I. Introduction
When embarking on any DIY project or professional repair task, having the right tools is essential. Among these tools, a reliable socket set stands out as a fundamental asset. However, when you delve into the world of sockets, you’ll quickly discover that there are different types to choose from, namely regular sockets and impact sockets. But which type is better for your needs? This article aims to dissect the differences between impact sockets and regular sockets, helping you make an informed decision that aligns with your specific requirements.
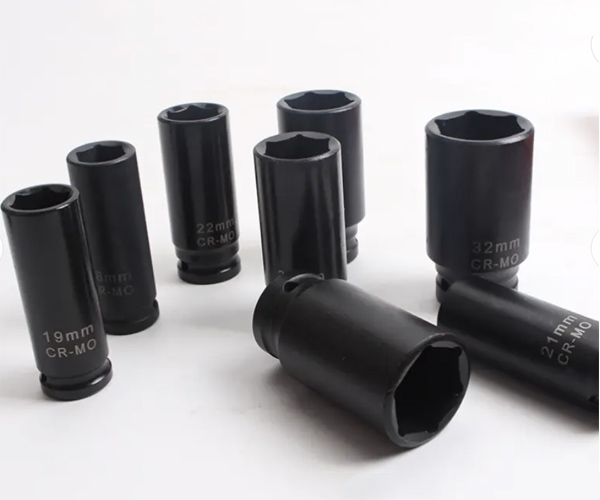
Sockets are indispensable in various applications, from automotive repairs to household maintenance. Understanding the nuances between impact sockets and regular sockets can significantly impact your efficiency and safety during tasks. By the end of this comprehensive guide, you’ll have a clear understanding of the strengths and limitations of each type, enabling you to choose the best socket set for your toolkit.
II. Understanding Sockets
Sockets are versatile tools designed to fit over the heads of fasteners such as nuts and bolts, allowing you to apply torque and either tighten or loosen them. They come in various sizes and shapes, accommodating different fastener types and sizes. Sockets are typically used in conjunction with a ratchet, which provides the leverage needed to turn the socket.
What Are Sockets?
At its core, a socket is a cylindrical tool with a square or hexagonal opening on one end, designed to fit over a corresponding fastener. The other end of the socket usually connects to a ratchet or wrench. Sockets are vital in both DIY and professional settings because they allow for efficient, controlled application of torque to fasteners, minimizing the risk of damage and enhancing the precision of the work.
Types of Sockets
There are two primary types of sockets: regular sockets and impact sockets. While they may appear similar at first glance, their design, construction, and intended uses differ significantly.
- Regular Sockets: These are the most common type of sockets, typically made from chrome vanadium steel. They are designed for general-purpose use and are widely available in various sizes and sets.
- Impact Sockets: These sockets are built to withstand higher levels of torque and are usually made from chrome molybdenum steel. They are specifically designed for use with impact tools, such as impact wrenches, which deliver sudden, high-torque impacts.
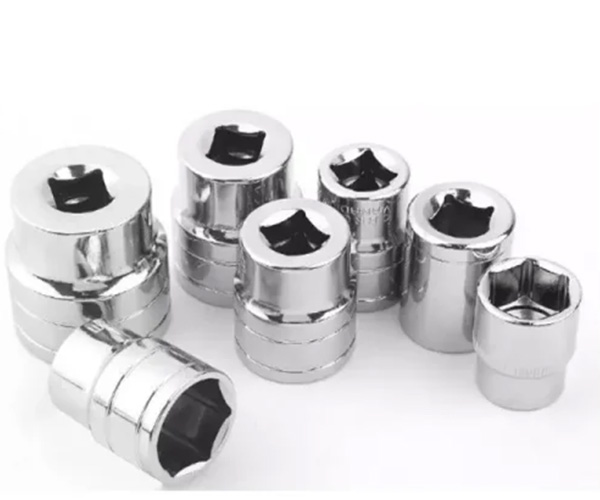
Materials Used
The material composition of a socket plays a crucial role in its durability and performance. Regular sockets are generally made from chrome vanadium steel, known for its hardness and resistance to wear and corrosion. On the other hand, impact sockets are typically made from chrome molybdenum steel, which offers greater strength and durability under high-stress conditions.
