I. Introduction
Sourcing and selecting the right hand tools for your business is more than just a routine task—it’s a critical decision that impacts your operations, productivity, and profitability. Whether you’re running a small workshop, a large-scale manufacturing facility, or a DIY enterprise, having the correct workshop tools can make all the difference. The global hand tools market is continually evolving, driven by advancements in technology, shifting consumer preferences, and the growing demand for durable and efficient tools. Understanding the nuances of this market is essential for any business looking to make informed decisions when sourcing these essential tools.
In today’s competitive landscape, choosing the right tools is not just about filling your shelves. It’s about ensuring that every tool you invest in adds value to your operations, meets the specific needs of your projects, and contributes to the overall safety and efficiency of your workplace. This comprehensive guide is designed to walk you through the entire process of sourcing and selecting hand tools, from understanding the various categories and their applications to evaluating suppliers and managing logistics.
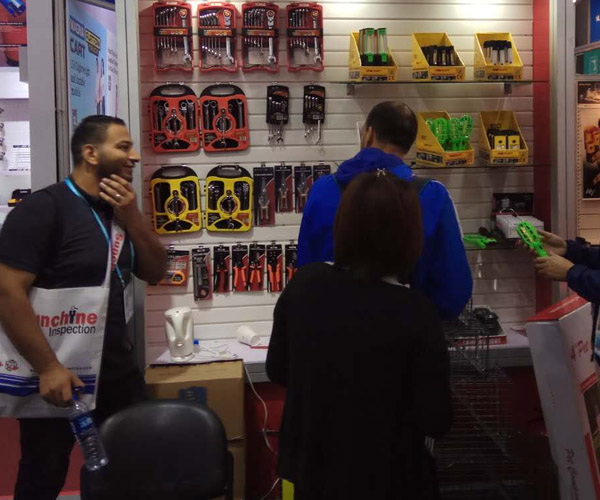
By the end of this guide, you will have a clear understanding of the factors to consider when choosing hand tools, the best practices for sourcing them, and the strategies to ensure you get the best value for your investment. Whether you are new to the industry or looking to refine your sourcing strategy, this guide will provide you with the insights you need to make well-informed decisions.
Let’s dive into the world of hand tools, explore their significance in various industries, and learn how to select and source them effectively to enhance your business operations.
II. Key Tool Categories
When it comes to outfitting your workshop or business, understanding the different categories of tools is crucial. Each category serves specific functions and caters to different aspects of your work, whether you’re involved in DIY projects, woodworking, or industrial applications. In this section, we’ll explore the three primary categories of tools: hand tools, power tools, and specialty tools, and discuss their relevance to your business needs.
Hand Tools
Hand tools are the backbone of any workshop. These are tools powered by human effort rather than electricity or batteries. They include basic yet essential items like screwdrivers, hammers, wrenches, pliers, and more specialized tools like chisels and hand saws. The simplicity and reliability of hand tools make them indispensable across various industries, from construction and automotive repair to home DIY projects.
For instance, screwdrivers and wrenches are critical for assembly tasks, while hammers and pliers are used for construction and repair work. Measuring tools like tape measures and calipers are also crucial for ensuring precision in projects. The durability and precision of hand tools are particularly important, as they often undergo significant wear and tear. Therefore, choosing high-quality hand tools is essential to ensure long-term efficiency and safety in your operations.
Power Tools
While hand tools are vital for many tasks, power tools bring speed and efficiency to more demanding projects. Power tools, such as drills, saws, sanders, and grinders, are powered by electricity or batteries, making them ideal for tasks that require more force or precision than what can be achieved manually. For example, a circular saw can make quick and accurate cuts in wood, a task that would be much slower and more labor-intensive with a hand saw.
Power tools are particularly valuable in industries like woodworking, metalworking, and construction, where the speed and precision of these tools can significantly enhance productivity. The choice of power tools should be guided by the specific requirements of your projects, considering factors like power output, ease of use, and safety features. Additionally, as technology evolves, newer models with advanced features like adjustable speed controls, ergonomic designs, and enhanced safety mechanisms are becoming available, offering even greater value.
Specialty Tools
Specialty tools are designed for specific tasks that regular hand tools or power tools cannot efficiently handle. These include items like welding equipment, woodworking planes, and precision cutting tools. For businesses involved in specialized crafts, such as metalworking, automotive repair, or custom woodworking, specialty tools are essential.
For example, a woodworking plane is used to smooth and shape wood surfaces, while welding equipment is necessary for joining metal parts. These tools often require a higher level of skill and understanding to use effectively, but they are invaluable for achieving professional-grade results. Investing in the right specialty tools can set your business apart by enabling you to offer services or products that require a higher level of craftsmanship.
