Introduction
A torque wrench is an essential tool in the arsenal of both professionals and DIY enthusiasts, offering precise control over the amount of torque applied to a fastener. This control is crucial for ensuring that bolts and nuts are neither under-tightened, which can lead to loosening and potential failure, nor over-tightened, which can cause damage to the fastener or the parts being assembled. Whether you’re working on automotive repairs, assembling machinery, or performing maintenance tasks, understanding how to use a torque wrench effectively is key to achieving optimal results and ensuring safety.
In this comprehensive guide, we will delve into the various types of torque wrenches available, how to choose the right one for your needs, and step-by-step instructions on how to use them properly. Additionally, we will cover essential topics such as tool calibration, maintenance, and common mistakes to avoid. By the end of this article, you will have a thorough understanding of torque wrenches, enabling you to use them confidently and accurately in any application.
What is a Torque Wrench?
A torque wrench is a precision tool designed to apply a specific amount of force to a fastener, such as a bolt or nut. The primary function of a torque wrench is to ensure that the fastener is tightened to the manufacturer’s specified torque value. This is crucial in various applications, from automotive repairs to industrial machinery, where precise torque measurement is essential to maintain the integrity of the assembly and ensure safety.
Torque wrenches come in various types, each designed to suit specific tasks and levels of precision. The most common types include click-type, beam-type, digital, and dial-type torque wrenches. Each type has its unique features and benefits, which we will explore in detail later in this article.
Why Accurate Torque Matters
Accurate torque application is critical in any assembly process, whether it’s tightening the lug nuts on a car wheel or securing bolts in a mechanical system. The importance of applying the correct torque cannot be overstated, as it directly impacts the performance, safety, and longevity of the assembly.
When a fastener is under-tightened, it may not provide the necessary clamping force, leading to loosening during operation. This can cause parts to shift or separate, resulting in malfunction or even catastrophic failure. On the other hand, over-tightening a fastener can stretch or deform it, potentially stripping the threads or damaging the components it secures. This can lead to costly repairs, equipment downtime, and safety hazards.
Therefore, using a torque wrench to achieve the correct torque is essential in any application where the integrity of the assembly is critical. Whether you’re working with sensitive electronic components, structural steel, or high-performance engines, precise tightening is the key to ensuring that everything stays securely in place without damaging the parts involved.
Types of Torque Wrenches
There are several types of torque wrenches available, each with specific advantages depending on the application. Below, we will explore the most commonly used types: click-type, beam-type, digital, and dial-type torque wrenches.
Click-Type Torque Wrench
The click-type torque wrench is perhaps the most popular and widely used type. It operates on a simple yet effective mechanism: when the desired torque setting is reached, the wrench emits a clicking sound, signaling the user to stop applying force. This click is generated by a calibrated spring mechanism inside the wrench, which releases a small amount of tension when the preset torque is achieved.
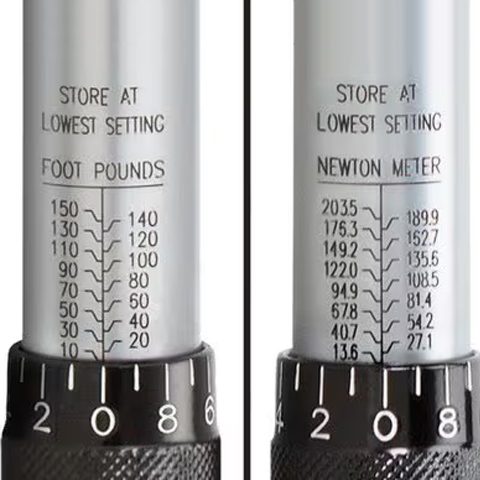
Advantages of Click-Type Torque Wrenches:
- Ease of Use: The click-type wrench is user-friendly, making it an excellent choice for both professionals and DIYers.
- Accuracy: This type of wrench provides consistent and reliable torque readings, essential for precise tightening.
- Versatility: Available in various sizes and torque ranges, click-type wrenches are suitable for a wide range of applications.
