Introduction
Understanding the nature and function of a manufacturing facility is crucial for businesses, especially those involved in the production and distribution of goods like hand tools. For companies looking to source products or establish production lines, knowing what constitutes a manufacturing facility and how it operates can be the difference between success and failure. In the global supply chain, particularly in the hand tool industry, the role of a factory is not merely a place where goods are assembled; it is a complex ecosystem that drives the production, quality control, and distribution of tools that professionals and DIY enthusiasts rely on.
In this article, we will delve into the intricacies of manufacturing facilities, with a particular focus on factories in China, a leading manufacturer of hand tools globally. We will explore what a manufacturing facility is, the various types of facilities involved in hand tool production, and why these facilities are critical to ensuring the quality and availability of the tools we use daily. Whether you are a business owner, a procurement officer, or simply curious about how your tools are made, this comprehensive guide will provide valuable insights into the world of hand tool manufacturing.
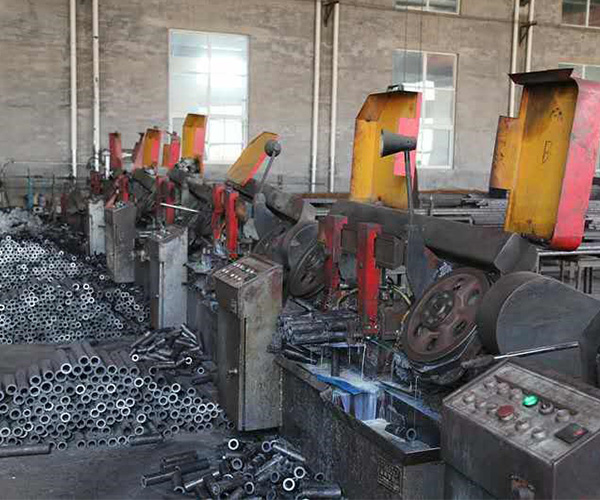
What Is a Manufacturing Facility?
A manufacturing facility is a specialized location where goods are produced on a large scale using machinery, labor, and raw materials. These facilities are designed to optimize the production process, allowing for the efficient creation of products that meet specific standards and requirements. In the context of hand tool production, a manufacturing facility is where raw materials such as steel, plastic, and rubber are transformed into the finished products that end up on store shelves and in toolboxes around the world.
Manufacturing facilities vary greatly in size and complexity, depending on the products being made and the scale of production. They may include a variety of departments and areas, each dedicated to a specific aspect of the production process. For example, a typical hand tool manufacturing facility might include production lines where tools are assembled, machining centers where raw materials are shaped and refined, quality control departments where products are tested for defects, and warehouses where finished goods are stored before being shipped to distributors or retailers.
The importance of a well-structured manufacturing facility cannot be overstated. It not only ensures that products are made efficiently and to the required specifications, but it also plays a key role in maintaining the safety of workers and the protection of the environment. In many countries, including China, manufacturers must adhere to strict safety and environmental regulations to prevent accidents and minimize their impact on the environment.
Key Characteristics of Manufacturing Facilities
Several key characteristics define a manufacturing facility, making it suitable for large-scale production:
- Production Capacity: This refers to the facility’s ability to produce a specific quantity of products within a given timeframe. For hand tools, production capacity can range from small batches of specialized tools to millions of units of mass-produced items.
- Machinery and Technology: Manufacturing facilities are equipped with various machines and technologies that enable the efficient transformation of raw materials into finished products. This includes everything from CNC machines for precise cutting and shaping to automated assembly lines that streamline the production process.
- Workforce: A skilled workforce is essential for the successful operation of a manufacturing facility. Workers are responsible for operating machinery, assembling products, performing quality checks, and managing the overall production process. In countries like China, the availability of a large, skilled labor force is one of the factors that make it a global leader in manufacturing.
- Quality Control: Ensuring that products meet specific standards is a critical aspect of manufacturing. Quality control departments within a facility are tasked with inspecting products at various stages of production to identify and address any defects or inconsistencies.
- Logistics and Supply Chain Management: A well-organized supply chain is vital for the smooth operation of a manufacturing facility. This includes the procurement of raw materials, the management of inventory, and the distribution of finished products to customers or retailers.
Manufacturing facilities are not just places where products are made; they are dynamic environments that require careful management and coordination to ensure that production runs smoothly and efficiently.
The Role of a Factory in Hand Tool Production
Hand tools are essential in various industries, from construction and automotive repair to home improvement and DIY projects. The production of these tools involves a complex process that requires precision, quality control, and efficiency. A factory dedicated to hand tool production is specifically designed to meet these demands, ensuring that the tools produced are reliable, durable, and of the highest quality.