III. Understanding the Types of Hand Tools
To make informed decisions when sourcing hand tools, it’s essential to understand the different types available and their specific applications. This knowledge will help you select the tools that best meet your business’s needs and ensure that your investment yields the highest returns.
Classification of Hand Tools
Hand tools can be broadly classified into several categories based on their function:
- Cutting Tools: These include tools like saws, knives, and scissors, which are used to cut materials such as wood, metal, or plastic. Precision and sharpness are critical factors to consider when choosing cutting tools, as they directly impact the quality of the work.
- Fastening Tools: Tools like screwdrivers, wrenches, and pliers fall under this category. They are used to assemble or disassemble components, making them essential for construction, repair, and maintenance tasks.
- Measuring Tools: Measuring accuracy is crucial in any project. Tools like tape measures, calipers, and levels are used to ensure precision in measurements, which is vital for achieving the desired outcomes in construction, carpentry, and other crafts.
- Striking Tools: Hammers and mallets are used for driving nails, shaping metal, or breaking apart materials. The durability and balance of these tools are important factors, as they often endure significant impact.
- Finishing Tools: These include files, rasps, and sandpaper, which are used to smooth or finish surfaces. The quality of finishing tools can greatly affect the final appearance and texture of your projects.
Choosing the Right Tools
When selecting hand tools, it’s important to match them to your specific project requirements. For instance, if your business involves detailed woodworking, you’ll need high-quality chisels and planes to achieve precise finishes. Similarly, for metalworking, robust wrenches and hammers are essential. Consider the following factors when choosing hand tools:
- Material Quality: Tools made from high-grade materials such as stainless steel or chrome vanadium alloy are more durable and provide better performance over time.
- Ergonomics: Ergonomically designed tools reduce fatigue and increase efficiency, especially when used for extended periods. Look for tools with comfortable grips and balanced weight distribution.
- Brand Reputation: Established brands often offer tools that are well-tested and reliable. Researching reviews and recommendations can help you identify trustworthy brands.
- Maintenance Needs: Consider how easy it is to maintain and sharpen your tools. Some tools may require regular maintenance to stay in optimal condition, while others are designed for minimal upkeep.
Selecting the right hand tools is a critical step in ensuring the success of your business projects. By choosing tools that are well-suited to your specific needs, you can enhance productivity, improve work quality, and reduce the risk of errors or injuries.
IV. Key Considerations Before Sourcing Hand Tools
Before you start sourcing hand tools, it’s important to take a step back and evaluate the specific needs of your business. This section covers the key considerations that will guide you in making the best decisions, ensuring that the tools you invest in are both cost-effective and of high quality.
Assessing Your Business Needs
The first step in sourcing hand tools is to assess the specific needs of your business. Consider the following questions:
- What types of projects will the tools be used for? Identifying the scope of your projects will help you determine which tools are essential and which are optional.
- How frequently will the tools be used? If a tool will be used daily, it’s worth investing in higher quality to ensure durability and performance. On the other hand, tools that are used less frequently might not require the same level of investment.
- What are the safety requirements? Some projects may require tools with specific safety features or certifications. Ensuring that your tools meet these requirements is crucial for maintaining a safe working environment.
Quality vs. Cost
One of the most important considerations when sourcing hand tools is the balance between quality and cost. While it might be tempting to opt for cheaper tools to save on initial costs, this can be a false economy in the long run. Low-quality tools are more likely to wear out quickly, leading to frequent replacements and potentially higher overall costs.
Investing in high-quality tools can offer several long-term benefits:
- Durability: High-quality tools are built to last, reducing the need for frequent replacements.
- Performance: Quality tools provide better precision and efficiency, which can enhance the quality of your work and reduce the time spent on each task.
- Safety: Better tools are often designed with safety in mind, reducing the risk of accidents and injuries.
To strike the right balance between quality and cost, consider the total cost of ownership over the tool’s lifespan rather than just the initial purchase price.
Brand Reputation and Reviews
The brand of the tools you choose can be a significant indicator of their quality and reliability. Established brands often have a reputation for producing durable, high-performance tools, backed by warranties and customer support. When selecting a brand, consider the following:
- Product reviews and testimonials: Look for feedback from other businesses or professionals in your industry. Positive reviews can be a good indicator of a tool’s reliability and performance.
- After-sales service: A brand that offers strong after-sales support, including warranties, repairs, and customer service, can be invaluable if you encounter issues with your tools.
- Availability of parts and accessories: Some brands offer a wide range of compatible parts and accessories, making it easier to maintain and upgrade your tools over time.
Certifications and Compliance
Depending on your industry and location, certain tools may need to meet specific safety standards or certifications. For example, tools used in electrical work may need to be insulated to prevent electrical shocks. Similarly, tools used in food processing may need to meet hygiene standards.
Ensuring that the tools you source are compliant with relevant regulations is crucial for maintaining safety and avoiding legal issues. When evaluating tools, check for certifications such as CE marking, ANSI standards, or ISO certifications that indicate compliance with industry standards.