Common Uses: Click-type torque wrenches are widely used in automotive repairs, such as tightening lug nuts, as well as in mechanical assembly and maintenance tasks where precise torque application is crucial.
Beam-Type Torque Wrench
The beam-type torque wrench is a simple and cost-effective tool that has been around for decades. It consists of a long lever arm with a scale and a pointer attached. As torque is applied, the beam deflects, and the pointer moves along the scale, indicating the amount of torque being applied.
Advantages of Beam-Type Torque Wrenches:
- Durability: With no moving parts, beam-type wrenches are incredibly durable and require minimal maintenance.
- Affordability: These wrenches are typically less expensive than other types, making them a cost-effective option for many users.
- Immediate Feedback: The user can see the torque being applied in real-time, allowing for precise adjustments.
Drawbacks:
- User Skill: Beam-type wrenches require the user to read the scale accurately while applying torque, which can be challenging in tight or awkward spaces.
- Size and Bulk: They tend to be larger and bulkier than other types, which can limit their use in confined areas.
Common Uses: Beam-type torque wrenches are often used in applications where durability and simplicity are more important than speed or ease of use. They are commonly found in automotive repair shops and home garages.
Digital Torque Wrench
Digital torque wrenches represent the latest in torque wrench technology. These wrenches use electronic sensors to measure and display the applied torque on a digital screen. Some models also offer additional features such as memory storage, data logging, and connectivity to other devices for data transfer.
Advantages of Digital Torque Wrenches:
- Precision: Digital wrenches provide highly accurate torque readings, making them ideal for critical applications.
- Ease of Use: The digital display makes it easy to set and read the desired torque value, reducing the likelihood of user error.
- Advanced Features: Many digital wrenches offer features like programmable settings, alert systems, and data storage, which are beneficial for professional users.
Drawbacks:
- Cost: Digital torque wrenches are generally more expensive than other types due to their advanced technology.
- Battery Dependency: These wrenches require batteries to operate, which can be a drawback if the battery dies during use.
Common Uses: Digital torque wrenches are used in high-precision applications, such as in aerospace, automotive manufacturing, and mechanical engineering, where accurate torque measurement is critical.
Dial-Type Torque Wrench
The dial-type torque wrench is known for its high accuracy and ease of use. It features a dial gauge that displays the applied torque, allowing the user to monitor and adjust the force in real-time. Unlike click-type wrenches, dial-type wrenches provide continuous feedback without requiring the user to reset the tool after each use.
Advantages of Dial-Type Torque Wrenches:
- Accuracy: Dial-type wrenches are among the most accurate torque wrenches available, making them ideal for precision tasks.
- Continuous Feedback: The dial gauge provides real-time feedback, allowing for precise control over the applied torque.
- Durability: These wrenches are built to withstand heavy use in demanding environments.
Drawbacks:
- Size and Weight: Dial-type wrenches can be heavier and bulkier than other types, making them less suitable for use in tight spaces.
- Cost: These wrenches are generally more expensive due to their precision and durability.
Common Uses: Dial-type torque wrenches are commonly used in industries where precision is paramount, such as in aerospace, military, and automotive manufacturing. They are also favored in quality control settings, where accurate and repeatable torque measurements are required.
How to Choose the Right Torque Wrench
Selecting the right torque wrench for your needs involves considering several factors, including the specific application, budget, and desired level of precision. Here’s a detailed guide to help you make an informed decision.
Application-Specific Requirements
The first step in choosing a torque wrench is to determine the specific requirements of your application. Different tasks may require different torque ranges, levels of precision, and tool types. For instance, if you are working on automotive repairs, such as tightening lug nuts, a click-type torque wrench with a moderate torque range would be suitable. However, if you are involved in assembling delicate machinery or electronics, a digital torque wrench with high precision might be necessary.
