Introduction
Selecting the right socket set is crucial for any toolkit, whether you’re a professional mechanic, a DIY enthusiast, or a woodworking hobbyist. The right choice can impact both the efficiency of your work and the longevity of your tools. Among the various types of sockets available, regular sockets are a staple due to their versatility and cost-effectiveness. This blog post delves into the advantages of regular sockets, comparing them with impact sockets, and exploring their construction, usage, and key benefits.
What Is an Impact Socket?
Impact sockets are designed specifically for use with impact tools, which deliver high torque through rapid bursts. These sockets are constructed from chrome molybdenum steel, known for its high strength and durability under intense conditions. The black oxide coating on impact sockets not only adds a layer of protection against rust and corrosion but also increases their resistance to wear and tear.
Material and Construction
The primary material used in impact sockets, chrome molybdenum steel, is chosen for its ability to withstand the high stresses encountered during impact work. This steel alloy is designed to handle the torque produced by impact wrenches without deforming or cracking. The black oxide coating provides additional corrosion resistance, making these sockets suitable for harsh environments.
Design and Purpose
Impact sockets are characterized by their thicker walls compared to regular sockets. This design allows them to absorb and distribute the energy from the impact tools more effectively. They also feature a cross hole for pin retention, which ensures a secure fit on the impact wrench and prevents slippage during use. The increased durability of impact sockets makes them ideal for heavy-duty applications where high torque is required.
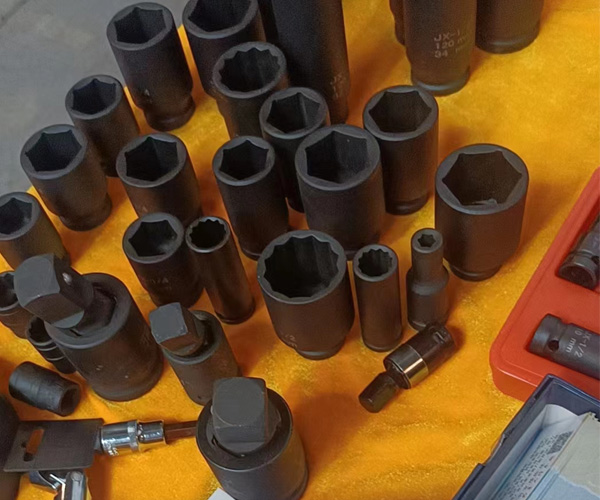
What Is a Regular Socket?
Regular sockets, on the other hand, are primarily designed for use with hand tools such as ratchets and breaker bars. They are typically made from chrome vanadium steel, which provides a balance of strength and affordability. The chrome finish on these sockets enhances their appearance and provides a degree of protection against rust.
Material and Construction
Chrome vanadium steel is a popular choice for regular sockets due to its good balance between strength and cost. This material offers adequate durability for most standard applications without the need for the heavy-duty specifications of impact sockets. The thinner walls of regular sockets are designed for use with manual hand tools, making them suitable for tasks that do not involve high-impact forces.
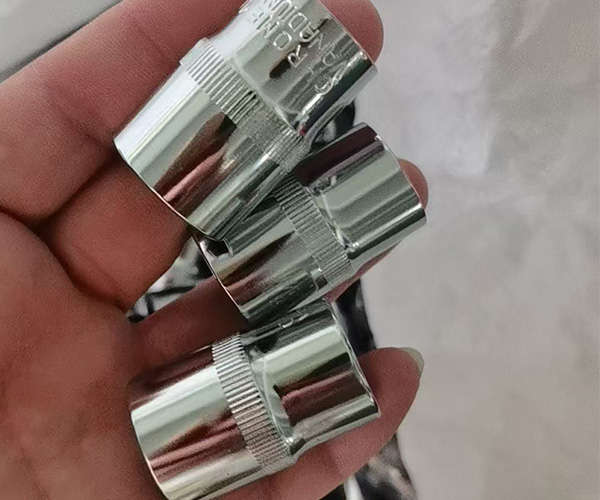
Design and Purpose
The design of regular sockets includes thinner walls and a polished chrome finish. This design choice helps reduce the overall weight of the socket, making it easier to maneuver and use with hand tools. Regular sockets are intended for everyday tasks and are well-suited for applications where precision and ease of use are more critical than the ability to handle extreme torque.