By carefully considering these factors before sourcing hand tools, you can make informed decisions that align with your business needs and ensure that you get the best value for your investment.
V. Safety Measures in Tool Sourcing and Usage
Safety should always be a top priority when sourcing and using hand tools. Proper safety measures not only protect your employees but also ensure the longevity and effectiveness of your tools. In this section, we’ll cover the essential safety measures you should implement in your workshop or business.
Personal Protective Equipment (PPE)
Personal protective equipment (PPE) is the first line of defense against workplace injuries. When working with hand tools, it’s essential that your team is equipped with the appropriate PPE. This includes items like gloves, safety goggles, ear protection, and sturdy footwear.
- Gloves: Protect hands from cuts, abrasions, and chemical exposure. When using cutting tools or handling sharp objects, gloves can prevent serious injuries.
- Safety Goggles: Protect eyes from flying debris, dust, and sparks. They are particularly important when working with tools like saws, grinders, or drills.
- Ear Protection: Tools like power drills and sanders can produce loud noises that can damage hearing over time. Earplugs or earmuffs can help protect against hearing loss.
- Sturdy Footwear: Steel-toed boots can protect feet from heavy objects that might fall, and slip-resistant soles can prevent accidents on slippery surfaces.
It’s important to ensure that all PPE is properly fitted and maintained. Regular training on the correct use of PPE can also help prevent accidents and injuries.
Workshop Safety Guidelines
Maintaining a safe workshop environment is essential for the well-being of your employees and the smooth operation of your business. Here are some key safety guidelines to follow:
- Tool Maintenance: Regularly inspect and maintain your tools to ensure they are in good working condition. Dull blades, loose handles, or faulty mechanisms can lead to accidents.
- Proper Tool Use: Ensure that all employees are trained on the correct use of each tool. Misusing a tool can result in injury or damage to the tool itself.
- Clear Workspaces: Keep work areas clean and free of clutter. A tidy workspace reduces the risk of trips, falls, and other accidents.
- Storage: Store tools properly when not in use. Tools left out can become hazards, and improper storage can lead to damage or wear over time.
Tool Maintenance and Safety
Proper maintenance of your hand tools is crucial for both safety and performance. Regular maintenance can prevent accidents caused by faulty tools and extend the lifespan of your equipment. Here are some maintenance tips to keep your tools in top condition:
- Sharpen Blades: Cutting tools like saws, knives, and chisels should be kept sharp to ensure clean cuts and reduce the risk of injury from using excessive force.
- Lubricate Moving Parts: Tools with moving parts, such as pliers or wrenches, should be regularly lubricated to prevent rust and ensure smooth operation.
- Check for Wear and Tear: Regularly inspect your tools for signs of wear, such as cracks, chips, or loose parts. Replace or repair any damaged tools immediately.
- Store Tools Properly: Store your tools in a dry, organized space to prevent rust and damage. Use toolboxes, racks, or cabinets to keep tools organized and accessible.
By implementing these safety measures, you can create a safer work environment, reduce the risk of accidents, and ensure that your tools remain in good working condition for years to come.
VI. Where to Source Hand Tools
Sourcing hand tools for your business involves more than just finding a supplier. It’s about identifying the best sources that offer quality, reliability, and cost-effectiveness. This section will explore the different avenues for sourcing hand tools, from domestic suppliers to international markets, and provide insights into how to evaluate these options.
Domestic vs. International Suppliers
When sourcing hand tools, one of the first decisions you’ll need to make is whether to source domestically or internationally. Each option has its advantages and disadvantages, depending on your business needs.
- Domestic Suppliers:
- Advantages: Faster shipping times, easier communication, and often better after-sales support. Domestic suppliers are also more likely to be familiar with local regulations and standards, reducing the risk of compliance issues.
- Disadvantages: Higher costs due to local manufacturing expenses and potentially limited variety.
- International Suppliers:
- Advantages: Lower costs, especially when sourcing from countries with lower labor and production costs like China or India. International suppliers often offer a wider range of products, including unique or specialized tools that may not be available domestically.
- Disadvantages: Longer shipping times, potential language barriers, and increased risk of communication issues. There may also be additional costs related to customs, tariffs, and compliance with international standards.
Choosing between domestic and international suppliers depends on your specific needs, including budget, timeline, and the level of support you require.
Online Marketplaces and Platforms
In today’s digital age, online marketplaces have become a popular source for hand tools. Platforms like Alibaba, Amazon Business, and Global Sources offer access to a wide range of suppliers, making it easier to compare products and prices.
- Alibaba: One of the largest online marketplaces for sourcing products from China and other countries. Alibaba allows you to browse a vast array of hand tools, communicate directly with suppliers, and request samples before making bulk purchases.