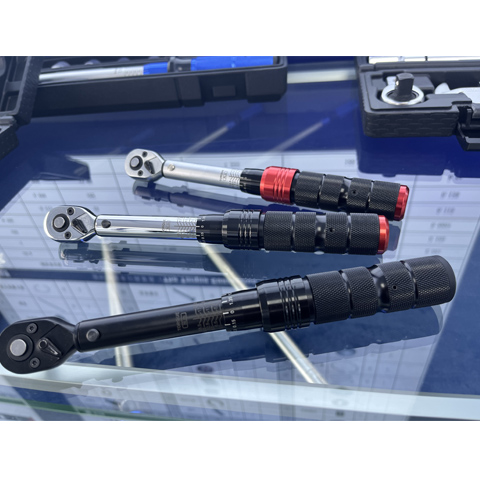
Factors to Consider:
- Torque Range: Ensure that the wrench you choose can cover the required torque range for your task. It’s generally recommended to select a wrench with a torque range that allows you to work within 20% to 80% of its capacity, as this is where most torque wrenches are most accurate.
- Accuracy: Depending on the application, you may need a torque wrench with a high level of accuracy. For critical applications, such as in aerospace or high-performance automotive work, a digital or dial-type wrench might be necessary.
- Size and Accessibility: Consider the physical size of the wrench and the accessibility of the area where you’ll be working. In tight spaces, a smaller wrench or one with a flexible head may be required.
Budget Considerations
Your budget is another important factor when choosing a torque wrench. While it’s tempting to opt for the cheapest option, it’s essential to balance cost with quality and accuracy. Investing in a higher-quality wrench can save you money in the long run by reducing the risk of over-tightening or under-tightening fasteners, which can lead to costly repairs or safety issues.
Options for Different Budgets:
- Entry-Level: If you’re on a tight budget and only need a torque wrench for occasional use, a beam-type or lower-end click-type wrench might be sufficient.
- Mid-Range: For regular use, consider investing in a higher-quality click-type wrench or a basic digital wrench. These offer better accuracy and durability without breaking the bank.
- High-End: For professional use or highly precise applications, it’s worth investing in a top-of-the-line digital or dial-type torque wrench. While more expensive, these tools offer unparalleled accuracy, advanced features, and durability.
Brand and Quality
The brand and quality of a torque wrench can significantly impact its performance and longevity. Established brands with a reputation for quality typically offer more reliable and accurate tools, backed by warranties and customer support. When choosing a torque wrench, it’s advisable to do some research on the brand’s reputation and read reviews from other users.
Top Brands to Consider:
- Snap-on: Known for its high-quality tools, Snap-on offers a wide range of torque wrenches that are favored by professionals in various industries.
- Craftsman: A reliable brand offering affordable and durable torque wrenches suitable for both DIYers and professionals.
- Tekton: Provides a range of torque wrenches with excellent value for money, known for their accuracy and reliability.
- GearWrench: Offers a variety of torque wrenches, including digital models, known for their precision and ease of use.
Choosing a reputable brand ensures that you’re investing in a tool that will provide consistent performance and last for years, reducing the likelihood of inaccuracies and the need for frequent calibration or replacement.
Preparation Before Using a Torque Wrench
Before you begin using a torque wrench, it’s essential to prepare properly to ensure accurate and safe operation. This involves understanding torque specifications, calibrating the tool, and taking necessary safety precautions.
Understanding Torque Specifications
Torque specifications are critical in ensuring that fasteners are tightened to the correct level, neither too loose nor too tight. These specifications are typically provided by the manufacturer of the parts or equipment you’re working with and are usually expressed in units of force, such as pound-feet (lb-ft) or newton-meters (Nm).
How to Find and Interpret Torque Specifications:
- Owner’s Manuals: The most reliable source of torque specifications is the owner’s manual or service manual for the equipment or vehicle you’re working on. These manuals typically provide detailed torque values for all fasteners.
- Online Resources: Many manufacturers also provide torque specifications on their websites or through online databases. Ensure that you’re accessing official and up-to-date information.
- Torque Specification Charts: Some tasks, such as tightening automotive lug nuts, may be covered by general torque specification charts that provide recommended torque values based on the size and grade of the fastener.
Reading Torque Specifications:
- Units of Measurement: Torque is typically measured in either pound-feet (lb-ft) or newton-meters (Nm). Make sure to use the correct unit when setting your torque wrench.