Comparison: Impact vs. Regular Sockets
When deciding between impact sockets and regular sockets, it’s important to understand the differences in material, design, and intended use. Here’s a detailed comparison:
Material & Construction
Impact sockets are made from chrome molybdenum steel, which is more resistant to extreme stress and wear compared to chrome vanadium steel used in regular sockets. The added strength of impact sockets helps them endure the high torque generated by impact tools without breaking.
Regular sockets, constructed from chrome vanadium steel, offer sufficient strength for most standard applications but may not handle the same level of stress as impact sockets. The choice of material reflects the intended use, with impact sockets built to withstand high-impact forces and regular sockets designed for more routine tasks.
Locking Pins
Impact sockets often feature a cross hole for locking pins, which ensures that the socket remains securely attached to the impact tool. This feature prevents accidental detachment and enhances safety during use. Regular sockets do not typically include locking pins, as they are intended for use with hand tools where such security measures are not as critical.
Usage
Impact sockets are best suited for heavy-duty tasks where high torque is required, such as automotive repairs and construction work. They are designed to handle the stress of impact tools and provide the strength needed for tough jobs.
Regular sockets, in contrast, are ideal for everyday maintenance and repair tasks using hand tools. They are versatile and can be used for a wide range of applications, including light automotive work, home repairs, and DIY projects.
Pricing
Impact sockets are generally more expensive due to their robust construction and specialized design. The higher cost reflects the durability and strength needed to withstand high-impact forces.
Regular sockets are more affordable, making them a cost-effective option for those who need reliable tools for standard tasks. Their lower price point makes them accessible for a wide range of users, from hobbyists to professionals.
Gripping Ability
The gripping ability of a socket can influence its performance in various tasks. Impact sockets are designed with features that enhance their grip on fasteners, reducing the risk of slipping under high torque conditions. Regular sockets, while not as specialized, still offer adequate gripping power for standard applications.
Shape and Design
Impact sockets typically have a more robust design with thicker walls and a black oxide finish. This design enhances their ability to handle high torque and resist corrosion.
Regular sockets have a thinner, lighter design with a chrome finish that provides a sleek appearance and protection against rust. Their design focuses on maneuverability and ease of use with hand tools.
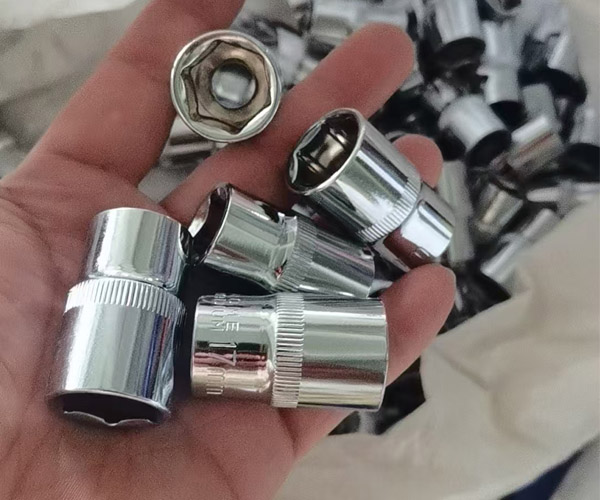
Heat Treating Capability
Impact sockets undergo rigorous heat treating processes to ensure they can withstand the high stresses of impact tools. This process enhances their strength and durability, making them suitable for demanding tasks.
Regular sockets also undergo heat treating, but to a lesser extent than impact sockets. This treatment provides sufficient durability for standard tasks without the need for the extreme strength required by impact sockets.
Size
Both impact and regular sockets come in a range of sizes to fit various fasteners. The choice of size depends on the specific application and the tool being used. Regular sockets typically cover a broad range of sizes suitable for general use.