- Amazon Business: Ideal for smaller businesses that need to purchase tools in smaller quantities. Amazon Business offers a streamlined purchasing process, with reviews and ratings that can help you assess product quality.
- Global Sources: Another major online marketplace that connects buyers with suppliers, primarily in Asia. Global Sources offers a variety of tools and provides resources to help you evaluate suppliers and negotiate terms.
When sourcing tools from online marketplaces, it’s important to thoroughly vet suppliers. Look for reviews, request samples, and verify the supplier’s credentials before making a purchase.
Trade Shows and Direct Supplier Visits
Trade shows and direct supplier visits remain valuable methods for sourcing hand tools, especially when you want to establish strong relationships with suppliers.
- Trade Shows: Attending trade shows gives you the opportunity to see the latest products, meet suppliers in person, and negotiate deals directly. Trade shows like the Canton Fair in China or the National Hardware Show in the USA are excellent venues for discovering new suppliers and trends in the hand tool industry.
- Direct Supplier Visits: Visiting a supplier’s factory allows you to assess their production capabilities, quality control processes, and working conditions. This firsthand experience can provide greater confidence in the supplier’s ability to meet your needs.
Both trade shows and direct visits require more time and resources compared to online sourcing, but they can result in stronger, more reliable partnerships.
Working with Distributors and Agents
In some cases, working with distributors or agents can simplify the sourcing process. Distributors often have established relationships with manufacturers and can offer a range of products from different brands. They may also provide additional services such as warehousing, logistics, and after-sales support.
- Advantages: Convenience, as distributors handle much of the sourcing and logistics work. They also offer the benefit of established relationships with manufacturers, which can lead to better pricing and service.
- Disadvantages: Potentially higher costs, as distributors add their own margin to the prices. There may also be less flexibility in product selection compared to sourcing directly from manufacturers.
Agents can also assist in the sourcing process, especially when dealing with international suppliers. A good agent will have local knowledge and connections, making it easier to navigate the complexities of international trade.
By carefully considering these sourcing options and evaluating the pros and cons of each, you can make informed decisions that align with your business’s needs and goals.
VII. How to Evaluate and Select Suppliers
Selecting the right supplier is a critical step in sourcing hand tools. The quality of your tools, the reliability of your supply chain, and ultimately the success of your business depend on this decision. In this section, we’ll discuss the key factors to consider when evaluating and selecting suppliers.
Supplier Vetting Process
Before committing to a supplier, it’s essential to conduct thorough vetting to ensure they can meet your requirements. Here are some steps to follow:
- Research the Supplier’s Background: Investigate the supplier’s history, reputation, and financial stability. A reputable supplier should have a proven track record of delivering quality products on time.
- Check References: Ask the supplier for references from other clients, preferably within your industry. Contact these references to inquire about their experiences with the supplier, focusing on reliability, product quality, and customer service.
- Factory Audits: If possible, conduct a factory audit to assess the supplier’s production capabilities and quality control processes. An audit can provide insights into the supplier’s ability to meet your specifications and deadlines.
- Sample Orders: Before placing a large order, request samples to evaluate the quality of the tools. This allows you to test the products and ensure they meet your standards.
Sample Orders and Quality Checks
Evaluating samples is a crucial part of the supplier selection process. Here’s how to effectively assess samples:
- Inspect the Materials: Check the materials used in the tools to ensure they are durable and suitable for your applications. For example, tools made from high-quality steel or other robust materials are more likely to withstand heavy use.
- Test the Functionality: Use the tools in real-world conditions to assess their performance. Pay attention to factors like ease of use, precision, and ergonomics.
- Check for Consistency: Ensure that the quality of the samples is consistent with the products you expect to receive in bulk. Consistency is key to maintaining product quality across multiple orders.
- Evaluate the Packaging: Proper packaging is important for protecting tools during transit and storage. Inspect the packaging for durability and adequacy.
Negotiating Terms and Conditions
Once you’ve identified a potential supplier, the next step is to negotiate the terms of your agreement. Key factors to consider include:
- Pricing: Negotiate a fair price that reflects the quality of the tools and the quantity you’re ordering. Be sure to consider all costs, including shipping, taxes, and duties.
- Minimum Order Quantities (MOQs): Suppliers often have MOQs, which can impact your purchasing decisions. Negotiate a MOQ that aligns with your needs and budget.
- Payment Terms: Discuss payment terms with the supplier, including deposit requirements, payment schedules, and any penalties for late payments. Clear terms help prevent misunderstandings and disputes.
- Lead Times: Ensure that the supplier can meet your delivery schedule. Discuss lead times and agree on penalties for delays, if necessary.
- Warranties and Returns: Clarify the supplier’s warranty and return policies. A strong warranty can provide peace of mind and protection against defects.