- Torque Ranges: Some tasks may provide a range of acceptable torque values (e.g., 80-100 lb-ft). In such cases, aim for the midpoint of the range to ensure optimal clamping force.
- Tightening Sequence: For assemblies with multiple fasteners, such as cylinder heads or wheels, the manufacturer may specify a tightening sequence. Follow this sequence to ensure even distribution of clamping force.
Calibration and Maintenance
Calibration is essential for ensuring that your torque wrench provides accurate readings. Over time, the internal components of a torque wrench can wear out or drift out of calibration, leading to inaccurate torque application.
Importance of Regular Calibration:
- Accuracy: Regular calibration ensures that your torque wrench continues to deliver accurate torque measurements, preventing under-tightening or over-tightening.
- Compliance: In professional settings, regular calibration is often required to comply with industry standards and regulations.
- Longevity: Proper calibration and maintenance can extend the life of your torque wrench, reducing the need for costly replacements.
Steps for Maintaining and Calibrating Your Torque Wrench:
- Calibration Frequency: As a general rule, a torque wrench should be calibrated every 5,000 cycles or once a year, whichever comes first. However, if the wrench is used frequently or in critical applications, more frequent calibration may be necessary.
- DIY Calibration Checks: While professional calibration is recommended, you can perform basic calibration checks at home using a known weight and a lever arm. If the readings are significantly off, professional calibration is necessary.
- Storage and Handling: Always store your torque wrench in its protective case when not in use, and avoid dropping or subjecting it to shock. This helps maintain its accuracy and prolongs its lifespan.
Safety Precautions
Using a torque wrench safely is crucial to prevent accidents and ensure accurate results. While torque wrenches are generally easy to use, improper handling or misuse can lead to serious consequences, including injury or damage to the tool or the workpiece.
Essential Safety Tips:
- Read the Manual: Before using a torque wrench, read the manufacturer’s instructions carefully. This will help you understand the specific features and limitations of your tool.
- Wear Protective Gear: Depending on the task, consider wearing safety glasses, gloves, and other protective gear to protect yourself from potential hazards.
- Avoid Over-Tightening: Stop applying force as soon as the desired torque is reached. Over-tightening can damage the fastener or the components it secures.
- Use the Correct Torque Range: Never use a torque wrench beyond its specified torque range, as this can damage the tool and result in inaccurate torque application.
By following these preparation steps, you can ensure that your torque wrench is ready for use and that you’re equipped to achieve precise and safe tightening in any application.
Step-by-Step Guide to Using a Torque Wrench
Using a torque wrench correctly involves several steps, from setting the desired torque value to applying the force and securing the fastener. Here’s a detailed, step-by-step guide to help you achieve accurate and consistent results.
Setting the Desired Torque
The first step in using a torque wrench is to set the desired torque value. This process varies slightly depending on the type of torque wrench you’re using, but the general principles are the same.
How to Set the Torque on Different Wrench Types:
- Click-Type Torque Wrench: Turn the handle of the wrench to adjust the torque setting, aligning the desired value with the reference line on the handle. Once set, lock the handle in place to prevent accidental adjustments during use.
- Digital Torque Wrench: Use the buttons or dial on the wrench to select the desired torque value, which will be displayed on the digital screen. Some digital wrenches allow you to store multiple torque settings for easy access.
- Beam-Type Torque Wrench: Since beam-type wrenches do not have a preset mechanism, you will need to monitor the scale while applying torque to reach the desired value.
- Dial-Type Torque Wrench: Rotate the dial to the desired torque value, ensuring that the indicator aligns with the correct setting.
Calibration Verification:
- Before using the wrench, it’s a good idea to verify its calibration, especially if it hasn’t been used in a while. Check for any signs of wear or damage, and if possible, perform a quick calibration check using a known weight.
Positioning the Wrench
Proper positioning of the torque wrench is crucial for accurate torque application. The wrench should be aligned with the axis of the fastener, and the handle should be gripped firmly.
