mechanism over time. This is a common problem with click-type wrenches.
- Solution: Always reset your wrench to its lowest setting (usually zero) before storing it. This keeps the internal spring from being under constant tension, extending the life of the tool.
Neglecting Calibration
Torque wrenches must be calibrated periodically to maintain accuracy. Neglecting this step can result in incorrect torque application, which can have serious consequences.
- Solution: Calibrate your wrench regularly—either annually or more frequently if you use it often. Most professional tool shops offer calibration services, but some wrenches allow you to do this yourself with the proper equipment.
Understanding Torque Settings for Different Applications
Knowing the proper torque setting for your task is critical to ensuring safety and functionality. Here are some common applications and their recommended torque settings:
Automotive Applications
In automotive work, torque wrenches are commonly used to tighten lug nuts, engine parts, and suspension components. Here are some examples of typical torque ranges:
- Lug Nuts: 80-100 lb-ft, depending on the vehicle.
- Spark Plugs: 15-25 lb-ft.
- Oil Drain Plug: 20-30 lb-ft.
These specifications help ensure that parts are secure without causing damage. Under-tightening lug nuts, for example, can cause wheels to loosen while driving, whereas over-tightening can strip threads and make future removal difficult.
DIY and Home Repair Applications
For DIY projects and home repairs, torque wrenches are often used for assembling furniture, tightening bolts on bikes, and working on household appliances. Common torque values for these tasks include:
- Bicycle Components: 4-6 Nm for stem bolts, 10-12 Nm for crank bolts.
- Furniture Assembly: Torque values vary but typically range between 5-15 Nm for most furniture fasteners.
Even for these smaller tasks, applying the correct amount of torque ensures that parts are securely fastened without being damaged.
Industrial Use
In industrial settings, where larger machinery and equipment are involved, torque specifications can be much higher. Hydraulic and pneumatic torque wrenches are often required for these tasks, as they can apply significant force.
- Heavy Machinery Bolts: 500-2,000 lb-ft, depending on the application.
- Construction Equipment: 300-1,500 lb-ft for securing large bolts and fasteners.
For industrial work, precise torque application is critical for maintaining the structural integrity of machinery and ensuring safety in the workplace.
How to Calibrate Your Torque Wrench
Torque wrenches must be calibrated regularly to ensure their accuracy. Calibration is a process that compares the readings of the wrench against a known standard, adjusting the tool as necessary to maintain its accuracy.
Why Calibration is Important
Over time, torque wrenches can lose their accuracy due to wear and tear or environmental factors. Calibration ensures that the wrench applies the correct torque every time, reducing the risk of over-tightening or under-tightening.
Step-by-Step Calibration Process
Here’s a basic overview of the calibration process:
- Test with a Known Standard: A calibrated testing device is used to measure the output torque of the wrench. You’ll apply the torque to the test device, and it will show whether your wrench is delivering accurate force.
- Adjust the Wrench: If the readings are off, the wrench will need to be adjusted. Some digital torque wrenches allow for easy recalibration through built-in settings, while others may require professional adjustment.
- Repeat the Test: After adjustment, test the wrench again to ensure accuracy. If the readings are still off, the wrench may need additional adjustment or professional servicing.
Signs It’s Time for Recalibration
You should recalibrate your torque wrench if:
- It has been dropped or exposed to extreme temperatures.
- You’ve used it frequently for heavy-duty tasks.
- You notice inconsistent torque application.
Maintenance and Care for Long-Term Use
Proper maintenance is essential to extend the life of your torque wrench and ensure its ongoing accuracy. Here’s how to take care of your tool:
Cleaning Your Torque Wrench
After each use, it’s a good idea to clean your torque wrench to remove dirt, oil, and other debris. Use a clean, dry cloth to wipe down the wrench, paying attention to the handle and the torque scale. Avoid using harsh chemicals or water, as these can damage the wrench’s internal components.
Storage Best Practices
Store your torque wrench in a clean, dry place, ideally in the case it came with. Moisture and extreme temperatures can affect the accuracy of the wrench, so avoid storing it in damp or excessively hot areas. If possible, hang the wrench to prevent pressure on the head or handle.
Routine Inspection Tips
Periodically inspect your wrench for signs of wear or damage, such as cracks in the handle, rust on the shaft, or difficulty adjusting the torque setting. If you notice any of these issues, stop using the wrench and either have it repaired or replaced.