Building Long-Term Supplier Relationships
Establishing and maintaining strong relationships with your suppliers is crucial for long-term success. Here are some strategies to build lasting partnerships:
- Communication: Maintain open and regular communication with your suppliers. Keep them informed of your needs, expectations, and any changes in your requirements.
- Collaboration: Work closely with your suppliers to address any issues that arise. Collaborative problem-solving can lead to better outcomes and stronger relationships.
- Consistency: Be consistent in your orders and payments. Reliable buyers are more likely to receive favorable treatment from suppliers, including better pricing and priority service.
- Feedback: Provide feedback to your suppliers on the quality of their products and services. Constructive feedback can help suppliers improve and better meet your needs in the future.
By carefully evaluating and selecting suppliers, you can ensure a reliable supply of high-quality hand tools that meet your business’s needs and contribute to your success.
VIII. Organization & Storage of Hand Tools
Proper organization and storage of hand tools are essential for maintaining a productive and efficient workshop. An organized workspace not only improves workflow but also helps prolong the life of your tools. This section will cover best practices for organizing and storing hand tools.
Workshop Layout
A well-designed workshop layout can significantly enhance productivity by ensuring that tools and materials are easily accessible and that workflow is smooth. Here are some tips for optimizing your workshop layout:
- Zoning: Divide your workshop into zones based on the tasks performed in each area. For example, create separate zones for cutting, assembly, and finishing. This reduces the need to move tools and materials between tasks, saving time and effort.
- Tool Placement: Place frequently used tools within easy reach of your workstations. Less frequently used tools can be stored further away. This reduces unnecessary movement and keeps your workspace clutter-free.
- Workbenches: Ensure that your workbenches are sturdy and appropriately sized for the tasks you’ll be performing. Consider installing benches with built-in storage for tools and materials.
- Lighting: Good lighting is essential for precision work and safety. Ensure that your workshop is well-lit, particularly in areas where detailed work is performed.
Storage Solutions
Proper storage solutions help keep your tools organized and protected from damage. Here are some effective storage options:
- Toolboxes: Portable toolboxes are ideal for storing small hand tools. They keep tools organized and protected, and they can be easily transported to different work areas.
- Racks and Pegboards: Wall-mounted racks and pegboards are excellent for organizing tools like wrenches, screwdrivers, and hammers. They keep tools visible and within easy reach, which can improve efficiency.
- Cabinets: Lockable cabinets are ideal for storing more valuable or dangerous tools. They provide security and protect tools from dust and moisture.
- Shelving: Heavy-duty shelving units can be used to store larger tools and materials. Shelving should be sturdy and capable of holding the weight of the items you plan to store.
Maintaining Cleanliness
Maintaining cleanliness in your workshop is not just about aesthetics—it’s also about safety and efficiency. Here’s how to keep your workspace clean and organized:
- Daily Clean-Up: Encourage a routine of cleaning up at the end of each workday. This includes putting away tools, sweeping the floor, and disposing of waste materials.
- Dust Control: Use dust collection systems or shop vacuums to control dust and debris. This is especially important in woodworking shops, where dust can accumulate quickly and pose a fire hazard.
- Tool Maintenance: Regularly clean your tools to remove dust, grease, and other debris. This helps prevent rust and ensures that tools are ready for use when needed.
- Organized Storage: Keep your storage areas organized by grouping similar tools together and labeling drawers and bins. This makes it easier to find tools and reduces the risk of misplacing or losing items.
By implementing these organization and storage practices, you can create a more efficient, safer, and more productive workshop environment.
IX. Logistics and Supply Chain Management
Effective logistics and supply chain management are crucial for ensuring that your hand tools arrive on time, in good condition, and at the best possible cost. This section will cover key aspects of managing logistics and supply chains when sourcing hand tools.
Shipping Options and Costs
Choosing the right shipping method is critical for managing costs and ensuring timely delivery of your hand tools. Here are the main shipping options:
- Air Freight: Air freight is the fastest shipping method but also the most expensive. It’s ideal for high-value or urgent shipments that need to reach their destination quickly.
- Sea Freight: Sea freight is more cost-effective for large shipments, especially when sourcing from overseas suppliers. However, it has longer transit times compared to air freight.
- Land Freight: Land freight (trucks and rail) is commonly used for domestic shipments or for transporting goods over shorter distances. It offers a balance between cost and speed.
When choosing a shipping method, consider factors such as the value of the tools, the size of the shipment, and your delivery timeline. Also, be aware of any additional costs, such as customs duties, taxes, and insurance, that may apply to your shipment.
Customs and Import Regulations
When sourcing hand tools from international suppliers, it’s important to understand and comply with customs and import regulations. Here are some key considerations:
- Import Duties and Taxes: Be aware of the duties and taxes that apply to your shipments. These costs can vary depending on the country of origin, the type of tools, and the value of the shipment.