Steps for Proper Positioning:
- Align with the Fastener: Ensure that the torque wrench is perfectly aligned with the fastener. Misalignment can lead to inaccurate torque readings and potential damage to the fastener.
- Secure Fit: Attach the wrench securely to the fastener, ensuring that it is fully engaged. A loose fit can cause the wrench to slip, leading to inaccurate torque application.
- Grip the Handle: Hold the handle of the wrench firmly, applying force evenly along its length. Avoid applying pressure to the head of the wrench, as this can affect the accuracy of the torque reading.
Applying Torque
Once the wrench is positioned correctly, you can begin applying torque. The key to accurate torque application is to apply force steadily and smoothly until the desired torque value is reached.
Techniques for Smooth and Steady Application:
- Apply Even Pressure: Apply pressure evenly and gradually, avoiding sudden jerks or rapid movements. This helps ensure that the torque is applied accurately and consistently.
- Listen for the Click: If you’re using a click-type torque wrench, listen for the distinctive click sound that indicates the desired torque has been reached. Stop applying force as soon as you hear the click.
- Monitor the Display: For digital and dial-type wrenches, monitor the display or dial gauge to see the torque value as you apply force. Stop when the desired value is reached.
Post-Use Procedures
After you’ve applied the correct torque, it’s important to follow proper post-use procedures to maintain the accuracy and longevity of your torque wrench.
Releasing the Tension:
- For click-type and dial-type wrenches, always release the tension by setting the torque value back to the lowest setting (usually the minimum torque value) after use. This helps prevent the internal spring mechanism from becoming fatigued.
Proper Storage Methods:
- Store the torque wrench in its protective case, away from moisture, dust, and extreme temperatures. This will help maintain its accuracy and extend its lifespan.
Following these steps will help you use your torque wrench effectively, ensuring that fasteners are tightened to the correct specifications every time.
Common Mistakes and How to Avoid Them
Even with careful preparation, it’s easy to make mistakes when using a torque wrench, especially if you’re not familiar with the tool. Understanding these common errors can help you avoid them and ensure that you achieve accurate and consistent results every time you use your wrench.
Over-Tightening or Under-Tightening
One of the most common mistakes is applying too much or too little torque to a fastener. Over-tightening can strip threads, warp components, and cause unnecessary stress on the fastener, while under-tightening can lead to loosening, leaks, and potential failure of the assembly.
Causes of Over-Tightening:
- Ignoring the Click: With a click-type torque wrench, it’s easy to miss or ignore the click sound, especially in noisy environments. Continuing to apply force after the click results in over-tightening.
- Incorrect Torque Setting: Setting the wrench to the wrong torque value, either too high or too low, is a common error, often due to misreading the scale or accidentally adjusting the setting.
Preventing Over-Tightening and Under-Tightening:
- Focus on the Task: Pay close attention to the wrench, especially when approaching the desired torque. For click-type wrenches, stop immediately after hearing the click.
- Double-Check Settings: Before applying torque, double-check the wrench’s settings to ensure they match the specified torque value for the task. This simple step can prevent many common errors.
- Use the Right Wrench: Ensure that the torque wrench is appropriate for the torque range of the task. Using a wrench with a torque range that doesn’t match the job can lead to inaccurate application.
Not Resetting the Wrench After Use
Failing to reset the torque wrench to its lowest setting after use is a common mistake that can affect the tool’s accuracy over time. When the wrench is left loaded (with the spring still compressed), the internal components can become fatigued, leading to inaccurate torque readings in future uses.
Consequences of Not Resetting the Wrench:
- Loss of Accuracy: The most immediate consequence is a loss of accuracy. The wrench may no longer apply the correct torque, leading to under-tightening or over-tightening.
- Increased Wear: Keeping the wrench loaded puts constant stress on the internal components, accelerating wear and shortening the tool’s lifespan.
How to Avoid This Mistake:
- Develop a Habit: Make it a habit to reset the wrench to its lowest setting immediately after use. This small step can greatly extend the life of your torque wrench and ensure continued accuracy.