What Are Hand Tools?
Hand tools are tools that are powered by manual effort rather than electricity or other sources of power. Examples include hammers, screwdrivers, wrenches, pliers, and saws. These tools are used in a wide range of applications, from basic household repairs to complex industrial tasks. The demand for high-quality hand tools is consistent across various markets, making the role of the manufacturing facility that produces them incredibly important.
Overview of Hand Tool Production
The production of hand tools typically involves several stages, each of which requires specialized equipment and expertise:
- Design and Prototyping: The process begins with the design of the tool, where engineers and designers work together to create a prototype that meets specific requirements. This stage involves detailed planning and testing to ensure that the tool will perform as expected.
- Raw Material Procurement: Once the design is finalized, the necessary raw materials are sourced. For hand tools, this usually includes high-quality steel, plastic, and rubber, which are selected based on their durability and suitability for the intended application.
- Machining and Fabrication: The raw materials are then processed using various machining techniques, such as cutting, milling, and forging. This stage is critical for shaping the tool components to the required specifications.
- Assembly: After the components are machined, they are assembled into the final product. This process may involve welding, riveting, or using adhesives to join different parts together.
- Heat Treatment and Finishing: Many hand tools undergo heat treatment to enhance their strength and durability. This is followed by finishing processes such as polishing, coating, or painting to improve the tool’s appearance and protect it from corrosion.
- Quality Control and Testing: Before the tools are packaged and shipped, they undergo rigorous quality checks to ensure they meet the required standards. This includes testing for strength, durability, and functionality.
- Packaging and Distribution: Finally, the finished tools are packaged and stored in warehouses before being distributed to retailers or directly to customers.
Why a Dedicated Facility Is Necessary
The production of hand tools requires precision and attention to detail at every stage of the process. A dedicated manufacturing facility is essential for ensuring that each tool meets the necessary quality standards. Such facilities are equipped with specialized machinery and staffed by skilled workers who are trained to handle the specific demands of hand tool production.
Moreover, a dedicated facility allows for better control over the entire production process, from the procurement of raw materials to the final quality checks. This ensures that any issues or defects can be identified and addressed quickly, minimizing the risk of faulty products reaching the market.
In addition, having a dedicated facility for hand tool production allows manufacturers to optimize their processes for efficiency and cost-effectiveness. This is particularly important in a competitive market where maintaining low production costs without compromising on quality can be a significant advantage.
Types of Facilities Involved in Hand Tool Manufacturing
The production of hand tools involves several different types of facilities, each playing a crucial role in the overall manufacturing process. Understanding the functions of these facilities can provide valuable insight into how hand tools are made and why the choice of facility type is so important.
1. Fabrication Shops
Definition and Characteristics: A fabrication shop is a facility where raw materials are cut, shaped, and assembled into components or finished products. In the context of hand tool manufacturing, fabrication shops are responsible for creating the individual parts that make up the tools, such as handles, blades, and screws.
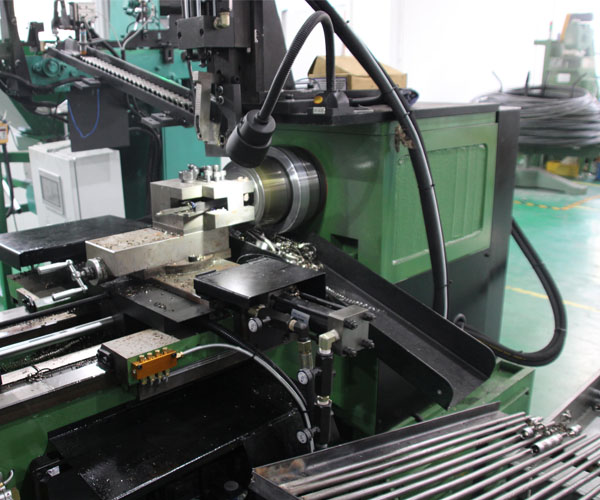
Role in Hand Tool Production: Fabrication shops are critical in the early stages of hand tool production. They use various processes, including cutting, welding, and machining, to transform raw materials into the specific shapes and sizes required for each tool. The precision and quality of the work done in fabrication shops have a direct impact on the overall quality of the finished product.
2. Machining Centers
Definition and Characteristics: Machining centers are specialized facilities equipped with advanced machinery used to precisely shape and finish metal components. These centers often utilize computer numerical control (CNC) machines, which allow for high levels of precision and repeatability.