Chrome vanadium steel provides a good balance of strength and cost-effectiveness, making regular sockets suitable for most DIY and light professional applications. Chrome molybdenum steel, while more expensive, offers superior impact resistance, making impact sockets ideal for heavy-duty and high-torque applications.
Understanding these fundamental differences is the first step in choosing the right socket set for your needs. Whether you’re a DIY enthusiast looking to expand your tool collection or a professional seeking reliable tools for demanding tasks, knowing the basics of socket types and materials will help you make a more informed decision.
III. Regular Sockets
Regular sockets are a staple in many toolboxes, prized for their versatility and ease of use. Understanding their design, common uses, and pros and cons can help you determine if they are the right fit for your tasks.
Design and Construction
Regular sockets are typically made from chrome vanadium steel, a material known for its durability and resistance to wear and corrosion. The manufacturing process involves forging the steel into the desired shape and then heat-treating it to enhance its strength and toughness. The surface of regular sockets is usually polished to a high shine and often coated with a layer of chrome to further protect against corrosion and provide a smooth finish that makes them easy to clean.
The design of regular sockets includes a hexagonal or square drive that fits onto the corresponding ratchet or wrench. The interior of the socket is also hexagonal, designed to fit snugly over the head of a fastener. This snug fit ensures efficient torque application, reducing the risk of slipping and rounding off fasteners.
Common Uses
Regular sockets are used in a wide range of applications, making them a versatile addition to any toolkit. Some common uses include:
- Automotive Repairs: From changing tires to engine work, regular sockets are essential for various automotive tasks.
- Household Maintenance: Regular sockets come in handy for assembling furniture, fixing appliances, and other household repairs.
- Bicycle Repairs: They are also useful for maintaining and repairing bicycles, including adjusting brakes and gears.
The versatility of regular sockets makes them suitable for both DIY enthusiasts and professionals who need reliable tools for everyday tasks.
Pros of Regular Sockets
- Cost-Effectiveness: Regular sockets are generally less expensive than impact sockets, making them a cost-effective choice for many users.
- Wide Availability: They are widely available in various sizes and sets, making it easy to find the right socket for your needs.
- Lightweight: Regular sockets are typically lighter than impact sockets, making them easier to handle and reducing fatigue during extended use.
Cons of Regular Sockets
- Limited Durability Under High Stress: Regular sockets are not designed to withstand the high torque levels generated by impact tools. Using them with such tools can lead to cracking or shattering.
- Not Suitable for Impact Tools: Due to their construction and material, regular sockets should not be used with impact wrenches or other high-torque tools, as this can damage both the socket and the tool.
In summary, regular sockets are an excellent choice for general-purpose use, offering a balance of affordability, availability, and ease of use. However, their limitations in high-torque applications mean they are best suited for tasks that do not require the use of impact tools.
IV. Impact Sockets
Impact sockets are designed to meet the demands of high-torque applications, providing superior strength and durability. Let’s delve into their design, common uses, and the pros and cons to understand why they might be the right choice for you.
Design and Construction
Impact sockets are constructed from chrome molybdenum steel, a material known for its exceptional strength and ability to withstand the stresses of high-torque applications. The manufacturing process for impact sockets involves forging the steel and subjecting it to a rigorous heat-treatment process that enhances its toughness and durability.