- Store Properly: Store the wrench in a dedicated case to remind yourself to reset it after each use.
Skipping Calibration
Calibration is essential to maintaining the accuracy of a torque wrench. Skipping this step can lead to inaccurate torque application, which can compromise the safety and integrity of the assembly.
Risks of Using an Uncalibrated Wrench:
- Inaccurate Torque Application: An uncalibrated wrench can drift out of specification, leading to over-tightening or under-tightening without the user realizing it.
- Non-Compliance: In professional settings, using an uncalibrated wrench can lead to non-compliance with industry standards, potentially resulting in penalties or rework.
How Often to Calibrate:
- Regular Use: For wrenches used regularly, calibration should be performed every 5,000 cycles or once a year, whichever comes first.
- Critical Applications: In critical applications, such as aerospace or automotive manufacturing, more frequent calibration may be necessary, especially if the wrench is used daily.
Using the Wrong Torque Wrench for the Job
Not all torque wrenches are created equal, and using the wrong type of wrench can lead to inaccurate torque application and potential damage to the tool or the fastener.
Examples of Mismatched Wrenches and Tasks:
- Using a Click-Type Wrench for Continuous Feedback: Click-type wrenches are not suitable for tasks that require continuous torque feedback, such as delicate assembly work. In these cases, a dial-type or beam-type wrench is more appropriate.
- Using a Beam-Type Wrench in Tight Spaces: Beam-type wrenches can be difficult to use in confined spaces due to their size and the need for a clear line of sight to read the scale.
Avoiding Mismatches:
- Understand the Task Requirements: Before starting a job, consider the specific torque requirements and the environment in which you’ll be working. Choose a torque wrench that matches these needs.
- Have Multiple Wrenches Available: If possible, keep a selection of torque wrenches on hand to cover a range of tasks and torque values.
By being aware of these common mistakes and taking steps to avoid them, you can ensure that your torque wrench provides accurate and reliable results every time.
Advanced Tips for Using a Torque Wrench
For those who are already familiar with the basics of using a torque wrench, advanced techniques can help further improve accuracy and efficiency. These tips are particularly useful for professional users or in applications where precision is critical.
Understanding Torque vs. Tightening Angle
While torque is the primary measure used to tighten fasteners, in some cases, a combination of torque and angle is required to achieve the correct clamping force. This is particularly common in automotive applications, where torque-to-yield fasteners are used.
When to Use Angle Over Torque:
- Torque-to-Yield Fasteners: These fasteners are designed to be tightened to a specific torque, followed by an additional angle of rotation. This method ensures that the fastener is stretched to its yield point, providing maximum clamping force.
- Critical Joints: In joints where precise clamping force is critical, using both torque and angle can provide a more accurate and consistent result than torque alone.
How to Combine Torque and Angle:
- Use a Torque Wrench with Angle Measurement: Some digital torque wrenches offer built-in angle measurement, allowing you to set both the torque and the angle on the same tool.
- Marking the Fastener: If you don’t have a wrench with angle measurement, you can manually mark the fastener and the surrounding area before tightening, then rotate the fastener by the specified angle after reaching the torque value.
Using Extensions and Adapters
Extensions and adapters are often necessary when working in tight or awkward spaces, but they can affect the torque applied to the fastener. Understanding how to correct for these effects is essential for maintaining accuracy.
How Extensions Affect Torque Readings:
- Length of Extension: Using an extension increases the distance from the wrench to the fastener, which can slightly alter the torque reading. The longer the extension, the more significant the effect.
- Angle of Application: Applying torque at an angle (rather than perpendicular to the fastener) can also affect the accuracy of the torque reading.
Correcting for Inaccuracies:
- Use a Torque Extension Calculator: Some manufacturers provide torque extension calculators or charts that help you adjust the torque setting based on the length of the extension and the desired torque value.
- Check the Angle: Always ensure that the wrench is applied as close to perpendicular as possible to the fastener. If you must use an angle, adjust the torque setting accordingly.
Checking and Re-Torquing
In some cases, it may be necessary to check and re-torque fasteners after an initial tightening. This is particularly important in applications where fasteners are subject to vibration or thermal expansion.