- Documentation: Ensure that all necessary documentation, such as invoices, packing lists, and certificates of origin, is in order. Accurate documentation is essential for smooth customs clearance.
- Compliance with Standards: Some tools may need to meet specific safety or quality standards to be imported. Ensure that your tools comply with the relevant regulations in your country.
Working with a customs broker can help simplify the process and ensure that your shipments comply with all necessary regulations.
Warehousing and Inventory Management
Proper warehousing and inventory management are essential for ensuring that your tools are readily available when needed. Here are some best practices:
- Storage Conditions: Ensure that your warehouse provides appropriate storage conditions for your tools. This includes controlling temperature and humidity to prevent rust and other damage.
- Inventory Tracking: Implement an inventory management system to track your tools and materials. This helps you monitor stock levels, manage reordering, and reduce the risk of stockouts.
- Order Fulfillment: Streamline your order fulfillment process to ensure that tools are picked, packed, and shipped efficiently. This can help reduce lead times and improve customer satisfaction.
- Regular Audits: Conduct regular inventory audits to ensure that your records match the physical stock. This helps identify discrepancies and prevent theft or loss.
By managing logistics and supply chains effectively, you can ensure that your tools are delivered on time, in good condition, and at a competitive cost.
X. Risk Management in Hand Tool Sourcing
Sourcing hand tools involves several risks, from quality control issues to supply chain disruptions. Effective risk management strategies can help mitigate these risks and ensure a smooth sourcing process. This section will discuss common risks and strategies for managing them.
Common Risks in Hand Tool Sourcing
Here are some of the most common risks associated with sourcing hand tools:
- Quality Control Issues: Tools that don’t meet quality standards can lead to project delays, increased costs, and safety hazards. Ensuring consistent quality is a major challenge, especially when sourcing from multiple suppliers.
- Shipping Delays: Delays in shipping can disrupt your supply chain and lead to missed deadlines. This is particularly concerning when sourcing tools from overseas suppliers.
- Supplier Reliability: A supplier that fails to meet delivery schedules or produces substandard products can severely impact your operations. Reliability is a key factor in supplier selection.
- Regulatory Compliance: Non-compliance with local regulations or standards can result in legal issues, fines, and even product recalls.
Strategies to Mitigate Risks
To mitigate these risks, consider the following strategies:
- Quality Control Measures: Implement strict quality control measures, including factory audits, sample testing, and third-party inspections. This ensures that the tools you receive meet your specifications and quality standards.
- Backup Suppliers: Establish relationships with multiple suppliers to reduce dependency on a single source. This provides a backup in case your primary supplier faces issues.
- Clear Contracts: Use detailed contracts that outline the terms of the agreement, including product specifications, delivery schedules, payment terms, and penalties for non-compliance. Clear contracts help protect your interests and provide a legal recourse in case of disputes.
- Regular Communication: Maintain regular communication with your suppliers to stay informed about any potential issues that could impact your orders. Proactive communication can help prevent delays and ensure timely delivery.
Contingency Planning
Having a contingency plan in place is essential for dealing with unexpected disruptions in your supply chain. Here are some elements to include in your contingency plan:
- Emergency Stock: Maintain a buffer stock of essential tools to cover unexpected delays or shortages. This ensures that your operations can continue without interruption.
- Alternative Shipping Methods: Identify alternative shipping methods or routes that can be used in case of disruptions. This helps ensure that your tools arrive on time, even if your usual shipping method is unavailable.
- Crisis Management Team: Establish a crisis management team responsible for handling supply chain disruptions. This team should be trained to respond quickly and effectively to minimize the impact on your business.
By implementing these risk management strategies, you can reduce the likelihood of disruptions and ensure a more reliable supply of hand tools for your business.
XI. Cost Management and Optimization
Managing costs effectively is crucial for maximizing the return on your investment in hand tools. This section will cover strategies for cost management and optimization, helping you get the best value for your money.
Cost Breakdown of Sourcing Hand Tools
Understanding the costs involved in sourcing hand tools is the first step in managing them effectively. Here’s a breakdown of the key cost components:
- Direct Costs: These include the purchase price of the tools, shipping costs, and any applicable duties and taxes. Direct costs are the most visible and easiest to track.
- Indirect Costs: Indirect costs include quality control expenses, warehousing costs, and inventory management. These costs can add up over time and should be factored into your total cost of ownership.
- Hidden Costs: Hidden costs can include things like delays in delivery, returns due to quality issues, and the cost of replacing defective tools. These costs are often overlooked but can significantly impact your bottom line.
By understanding all the costs involved, you can make more informed decisions and identify areas where savings can be made.
Strategies to Reduce Sourcing Costs
Here are some strategies for reducing your sourcing costs:
- Bulk Purchasing: Buying in bulk can lead to significant discounts from suppliers. However, it’s important to balance the cost savings with the potential risks of overstocking, such as increased storage costs or obsolescence.