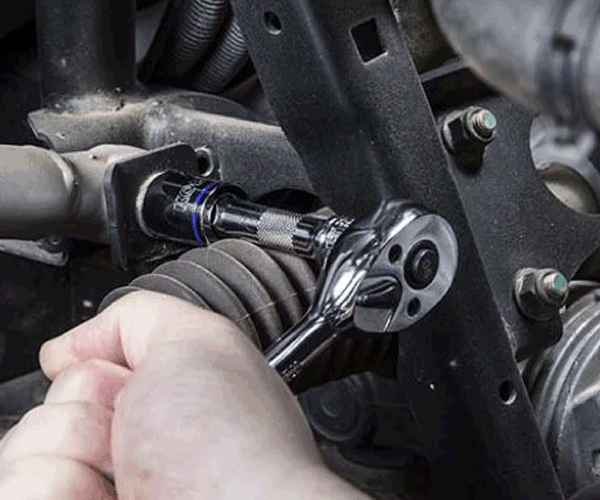
One of the key features of impact sockets is their thicker walls compared to regular sockets. This design element provides additional strength, allowing the socket to absorb the sudden impacts and high torque generated by impact tools. The exterior of impact sockets is typically coated with a black oxide finish, which offers protection against corrosion and adds an extra layer of durability.
The internal design of impact sockets includes a six-point (hexagonal) or twelve-point (double hexagonal) configuration, providing a secure fit over the fastener. This design minimizes the risk of rounding off fasteners, even under high stress, ensuring efficient and safe torque application.
Common Uses
Impact sockets are essential in professional and heavy-duty settings where high torque levels are common. Some typical uses include:
- Automotive Repairs: Impact sockets are widely used in automotive workshops for tasks such as changing tires, working on suspension systems, and engine repairs.
- Industrial Applications: They are also crucial in various industrial settings, including machinery maintenance and assembly lines.
- Construction Projects: Impact sockets are used in construction for tasks that involve heavy machinery and equipment.
The ability to withstand high torque makes impact sockets indispensable for professionals who need reliable and durable tools for demanding tasks.
Pros of Impact Sockets
- High Durability and Strength: Impact sockets are designed to handle the high torque and sudden impacts generated by impact tools, making them extremely durable.
- Safety Features: The thicker walls and robust construction of impact sockets reduce the risk of cracking or shattering, enhancing safety during use.
- Suitable for High-Torque Applications: Impact sockets are specifically designed for use with impact wrenches and other high-torque tools, ensuring optimal performance and longevity.
Cons of Impact Sockets
- Higher Cost: Impact sockets are generally more expensive than regular sockets, reflecting their superior construction and durability.
- Heavier Weight: The thicker walls and robust construction make impact sockets heavier, which can lead to fatigue during extended use.
- Limited Use in Low-Torque Situations: While impact sockets excel in high-torque applications, their heavier weight and higher cost may not be justified for lighter tasks.
Impact sockets are an excellent investment for professionals and anyone who frequently works with high-torque tools. Their durability, safety features, and performance in demanding applications make them a valuable addition to any toolkit. However, their higher cost and weight mean they might not be necessary for lighter, everyday tasks where regular sockets suffice.
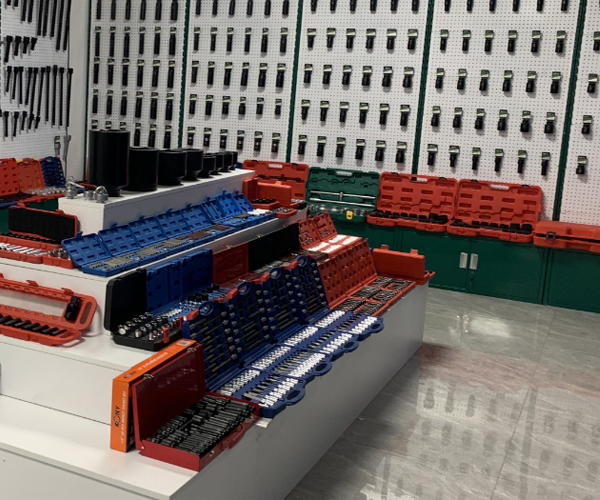
Thank you for your interest in Kolarwin hand tools. Our tools are designed for both DIY enthusiasts and professional use. If you have specific product requirements or need further information, please let us know. We would be happy to provide you with a detailed product catalog, pricing, and other relevant information.
For more details, please visit our website at www.kolarwin-tools.com