Processes Used: Machining centers employ various techniques such as milling, turning, and drilling to create the intricate shapes and fine details required for hand tools. The use of CNC technology ensures that each component is produced to exact specifications, which is essential for ensuring the functionality and durability of the tools.
Importance in Tool Manufacturing: The work done in machining centers is vital for producing high-quality hand tools. By ensuring that each component is machined to the correct dimensions and tolerances, machining centers help to guarantee that the final product will perform as intended and have a long service life.
3. Assembly Plants
Definition and Characteristics: An assembly plant is a facility where the individual components of a product are brought together and assembled into the final product. In hand tool manufacturing, assembly plants are where the different parts of a tool are joined to create the finished product.
Role in Tool Production: Assembly plants play a crucial role in the hand tool manufacturing process. This is where the various components created in fabrication shops and machining centers are brought together to form the final tool. The assembly process may involve welding, riveting, or using fasteners to join the parts together, followed by any necessary finishing steps such as polishing or coating.
Examples in Hand Tool Industry: In the hand tool industry, assembly plants are responsible for producing a wide range of tools, from simple hammers and screwdrivers to more complex items like multi-tools and specialized pliers. The efficiency and precision of the assembly process directly impact the quality and consistency of the final products.
4. Quality Control Facilities
Definition and Characteristics: Quality control facilities are specialized areas within a manufacturing facility where products are inspected and tested to ensure they meet the required standards. These facilities are equipped with the tools and equipment needed to perform various tests on the products, such as strength testing, dimensional checks, and durability assessments.
Importance in Hand Tool Manufacturing: Quality control is a critical aspect of hand tool manufacturing. The tools produced must meet strict standards for strength, durability, and performance to ensure they are safe and effective for use. Quality control facilities play a key role in identifying any defects or issues with the tools before they are shipped to customers, helping to maintain the manufacturer’s reputation for quality and reliability.
5. Packaging and Distribution Centers
Definition and Characteristics: Packaging and distribution centers are the final stage in the manufacturing process, where finished products are packaged for shipping and stored before being distributed to retailers or customers. These facilities are designed to ensure that products are properly protected during transit and that they reach their destination in perfect condition.
Impact on Hand Tool Industry: Efficient packaging and distribution are crucial for ensuring that hand tools are available to customers when and where they need them. These centers play a vital role in the global supply chain, ensuring that products are delivered on time and in good condition. Proper packaging also helps to protect the tools from damage during shipping, which is essential for maintaining customer satisfaction.
Case Study: A Typical Hand Tool Manufacturing Facility
To better understand the role of manufacturing facilities in hand tool production, let’s explore a case study of a typical hand tool manufacturing facility in China. This facility represents a standard model for hand tool production, showcasing the various processes and challenges involved in creating high-quality tools.
Facility Layout and Design
The layout of a hand tool manufacturing facility is carefully planned to optimize the flow of materials and the efficiency of the production process. The facility is typically divided into several key areas, each dedicated to a specific stage of production. These areas include raw material storage, fabrication shops, machining centers, assembly lines, quality control stations, and packaging and distribution centers.
The design of the facility is also influenced by the types of tools being produced. For example, a facility that specializes in producing large, heavy tools such as hammers and wrenches may have different layout requirements than a facility focused on smaller, precision tools like screwdrivers and pliers. The overall goal is to create a workspace that allows for the efficient movement of materials and products through each stage of production while minimizing waste and reducing production costs.
Production Processes
The production process in a typical hand tool manufacturing facility involves several stages, each requiring specialized equipment and skilled labor. The process begins with the procurement of raw materials, which are then processed in the facility’s fabrication shops and machining centers. Once the components are machined to the required specifications, they are assembled into the final product on the assembly line.
Throughout the production process, quality control checks are conducted at various stages to ensure that the tools meet the necessary standards. Any defects or issues identified during these checks are addressed immediately to prevent faulty products from reaching the market.
Workforce and Technology
A skilled workforce is essential for the successful operation of a hand tool manufacturing facility. Workers in these facilities are trained to operate specialized machinery, perform precision machining tasks, and assemble products with a high degree of accuracy. In addition to manual labor, many facilities also employ advanced technologies such as CNC machines and automated assembly lines to enhance production efficiency and ensure consistent quality.
The combination of skilled labor and advanced technology allows the facility to produce high-quality hand tools that meet the demands of customers around the world. This is particularly important in markets where quality and reliability are critical factors in purchasing decisions.
Challenges Faced
Operating a hand tool manufacturing facility comes with several challenges, including maintaining precision and consistency in production, adhering to strict safety and environmental regulations, and managing production costs. In addition, manufacturers must also contend with fluctuations in demand, changes in raw material prices, and competition from other producers.