- Negotiation: Don’t be afraid to negotiate with suppliers to secure better pricing, especially if you’re placing large or repeat orders. Negotiating payment terms, such as extended payment periods, can also help improve your cash flow.
- Alternative Sourcing Locations: Consider sourcing tools from different regions or countries where production costs are lower. For example, sourcing from emerging markets like Vietnam or India may offer cost advantages compared to traditional suppliers in China or Europe.
- Value Engineering: Work with your suppliers to identify cost-saving opportunities through value engineering. This could involve redesigning tools to use less expensive materials without compromising quality or performance.
Maximizing ROI
Maximizing the return on your investment (ROI) in hand tools involves more than just managing costs—it’s about ensuring that your tools contribute to the overall success of your business. Here’s how to maximize ROI:
- Invest in Quality: While it’s important to manage costs, don’t compromise on quality. High-quality tools may have a higher upfront cost, but they typically last longer and perform better, leading to lower overall costs and higher productivity.
- Monitor Tool Performance: Regularly assess the performance of your tools to ensure they are meeting your expectations. Tools that consistently underperform should be replaced, even if they are still relatively new.
- Optimize Usage: Ensure that your tools are being used efficiently and for the right tasks. Training your team on proper tool usage can help extend the life of your tools and reduce the need for replacements.
- Regular Maintenance: Regular maintenance not only improves safety but also extends the life of your tools, providing better value over time.
By focusing on both cost management and maximizing ROI, you can ensure that your investment in hand tools supports the growth and success of your business.
XII. Sourcing Hand Tools for Different Business Sizes
The size of your business plays a significant role in how you approach sourcing hand tools. Whether you’re a small business or a large enterprise, your sourcing strategy needs to align with your operational needs and budget. This section will explore sourcing strategies for businesses of different sizes.
Small Businesses
For small businesses, sourcing hand tools often involves working within a limited budget while still ensuring that you have the tools needed to get the job done. Here are some tips for small businesses:
- Prioritize Essential Tools: Focus on sourcing the most essential tools first. Identify the tools that are critical to your operations and prioritize their purchase.
- Consider Quality Over Quantity: It’s better to invest in a few high-quality tools than to buy a large number of lower-quality ones. Quality tools will last longer and perform better, providing better value over time.
- Explore Group Buying: Small businesses can benefit from joining buying groups or cooperatives, which allow multiple businesses to pool their purchasing power to secure better prices from suppliers.
- Leverage Local Suppliers: Working with local suppliers can reduce shipping costs and lead times. Local suppliers may also offer more personalized service and support.
- Scale Up Gradually: As your business grows, gradually expand your tool inventory. This allows you to spread out your costs and avoid overextending your budget.
Medium and Large Enterprises
Larger businesses often have more complex sourcing needs due to higher volumes, greater diversity of tools, and the need for consistency across multiple locations. Here’s how medium and large enterprises can approach tool sourcing:
- Supplier Diversification: Large businesses should diversify their supplier base to reduce risk and ensure a reliable supply of tools. Working with multiple suppliers also allows for competitive pricing and access to a broader range of products.
- Centralized Procurement: For businesses with multiple locations, centralized procurement can help standardize tools and achieve economies of scale. Centralized purchasing ensures consistency in quality and pricing across the organization.
- Bulk Purchasing: Larger businesses can take advantage of bulk purchasing to secure significant discounts. However, it’s important to manage inventory levels carefully to avoid overstocking.
- Customized Tools: For specialized tasks, large enterprises may benefit from sourcing customized tools. Working directly with manufacturers to design tools that meet specific requirements can improve efficiency and performance.
- Technology Integration: Implementing procurement software can streamline the sourcing process, improve visibility into supply chains, and enhance decision-making. Software solutions can also help with tracking tool usage, maintenance, and inventory.
By tailoring your sourcing strategy to the size of your business, you can ensure that you have the right tools in place to support your operations while managing costs effectively.
XIII. Future Trends in Hand Tool Sourcing
The hand tool industry is constantly evolving, driven by technological advancements, changing consumer demands, and global market shifts. Staying ahead of these trends is essential for businesses looking to maintain a competitive edge. This section will explore some of the key trends shaping the future of hand tool sourcing.