When to Re-Torque:
- After Initial Operation: For some assemblies, such as engine components, it’s advisable to re-torque fasteners after the assembly has been subjected to initial operation or thermal cycling. This helps ensure that the fasteners remain secure as the components settle.
- Maintenance Checks: In applications subject to vibration, such as heavy machinery or automotive components, periodic re-torqueing may be necessary to maintain clamping force and prevent loosening.
Best Practices for Re-Torquing:
- Use the Same Torque Wrench: To ensure consistency, use the same torque wrench that was used for the initial tightening, if possible.
- Follow Manufacturer Guidelines: Always follow the manufacturer’s guidelines for re-torqueing intervals and procedures.
By mastering these advanced techniques, you can achieve even greater precision and reliability in your torque applications, ensuring that your assemblies are secure and long-lasting.
Troubleshooting and Maintenance
Even with careful use, torque wrenches can experience issues over time. Knowing how to troubleshoot common problems and maintain your tool can help extend its lifespan and ensure ongoing accuracy.
Recognizing Wear and Tear
Over time, torque wrenches can develop wear and tear that affects their accuracy and performance. Recognizing the signs early can prevent further damage and maintain the tool’s reliability.
Signs Your Torque Wrench Needs Repair or Replacement:
- Inconsistent Torque Readings: If the torque readings vary significantly from use to use, even with the same setting, it may indicate internal wear or damage.
- Physical Damage: Cracks, dents, or bends in the wrench’s handle or head can compromise its accuracy and safety.
- Difficulty Setting Torque: If the adjustment mechanism becomes stiff or unresponsive, it may be a sign of internal issues that need to be addressed.
What to Do If You Notice Wear and Tear:
- Stop Using the Wrench: If you notice any signs of wear or damage, stop using the wrench immediately to prevent further damage or inaccurate torque application.
- Consult a Professional: For significant wear or damage, it’s best to consult a professional for repair or calibration. In some cases, it may be more cost-effective to replace the wrench.
DIY Calibration Check
While professional calibration is recommended, you can perform a basic calibration check at home to ensure that your torque wrench is within an acceptable range of accuracy.
Simple Methods to Check Calibration:
- Use a Known Weight: Attach a known weight to the end of the wrench’s handle and apply torque to a secure, stationary object. Compare the torque reading to the expected value based on the weight and the length of the wrench’s handle.
- Compare with Another Wrench: If you have access to another torque wrench that is known to be accurate, use it to check your wrench’s readings by applying the same torque to a fastener and comparing the results.
When to Seek Professional Calibration:
- Significant Deviation: If your DIY calibration check reveals a significant deviation from the expected torque value, it’s time to seek professional calibration or repair.
- Annual Maintenance: Even if your wrench appears to be accurate, it’s still a good idea to have it professionally calibrated at least once a year, especially if it’s used frequently.
Professional Servicing
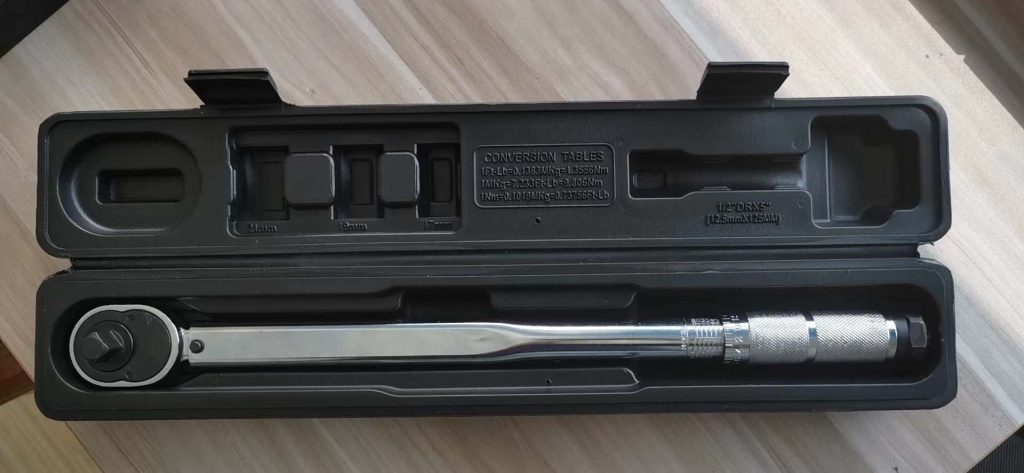
In some cases, professional servicing is necessary to restore your torque wrench’s accuracy and functionality. This is especially true for digital and high-precision wrenches, which may require specialized tools and expertise for calibration and repair.