To address these challenges, many facilities invest in continuous improvement initiatives, such as adopting lean manufacturing practices, implementing advanced quality control systems, and exploring new technologies that can enhance production efficiency and reduce costs. By staying ahead of these challenges, manufacturers can maintain their competitive edge and continue to deliver high-quality products to their customers.
Key Components of a Successful Hand Tool Manufacturing Facility
To ensure the successful production of hand tools, a manufacturing facility must have several key components in place. These components work together to create an environment that supports efficient production, maintains high standards of quality, and meets the demands of customers.
1. Technology and Automation
Technology and automation play a critical role in modern manufacturing facilities. The use of advanced machinery, such as CNC machines and automated assembly lines, allows manufacturers to produce hand tools with a high degree of precision and consistency. Automation also helps to reduce production costs by minimizing the need for manual labor and increasing production efficiency.
In addition to traditional manufacturing technologies, many facilities are also adopting new technologies such as 3D printing and robotics. These technologies offer the potential to further enhance production capabilities, allowing manufacturers to create more complex and customized products with greater speed and accuracy.
2. Skilled Workforce
While technology and automation are important, a skilled workforce is equally essential for the successful operation of a manufacturing facility. Workers in these facilities must be trained to operate complex machinery, perform precision tasks, and ensure that products meet the required standards. Ongoing training and development programs are critical for maintaining a skilled workforce and ensuring that employees are equipped with the knowledge and skills needed to keep up with the latest manufacturing techniques and technologies.
3. Supply Chain Management
Effective supply chain management is crucial for ensuring that a manufacturing facility operates smoothly and efficiently. This involves the timely procurement of raw materials, the management of inventory, and the coordination of logistics to ensure that finished products are delivered to customers on time. In the hand tool industry, where quality and reliability are critical, having a well-organized supply chain is essential for maintaining customer satisfaction and competitiveness in the market.
4. Quality Assurance and Compliance
Quality assurance is a critical component of any manufacturing facility. To produce hand tools that meet the required standards, manufacturers must have rigorous quality control systems in place. This includes regular inspections and testing at various stages of production, as well as compliance with industry standards and certifications, such as ISO and CE. By ensuring that products meet these standards, manufacturers can build trust with their customers and maintain a reputation for quality and reliability.
5. Sustainability Practices
Sustainability is becoming increasingly important in the manufacturing industry, and hand tool manufacturers are no exception. To minimize their environmental impact, many facilities are adopting sustainable practices such as reducing waste, recycling materials, and using energy-efficient technologies. These practices not only help to protect the environment but can also lead to cost savings and improved efficiency.
In addition to environmental sustainability, social responsibility is also an important consideration. This includes ensuring that workers are treated fairly, providing safe working conditions, and engaging in ethical business practices. By prioritizing sustainability, manufacturers can create a positive impact on their communities and build a reputation as responsible corporate citizens.
The Importance of Facility Type in Business Decisions
Choosing the right type of manufacturing facility is a critical decision for businesses involved in hand tool production. The type of facility chosen can have a significant impact on production costs, efficiency, and the quality of the final product.
Choosing the Right Facility for Production
When selecting a manufacturing facility, businesses must consider several factors, including the type of products being produced, the scale of production, and the specific requirements of the manufacturing process. For example, a facility that specializes in mass production may be ideal for producing large quantities of simple hand tools, while a facility with advanced machining capabilities may be better suited for producing high-precision tools.
In addition to the type of facility, businesses must also consider the location of the facility. Factors such as proximity to raw material suppliers, access to skilled labor, and transportation infrastructure can all impact the efficiency and cost-effectiveness of the production process.
Impact on Cost and Efficiency
The choice of manufacturing facility can have a significant impact on production costs and efficiency. Facilities that are equipped with advanced technologies and automation can often produce products more efficiently, reducing the overall cost of production. Additionally, facilities that are well-organized and optimized for the specific requirements of the production process can help to minimize waste and reduce the time required to produce each product.
However, it is important to note that the initial investment in advanced technologies and automation can be substantial. Businesses must weigh the potential cost savings and efficiency gains against the upfront costs when deciding whether to invest in these technologies.
Scalability and Flexibility
In today’s rapidly changing market, scalability and flexibility are essential for businesses involved in hand tool production. A facility that can quickly adapt to changes in demand or production requirements is more likely to succeed in the long term. This includes the ability to scale up production in response to increased demand, as well as the flexibility to produce a wide range of products.