Technological Advances in Tool Manufacturing
Technology is playing an increasingly important role in the manufacturing of hand tools. Here are some of the key technological advancements impacting the industry:
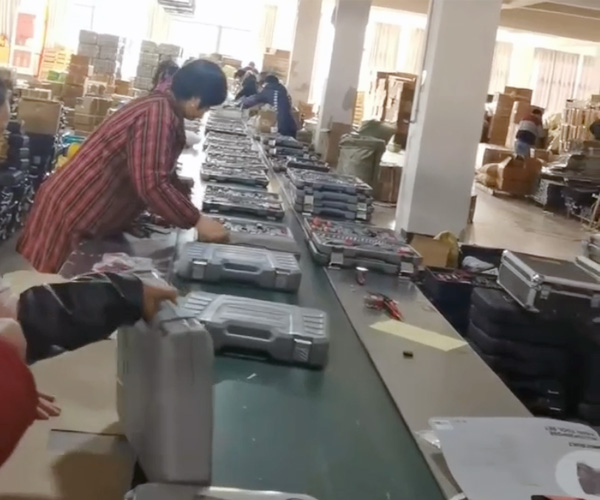
- Automation and Robotics: The use of automation and robotics in manufacturing is improving the precision and efficiency of tool production. Automated systems can produce tools with tighter tolerances and more consistent quality, reducing the need for manual labor and minimizing errors.
- Smart Tools: The rise of smart tools—hand tools embedded with sensors and connected to the Internet of Things (IoT)—is transforming how tools are used and maintained. Smart tools can monitor their own usage, track wear and tear, and provide real-time data to users, helping to optimize tool usage and maintenance.
- 3D Printing: 3D printing technology is being used to produce custom tools and prototypes more quickly and cost-effectively than traditional manufacturing methods. This technology allows for greater flexibility in tool design and faster production times.
Sustainability and Eco-Friendly Tools
As environmental concerns continue to grow, there is increasing demand for sustainable and eco-friendly hand tools. Here’s how the industry is responding:
- Sustainable Materials: Manufacturers are exploring the use of sustainable materials, such as recycled metals and biodegradable plastics, in the production of hand tools. These materials help reduce the environmental impact of tool production and disposal.
- Energy-Efficient Manufacturing: Companies are adopting energy-efficient manufacturing processes to reduce their carbon footprint. This includes using renewable energy sources, minimizing waste, and optimizing resource usage.
- Eco-Friendly Packaging: In addition to sustainable tools, there is also a focus on eco-friendly packaging. Manufacturers are reducing the use of plastic packaging and opting for recyclable or compostable materials.
Businesses that prioritize sustainability in their sourcing decisions can benefit from meeting consumer demand for eco-friendly products while also contributing to environmental conservation.
Market Shifts and Emerging Sourcing Regions
The global landscape of hand tool sourcing is changing, with new regions emerging as key players in the market. Here are some of the trends to watch:
- Shift from China: While China remains a dominant player in the hand tool market, rising labor costs and trade tensions are prompting some companies to explore alternative sourcing locations. Countries like Vietnam, India, and Mexico are becoming increasingly attractive due to their lower production costs and improving manufacturing capabilities.
- Regional Manufacturing Hubs: There is a growing trend towards regional manufacturing hubs that serve specific markets. For example, Eastern Europe is becoming a key hub for tool production serving the European market, while Southeast Asia is emerging as a hub for the Asia-Pacific region.
- Reshoring: Some companies are bringing manufacturing back to their home countries (reshoring) to reduce dependency on foreign suppliers and mitigate risks associated with global supply chains. This trend is particularly strong in the United States and Europe.
By staying informed about these trends and adapting your sourcing strategy accordingly, you can position your business for success in a rapidly changing market.
XIV. Conclusion
Sourcing and selecting the right hand tools for your business is a multifaceted process that requires careful consideration of various factors, from understanding the types of tools available to evaluating suppliers and managing costs. By following the strategies and best practices outlined in this guide, you can ensure that you make informed decisions that support your business’s growth and success.
Recap of Key Takeaways
- Understand Your Needs: Assess your business’s specific needs to determine which tools are essential and what quality level is required.
- Evaluate Suppliers Carefully: Conduct thorough vetting of suppliers to ensure reliability, quality, and compliance with relevant standards.
- Prioritize Safety: Implement safety measures, including the use of PPE and regular tool maintenance, to protect your employees and prolong the life of your tools.
- Manage Costs Wisely: Balance quality with cost-effectiveness, and explore strategies like bulk purchasing and value engineering to reduce expenses.
- Stay Informed: Keep up with industry trends, such as technological advancements and sustainability, to maintain a competitive edge.
Final Tips for Successful Sourcing
- Communicate Regularly with Suppliers: Maintaining strong communication with your suppliers can prevent misunderstandings and ensure that your orders are fulfilled to your satisfaction.
- Be Proactive with Risk Management: Anticipate potential risks and have contingency plans in place to address supply chain disruptions and other challenges.
- Continually Assess Your Tool Inventory: Regularly review your tool inventory to identify any gaps, overstocked items, or tools that need replacement.
Encouragement to Stay Informed
The world of hand tool sourcing is dynamic, with new developments and trends constantly emerging. By staying informed and adapting to changes in the market, you can ensure that your business remains competitive and well-equipped to meet the demands of your industry.