Advantages of Regular Sockets
Regular sockets offer several advantages that make them a valuable addition to any toolkit. Their benefits extend beyond mere functionality, making them a preferred choice for many users.
Maneuverability
One of the key advantages of regular sockets is their maneuverability. Their thinner walls and lighter design make them easier to handle, especially in tight spaces where precision is required. This feature is particularly beneficial in applications such as automotive repairs, where access to confined areas is often necessary.
Versatility
Regular sockets are known for their versatility. They are suitable for a wide range of tasks, from basic home repairs to more complex automotive work. Their ability to handle various sizes of fasteners and bolts makes them an essential tool for many different projects.
Cost-Effectiveness
Regular sockets are generally more affordable compared to impact sockets. This cost-effectiveness makes them an attractive option for those who need reliable tools without breaking the bank. The lower price point allows users to build a comprehensive socket set without significant financial investment.
Durability
While not as heavy-duty as impact sockets, regular sockets still offer a good level of durability. Made from chrome vanadium steel, they provide adequate strength for most standard applications. With proper care and maintenance, regular sockets can serve effectively for many years.
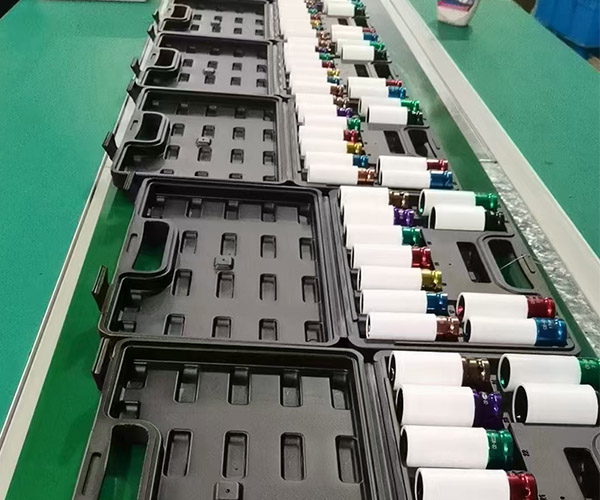
Safety Considerations
Using the right type of socket is crucial for safety. Impact sockets are specifically designed for high-torque impact tools and should not be used with hand tools due to their unique construction. Conversely, regular sockets are intended for use with hand tools and may not withstand the stresses of impact tools.
Risks of Using Regular Sockets with Impact Tools
Using regular sockets with impact tools can pose several risks. The thinner walls and different construction of regular sockets make them less capable of handling the high torque and rapid bursts delivered by impact tools. This mismatch can lead to socket failure, which may result in injury or damage to the workpiece.
Recommended Uses for Each Type of Socket
To ensure safety and effectiveness, it is essential to use the appropriate socket for the task at hand. Impact sockets should be used exclusively with impact tools, while regular sockets are best suited for manual hand tools. Following these guidelines will help prevent accidents and ensure optimal performance.
Common Problems and Solutions
Even the best tools can encounter issues over time. Understanding common problems with regular sockets and their solutions can help maintain their effectiveness and extend their lifespan.
Socket Slippage and Fit Issues
Socket slippage occurs when a socket does not securely fit the fastener, leading to ineffective torque application and potential damage. This issue is often caused by using a socket that does not match the size of the fastener precisely or by wear and tear on the socket.
Solutions:
- Ensure Proper Fit: Always choose the correct socket size for the fastener. Using a socket that fits snugly will reduce the risk of slippage and ensure effective torque application.
- Regular Inspection: Check sockets regularly for signs of wear or deformation. Replace any sockets that show signs of significant damage or wear to prevent further issues.
- Avoid Over-Torquing: Using excessive force can cause slippage and damage. Apply the recommended amount of torque to prevent overloading the socket.
Rust and Corrosion
Rust and corrosion can affect the performance and appearance of regular sockets, particularly if they are exposed to moisture or harsh environments. The chrome finish on regular sockets provides some protection, but it is not entirely rust-proof.