By choosing a facility that offers scalability and flexibility, businesses can better respond to market trends and customer needs, ensuring that they remain competitive in the global market.
Future Trends in Manufacturing Facilities
The manufacturing industry is constantly evolving, and hand tool manufacturers must stay ahead of the latest trends to remain competitive. Several key trends are likely to shape the future of manufacturing facilities, including technological advancements, the shift toward smart manufacturing, and the increasing importance of sustainability.
Technological Advancements
Technological advancements are driving significant changes in the manufacturing industry. The adoption of advanced technologies such as 3D printing, robotics, and artificial intelligence is transforming the way products are designed and produced. These technologies offer the potential to improve production efficiency, reduce costs, and create more complex and customized products.
In addition, the use of data analytics and machine learning is enabling manufacturers to optimize their production processes and make more informed decisions. By harnessing the power of data, manufacturers can identify inefficiencies, predict maintenance needs, and improve overall production quality.
Shift Toward Smart Manufacturing
The shift toward smart manufacturing, also known as Industry 4.0, is revolutionizing the manufacturing industry. Smart manufacturing involves the integration of advanced technologies such as the Internet of Things (IoT), artificial intelligence, and machine learning into the production process. This allows for greater automation, real-time monitoring, and more efficient use of resources.
Smart manufacturing also enables manufacturers to create more flexible and responsive production systems that can quickly adapt to changes in demand or production requirements. By embracing smart manufacturing, hand tool manufacturers can improve their competitiveness and better meet the needs of their customers.
Sustainability and Eco-Friendly Practices
As environmental concerns continue to grow, sustainability is becoming increasingly important in the manufacturing industry. Manufacturers are under pressure to reduce their environmental impact and adopt more sustainable practices. This includes reducing waste, recycling materials, using energy-efficient technologies, and minimizing emissions.
In addition to environmental sustainability, social responsibility is also becoming a key consideration for manufacturers. This includes ensuring fair labor practices, providing safe working conditions, and engaging in ethical business practices.
By prioritizing sustainability, hand tool manufacturers can create a positive impact on the environment and their communities, while also building a reputation as responsible corporate citizens.
Conclusion
The production of hand tools is a complex and demanding process that requires precision, quality control, and efficiency. A dedicated manufacturing facility is essential for ensuring that hand tools are produced to the highest standards and meet the needs of customers around the world. From fabrication shops and machining centers to assembly plants and quality control facilities, each type of facility plays a crucial role in the production process.
By understanding the key components of a successful manufacturing facility and staying ahead of the latest trends in the industry, businesses can improve their competitiveness and better meet the needs of their customers. Whether you are a business owner, a procurement officer, or simply curious about how your tools are made, this comprehensive guide provides valuable insights into the world of hand tool manufacturing.
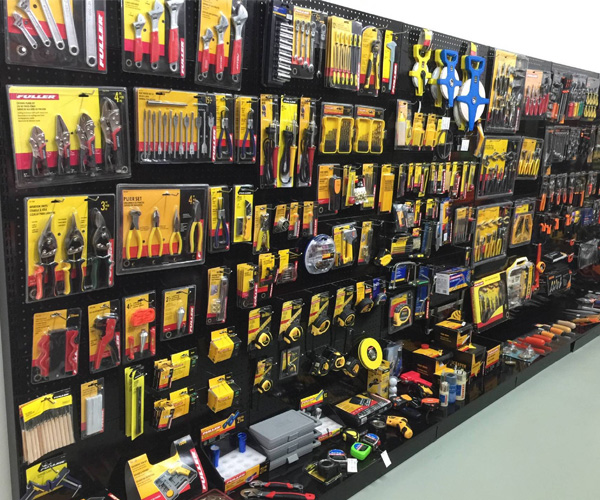
FAQs
What is a manufacturing facility? A manufacturing facility is a specialized location where goods are produced on a large scale using machinery, labor, and raw materials.
Why is a specific facility necessary for hand tool production? A dedicated facility is necessary to ensure that hand tools are produced with the precision, quality, and efficiency required to meet industry standards and customer expectations.
How do different types of facilities impact the quality of hand tools? Each type of facility plays a specific role in the production process, from fabrication to quality control, ensuring that the final product meets the required standards.
What are the key components of a successful manufacturing facility? Key components include advanced technology and automation, a skilled workforce, effective supply chain management, rigorous quality assurance, and a commitment to sustainability.
What future trends will affect hand tool manufacturing? Technological advancements, the shift toward smart manufacturing, and the increasing importance of sustainability are likely to shape the future of the industry.