Safety Tips When Using a Torque Wrench
Like any tool, torque wrenches should be used safely to avoid injury or damage. Here are some key safety tips:
Personal Safety Gear
When using a torque wrench, especially in automotive or industrial settings, always wear appropriate personal protective equipment (PPE). This might include:
- Safety glasses: To protect your eyes from debris or shattering parts.
- Gloves: For better grip and protection against sharp or hot surfaces.
- Sturdy footwear: To prevent foot injuries when working around heavy machinery.
Safe Use of Torque Wrenches
Always follow these basic safety protocols when using a torque wrench:
- Ensure that the fastener and the wrench are properly aligned to avoid slipping or damaging the tool.
- Avoid standing in an awkward position or applying force at an odd angle.
- Never use a torque wrench as a hammer or pry bar, as this can damage the wrench and lead to inaccurate readings.
What to Do if Something Goes Wrong
If your torque wrench malfunctions during use (e.g., it doesn’t click or the digital display malfunctions), stop using it immediately. Continuing to use a faulty wrench can lead to improper torque application, which could damage your equipment or cause injury.
Top Torque Wrench Myths Debunked
There are several misconceptions about torque wrenches that can lead to improper use or care. Let’s debunk some of the most common myths:
Myth 1: All Torque Wrenches Are the Same
This is far from true. Different types of torque wrenches are designed for different applications. A click-type wrench is ideal for automotive work, while a beam torque wrench is better suited for less critical tasks. Digital torque wrenches offer greater accuracy and ease of use but tend to be more expensive.
Myth 2: You Don’t Need to Calibrate a New Wrench
Even new torque wrenches can be out of calibration due to shipping and handling. It’s always a good idea to check the calibration of a new wrench before using it, especially for critical tasks.
Myth 3: Torque Wrenches Can Be Used for Loosening Bolts
While some torque wrenches can technically be used to loosen bolts, this is not their intended purpose. Using a torque wrench for loosening can damage the internal components, leading to inaccurate torque readings.
FAQs: Your Most Common Torque Wrench Questions Answered
Here are some frequently asked questions about torque wrenches, along with clear, concise answers:
- How often should I calibrate my torque wrench?
- Calibration should be done at least once a year or after every 5,000 uses. If the wrench is dropped or exposed to extreme temperatures, it should be recalibrated immediately.
- Can I use a torque wrench for loosening bolts?
- While it’s possible, it’s not recommended. Torque wrenches are designed for tightening bolts to a specific torque setting, and using them to loosen bolts can damage the tool.
- What torque wrench should I use for a beginner-level project?
- A click-type torque wrench is a great option for beginners, as it’s easy to use and provides an audible click when the correct torque is reached.
- How do I know if I’m over-torquing a fastener?
- Over-torquing can often be felt as resistance increases sharply. If your torque wrench clicks and you continue to apply pressure, you are likely over-torquing.
- Can I store my torque wrench in a garage or outdoor shed?
- It’s not recommended. Torque wrenches should be stored in a dry, climate-controlled environment to avoid exposure to moisture and temperature extremes, which can affect calibration.
Conclusion: Final Tips for Proper Torque Wrench Application
Using a torque wrench correctly ensures that your projects—whether in automotive repair, home DIY, or industrial settings—are safe, reliable, and long-lasting. Remember to always set the correct torque, maintain your wrench regularly, and recalibrate it as needed. With the right care and attention, your torque wrench will serve you well for many years to come.
Additional Resources and Further Reading
- Video Tutorials: Check out these torque wrench operating videos for step-by-step demonstrations.
- Torque Conversion Charts: Download our free torque conversion chart to simplify torque unit conversions.
- Recommended Projects: Try these beginner-level projects to get familiar with using a torque wrench.
Thank you for reading, and we hope this guide has made using your torque wrench easier and more effective.
Call to Action for OEM Project at Kolarwin Tools
At Kolarwin Tools, we specialize in delivering high-quality, customized hand tools, car repair tools, and DIY tools through our comprehensive OEM services. Whether you’re looking to launch your own brand or expand your product line, our team is ready to bring your vision to life with precision and reliability.
Partner with us today!
- Get Started: Reach out to our team for a free consultation and let us help you turn your ideas into high-quality tools.
- Contact Us: Email us at sales@kolarwintools.com or call +86-13929482960 for personalized service and a custom OEM quote.
- Visit Us on Alibaba: Check out our products and start your OEM journey with us today on Alibaba.
With Kolarwin Tools, you’re choosing a partner dedicated to quality, efficiency, and long-term success. Let’s build something great together!