Solutions:
- Proper Storage: Store sockets in a dry environment to prevent exposure to moisture. Using a tool chest or cabinet with proper ventilation can help reduce the risk of rust.
- Regular Cleaning: Clean sockets regularly to remove any contaminants that could lead to corrosion. Use a dry cloth to wipe off any moisture and apply a light oil to maintain the finish.
- Use Rust-Preventive Sprays: Applying a rust-preventive spray can offer additional protection against corrosion, especially if tools are stored in less controlled environments.
Wear and Tear
Regular use of sockets will inevitably lead to wear and tear, affecting their performance and longevity. Common signs of wear include rounded edges, decreased gripping ability, and visible cracks or deformation.
Solutions:
- Regular Maintenance: Inspect sockets for signs of wear and replace any that are significantly damaged. Regular maintenance can help identify issues before they impact performance.
- Follow Manufacturer Guidelines: Adhere to the manufacturer’s recommendations for usage and maintenance to ensure sockets remain in good condition.
- Proper Use: Use sockets only for their intended purposes. Avoid using them for tasks that exceed their designed capacity to prevent unnecessary wear.
Practical Applications and Examples
Regular sockets are versatile tools with applications across various fields. Understanding their practical uses can help users make the most of their socket sets.
Automotive Repairs
In automotive repair, regular sockets are used for tasks such as removing and installing bolts, nuts, and fasteners. Their versatility makes them suitable for a range of applications, from routine maintenance to more complex repairs.
Examples:
- Changing Oil: Regular sockets can be used to remove oil drain plugs and other components during an oil change.
- Replacing Parts: Use regular sockets for tasks like replacing spark plugs or alternator bolts.
Woodworking and DIY Projects
For woodworking and DIY projects, regular sockets are valuable for assembling furniture, securing hardware, and performing general repairs. Their maneuverability and ease of use make them a preferred choice for many home improvement tasks.
Examples:
- Assembling Furniture: Regular sockets are useful for tightening bolts and nuts in flat-pack furniture assembly.
- DIY Repairs: Use them for various home repairs, such as fixing cabinetry or securing fixtures.
Professional Use
Professionals in fields such as construction, maintenance, and repair rely on regular sockets for their versatility and reliability. They are commonly used in workshops and job sites for various tasks that require precise and reliable tools.
Examples:
- Construction: Regular sockets assist in securing structural components and assembling machinery.
- Maintenance: Use them for routine maintenance tasks, including equipment repairs and part replacements.
Conclusion
Regular sockets offer numerous advantages that make them a valuable addition to any toolkit. Their versatility, cost-effectiveness, and durability make them suitable for a wide range of applications, from automotive repairs to DIY projects. By understanding their benefits and proper usage, users can maximize their efficiency and ensure their tools remain in good condition.
Summary of Main Points
- Material and Construction: Regular sockets are made from chrome vanadium steel, offering a balance of strength and affordability. Their thinner walls and chrome finish make them suitable for hand tools.
- Design and Purpose: Designed for use with hand tools, regular sockets provide maneuverability and versatility for various tasks.
- Comparison with Impact Sockets: Regular sockets differ from impact sockets in terms of material, design, and intended use. They are not suitable for high-torque impact tools but excel in standard applications.
- Advantages: Regular sockets offer ease of use, cost-effectiveness, and good durability for everyday tasks.
- Safety Considerations: Using the right socket for the right tool is crucial for safety and performance.
Recommendations for Use
To get the most out of your regular sockets, choose the correct size for your tasks, maintain them regularly, and use them for their intended purposes. Proper care will ensure their longevity and effectiveness.
Call to Action
Explore our range of regular sockets to find the perfect set for your needs. Whether you’re a professional mechanic or a DIY enthusiast, having the right tools can make all the difference in your projects. Visit our website to learn more about our products and find the best options for your toolkit.
Additional Resources
- Further Reading and References: For more detailed information on socket types and their applications, check out our other blog posts and guides.
- Product Recommendations: Discover our selection of high-quality regular sockets and socket sets designed to meet your needs. Browse our catalog for options that offer reliability and performance.