When to Seek Professional Calibration and Servicing:
- Digital Wrenches: Digital torque wrenches are complex tools that require specialized equipment for calibration. If your digital wrench is displaying inaccurate readings or other issues, professional servicing is recommended.
- Heavily Used Wrenches: Wrenches used in demanding environments or for critical applications should be serviced more frequently to ensure ongoing accuracy and reliability.
Finding Certified Service Centers:
- Manufacturer’s Website: Most manufacturers offer a list of certified service centers on their websites. These centers are equipped to handle calibration and repairs according to the manufacturer’s specifications.
- Local Tool Shops: Some local tool shops may also offer calibration and repair services. Be sure to verify that they are certified to work on your specific brand and model of torque wrench.
By staying on top of maintenance and addressing issues as they arise, you can ensure that your torque wrench remains a reliable tool in your arsenal, providing accurate torque readings for years to come.
FAQs About Torque Wrenches
In this section, we’ll address some common questions about torque wrenches to help you gain a deeper understanding of how to use and maintain this essential tool.
What Size Torque Wrench Should I Buy?
- Answer: The size of the torque wrench you need depends on the range of torque values you’ll be working with. For most automotive applications, a wrench with a range of 10-150 lb-ft is sufficient. For more specialized tasks, such as working with small fasteners, a smaller wrench with a range of 5-25 lb-ft may be necessary.
Can I Use a Torque Wrench as a Ratchet?
- Answer: While some torque wrenches can function as ratchets, it’s generally not recommended to use them for this purpose. Torque wrenches are precision tools, and using them as a ratchet can lead to wear and tear, affecting their accuracy. It’s best to use a dedicated ratchet for loosening and tightening fasteners before using the torque wrench to apply the final torque.
How Do I Store a Torque Wrench?
- Answer: Store your torque wrench in a protective case, away from moisture, dust, and extreme temperatures. Always reset the wrench to its lowest torque setting before storage to prevent the internal spring from becoming fatigued.
How Often Should I Calibrate My Torque Wrench?
- Answer: Torque wrenches should be calibrated every 5,000 cycles or once a year, whichever comes first. However, if the wrench is used frequently or in critical applications, more frequent calibration may be necessary.
Can I Use a Torque Wrench for Both Tightening and Loosening?
- Answer: Torque wrenches are designed for tightening fasteners to a specific torque value. While some wrenches can be used for loosening, it’s generally not recommended, as this can affect the tool’s accuracy and durability. Use a standard ratchet or breaker bar for loosening fasteners instead.
Conclusion
Torque wrenches are indispensable tools for ensuring that fasteners are tightened to the correct specifications, which is crucial for the safety, performance, and longevity of any assembly. By understanding how to choose the right torque wrench, preparing it for use, and following best practices for operation, you can achieve precise and consistent results every time.
Whether you’re a professional mechanic, an engineer, or a DIY enthusiast, investing in a high-quality torque wrench and using it correctly will pay off in the long run by preventing damage, ensuring safety, and reducing the likelihood of costly repairs. Remember to avoid common mistakes, keep your wrench calibrated, and maintain it properly to ensure it remains a reliable tool in your collection.
As a torque wrench supplier from China, we understand the importance of quality and precision in every tool we provide. If you have any questions or need assistance in selecting the right torque wrench for your needs, don’t hesitate to reach out. We’re here to help you achieve the best results in every project you undertake.